Top Automotive PCB Manufacturers: Choosing the Right Partner
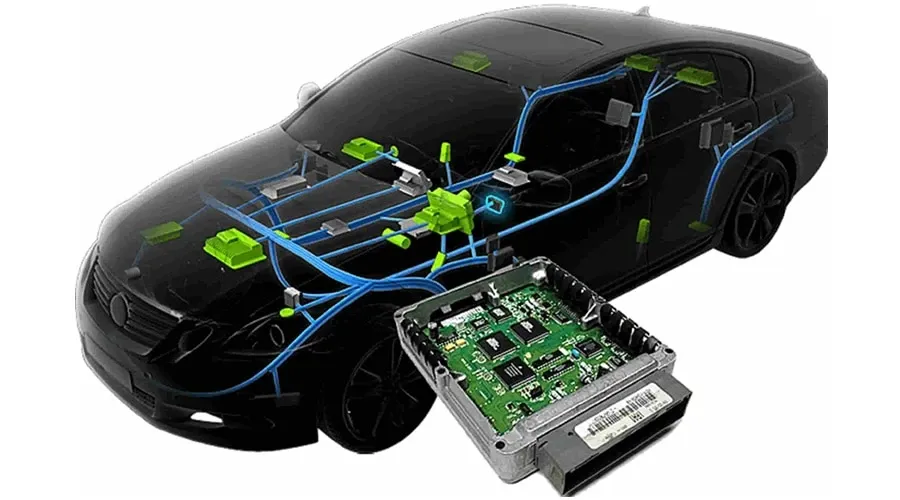
The automotive industry is undergoing a rapid transformation, with electronics playing an increasingly vital role. From advanced driver-assistance systems (ADAS) to infotainment and electric vehicle powertrains, reliable Printed Circuit Boards (PCBs) are the backbone of automotive innovation. Selecting the right automotive PCB manufacturer is crucial for ensuring the performance, durability, and safety of these critical systems. This article explores key considerations and profiles some of the leading automotive PCB manufacturers shaping the future of car electronics.
Understanding the Demands of Automotive PCBs
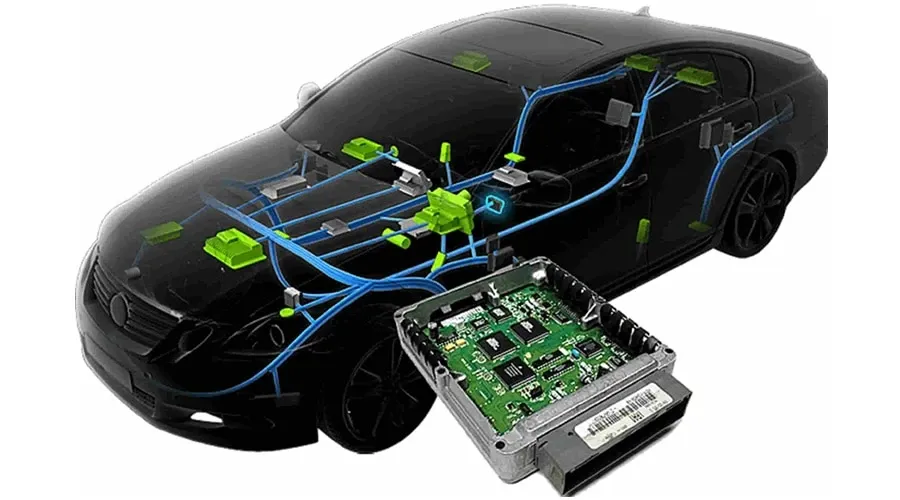
Automotive printed circuit boards (PCBs) operate in uniquely challenging environments, demanding exceptional reliability and performance. These PCBs are not merely electronic components; they are integral to the safety and functionality of modern vehicles. They must consistently perform under extreme conditions, such as fluctuating temperatures, constant vibrations, and exposure to moisture and corrosive substances.
The automotive industry's stringent requirements necessitate specialized manufacturing processes and materials. Unlike PCBs used in consumer electronics, automotive PCBs must adhere to higher quality standards and rigorous testing protocols to ensure long-term durability and operational integrity.
Challenge | Impact on PCBs | Required Solution |
---|---|---|
Extreme Temperatures (-40°C to 150°C) | Material degradation, solder joint failure, and thermal stress. | High-Tg materials, robust thermal design, and specialized solder alloys. |
Vibration and Mechanical Shock | Component fatigue, solder joint cracking, and board delamination. | Reinforced board materials, advanced mounting techniques, and vibration dampening. |
Humidity and Moisture | Corrosion, electrochemical migration, and insulation breakdown. | Conformal coatings, corrosion-resistant materials, and hermetic sealing. |
Chemical Exposure (oils, solvents) | Material degradation and electrical failures. | Chemical-resistant materials and protective coatings. |
Electromagnetic Interference (EMI) | Signal degradation, system malfunction, and interference with other electronics. | Shielding layers, proper grounding, and controlled impedance routing. |
Key Criteria for Selecting Automotive PCB Manufacturers
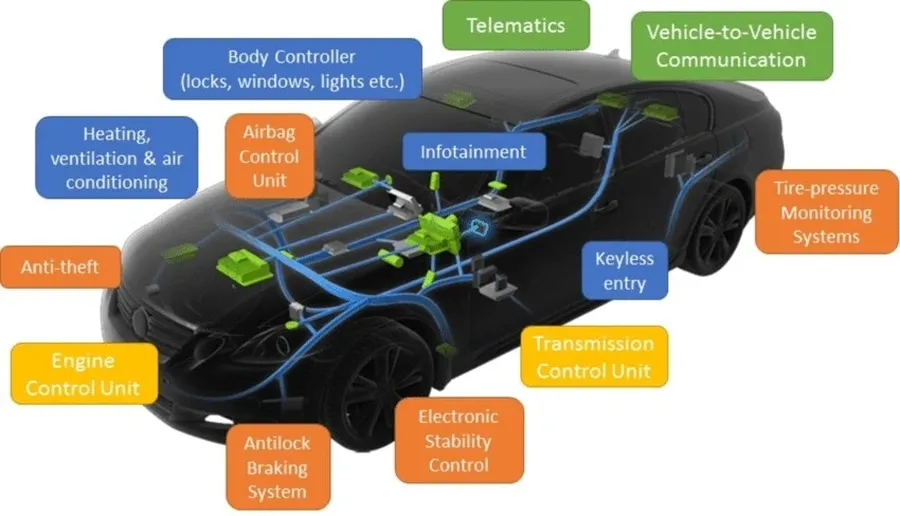
Selecting the right automotive PCB manufacturer is crucial for ensuring the reliability and performance of electronic systems in vehicles. This decision involves evaluating several critical factors that go beyond typical PCB manufacturing requirements, encompassing stringent quality standards, advanced technical capabilities, and robust production capacity.
Criteria | Description | Importance |
---|---|---|
Certifications (ISO/TS 16949) | Ensures adherence to automotive industry quality management standards, demonstrating a commitment to consistent quality and process control. | Mandatory for automotive supply chain qualification, assures compliance with rigorous quality protocols. |
Material Expertise (High-Tg, PTFE) | Capability to handle advanced materials that withstand high temperatures and harsh conditions, essential for automotive applications. | Critical for PCB durability and reliability in extreme environmental conditions. High-Tg materials resist deformation at higher temperatures; PTFE offers superior electrical performance at high frequencies. |
Advanced Technology (HDI, Embedded Components) | Proficiency in producing high-density interconnect (HDI) PCBs and integrating embedded components for compact and complex automotive electronics. | Enables miniaturization and higher functionality integration, crucial for modern automotive systems such as ADAS and infotainment. |
Volume Production Capacity | Ability to meet high-volume production demands without compromising quality or delivery timelines. | Ensures timely delivery and scalability, critical for large-scale automotive production. |
Testing and Validation | Comprehensive testing protocols and validation methods to ensure PCBs meet functional and performance specifications. | Reduces the risk of early failures in the field, ensuring product safety and reliability. |
Design For Manufacturability (DFM) | Strong DFM capabilities to optimize PCB layouts, reducing production costs and minimizing errors. | Facilitates smoother manufacturing and higher yields, reducing production costs and improving overall quality. |
Profiles of Leading Automotive PCB Manufacturers
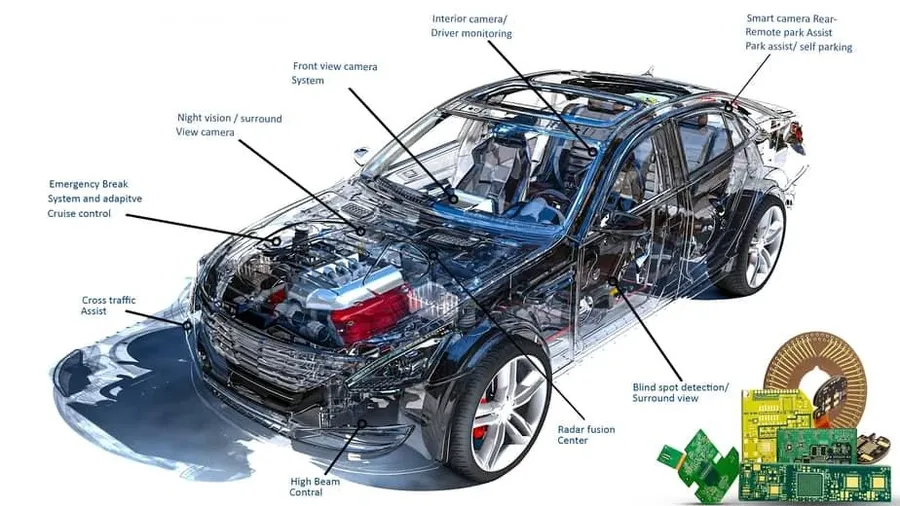
The automotive sector demands the highest levels of reliability and performance from its electronic components. This has led to the emergence of specialized PCB manufacturers, known for their expertise and experience in this area. This section highlights some key players in the automotive PCB market, focusing on their technological capabilities, strengths, and industry track records.
Manufacturer | Strengths | Technology Focus | Experience |
---|---|---|---|
TTM Technologies | High-mix, high-volume production, global footprint | HDI, rigid-flex, complex multilayer PCBs | Extensive experience in automotive, aerospace, and defense industries |
Sanmina | Global manufacturing and supply chain, strong engineering services | Advanced materials, embedded components, System-in-Package (SiP) | Significant experience in automotive, medical, and industrial sectors |
AT&S | Specialized in high-end PCBs, global production network | HDI, embedded components, high-frequency PCBs | Major supplier to automotive, industrial, and medical markets |
Würth Elektronik | Extensive catalog, strong R&D capabilities, global presence | Standard and custom PCBs, wide range of materials | Long-standing history in electronics, serving diverse industries including automotive |
Multek | Focus on high-volume manufacturing, global facilities | Rigid, flex, and rigid-flex PCBs, automotive-grade materials | Established presence in the automotive, consumer electronics, and industrial markets |
PCB Manufacturing Technologies for Automotive Applications
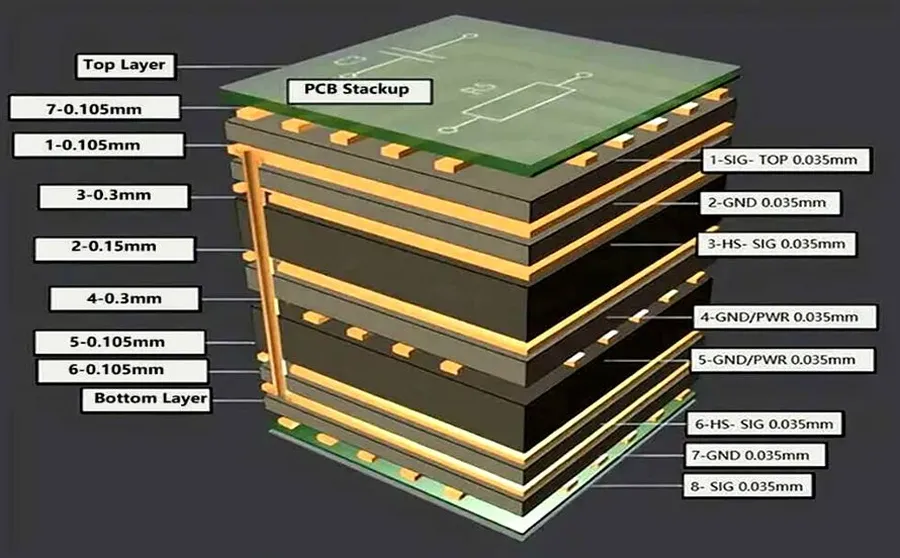
The automotive industry's relentless pursuit of enhanced safety, performance, and connectivity has driven the evolution of PCB manufacturing technologies. These technologies are pivotal for implementing advanced driver-assistance systems (ADAS), infotainment, and powertrain controls, requiring PCBs that are not only robust but also highly functional.
PCB Technology | Description | Automotive Application | Key Advantages |
---|---|---|---|
Multi-layer PCBs | PCBs with three or more conductive layers separated by insulating materials. | Engine control units (ECUs), transmission control, advanced driver-assistance systems (ADAS). | High component density, increased functionality, and improved signal routing capabilities. |
Rigid-Flex PCBs | Combine rigid and flexible circuit boards into one unit. | Infotainment systems, dashboards, sensors and camera modules. | Reduce weight, enhance space utilization, and increase design flexibility. |
High-Frequency PCBs | Designed to operate at high frequencies using materials with low dielectric loss. | Radar, LiDAR, telematics and high-speed data communication modules. | Enable high-speed data transmission, reduce signal loss, and minimize signal interference |
HDI (High Density Interconnect) PCBs | Features finer lines and spaces, microvias, and high connection density. | Advanced driver assistance systems, autonomous driving platforms, and infotainment systems. | Allows compact designs with complex functionalities. |
Embedded Component PCBs | Passive or active components are embedded within the layers of the PCB. | Power electronics modules, sensor interfaces, and high-density control units. | Increased space efficiency, improved reliability, and enhanced thermal management. |
The Importance of PCB Material Selection in Automotive

The selection of appropriate materials for automotive PCBs is paramount due to the extreme operating conditions they must endure. These conditions include high and low temperature fluctuations, significant vibration, high humidity and chemical exposure. The integrity and longevity of automotive electronics depend critically on the correct choice of materials, thus ensuring long-term reliability and performance.
Material | Description | Typical Automotive Application | Advantages | Disadvantages |
---|---|---|---|---|
FR-4 | A widely used fiberglass-epoxy laminate. It is the workhorse material for PCBs. | Less critical automotive control modules, sensors in mild environments | Cost-effective, readily available, good mechanical properties. | Limited thermal performance, susceptible to moisture absorption. |
High-Tg Epoxy | Epoxy laminate with a higher glass transition temperature (Tg), offering superior thermal performance. | ECU's, under-the-hood electronics where higher operating temperature exist. | Better high-temperature performance, improved long-term reliability. | Higher cost than FR-4, may require different processing techniques. |
PTFE (Teflon) | Fluoropolymer with excellent electrical and thermal properties. | Radar systems, high-frequency communication modules | Exceptional high-frequency performance, low dielectric loss, excellent thermal stability. | Expensive, more difficult to process, requires specialized design techniques. |
Ceramic Substrates | Inorganic materials, offering excellent thermal and mechanical properties. | High-power applications, LED modules, extreme temperature sensors. | Superior thermal conductivity, excellent mechanical strength, low thermal expansion. | High cost, difficult to machine, may require specialized assembly techniques. |
The correct material selection ensures long-term reliability, reducing the risk of field failures, which can have significant safety implications in automotive applications. The choice of material is a delicate balance between performance requirements and cost considerations and understanding the trade-offs is essential for effective design.
Cost Considerations and Supply Chain Reliability for Automotive PCBs
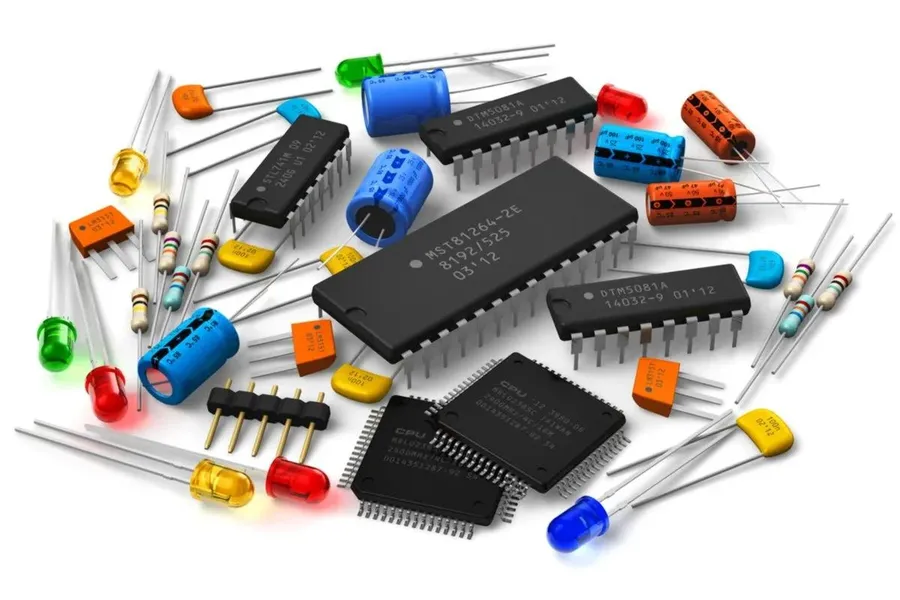
Selecting an automotive PCB manufacturer involves a critical balance between cost and quality, as these components are vital to vehicle safety and performance. Transparent pricing and robust supply chain partnerships are crucial to mitigate production risks and ensure a consistent supply of reliable PCBs. The automotive industry's strict requirements demand that cost optimization never compromise quality.
The goal is to secure high-quality, reliable PCBs within budget, avoiding potential production delays due to unforeseen supply chain issues. This requires a proactive approach to manufacturer selection, considering not only the initial cost but also the long-term implications on production efficiency and product reliability.
Factor | Description | Impact |
---|---|---|
Initial Cost | The per-unit price of PCBs. | Direct impact on product budget; may lead to choosing lower-quality components if solely focused on cost. |
Quality | Conformity to automotive standards (e.g., IATF 16949) and performance requirements. | Impacts long-term reliability, safety, and overall product performance. Compromising quality can lead to higher costs in the long run due to failures. |
Supply Chain Reliability | The manufacturer's capacity to consistently deliver PCBs on time and in the required volumes. | Ensures uninterrupted production schedules. Disruptions can result in costly delays and missed deadlines. |
Pricing Transparency | Clear and predictable pricing structure with no hidden fees. | Allows accurate budgeting and avoids unexpected financial burdens. |
Partnership | The level of collaboration and communication with the manufacturer. | Promotes better responsiveness, problem-solving, and adaptability to unforeseen issues. |
Automotive PCB Design Best Practices
Designing Printed Circuit Boards (PCBs) for automotive applications demands a rigorous approach to ensure reliability, safety, and performance in harsh operating environments. This section outlines essential best practices for automotive PCB design, focusing on signal integrity, thermal management, and electromagnetic compatibility (EMC), all while prioritizing safety and reliability.
- Signal Integrity
Maintain signal integrity through controlled impedance routing, minimizing signal reflections and ensuring clean data transmission. Use differential pairs and ground planes to reduce noise and crosstalk. Simulation tools should be used to analyse signal behaviour and perform impedance matching. - Thermal Management
Effective thermal management is critical for automotive PCBs which are often exposed to extreme temperatures. Use thermal vias to transfer heat to heat sinks, and consider using materials with high thermal conductivity. Design for airflow and consider component placement to optimize heat dissipation. - Electromagnetic Compatibility (EMC)
Automotive PCBs must comply with stringent EMC standards. Implement proper grounding techniques and use shielding to prevent electromagnetic interference (EMI). Utilize filter circuits to reduce noise emissions. Compliance testing should be included as part of the development cycle. - Material Selection
Choose materials that can withstand the operating environment. High glass transition temperature (Tg) laminates are essential for PCBs that need to operate in hot environments, while materials such as PTFE are required for high-frequency applications like radar. Considerations should be given to CTE matching to improve reliability. - Component Placement
Carefully position components to minimize potential interference and improve heat dissipation. High-current components should be placed near the power source, while sensitive components should be placed away from noise sources. Ensure sufficient space between components for repair purposes. - Layer Stack-Up
A well-planned layer stack-up is vital for performance and noise reduction. Utilize a multi-layer PCB design with dedicated power and ground planes to minimize impedance and noise. Arrange signal layers to reduce cross-talk between adjacent traces and plan stack up around controlled impedance requirements. - Safety and Reliability
Incorporate safety features such as redundant paths and protection circuits. Conduct rigorous testing and validation to ensure the board will be reliable in all operating conditions. Follow automotive design guidelines such as IPC-A-600 and AEC-Q100 standards.
Frequently Asked Questions About Automotive PCBs and Manufacturers
This section addresses common questions about automotive PCBs, their manufacturing, and the standards they must adhere to, providing clarity for engineers and procurement professionals.
- Who are the leading automotive PCB manufacturers?
Several manufacturers excel in automotive PCB production, including TTM Technologies, Sanmina, and others. The 'best' manufacturer depends on specific project requirements, such as technology demands, volume, and geographic location. Evaluating their certifications, material expertise, and production capacity is crucial. - What are the critical quality standards for automotive PCBs?
Automotive PCBs must adhere to stringent quality standards, primarily IATF 16949 certification, which ensures consistent quality management systems and processes tailored for the automotive industry. Additionally, standards like IPC-A-600 and IPC-A-610 are often used as references for manufacturing quality and acceptability of PCBs. - What is the automotive-grade PCB standard?
There isn't one single 'automotive-grade' standard, but rather a combination of certifications and materials that meet automotive demands. It includes high-reliability materials like high-Tg FR-4 or ceramics, rigorous quality control processes (IATF 16949), and the ability to withstand extreme temperatures, vibrations, and humidity. The IPC standards also form a key reference. - What role do PCBs play in automotive applications?
PCBs are the backbone of all automotive electronic systems, from engine control units (ECUs) and infotainment systems to advanced driver-assistance systems (ADAS) like radar and LiDAR. They facilitate electrical connections and provide physical support for the electronic components, allowing various vehicle functions to operate efficiently and reliably. - What specific materials are required for automotive PCBs?
Automotive PCBs often require high-performance materials due to the harsh operating environment. Common materials include FR-4 with a higher Tg (glass transition temperature), PTFE (Teflon) for high-frequency applications (like radar), and ceramic substrates for high-power components. The selection depends on temperature, frequency, and mechanical stress requirements. - What is the importance of material selection for automotive PCBs?
Proper material selection is crucial for long-term reliability of automotive PCBs, especially given the harsh environmental conditions. Materials must withstand high temperatures, vibrations, moisture, and chemical exposure, all of which could degrade the PCB over time. Choosing the right materials directly affects the durability and life span of the PCB and, consequently, the vehicle’s electronic systems. - How does one ensure a reliable supply chain for automotive PCBs?
A reliable supply chain for automotive PCBs involves choosing manufacturers with strong capacity, robust production planning, and transparency in pricing. Multiple sourcing options, strategic partnerships, and detailed contracts can help mitigate risks and avoid production delays. Performing regular supplier audits is essential to maintaining quality standards.
Choosing the right automotive PCB manufacturer is crucial to ensuring reliability, performance, and compliance with strict industry standards. This involves careful assessment of factors such as their expertise, certifications, technology, materials, and supply chain reliability. As the automotive industry continues to innovate, partnering with a reputable and experienced manufacturer will remain paramount for success in the competitive market. Working with the right automotive PCB manufacturers will ensure that your car electronics are safe and reliable. The future of driving depends on it.
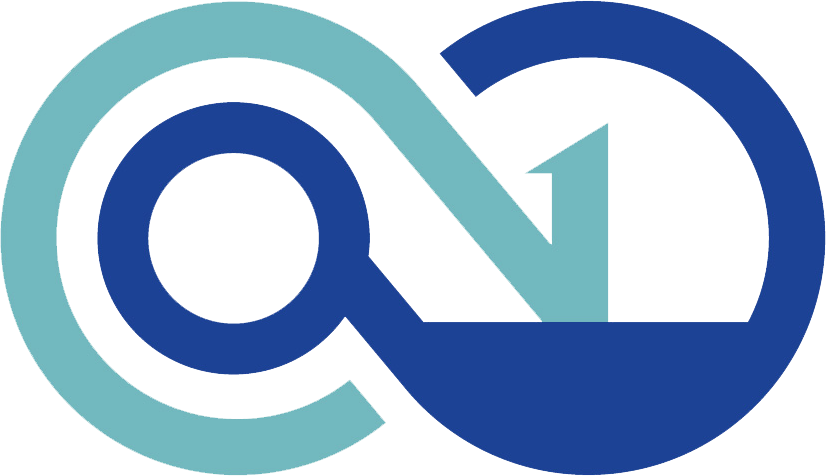