The Ultimate Guide to PCB Manufacturing: From Design to Finished Board
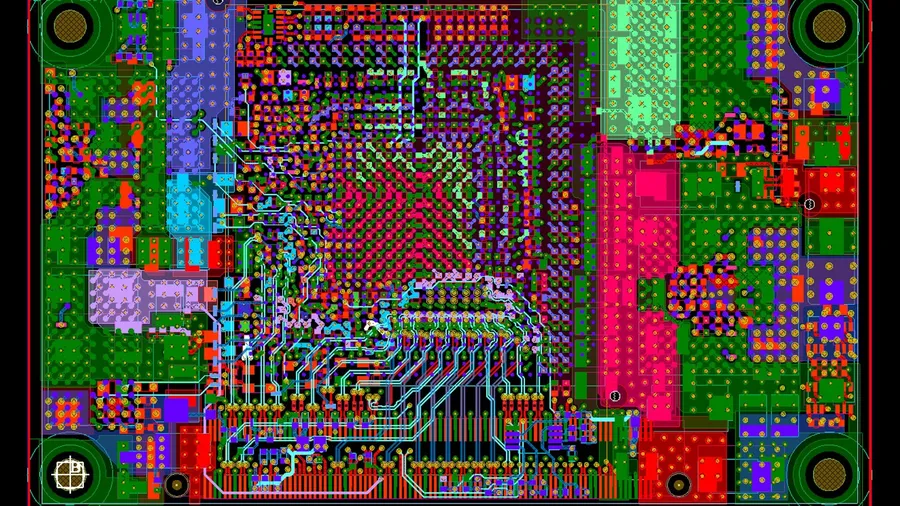
Printed circuit boards (PCBs) are the backbone of modern electronics, silently powering everything from smartphones to satellites. Understanding the intricate process of PCB manufacturing—from the initial design concepts to the finished product—is crucial for anyone involved in electronics. This guide will take you through each stage, explaining the key steps involved and offering valuable insights to help you make informed choices about your PCB needs.
The PCB Design Process: Turning Ideas into Reality
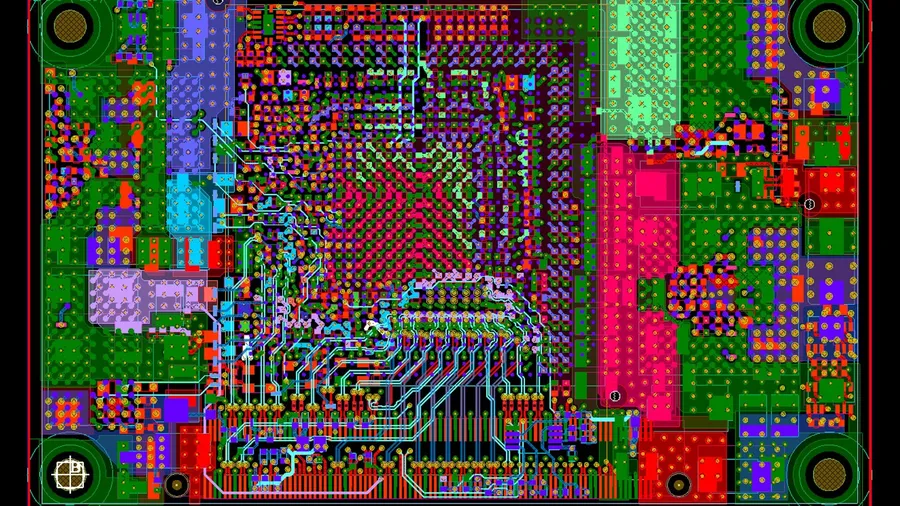
The genesis of any successful Printed Circuit Board (PCB) lies in a meticulously executed design process. This phase, preceding physical manufacturing, is critical for translating a conceptual idea into a functional, manufacturable board. It involves schematic capture, PCB layout, and careful consideration of materials, layer configuration, and component placement—all pivotal factors in achieving optimal manufacturing outcomes.
- Schematic Capture
The process of creating a digital representation of the electronic circuit using symbols and connections, defining the electrical functionality of the board. - PCB Layout
The art and science of arranging physical components and electrical traces on the board’s substrate, optimizing for signal integrity, thermal management, and manufacturability. - Material Selection
Choosing the appropriate substrate material (e.g., FR-4, Rogers) based on electrical, thermal, and mechanical performance requirements. - Layer Stack-Up
Defining the arrangement of copper and insulating layers in a multi-layer PCB, optimized to control impedance, reduce noise, and enhance overall performance. Proper layer stack-up is often overlooked, but is vital to the final performance. - Component Placement
Strategic arrangement of components on the board to minimize trace lengths, prevent signal interference, and ensure efficient assembly.
Fabrication Steps: From Design Files to Physical Boards
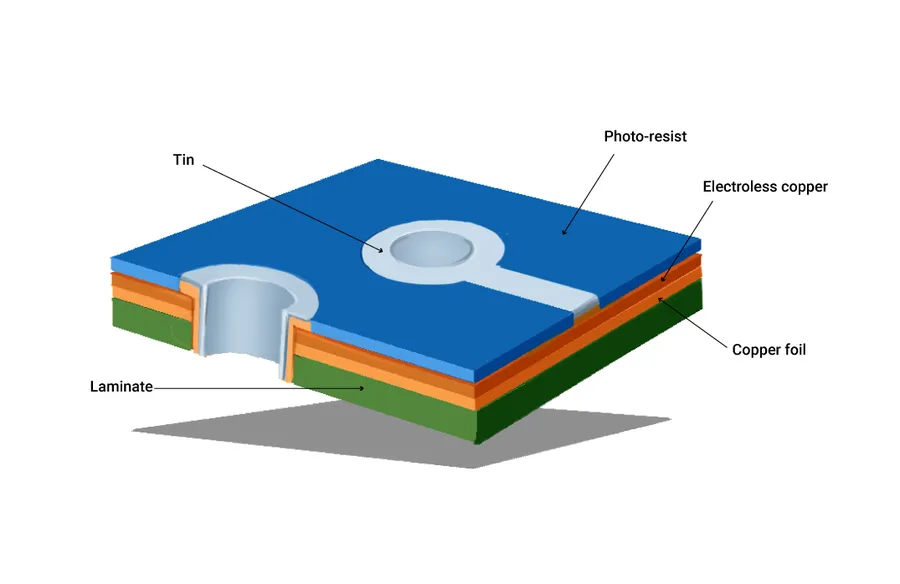
The transformation of a PCB design from digital blueprints into a tangible physical board involves a series of intricate fabrication steps. This section details these critical processes, ensuring that a design's intent is accurately materialized into the final PCB.
- Film Plotting
The fabrication process begins with film plotting, where the PCB design's layers are transferred onto a photographic film. High-resolution plotters use CAD/CAM data to create highly accurate patterns on transparent film, which act as a mask for subsequent imaging processes. Precision in film plotting is vital to ensure that features, such as traces and pads, are accurately replicated. - Copper Clad Lamination
The process of creating a copper-clad laminate (CCL) involves using a glass-reinforced epoxy substrate onto which a thin layer of copper is bonded on one or both sides. The copper layer serves as the foundation for circuits, and its thickness must be accurately controlled to ensure that the required electrical performance is achieved. - Imaging
Following the application of a photoresist to the copper-clad laminate, the photographic film is carefully aligned and exposed to UV light. This transfers the precise patterns of the PCB design onto the photoresist, rendering some of the areas resistant to the etching process while leaving others vulnerable. The outcome is a latent image of the desired copper pattern. - Etching
The etching process removes the exposed copper not protected by the hardened photoresist, leaving behind the desired circuit patterns. Chemical etchants, such as ferric chloride, are used to dissolve the unwanted copper. The process parameters are strictly controlled to ensure that the circuit traces are formed accurately with the required width and spacing, thus maintaining the integrity of the PCB design. - Drilling
Drilling creates the holes needed for through-hole components and vias, which facilitate the electrical connections between different layers of the PCB. Precision drilling machines, controlled by digital data, are used to create holes with the required diameters and locations, which is crucial for the effective assembly of components. The process of drilling needs to be accurately aligned to the design. - Plating
Plating involves depositing a thin layer of conductive material onto the walls of drilled holes and onto the exposed copper areas on the surface. This step is crucial to ensure reliable electrical connections between the board's layers. Electrolytic plating is commonly used to ensure that the via walls and the circuit traces are conductive, and the right thickness is achieved.
Inner Layer Production: The Core of Multi-layer PCBs
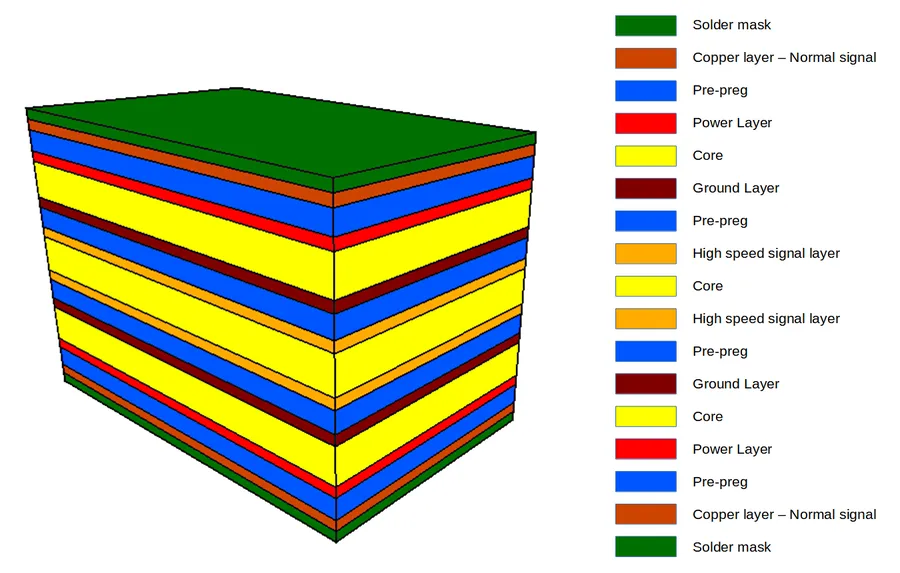
The creation of inner layers is a pivotal step in manufacturing multilayer PCBs, demanding meticulous control and precision. This process, specific to multilayer boards, involves a sequence of imaging, etching, and layering, crucial for building the functional complexity of modern electronics. These inner layers form the backbone of multilayer PCBs, providing electrical connectivity and signal routing within the board.
The process of inner layer production is technically complex and requires high precision, it ensures signal integrity and proper electrical function of the final product.
- Imaging
The process begins by transferring the PCB design onto a copper-clad laminate. This involves using a photo-sensitive resist and a UV light exposure system to selectively harden the areas that will become conductive traces. The resist acts as a mask, protecting the copper from the subsequent etching process. - Etching
After imaging, the unexposed photoresist is removed, and the board is immersed in an etching solution. This solution dissolves the unprotected copper, leaving behind only the copper traces defined by the hardened resist. This precise removal of copper is critical for circuit integrity. - Layering
After etching, the layers undergo a cleaning process, and are then stacked with other inner layers, along with prepreg, which acts as the bonding material. This process is critical for ensuring proper alignment and structural integrity before the layers are pressed together. Precise registration is essential to ensure the electrical connections between layers work.
Process Step | Description | Key Requirements |
---|---|---|
Imaging | Transferring the design onto copper clad laminate using photoresist and UV exposure. | High-resolution, accurate photo masks, controlled UV exposure. |
Etching | Removing unwanted copper using chemical solutions after imaging. | Precise control of etching time and chemical concentration, uniform etching. |
Layering | Stacking etched layers with prepreg, to build multilayer structure | Precise layer alignment and consistent bonding of layers |
Drilling, Plating, and Layer Bonding: Connecting the Layers
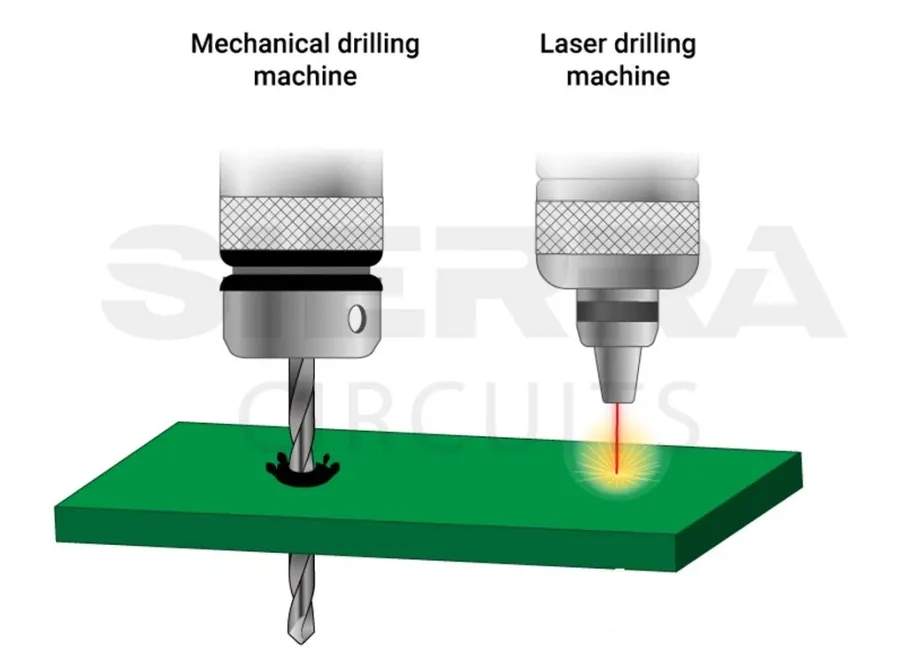
Following the etching process, the creation of electrical connections between different layers of a PCB requires precise drilling, plating, and layer bonding techniques. This stage is crucial in transforming individual layers into a fully functional, interconnected circuit board.
The following processes detail the methodologies employed in creating these vital interlayer connections.
Process | Description | Purpose | Key Considerations |
---|---|---|---|
Precision Drilling | High-precision drilling machines create holes through the layers of the PCB. These holes are the foundation for vias and component mounting. | To establish precise paths for electrical connections and accommodate component leads. | Drill bit size, hole location accuracy, and material compatibility. |
Electroless Plating | A thin layer of conductive material (typically copper) is deposited inside the drilled holes using a chemical process, creating a conductive base. | To enable subsequent electrolytic plating and create an initial conductive pathway. | Uniformity of plating, chemical concentration, and process temperature. |
Electrolytic Plating | A thicker layer of copper is electroplated onto the electroless layer, strengthening the conductive pathway in the holes and on the surface. | To create robust and reliable connections through the drilled vias and enhance surface conductivity for the next steps. | Plating thickness control, current density, and bath chemistry. |
Layer Bonding | Pre-etched, drilled and plated layers are stacked and pressed together under heat and pressure using a bonding adhesive (prepreg). | To create a solid, integrated multi-layer PCB with strong interlayer adhesion. | Alignment accuracy, bonding temperature, pressure, and prepreg material. |
Soldermask and Silkscreen Application: Protecting and Identifying
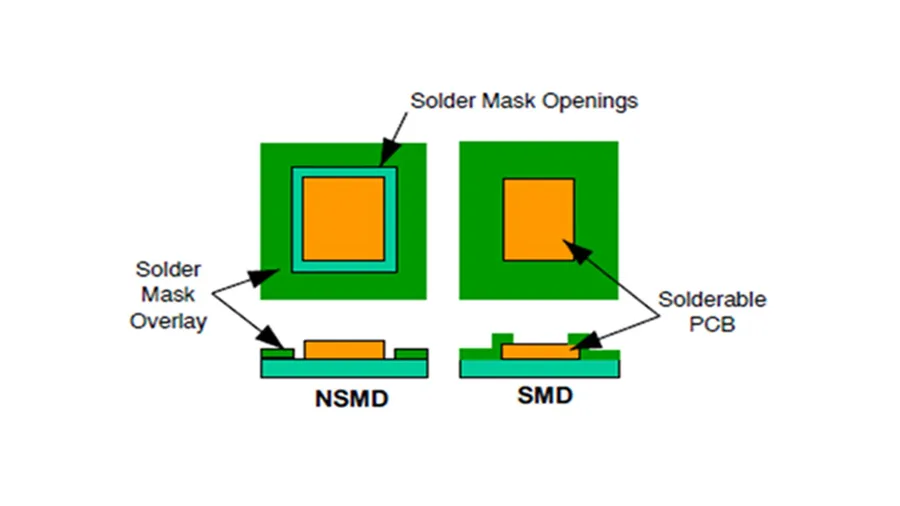
Soldermask and silkscreen applications are critical steps in PCB manufacturing, ensuring both the long-term reliability and ease of use of the final product. The soldermask acts as a protective layer, preventing shorts and corrosion, while the silkscreen provides vital component identification information, assisting during assembly and maintenance.
The application process is typically automated to ensure high precision and consistency across the PCB surface. These layers are not merely cosmetic but are fundamental to the functional longevity and serviceability of the circuit board.
Feature | Soldermask | Silkscreen |
---|---|---|
Purpose | Protect copper traces from corrosion and electrical shorts | Provide component identification, polarity, and test points |
Material | Polymer-based epoxy or similar material | Epoxy ink or UV curable ink |
Color | Typically green, but can be other colors such as red, blue, black, and white | Typically white, but other colors are also available |
Application | Applied after plating, before silkscreen | Applied after soldermask |
Curing | Cured using heat or UV light | Cured using UV light or heat |
Surface Finishing: Ensuring Solderability and Durability

Surface finishing is a critical step in PCB manufacturing, directly impacting the board's solderability, resistance to corrosion, and overall reliability. The selection of the appropriate surface finish is crucial for optimal performance and longevity of the assembled PCB.
Surface Finish | Description | Advantages | Disadvantages | Typical Applications |
---|---|---|---|---|
HASL (Hot Air Solder Leveling) | Molten solder is applied and then leveled with hot air knives. | Low cost, good solderability, widely available. | Uneven surface, not suitable for fine-pitch components, leaded (Pb) HASL is not RoHS compliant. | General purpose PCBs, through-hole and larger SMT components. |
ENIG (Electroless Nickel Immersion Gold) | A layer of nickel is plated followed by a thin layer of immersion gold. | Excellent solderability, good corrosion resistance, flat surface for fine-pitch components, RoHS compliant. | Higher cost, black pad risk, not suitable for direct wire bonding. | Fine-pitch SMT components, wire bonding, high-reliability applications. |
OSP (Organic Solderability Preservative) | A thin organic layer is applied to the copper surface to protect it from oxidation. | Low cost, flat surface, good solderability, RoHS compliant. | Short shelf life, sensitive to handling, may not withstand multiple reflow cycles. | Cost-sensitive applications, lower complexity designs, boards with few assembly cycles. |
Immersion Tin | A thin layer of tin is deposited through chemical immersion. | Good solderability, flat surface, RoHS compliant. | Tin whiskers can be a reliability issue, sensitive to handling and storage. | Applications where moderate performance and cost is a factor. |
Immersion Silver | A thin layer of silver is deposited through chemical immersion. | Excellent solderability, good conductivity, RoHS compliant | Susceptible to tarnishing, requires special storage to prevent oxidation. | High-frequency applications, switch contacts, or other applications which require high conductivity. |
PCB Assembly: Populating the Board with Components
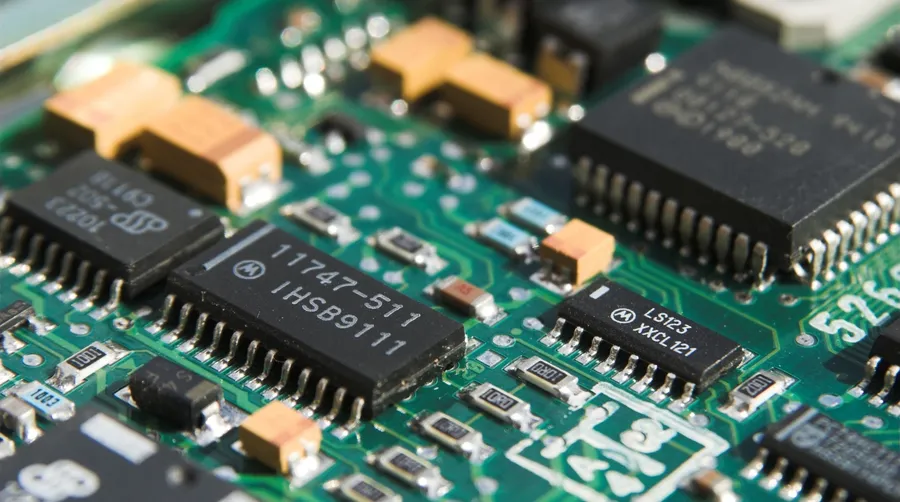
PCB assembly is the crucial stage where electronic components are precisely placed and soldered onto the fabricated printed circuit board, transforming it from a bare board into a functional electronic module. This process involves sophisticated techniques and equipment to ensure accurate placement and reliable electrical connections.
The assembly process can be broadly categorized into automated and manual methods, each suited for different production volumes and complexity levels.
- Automated Assembly
Automated assembly utilizes pick-and-place machines to accurately position components on the board, followed by reflow soldering to create permanent connections. This method is ideal for high-volume production, ensuring consistent quality and minimizing errors. - Manual Assembly
Manual assembly, while more labor-intensive, is often employed for prototyping, small production runs, or for boards with unique component requirements that automated processes can't handle. It requires skilled technicians who can place and solder components with precision and care.
Method | Volume | Accuracy | Cost | Application |
---|---|---|---|---|
Automated Assembly | High | High | Lower per unit | Mass production, complex designs |
Manual Assembly | Low | Variable (skilled labor required) | Higher per unit | Prototyping, low-volume runs, unique component requirements |
Regardless of the method, meticulous attention to detail and adherence to industry standards are essential to prevent defects and ensure the final product's reliability.
Quality Control and Testing: Ensuring Reliability in PCB Manufacturing
Rigorous quality control and testing are indispensable in PCB manufacturing to guarantee that the final product aligns with the stringent specifications required for reliable electronic performance. These processes are designed to detect and rectify any manufacturing defects, ensuring that each PCB operates as intended and meets the highest standards of reliability and longevity.
The testing phase involves multiple stages, from initial visual inspections to sophisticated electrical and functional tests. Each type of test serves a unique purpose, contributing to a comprehensive evaluation of the manufactured PCB.
Below are key quality control and testing methods used in PCB manufacturing:
- Visual Inspection
A preliminary check for obvious defects such as misaligned layers, broken traces, or solder mask issues using manual or automated optical inspection (AOI) systems. - Electrical Testing
This involves continuity testing to confirm that each electrical connection is correctly established and that no shorts exist between traces, and impedance testing to verify signal integrity, which is critical for high-speed circuits. - Functional Testing
Testing the PCB's performance under operational conditions using either custom test fixtures or standard functional test setups, designed to verify the PCB’s functionality under normal operational conditions. - X-Ray Inspection
An advanced inspection technique used to examine internal structures like solder joints or internal layers, which are not visible with standard visual inspection methods, especially useful in detecting hidden defects such as voids in solder or misaligned internal layers. - Automated Optical Inspection (AOI)
This involves using cameras to scan the board for defects such as missing or misplaced components, solder bridges, and incorrect component orientation. This type of test often comes after reflow soldering and is effective at reducing defects caused during the assembly process.
These testing methods are crucial to ensure that the manufactured PCBs are ready for their intended applications and conform to the highest reliability standards, minimizing the risk of product failures, which can be costly and damaging to reputation.
Frequently Asked Questions about PCB Manufacturing
This section addresses common questions regarding PCB manufacturing, providing clear and concise answers to enhance understanding of the processes involved in creating printed circuit boards.
- What does PCB stand for in manufacturing?
PCB stands for Printed Circuit Board. It's a board made of non-conductive material with conductive pathways or traces on its surface that electrically connect electronic components. - What is the typical PCB manufacturing process?
The typical PCB manufacturing process involves several key steps: design, film plotting, etching, drilling, plating, soldermask application, silkscreen application, surface finishing, and finally, testing and quality control. Each step is critical in creating a functional and reliable PCB. - Are PCBs expensive to manufacture?
The cost of PCB manufacturing varies widely depending on factors such as the complexity of the design, the materials used, the quantity ordered, and the manufacturing technology employed. Simple single-layer boards are generally less expensive than complex multi-layer PCBs with specialized features. Volume orders often result in lower per-unit costs. - Who is a leading PCB manufacturer in the world?
The global PCB manufacturing landscape is quite diverse, with many reputable companies. Identifying a single 'leading' manufacturer depends on criteria such as volume, technology, and regional presence. Some prominent manufacturers include companies with a strong global footprint in Asia, Europe, and North America, constantly evolving to meet market demands for high-complexity PCBs. Researching current market reports and industry analysis would give the most up-to-date information. - How do I select the right PCB manufacturer for my project?
Choosing the right PCB manufacturer involves assessing your specific needs. Key factors to consider include the manufacturer's technology capabilities, lead times, pricing, quality control processes, customer service, and their experience with similar projects. Getting prototypes is also essential for verifying the quality and reliability of your designs before entering mass production. Reviewing customer feedback, certifications and samples are important steps in the selection process. - What are common PCB surface finishes and why are they important?
Common PCB surface finishes include HASL (Hot Air Solder Leveling), ENIG (Electroless Nickel Immersion Gold), and OSP (Organic Solderability Preservative). Surface finishes protect the copper traces from corrosion, ensuring good solderability of components, and thus enhance the reliability of the assembled board. - How can I reduce the cost of PCB manufacturing?
To reduce PCB manufacturing costs, consider simplifying the design, standardizing component choices, optimizing the board size and layout, and increasing order volumes. Negotiating with manufacturers and choosing appropriate materials can also lead to cost savings. It's essential to find the right balance between cost reduction and maintaining the required performance and reliability of the board.
Understanding the nuances of PCB manufacturing is essential for any electronics project. From meticulous design to precise fabrication, every step plays a crucial role in the final performance and reliability of the product. By choosing the right materials, processes, and manufacturer, you can ensure that your PCB is manufactured to the highest standards, resulting in a high-performing and durable electronic device. As technology advances, so too will the process of PCB manufacturing, always striving for better, smaller, and more efficient solutions.
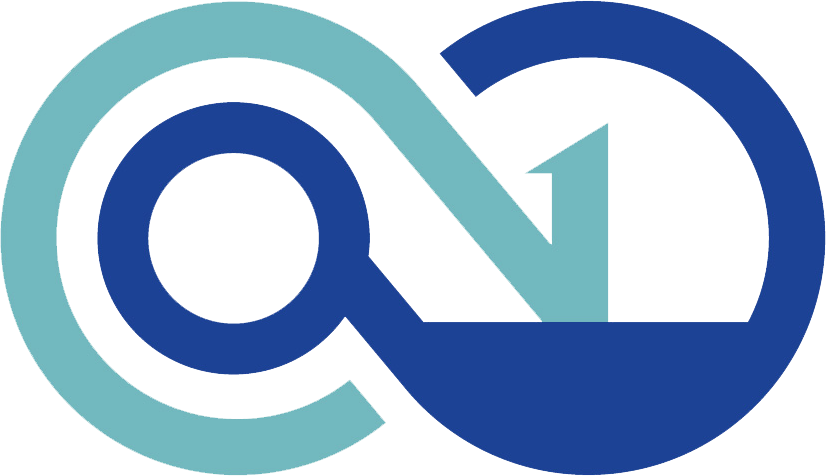