Navigating the Global PCB Landscape: Top Manufacturers Shaping the Future
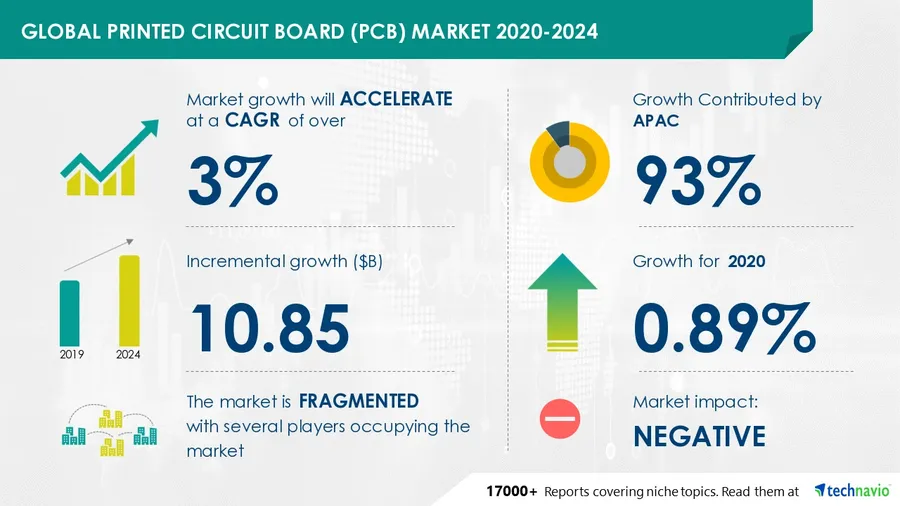
In today's interconnected world, printed circuit boards (PCBs) are the unsung heroes powering virtually every electronic device we use. From smartphones to medical equipment, the demand for high-quality PCBs is constantly rising. This article will introduce you to some of the top PCB manufacturers in the world, like AT&S, TTM Technologies, and PCBONLINE, shedding light on their critical role and the technology that makes our modern world possible. We’ll delve into their capabilities, regional strengths, and contributions to the booming electronics industry.
Global PCB Market Overview
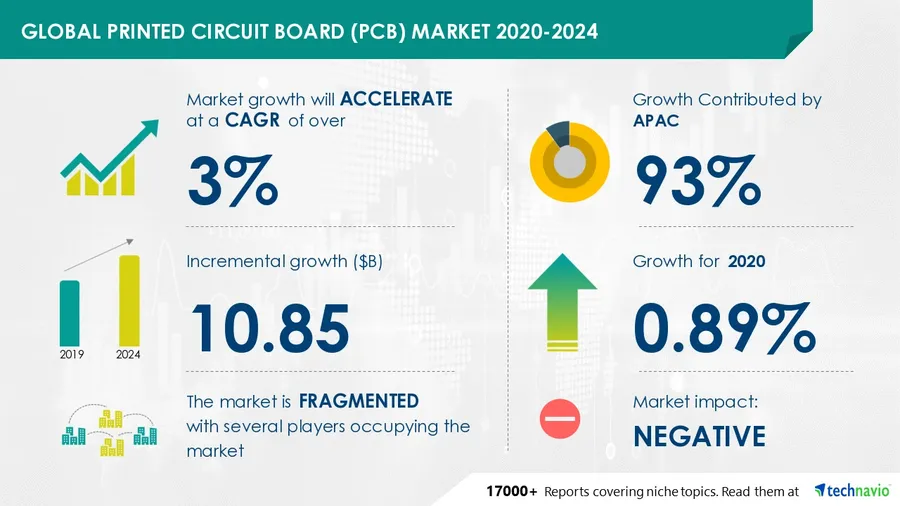
The global Printed Circuit Board (PCB) market is a cornerstone of the electronics industry, experiencing continuous growth driven by technological advancements and the increasing demand for electronic devices across various sectors. This market's dynamism is fueled by innovations in consumer electronics, automotive technology, industrial automation, and telecommunications, creating a vital link in the global electronics supply chain.
Key drivers include the proliferation of smartphones, wearable technology, the rise of the Internet of Things (IoT), and the expanding automotive sector that demands advanced electronics for safety and connectivity. The industry is also heavily influenced by technological progress, with demand shifting toward more complex and high-density PCBs.
Top PCB Manufacturers Worldwide: A Closer Look
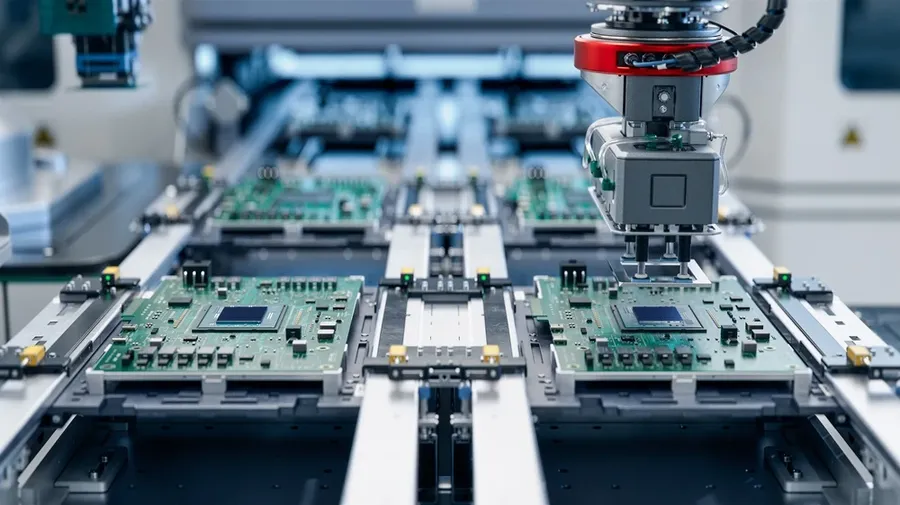
The global PCB manufacturing landscape is dominated by a select group of companies, each distinguished by their unique strengths, specializations, and technological prowess. These leading manufacturers are pivotal in supporting the electronics industry's demand for high-quality, reliable circuit boards.
Manufacturer | Headquarters | Core Competencies | Specializations |
---|---|---|---|
AT&S | Austria | High-end PCBs, HDI, IC substrates | Automotive, Industrial, Medical |
TTM Technologies | USA | Complex PCBs, RF and microwave, HDI | Aerospace, Defense, Data Centers, Medical |
PCBONLINE | China | Diverse PCB offerings | Consumer electronics, industrial, automotive |
Zhen Ding Technology | Taiwan | Flexible PCBs, HDI | Mobile devices, IoT, wearable tech |
Regional Strengths: Asia's Dominance in PCB Manufacturing
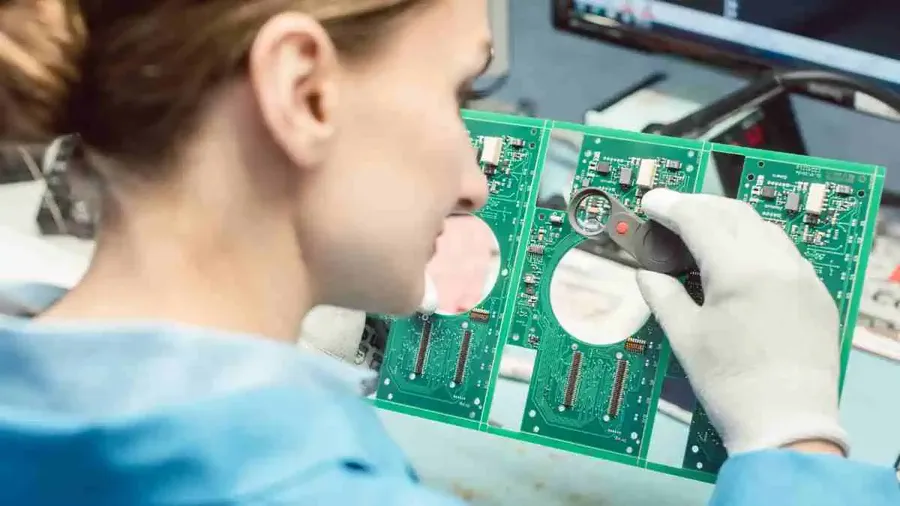
The Asia-Pacific region stands as the preeminent global hub for PCB manufacturing, with China, Taiwan, and Japan leading the way. This dominance stems from a confluence of factors, including cost advantages, scalable production capabilities, and efficient supply chain ecosystems that have solidified the region's position in the global electronics industry.
Key players in this region include:
- Unimicron (Taiwan)
A major manufacturer known for its advanced PCB technologies and high-volume production. - Nippon Mektron (Japan)
Renowned for its high-quality flexible PCBs and a strong presence in automotive and consumer electronics. - Compeq (Taiwan)
A leading PCB supplier specializing in high-layer count and advanced technologies catering to diverse sectors.
The concentration of manufacturing expertise, infrastructure, and a skilled workforce allows these companies to offer competitive pricing and rapid scalability for their PCB production, reinforcing Asia's stronghold in the global market.
Advantage | Description |
---|---|
Cost Efficiency | Lower labor costs and government incentives contribute to more competitive pricing. |
Scalability | Advanced infrastructure and high-volume capacity enable rapid production scaling to meet global demand. |
Supply Chain Efficiency | Proximity to raw material suppliers and electronic assembly plants fosters a streamlined and responsive supply chain. |
North American PCB Manufacturing Landscape
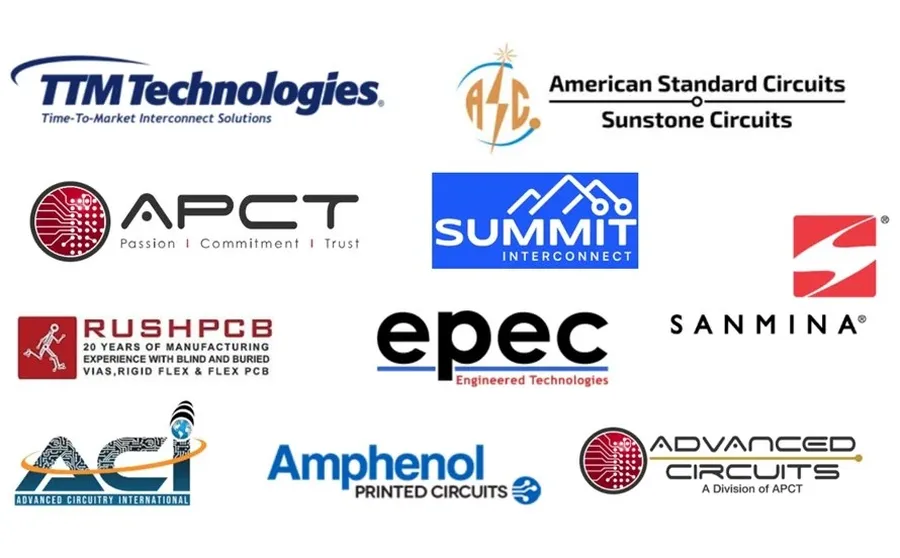
The North American PCB manufacturing landscape, primarily centered in the United States, presents a unique set of characteristics compared to the dominant Asian market. While not as large in volume as Asia, North American manufacturers distinguish themselves through technological innovation, high-reliability production, and a focus on specialized sectors such as aerospace, defense, and medical devices. This section will explore key players, their specializations, and the regional challenges and opportunities.
Key PCB Manufacturers in North America
- TTM Technologies
A major player in North America, TTM Technologies offers a broad range of PCB products from high-volume commercial applications to highly complex custom boards for aerospace and defense industries. Their capabilities include advanced materials, HDI technology and RF/Microwave designs. - American Standard Circuits
Specializing in high-reliability, mission-critical PCBs, American Standard Circuits focuses on providing quality solutions for industries with stringent requirements, such as military and aerospace applications. They also offer quick-turn prototyping services. - Flex Ltd.
While a global company, Flex has a significant presence in North America and is known for its scalable manufacturing capabilities, particularly in printed circuit board assembly and system integration, catering to various sectors such as consumer electronics, automotive, and healthcare.
Challenges and Opportunities
- Higher Operating Costs
Compared to Asian manufacturers, North American facilities face higher labor, energy and material costs, posing challenges to price competition. - Strong Demand for High Reliability PCBs
The region benefits from strong demand in the high-reliability sectors, such as military and aerospace, which require complex, highly durable PCBs often at lower volumes than consumer electronics. - Emphasis on Technological Innovation
North American manufacturers focus on technology innovation and early adoption of advanced materials, processes, and design. These efforts position them at the forefront of high-tech PCB developments and applications. - Supply Chain Resilience
A shorter supply chain is an increasing priority for many North American companies seeking to mitigate supply disruptions and geopolitical risks. This creates opportunities for domestic PCB manufacturers, particularly those that can provide high quality at acceptable lead times.
Key Factors in Choosing a PCB Manufacturer
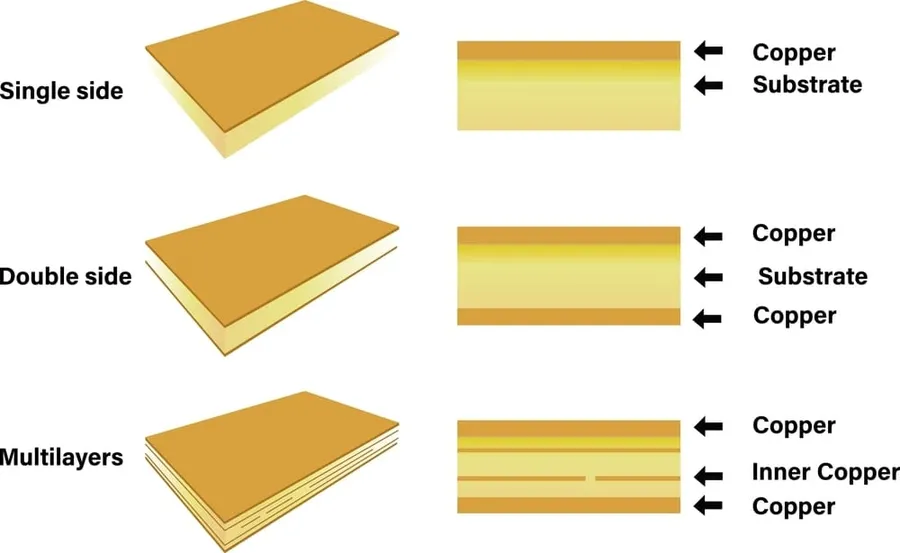
Selecting the right PCB manufacturer is a critical decision that impacts product quality, reliability, and time-to-market. This section details the essential factors to consider, ensuring a choice that aligns with specific project needs and objectives.
Factor | Description | Importance |
---|---|---|
Quality Standards | Adherence to industry standards (IPC), process control, and material quality. | Crucial for reliability and performance. |
Manufacturing Capabilities | Ability to produce single-sided, double-sided, multilayer, HDI, flexible, and rigid-flex PCBs. | Ensures compatibility with your design needs. |
Technological Proficiency | Expertise in advanced manufacturing techniques, including microvias, fine line traces, and advanced materials. | Needed for cutting-edge applications. |
Cost-Effectiveness | Overall cost, including tooling, production, and shipping. Not only focusing on unit cost, but also total cost of ownership. | Impacts project budget viability. |
Lead Times | Production time from order placement to delivery. This includes prototype and production lead times. | Affects project timelines and time to market. |
Certifications | Compliance with ISO 9001, ISO 14001, AS9100, or other relevant certifications. | Demonstrates commitment to quality and environmental standards. |
Customer Service | Responsiveness, communication, and technical support throughout the process. | Enhances collaboration and resolves issues efficiently. |
Material Options | Availability of different materials, including FR-4, high-Tg FR-4, Rogers, and polyimide. | Important for specific applications and performance needs. |
Volume Flexibility | Ability to handle both small prototype runs and large-scale production. The ability to scale with your product needs. | Crucial for product evolution. |
Technological Advancements and Innovation in PCB Manufacturing
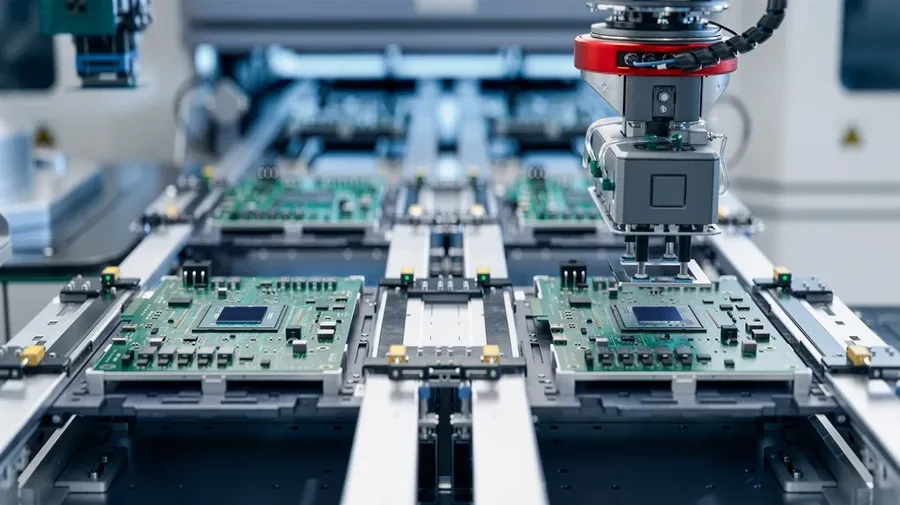
The PCB manufacturing sector is undergoing rapid transformation driven by technological advancements and innovative processes. These developments are crucial for supporting the increasing complexity and performance demands of modern electronics. Top manufacturers are at the forefront of implementing these cutting-edge technologies to enhance their production capabilities and product offerings.
Key technological drivers include:
- High-Density Interconnect (HDI) Technology
HDI technology enables the creation of PCBs with finer lines, smaller vias, and higher component density. This is critical for compact devices with advanced functionality. Techniques such as microvias, laser direct imaging (LDI), and sequential lamination are essential for HDI PCB manufacturing. Top manufacturers are expanding their investments in HDI to cater to growing demand for miniaturized electronics. - Flexible PCBs
Flexible PCBs, or flex circuits, offer the advantage of being bendable and conformable, making them suitable for applications with non-planar surfaces. Advanced materials such as polyimide films and thinner copper layers are used to create flexible PCBs. The increased adoption of wearable devices and flexible electronics is driving innovation and implementation of flexible PCB technologies. - Advanced Materials
The use of advanced materials is critical in enhancing the thermal, electrical, and mechanical performance of PCBs. These materials include: low-loss dielectrics for high-frequency applications, thermally conductive substrates for better heat dissipation, and high-performance resins. Manufacturers are actively researching and incorporating new materials to meet diverse design requirements. - Embedded Components
Embedding components directly into the PCB layers offers advantages such as reduced board size, enhanced signal integrity, and improved electrical performance. Manufacturers are developing techniques to integrate resistors, capacitors, and even ICs within the PCB structure. This allows for higher functional density and greater design flexibility. - Automated Manufacturing Processes
Automation is playing an increasingly important role in PCB manufacturing. Automated lines with robotic systems for component placement, inspection and testing contribute to improved efficiency, reduced lead times and higher product quality. Many top manufacturers are employing digital manufacturing practices to improve traceability and reduce errors.
Top manufacturers are not just adopting these technologies but also actively innovating and developing their proprietary processes. These innovations are crucial for maintaining a competitive advantage and catering to the ever-evolving demands of the electronics industry. The successful implementation of these advancements requires substantial investments in research, development, and manufacturing infrastructure.
Frequently Asked Questions About PCB Manufacturers
This section addresses common questions regarding PCB manufacturers, providing insights to help you navigate the complexities of this industry. We delve into key aspects such as identifying top manufacturers, understanding regional production strengths, and evaluating manufacturer quality.
- Who is generally considered the best PCB manufacturer?
Determining the 'best' PCB manufacturer is subjective and depends heavily on specific project needs, including technology requirements, volume, and budget. There isn't a single universally acknowledged 'best' manufacturer. However, companies like AT&S, TTM Technologies, and Zhen Ding Technology consistently rank highly due to their technological capabilities, reliability and capacity. It's crucial to assess manufacturers based on your own project's requirements. - Which country is the largest manufacturer of PCBs?
China currently dominates the global PCB manufacturing landscape, accounting for a significant share of the world's PCB production. The country's vast manufacturing infrastructure, lower labor costs, and strategic government support have established it as a leading hub for PCB production. Other major PCB producing regions are in Asia including Taiwan, South Korea and Japan. - Which PCB company offers the best quality PCBs?
The definition of 'best' quality varies by industry and application. Generally, companies like AT&S, TTM Technologies and Nippon Mektron are known for high quality PCBs, particularly in advanced applications. However, quality is not solely a company attribute. Many smaller manufacturers can produce high-quality boards for certain application with good quality control. The 'best' quality is usually achieved when a manufacturer can consistently meet or exceed a customer's specific requirements and quality standards. - Who is the largest PCB manufacturer in the USA?
TTM Technologies is among the largest PCB manufacturers in the USA, recognized for its broad range of manufacturing capabilities. The US PCB manufacturing sector has experienced a resurgence as companies diversify supply chains, seeking to mitigate risks in their supply networks. Other US based leaders are American Standard Circuits and Flex Ltd. However, it is important to note that many US based companies also use overseas production for parts of their supply chain. - What are the key factors to consider when selecting a PCB manufacturer?
Selecting the correct PCB manufacturer involves careful consideration of various factors. These include the manufacturer's experience, manufacturing capabilities (e.g., multilayer, HDI, flex), quality control certifications (e.g., ISO 9001, AS9100), turnaround times, cost structure, and customer support. It is critical that the manufacturer can meet both current and future technical requirements. For example, if miniaturization is expected to be a future requirement, you should select a partner that has experience in this area. A comprehensive evaluation based on these factors helps ensure the selection of a suitable PCB partner. - How do I verify the quality of a PCB manufacturer?
Verifying a PCB manufacturer's quality involves several steps. First, assess their certifications and adherence to industry standards. Request sample boards to conduct thorough testing. Audit the manufacturer in person or through a third party. If possible, discuss quality issues with past customers, to get a realistic view of their quality record. These procedures help assess the manufacturers quality and reduce the risk of errors. - What impact does PCB lead time have on a project?
Lead time is critical in project planning, particularly for time sensitive projects. Extended lead times can delay project launches, increase storage costs and cause financial losses. It is often best to select a manufacturer with the necessary capacity and production capability, which will help reduce the risk of late delivery. If lead time is a critical element of project success, it is beneficial to have established protocols to escalate production timelines.
Future Trends in the PCB Industry
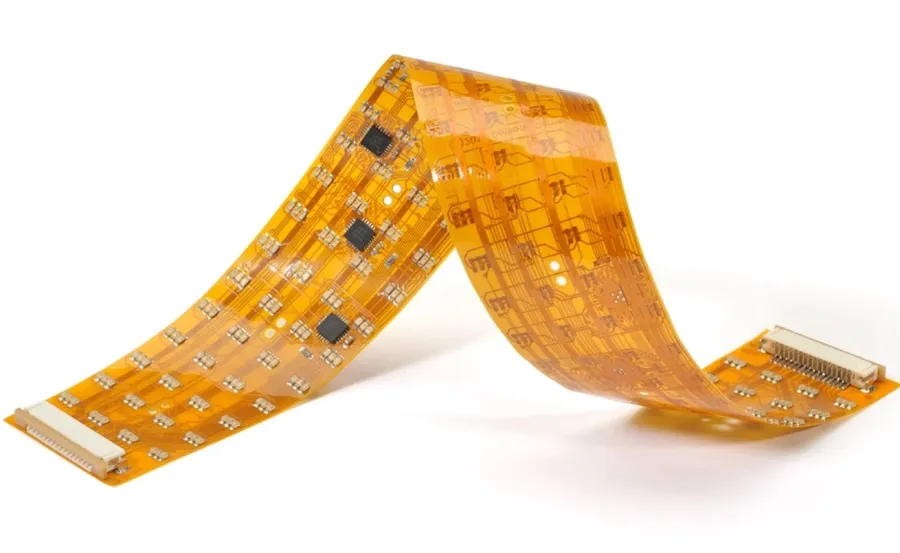
The PCB industry is undergoing a rapid transformation driven by technological advancements, increasing environmental concerns, and evolving global supply chains. Top manufacturers are actively adapting to these shifts, positioning themselves to lead in an era of smarter, more sustainable, and increasingly complex electronic devices.
Emerging trends include the rise of miniaturization, requiring high-density interconnect (HDI) and micro-via technology, and the increasing demand for flexible PCBs for wearable technology and other novel applications. Simultaneously, there is a strong push for more sustainable PCB manufacturing processes, focusing on material recycling, energy efficiency, and reduced chemical usage. The global supply chain is also experiencing significant shifts, prompting manufacturers to adopt more resilient and diversified sourcing strategies.
- Miniaturization and High-Density Interconnect (HDI):
The continuous drive towards smaller and more powerful devices fuels the demand for HDI PCBs. These advanced boards allow for increased functionality in smaller form factors through finer lines and spaces, micro-vias, and stacked vias. - Flexible and Stretchable PCBs:
Flexible PCBs (FPCBs) are gaining traction in applications requiring adaptability, such as wearables, medical devices, and automotive electronics. Emerging technology extends this further with stretchable PCBs, enabling a new realm of possibilities for bendable and conformal electronics. - Advanced Materials:
Innovation in substrate materials is critical to meet the demands of faster signal transmission, better thermal management, and environmental compliance. Research into bio-based polymers and other sustainable options is gaining importance. High-performance materials with enhanced dielectric properties, and thermal conductivity to allow for more efficient circuit operation are also in growing demand. - Sustainability and Green Manufacturing:
The PCB industry faces growing pressure to minimize its environmental footprint. This trend is pushing manufacturers to adopt eco-friendly materials, water-based processing chemicals, closed-loop water systems, and comprehensive recycling programs for end-of-life PCBs. - Smart Manufacturing and Automation:
To improve efficiency, quality, and traceability, manufacturers are increasingly integrating automation, AI, and big data analytics into production processes. This transition towards Industry 4.0 concepts allows for optimized production and better yield rates, as well as a reduction in lead times. - Supply Chain Resilience:
Geopolitical uncertainties and global disruptions have highlighted the need for diversified supply chains. Leading PCB manufacturers are adopting regional manufacturing strategies and investing in redundant production capacity to mitigate risks and assure stable deliveries.
In response to these trends, top manufacturers are investing heavily in research and development, adopting advanced manufacturing techniques, and forming strategic alliances to expand their technological and market reach. This proactive approach ensures they remain at the forefront of innovation, enabling the next generation of electronic products. As an example, some large manufacturers are establishing separate divisions focusing on advanced material research, and others are investing in the development of more sustainable manufacturing processes using renewable energy.
The PCB industry is a dynamic ecosystem with several key players globally. Top PCB manufacturers in the world, including companies like AT&S, TTM Technologies, and PCBONLINE, are not just producing essential components; they are actively driving innovation in electronics. Whether you're an engineer, a procurement manager, or just curious, understanding the landscape of these PCB powerhouses is key to grasping the foundations of modern electronics. As technology advances and demands for more efficient, flexible, and high-performing circuit boards evolve, the companies highlighted here will continue to play a pivotal role in shaping the future of our digital world.
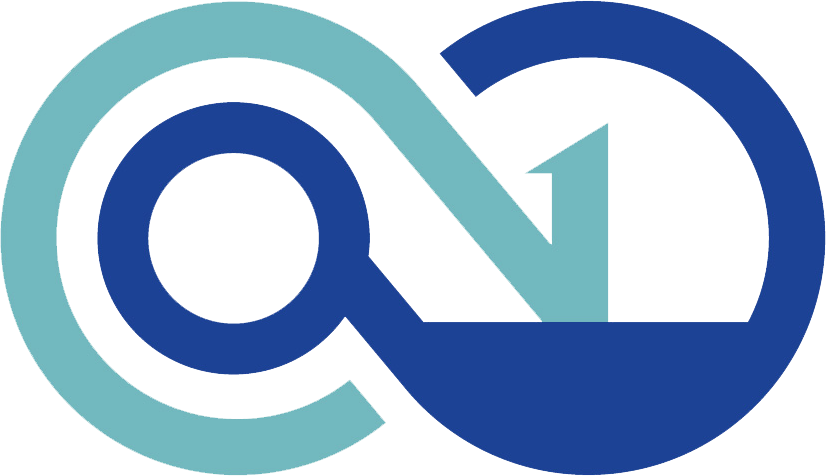