Top FR4 Manufacturers: Choosing the Right Partner for Your PCB Needs
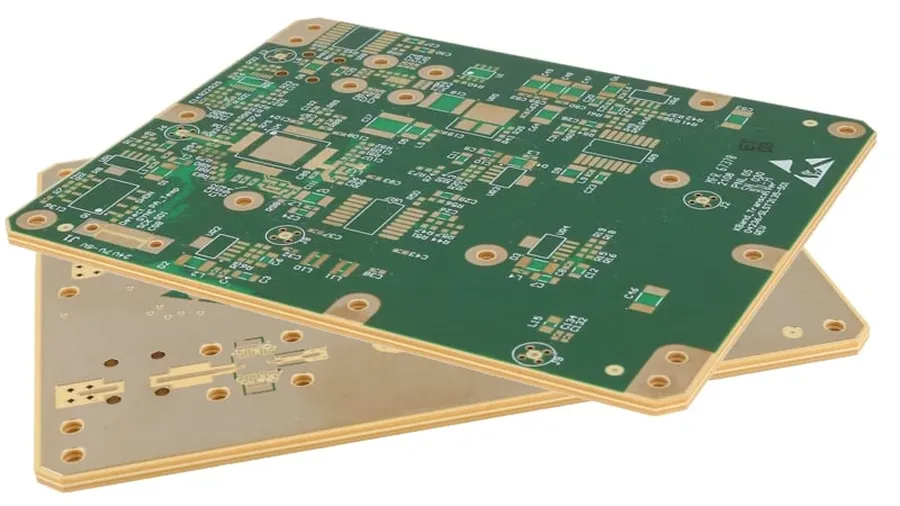
In today's fast-paced tech world, printed circuit boards (PCBs) are the backbone of nearly every electronic device, from smartphones to complex industrial machinery. FR4, a versatile and cost-effective material, is a common choice for PCB production. Choosing the right FR4 manufacturers is essential for the quality and reliability of your project. This article dives into the world of FR4 PCB manufacturing, guiding you through the critical factors, top suppliers, and frequently asked questions to empower your decision-making process, and to ensure your designs become reliable, top performing products.
What is FR4 Material and Why is it Important for PCB Manufacturing?
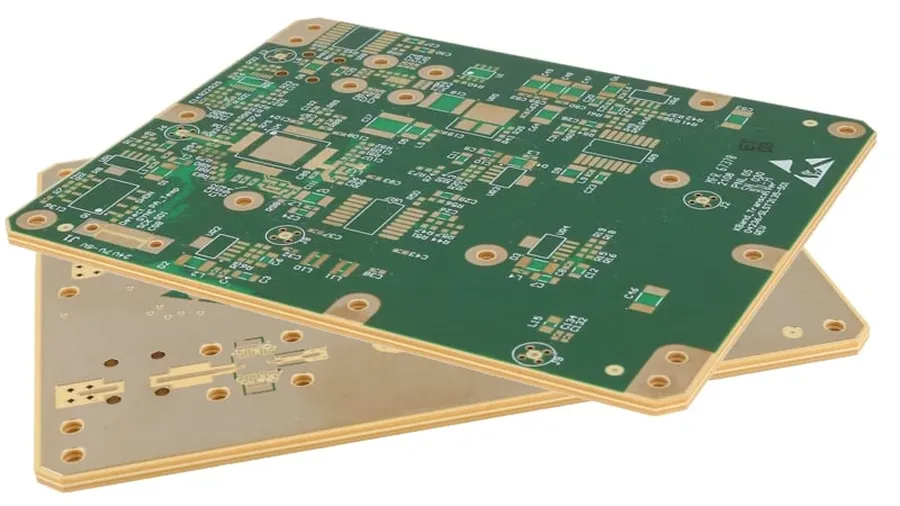
FR4, a ubiquitous material in printed circuit board (PCB) manufacturing, is a composite material primarily composed of woven fiberglass cloth impregnated with a flame-retardant epoxy resin binder. Its widespread adoption stems from a balance of desirable characteristics, including high electrical insulation properties, considerable mechanical strength, and good thermal performance, making it exceptionally well-suited for a vast array of electronic applications.
The composition of FR4 provides a robust foundation for PCB construction. The fiberglass cloth acts as a reinforcement, enhancing the material's mechanical strength and dimensional stability. The epoxy resin matrix, on the other hand, provides electrical insulation, chemical resistance, and thermal stability, ensuring the reliable operation of electronic circuits mounted on the board. This synergistic combination of properties is essential for maintaining signal integrity and the physical robustness required in electronic devices.
FR4's key characteristics make it invaluable for PCB manufacturing:
- Electrical Insulation
FR4 exhibits excellent electrical insulation properties, preventing shorts and signal leakage between conductive layers and components on the PCB. This is crucial for ensuring the intended functionality of electronic circuits. - Mechanical Strength
The fiberglass reinforcement provides substantial mechanical strength, allowing the board to withstand handling, assembly processes, and operational stresses without fracturing or significant deformation. - Thermal Stability
FR4 maintains dimensional stability over a wide range of temperatures, an essential trait for reliable performance in varying operational environments where thermal expansion and contraction can occur. - Cost-Effectiveness
FR4 is readily available and relatively inexpensive, making it a commercially viable material for high-volume production and cost-sensitive electronic applications. - Chemical Resistance
FR4 is generally resistant to common chemicals used in PCB manufacturing and operational environments, further increasing its reliability and longevity.
Key Considerations When Selecting FR4 Manufacturers
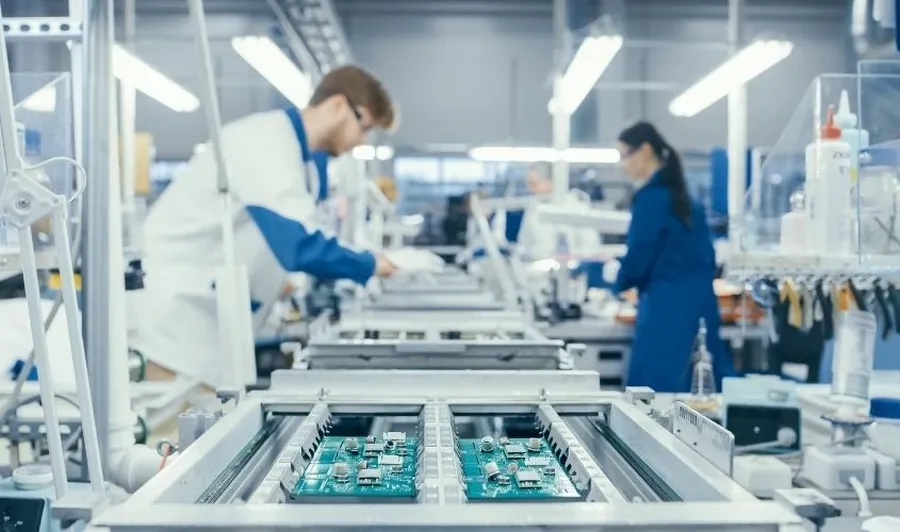
Selecting the right FR4 manufacturer is crucial for ensuring the quality and reliability of your printed circuit boards (PCBs). Several factors should be carefully considered to make an informed decision, impacting both the cost and performance of your final product. These factors encompass manufacturing capabilities, adherence to industry standards and certifications, the quality of materials used, the time taken to complete your order, and the pricing structure.
- Manufacturing Capabilities
Assess if the manufacturer has the equipment and expertise to handle your specific PCB requirements, including layer count, board thickness, minimum trace width and spacing, and hole sizes. Advanced capabilities such as laser drilling, blind/buried vias, and impedance control may also be necessary depending on the complexity of your design. - Certifications and Compliance
Ensure that the manufacturer holds relevant certifications such as ISO 9001, ISO 14001, and UL certifications. Compliance with industry standards ensures that their manufacturing processes and products meet stringent quality and environmental standards. These certifications are critical for product safety and reliability. - Material Quality
FR4 material can vary in quality; it's essential to confirm the grade of FR4 used by the manufacturer, this should be backed up with certificates of conformance. Inferior FR4 may exhibit poor dielectric properties, inconsistent thickness, or lower thermal resistance, impacting the long-term performance and reliability of your PCBs. - Turnaround Time
Evaluate the typical turnaround time offered by the manufacturer. For prototyping and urgent projects, fast turnaround times are vital. However, be aware that expedited services might come at an increased cost. Ensure that delivery timelines align with your project schedule without compromising quality. - Pricing Structure
Compare pricing structures across different manufacturers, but avoid choosing solely based on the lowest quote. Look for a balance between cost and value, considering all factors such as quality, certifications, and turnaround time. A thorough cost-benefit analysis is crucial for your project's financial planning.
Top FR4 Manufacturers Worldwide: A Comparative Analysis
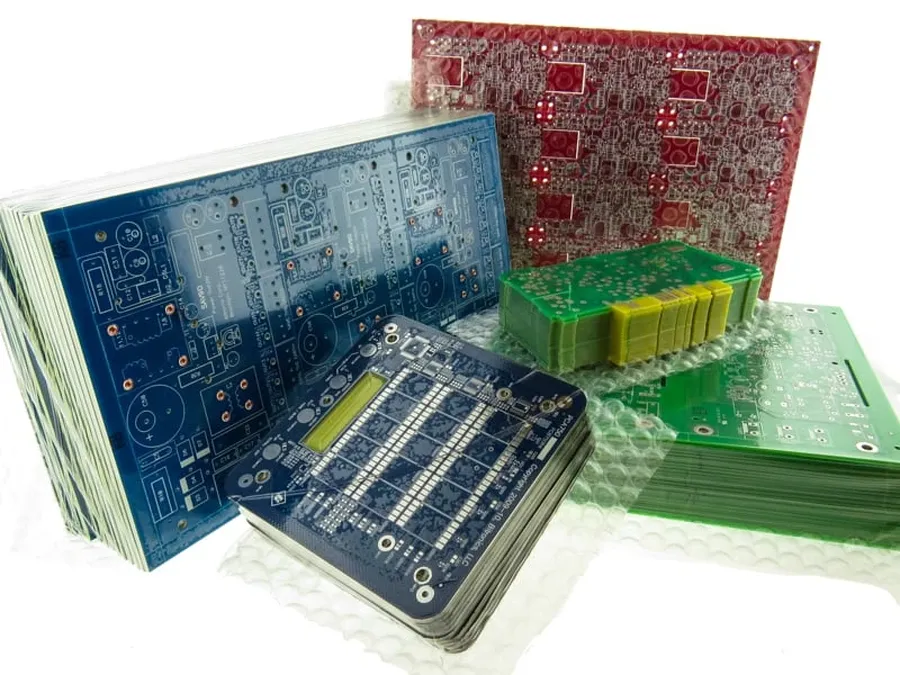
Selecting the right FR4 manufacturer is crucial for ensuring the quality and reliability of printed circuit boards (PCBs). This section provides a comparative analysis of top FR4 manufacturers globally, highlighting their strengths, specialties, and geographical reach to assist in making informed decisions. This is not an exhaustive list but is designed to provide a starting point for your selection process.
Manufacturer | Strengths | Specialties | Geographical Reach | Certifications |
---|---|---|---|---|
Kingboard Chemical Holdings Ltd. | High-volume production, vertically integrated supply chain | Mass production of FR4 laminates and PCBs | Global, with major operations in Asia | ISO 9001, ISO 14001 |
Taiwan Union Technology Corporation (TUC) | Advanced material research, wide range of FR4 types | High-performance FR4 for various applications | Asia, Europe, North America | ISO 9001, IATF 16949 |
Ventec International Group | High-reliability FR4 materials, strong technical support | Specialty FR4 for demanding environments | Global, with manufacturing and distribution in key regions | ISO 9001, AS9100 |
Isola Group | Extensive material portfolio, innovative solutions | High-speed and high-frequency FR4 materials | Global presence with multiple manufacturing locations | ISO 9001, ISO 14001 |
Elite Material Co., Ltd (EMC) | Large production capacity, cost-effective solutions | Standard FR4 materials for general applications | Primarily Asia, expanding globally | ISO 9001, ISO 14001 |
Nanya Plastics Corporation | Diversified product range, significant production volume | FR4 laminates, prepregs and PCB | Asia, with global sales network | ISO 9001, IATF 16949 |
Shengyi Technology Co., Ltd. | Leading supplier in China, rapid response capabilities | High Tg FR4 and halogen-free options | Asia and worldwide | ISO 9001, ISO 14001 |
FR4 Material Properties and Specifications
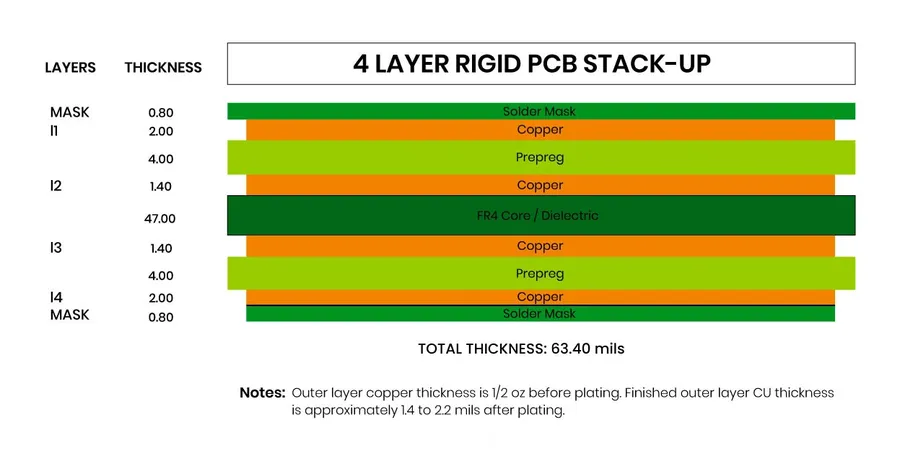
FR4, a composite material composed of woven fiberglass cloth with an epoxy resin binder, possesses a unique combination of properties that make it exceptionally suitable for printed circuit board (PCB) fabrication. These properties include a specific dielectric constant, thermal resistance, and mechanical strength, all of which play a critical role in the performance and reliability of the final product. Understanding these characteristics is crucial for engineers and designers when selecting FR4 for PCB applications, ensuring the material aligns with the design and performance requirements.
Property | Typical Value | Unit | Significance |
---|---|---|---|
Dielectric Constant | 4.2 - 4.8 | - | Affects signal propagation speed and impedance in circuits; lower values generally preferred for high-frequency applications. |
Dissipation Factor (Loss Tangent) | 0.015 - 0.025 | - | Indicates signal loss due to energy absorption by the material; lower values are better for signal integrity. |
Glass Transition Temperature (Tg) | 130-180 | °C | The temperature at which the material transitions from a rigid to a softened state; affects PCB reliability, particularly in elevated temperature environments. |
Thermal Conductivity | 0.2 - 0.3 | W/m·K | Measures the ability of FR4 to conduct heat; important for thermal management and heat dissipation in PCBs. |
Tensile Strength | 200 - 350 | MPa | Indicates material's resistance to being pulled apart; important for structural integrity and PCB durability. |
Flexural Strength | 250 - 400 | MPa | Indicates material's resistance to bending stress; relevant for flexible and rigid-flex PCBs. |
Water Absorption | 0.01% - 0.2% | % | The amount of moisture the material can absorb; impacts dielectric properties and dimensional stability in humid environments. |
Flammability Rating | UL94 V-0 | - | Indicates the material's ability to self-extinguish in the presence of a flame; safety requirement for most electronic devices. |
FR4 PCB Manufacturing Process Overview
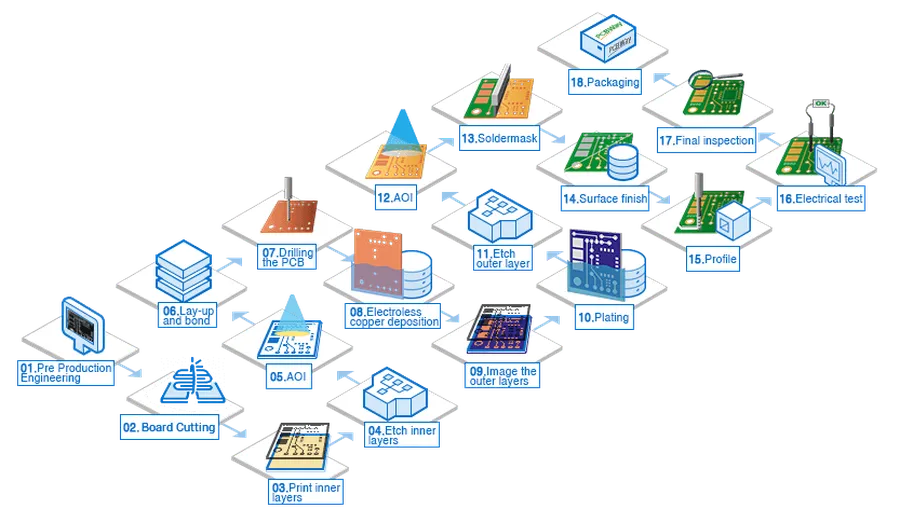
The fabrication of FR4 PCBs is a complex, multi-stage process that transforms raw materials into functional circuit boards. This process encompasses a series of precise steps, each critical to the performance and reliability of the final product. From design implementation to shipment, each stage requires strict adherence to quality standards.
- Design and CAM (Computer-Aided Manufacturing)
The process begins with the PCB design using CAD software. This design is then translated into CAM files, which guide the manufacturing equipment. This stage includes defining layers, traces, pads, and vias. - Material Preparation
FR4 base material, typically a glass-reinforced epoxy laminate, is prepared according to the specifications of the design. This may include cutting the material to the appropriate size and cleaning the surfaces to ensure proper adhesion. - Inner Layer Imaging
For multilayer PCBs, the inner layers are patterned. A photosensitive resist is applied to the copper-clad laminate, exposed to UV light through a photomask, and developed. The unwanted copper is then etched away, leaving the desired traces and pads. - Layer Lamination
The patterned inner layers are stacked together with prepreg (partially cured epoxy resin) layers and copper foils. This stack-up is then subjected to high heat and pressure in a hydraulic press to bond all layers. Lamination is critical for ensuring structural integrity and electrical insulation. - Drilling
Holes for vias and component leads are drilled using precise CNC drilling machines. These holes are necessary to establish electrical connections between different layers and mount components. - Electroless Copper Plating
A thin layer of copper is deposited on the walls of the drilled holes and over the entire surface of the board. This provides the conductive path needed for through-hole connections. - Outer Layer Imaging
Similar to inner layer processing, a photosensitive resist is applied, exposed, and developed to define the traces on the outer layers. Following this the unwanted copper is etched away, leaving the final circuit pattern. - Solder Mask Application
A solder mask, a protective layer, is applied to all board surfaces except where components will be soldered. This prevents solder bridges and provides insulation. - Surface Finish
A surface finish, such as HASL (Hot Air Solder Leveling), ENIG (Electroless Nickel Immersion Gold), or OSP (Organic Solderability Preservative), is applied to the exposed copper pads to enhance solderability and protect against oxidation. - Silkscreen Printing
Silkscreen printing is applied, adding component references, logos, and other markings to aid in assembly and identification. - Electrical Testing
Each PCB is electrically tested using flying probe testers or bed-of-nails fixtures to ensure continuity and proper function. This step verifies that the board meets all design specifications. - Final Inspection and Shipment
The boards undergo a final visual inspection to check for defects. Approved boards are then cleaned, packaged, and shipped.
Frequently Asked Questions About FR4 PCBs
This section addresses common inquiries regarding FR4 PCBs, providing clear and concise answers to help users understand this essential material and its applications in circuit board manufacturing. The following questions delve into manufacturing origins, leading suppliers, material limitations, and general best practices.
- Who manufactures FR4 material?
FR4 is not made by a single entity but rather is a standard designation for a composite material that meets certain specifications. Numerous chemical companies and material suppliers around the world produce FR4 base materials. These materials are then used by PCB manufacturers to create circuit boards. Key material suppliers include companies like Isola Group, Panasonic, and Nan Ya Plastics, among others, which offer a range of FR4 variations with slightly different properties. - Who are the largest PCB manufacturers in the USA?
The PCB manufacturing landscape in the USA is quite competitive, with several companies holding significant market share. Some of the larger US-based PCB manufacturers known for their capacity, technology, and advanced capabilities include TTM Technologies, Sanmina, and Viasystems. Note that market positions can fluctuate and it's beneficial to review recent market reports for the most up-to-date rankings. - Who is considered the best PCB manufacturer, and how should you evaluate your options?
Defining the 'best' PCB manufacturer is subjective and depends on specific project requirements. Factors such as technology capabilities (e.g., HDI, multi-layer), material expertise, certifications (e.g., ISO, AS9100), and customer service play crucial roles. A thorough evaluation of potential manufacturers should include assessments of sample quality, compliance with manufacturing standards, and their ability to meet specific needs within your production volume and budget. It's also important to consider a manufacturer's expertise with FR4 or other materials necessary for your project. - What are the disadvantages of using FR4 in PCB manufacturing?
While FR4 is a versatile and widely used material, it has limitations. One significant drawback is its moderate thermal conductivity, making it less suitable for high-power applications where heat dissipation is critical. Additionally, FR4 can have higher dielectric losses at higher frequencies compared to specialized materials. Its relatively high moisture absorption can also be a concern in humid environments. Lastly, FR4 is not eco-friendly. For applications that demand superior thermal, electrical, or environmental resistance, alternative materials may be more appropriate. - What is the typical lifespan of FR4 PCB?
The lifespan of an FR4 PCB is largely influenced by its operating environment and the conditions it is exposed to. In normal ambient conditions, an FR4 PCB can last for many years, often exceeding a decade or more with proper handling and operation. Factors that could shorten its lifespan include exposure to extreme temperatures, high humidity, chemical contamination, and excessive electrical or mechanical stress. Proper design and usage of the PCB significantly influence its longevity. - How does FR4 compare to other PCB materials in terms of cost?
FR4 is generally considered one of the most cost-effective materials for PCB manufacturing due to its wide availability and ease of processing. While other materials like polyimide or PTFE (Teflon) offer superior electrical or thermal properties, they come at a significantly higher price point. The cost-effectiveness of FR4 is a major reason for its popularity in a broad range of applications, making it a preferred choice where performance requirements do not mandate specialized materials.
How to Ensure Quality Control When Working with FR4 Manufacturers
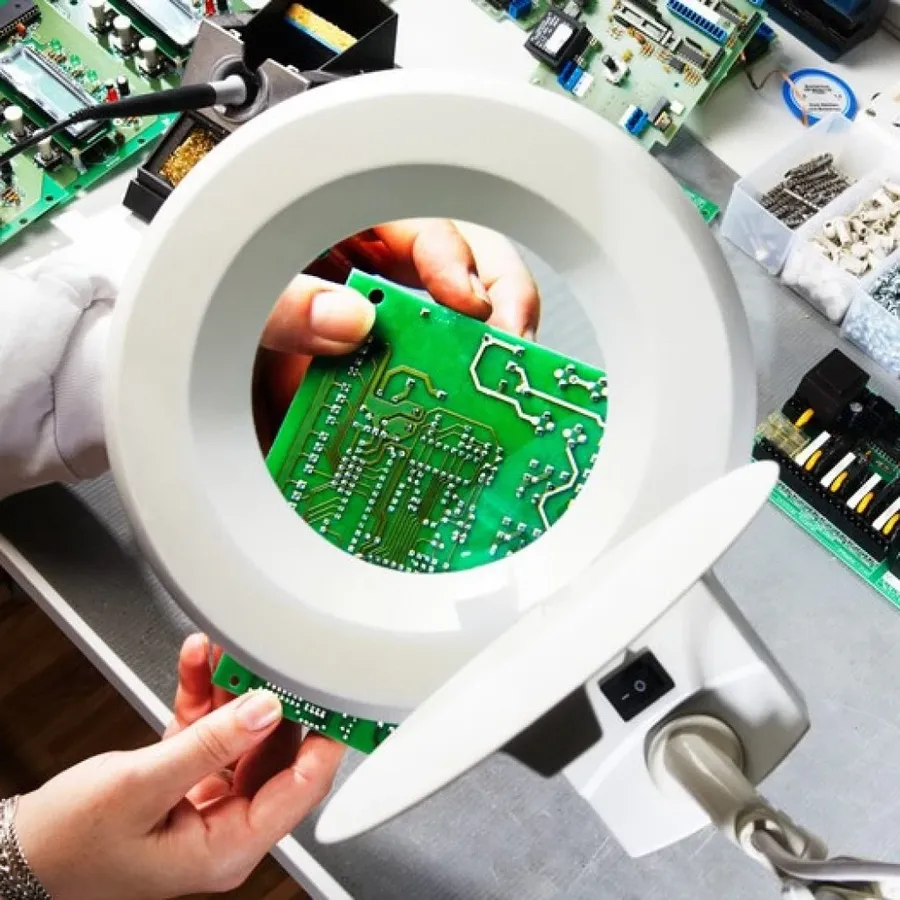
Ensuring quality control when working with FR4 manufacturers is crucial for producing reliable and functional PCBs. This involves implementing rigorous checks throughout the manufacturing process, from initial design reviews to final product inspection, to minimize defects and ensure the end product meets required specifications.
- Pre-Production Design Review:
Conduct a thorough review of your PCB design files with the manufacturer before production. This includes checking for design rule violations, ensuring correct layer stack-up, and confirming that all critical dimensions and clearances are within acceptable tolerances. This is a critical step in preventing manufacturing issues that may arise from a poorly designed board. - Material Verification:
Verify that the FR4 material used by the manufacturer meets your required specifications. Request material certifications and datasheets, particularly if specific electrical, thermal, or mechanical properties are required. Ensure the material thickness and composition are as specified in your design documents. - First Article Inspection (FAI):
Request a first article inspection of a small batch of PCBs before mass production begins. FAI includes a complete inspection and verification of all parameters, such as dimensions, surface finish, copper plating thickness, drilling accuracy, and electrical performance. This will confirm that the manufacturer’s process meets your specifications before committing to volume production. - In-Process Monitoring and Inspection:
Implement continuous monitoring and inspection during the manufacturing process. This includes monitoring critical parameters such as temperature control during lamination, precise control of chemical concentrations during etching, and careful control of the plating process for copper thickness. Regular sampling should be conducted and documented to ensure process control. - Electrical Testing:
Perform electrical testing on each board. This includes continuity and isolation tests, as well as any other tests relevant to your design such as high-voltage testing or signal integrity assessments. Test reports should be generated and analyzed to identify and rectify potential problems. This testing ensures the circuit functionality before delivery. - Final Visual Inspection:
Conduct a thorough final visual inspection of the completed PCBs before shipment. This inspection is to verify the surface finish, solder mask quality, component placement accuracy, and other parameters. Verify the dimensions and alignment of the boards to ensure fit into final applications. This acts as a final safeguard against defects. - Documentation and Traceability:
Ensure that the manufacturer maintains complete documentation for every process, including material lot numbers, process parameters, and test results. Traceability is crucial in identifying the source of any quality issue and enables efficient corrective actions. This step ensures that quality issues can be traced and addressed efficiently.
Future Trends in FR4 PCB Manufacturing and Materials
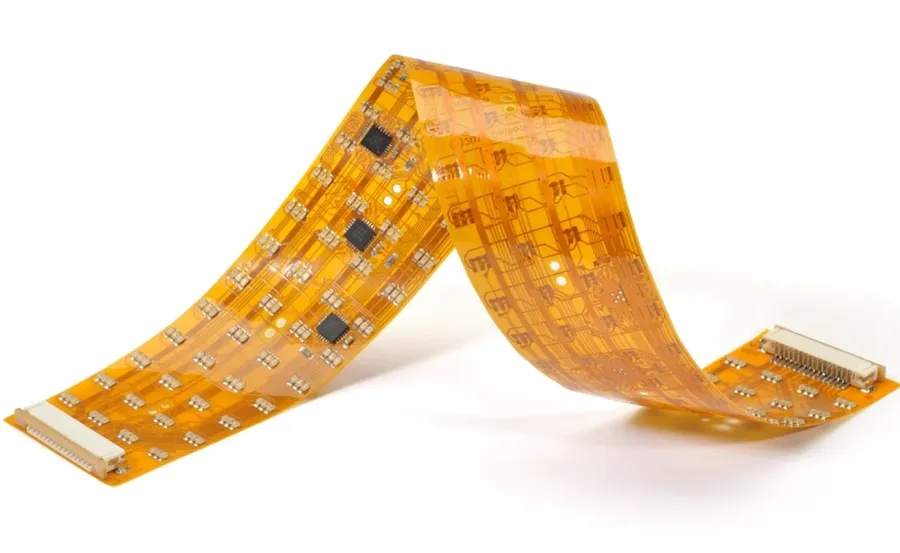
The FR4 PCB industry is continuously evolving, driven by the demand for higher performance, increased sustainability, and cost-effectiveness. Future trends are focusing on advancements in materials, manufacturing processes, and environmental considerations to meet the increasing complexities and demands of electronic devices.
- Eco-Friendly FR4 Alternatives
Growing environmental concerns are driving research into bio-based and recyclable alternatives to traditional FR4. These materials aim to reduce the carbon footprint associated with PCB production, offering options like plant-based resins and fiber reinforcements to achieve comparable or superior performance while being more sustainable. - Advanced Additive Manufacturing Techniques
Additive manufacturing, also known as 3D printing, offers a streamlined approach for PCB fabrication that can significantly reduce material waste and enables the creation of highly complex board designs. This is expected to enable faster prototyping, more customized board designs and ultimately, more efficient FR4 PCB manufacturing. - Enhanced Thermal Management Solutions
With devices generating increasing amounts of heat, innovative thermal management techniques such as embedded heat sinks and thermally conductive FR4 materials are being developed. These solutions will improve the reliability and longevity of electronic devices by addressing heat-related issues more effectively. - Smart Manufacturing and Automation
The incorporation of Artificial Intelligence (AI) and the Internet of Things (IoT) is transforming FR4 PCB manufacturing, leading to more efficient production, predictive maintenance, and improved quality control. Automated systems and data analysis can optimize processes, reduce human error and lower costs. - High-Performance FR4 Composites
Research into new FR4 composite materials is focused on enhancing mechanical strength, improving electrical properties, and increasing thermal capabilities of the material. These advancements will enable the use of FR4 in more demanding applications.
Selecting the right FR4 manufacturers is vital for ensuring the success of your PCB projects. By carefully considering manufacturing capabilities, material quality, and turnaround times, you can optimize your supply chain for reliable FR4 PCB production. As FR4 continues to be a cornerstone in electronics manufacturing, staying informed about the latest trends and technologies in this field will be key for continuous improvement. And with the best [fr4 manufacturers], your projects will always be in capable hands, ensuring reliable, high performance designs.
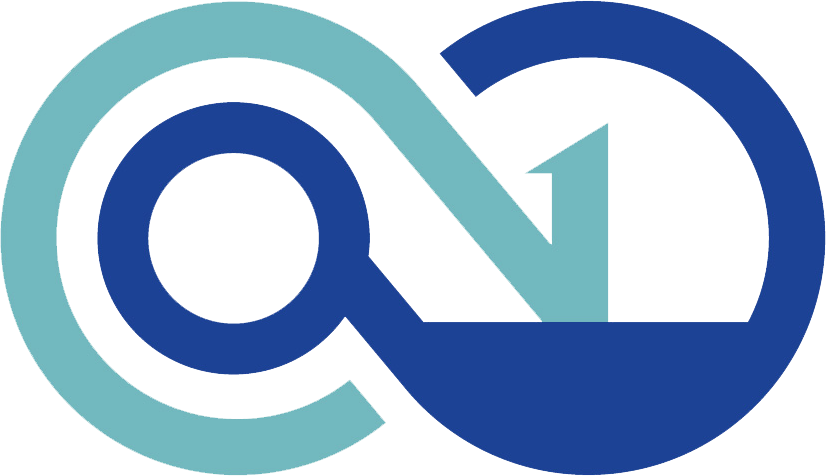