Top IMS PCB Manufacturer: Choosing the Right Partner for Your Thermal Needs
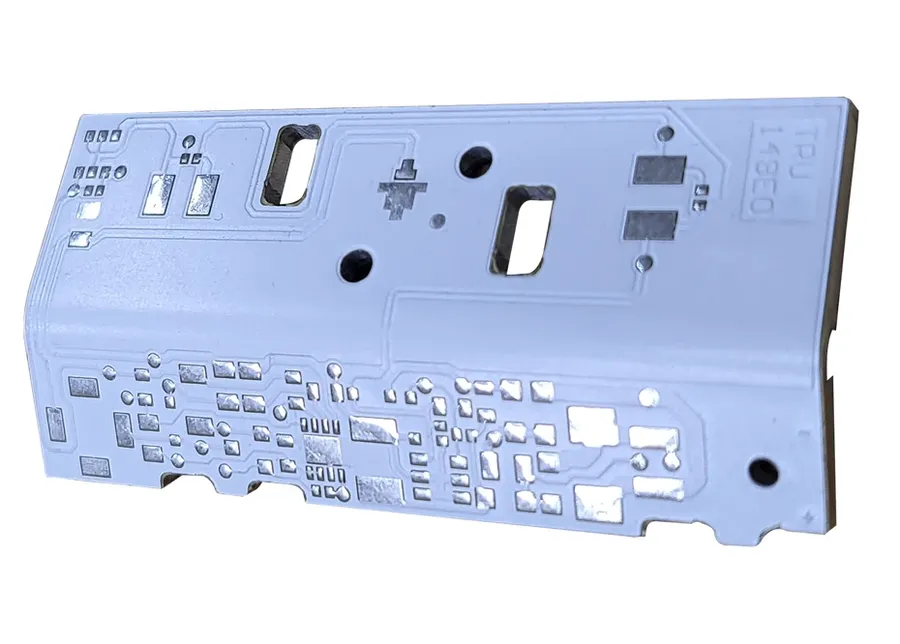
In today's electronics landscape, thermal management is critical, especially for high-power applications. Insulated Metal Substrate (IMS) PCBs, offered by specialized IMS PCB manufacturers, offer superior heat dissipation compared to traditional FR4 PCBs. This article delves into the world of IMS PCBs, exploring their benefits and guiding you to selecting the right IMS PCB manufacturer for your project, enhancing the reliability and performance of your electronic products.
What is an IMS PCB?
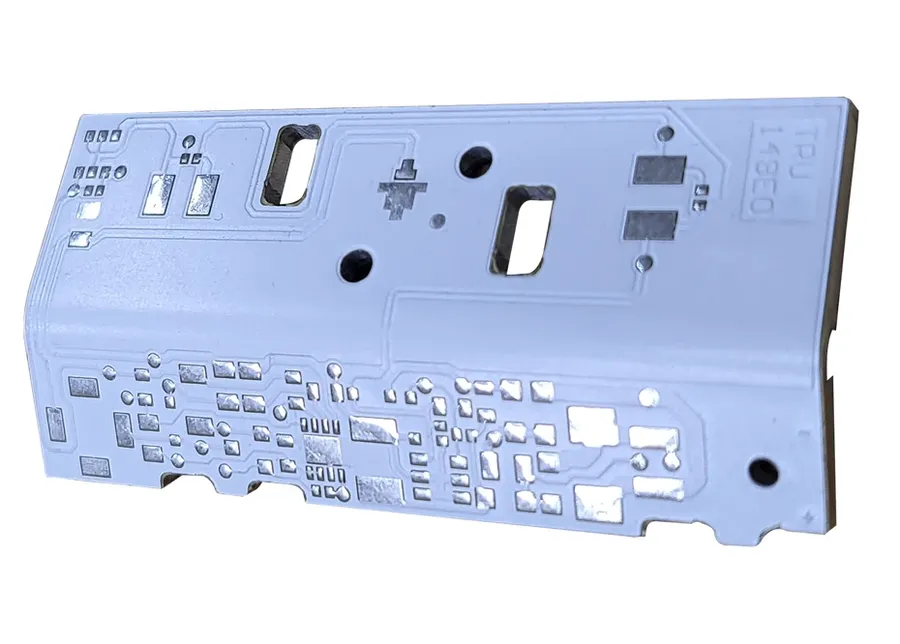
An Insulated Metal Substrate (IMS) PCB, also known as a metal core PCB (MCPCB), is a specialized printed circuit board engineered for superior thermal management. Unlike traditional FR-4 PCBs, which use a non-conductive fiberglass composite, IMS PCBs feature a metal base, typically aluminum or copper, which acts as a heat spreader. This construction allows for efficient heat dissipation, making IMS PCBs ideal for high-power electronic applications.
The fundamental structure of an IMS PCB consists of three primary layers:
- Metal Base
This layer provides the structural foundation and thermal conductivity. Common materials include aluminum and copper, selected for their high thermal transfer capabilities and mechanical strength. Aluminum is more common due to its cost-effectiveness, while copper offers superior thermal performance. - Dielectric Layer
A thin layer of thermally conductive, electrically insulating material is applied to the metal base. This layer ensures electrical isolation between the metal base and the copper circuitry while facilitating efficient heat transfer. Various dielectric materials are used, each with specific thermal and electrical properties, impacting the overall performance of the IMS PCB. Key properties include thermal conductivity, dielectric strength, and operating temperature range. - Copper Circuit Layer
This layer, similar to that found in conventional PCBs, consists of etched copper traces and pads that create the electrical circuitry. The copper layer is where the electronic components are mounted and interconnected.
The selection of materials in an IMS PCB is critical and depends on the application requirements. For example, high-power applications may require copper bases and high-performance dielectrics, while less demanding applications may use aluminum bases and standard dielectrics.
Advantages of Using IMS PCBs
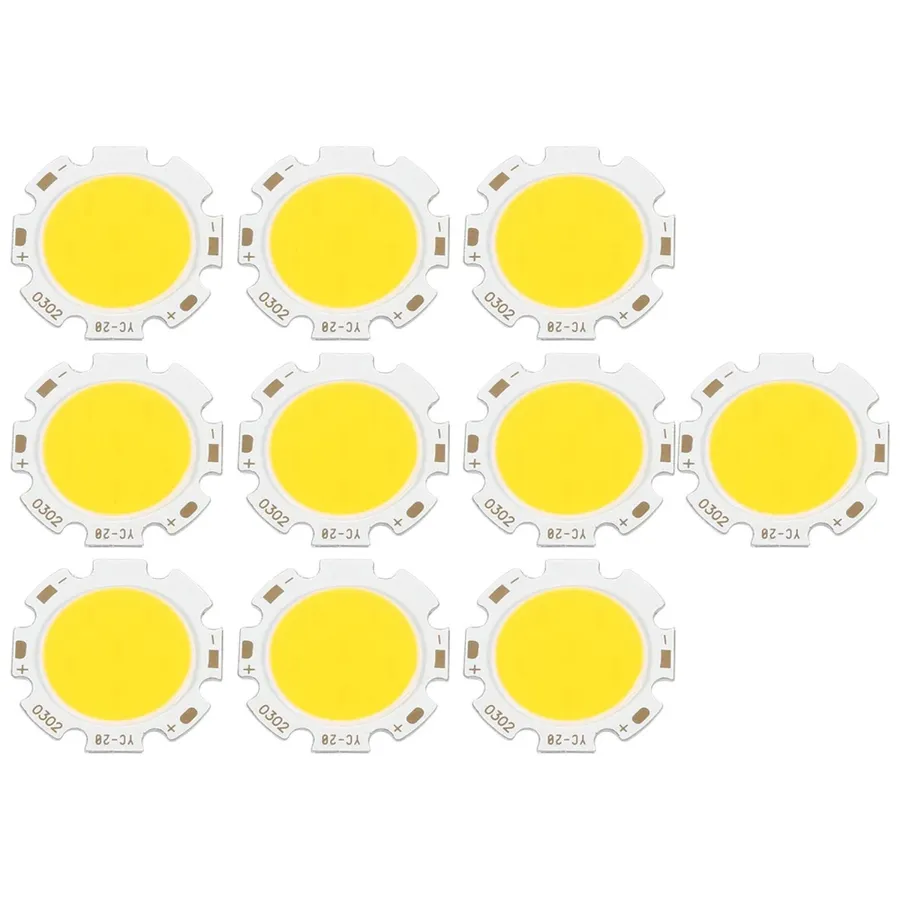
Insulated Metal Substrate (IMS) PCBs offer significant advantages over traditional FR4 PCBs, primarily in thermal management, mechanical robustness, and dimensional stability, making them ideal for high-power and thermally demanding applications. The inherent structure of an IMS PCB, with its metal core, provides an efficient heat dissipation path, mitigating the risk of component overheating and improving the overall reliability of electronic devices.
- Superior Thermal Conductivity
The metal base, typically aluminum or copper, in IMS PCBs exhibits significantly higher thermal conductivity compared to FR4. This allows for efficient heat transfer away from heat-generating components, reducing the risk of thermal failure and improving device performance. - Enhanced Heat Dissipation
IMS PCBs facilitate superior heat dissipation due to the direct thermal path from components to the metal substrate, which acts as a heat sink. This is crucial in applications such as high-power LEDs and power electronics where substantial heat generation is unavoidable. - Increased Mechanical Strength
The presence of a metal core in IMS PCBs provides greater mechanical strength and rigidity, making them more durable and resistant to bending or warping. This is particularly beneficial in environments that require robust and reliable electronic components. - Improved Dimensional Stability
IMS PCBs exhibit superior dimensional stability compared to FR4 PCBs, especially under thermal stress. This means they maintain their shape and size with less deformation, which is essential for precision applications where tight tolerances are required. - Longer Component Lifespan
By effectively managing heat, IMS PCBs help extend the operational lifespan of electronic components. Lower operating temperatures reduce the thermal stress on components, leading to increased longevity and reliability. - Reduced Risk of Component Failure
The enhanced thermal management properties of IMS PCBs contribute to a lower risk of component failure due to overheating. This minimizes downtime and maintenance costs for critical applications.
Key Applications of IMS PCBs
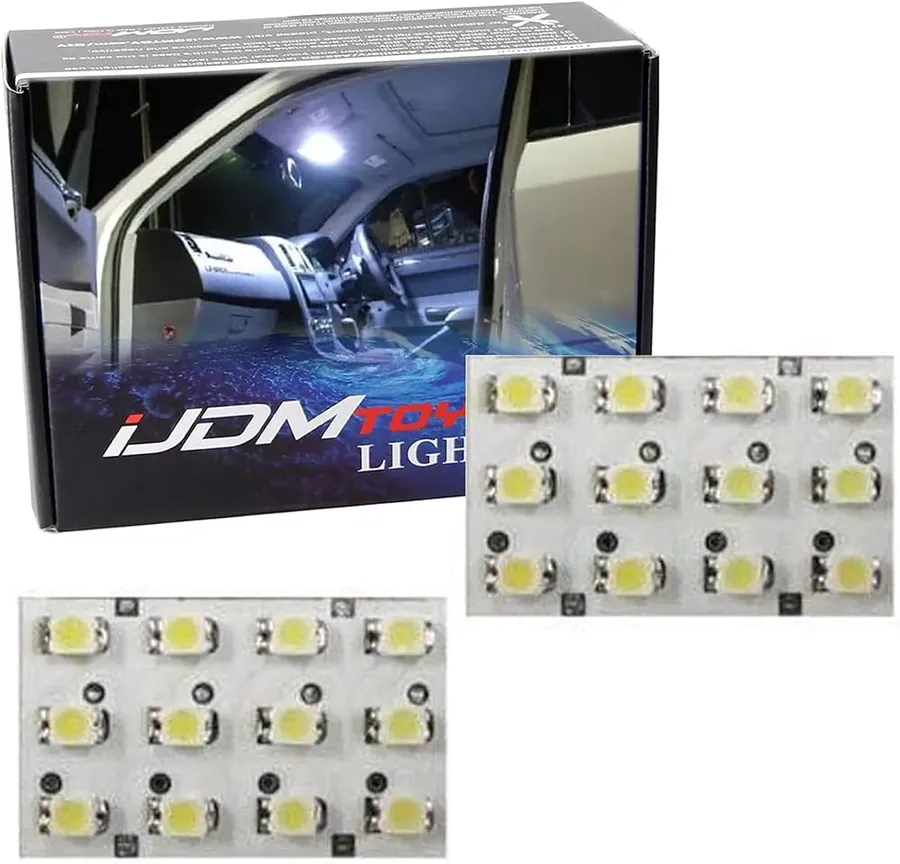
Insulated Metal Substrate (IMS) PCBs are crucial in applications requiring effective heat management due to their superior thermal conductivity. Their ability to dissipate heat efficiently makes them essential components in high-power and thermally demanding electronic systems.
- LED Lighting
IMS PCBs are widely used in LED lighting applications, including streetlights, automotive lighting, and indoor lighting, to manage the heat generated by high-power LEDs, ensuring their longevity and optimal performance. - Power Electronics
In power electronics, IMS PCBs are used in power supplies, motor drives, and inverters, where high currents and voltages generate substantial heat. Their thermal efficiency helps prevent component failure and ensures the reliability of power systems. - Automotive Systems
IMS PCBs are increasingly used in automotive electronics such as engine control units (ECUs), lighting systems, and power steering, where temperature fluctuations and high power consumption demand robust thermal management solutions. - Industrial Control Systems
Industrial control systems, including robotics, automation equipment, and process control, also benefit from IMS PCBs in high-temperature environments to maintain the accuracy and stability of their electronic circuits. - Renewable Energy Technologies
In renewable energy sectors, such as solar inverters and wind turbine control systems, IMS PCBs provide essential heat dissipation, improving the efficiency and reliability of these critical components under heavy loads.
How to Choose an IMS PCB Manufacturer: Key Considerations
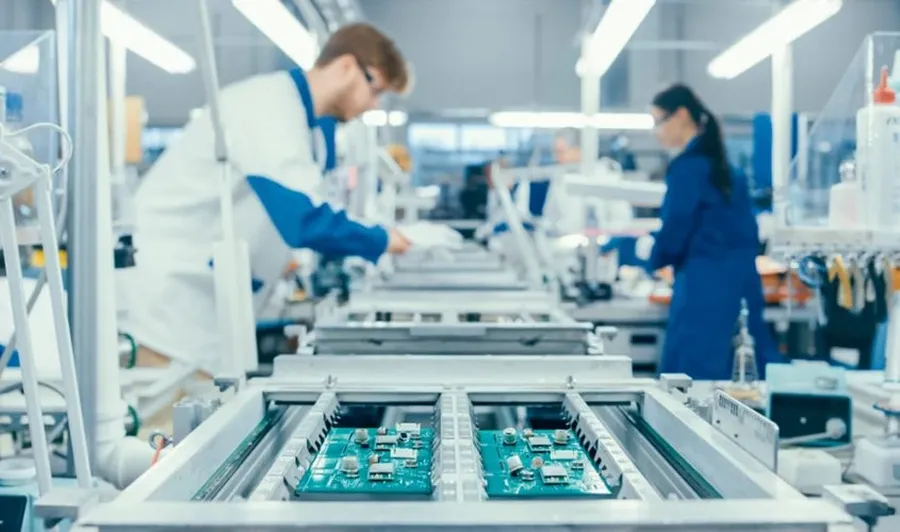
Selecting the right Insulated Metal Substrate (IMS) PCB manufacturer is crucial for the success of any project requiring efficient thermal management. This decision should be based on a thorough evaluation of several key factors to ensure the chosen partner can meet your specific requirements, particularly for high-power applications.
- Experience and Expertise
Look for a manufacturer with a proven track record in producing IMS PCBs. Their experience will translate into fewer production issues and a better understanding of material behavior. Verify their experience with similar projects and material combinations. Longevity in the market often signifies a higher level of reliability and proficiency. - Certifications (ISO, UL)
Ensure the manufacturer holds relevant certifications such as ISO 9001 (Quality Management System) and UL certification for PCB manufacturing. These certifications guarantee adherence to quality standards and safety regulations, respectively. UL certification is especially important for products destined for specific markets where safety standards are strictly enforced. - Manufacturing Capabilities
Assess their production capabilities, including the range of materials they can process, layer counts, maximum board size, and precision capabilities. Ensure they are equipped with the latest technology for IMS fabrication, which includes precision machining for metal substrates, controlled dielectric coating processes, and accurate layer alignment. - Prototyping Services
A manufacturer that offers robust prototyping services will significantly speed up the development cycle. They should be able to produce small batches quickly for design validation, enabling you to test different design parameters and materials before mass production. Fast prototype turnaround is essential to accelerating your time to market. - Material Selection
The manufacturer should be knowledgeable about various IMS PCB materials, including aluminum, copper, and different dielectric options. They should provide guidance on selecting materials based on your project’s specific thermal, electrical, and mechanical requirements. Their insight into cost-performance trade-offs will contribute to optimized board design. - Turnaround Time
Evaluate their lead time for both prototypes and mass production. This is crucial for aligning your project timeline. Manufacturers with established processes and efficient supply chains can typically offer shorter lead times. Discuss delivery schedules and flexibility to accommodate potential changes. - Cost
While cost is a key consideration, it should not be the sole determining factor. Balance cost with the manufacturer’s capabilities, experience, and quality standards. Be wary of manufacturers offering extremely low prices, as this might indicate compromises in quality or materials. Request a detailed breakdown of costs and ensure transparency in pricing structure.
IMS PCB Materials: A Comparative Analysis
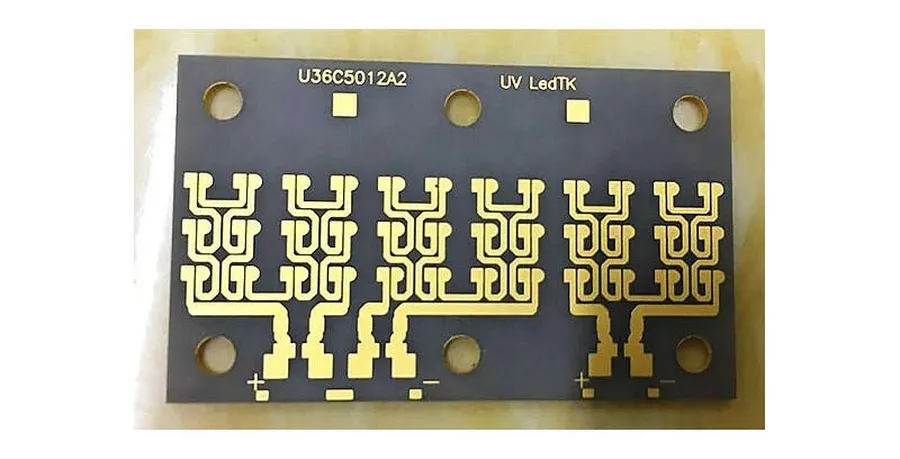
The selection of materials for Insulated Metal Substrate (IMS) PCBs is crucial to their performance, influencing thermal management, cost, and application suitability. This section provides a detailed comparison of common materials, emphasizing their thermal properties and application fit, presented in a structured table format for clear understanding.
Material | Thermal Conductivity (W/m·K) | Cost | Application Suitability | Key Considerations |
---|---|---|---|---|
Aluminum | 120-240 | Low to Moderate | General purpose, LED lighting, power electronics | Lightweight, good heat dissipation, widely available, standard base material |
Copper | 380-400 | Moderate to High | High-power applications, demanding thermal requirements | Excellent thermal conductivity, good mechanical strength, higher cost than aluminum |
Dielectric (Epoxy-based) | 0.2-0.4 | Low to Moderate | General purpose dielectric, lower-power applications | Standard dielectric, provides electrical insulation, cost-effective |
Dielectric (Polyimide-based) | 0.3-0.5 | Moderate to High | High-temperature and high-reliability applications | Higher temperature resistance, better long-term reliability, higher cost than epoxy |
Dielectric (Ceramic-filled) | 1-3 | High | High-power and high-temperature applications, demanding thermal performance | Superior thermal performance, increased material cost |
IMS PCB Design Considerations
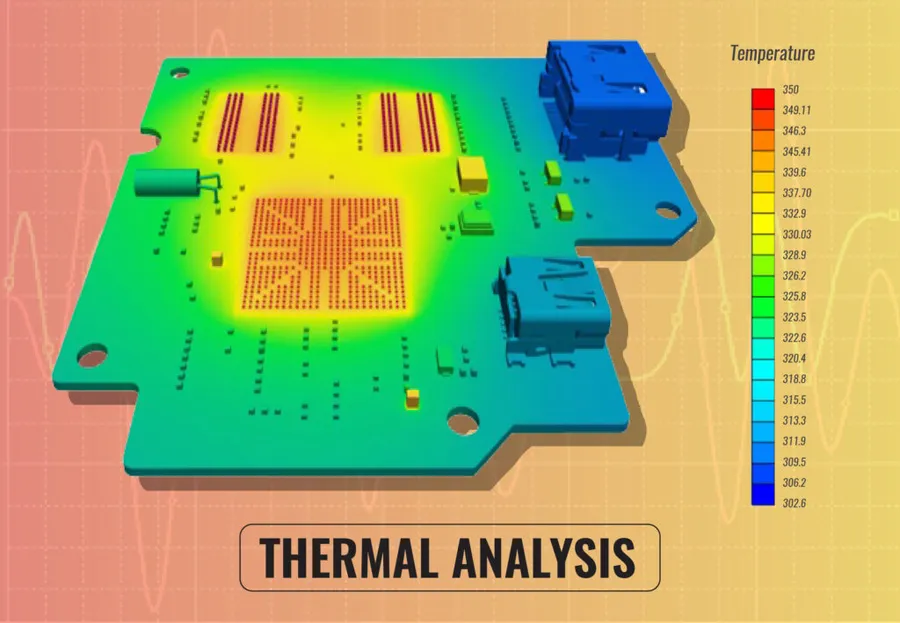
Designing Insulated Metal Substrate (IMS) PCBs requires careful attention to specific parameters that differ from traditional FR4 boards to ensure optimal thermal performance and reliability. Key aspects include trace width and spacing, via design, thermal pad placement, and layer stack-up, all of which directly impact the board's ability to dissipate heat and function correctly. Close collaboration with your IMS PCB manufacturer is essential during the design phase to optimize these parameters based on their expertise and capabilities.
- Trace Width and Spacing
Wider traces are generally preferred to increase the current carrying capacity and minimize heat buildup. The spacing between traces must also be sufficient to avoid thermal interference and short circuits, taking into account the specific current and voltage requirements of the application. Consult with your manufacturer for recommended trace widths based on your application needs. - Via Design
Vias in IMS PCBs play a dual role: electrical connection and thermal conduction. Vias should be placed strategically to facilitate efficient heat transfer from the components to the metal base. Multiple vias with larger diameters can be used for enhanced heat dissipation. The type of via, whether plated through-hole or blind/buried, can also influence thermal performance. - Thermal Pad Placement
Components that generate significant heat should have thermal pads directly connected to the metal base through vias. The size and shape of the thermal pads should be optimized to maximize the heat transfer surface area. Utilizing thermal vias beneath these pads enhances heat dissipation capabilities, especially for high-power applications. - Layer Stack-Up
The layer stack-up significantly impacts the thermal performance of IMS PCBs. The dielectric layer should be as thin as possible while maintaining adequate electrical insulation to minimize thermal resistance. The metal base material and its thickness also contribute to thermal performance; often aluminum or copper bases are used. Proper selection and design of stack-up will be beneficial for managing heat.
Frequently Asked Questions About IMS PCBs
This section addresses common queries about Insulated Metal Substrate (IMS) PCBs, offering clarity on their construction, applications, and distinctions from traditional FR4 PCBs. The intent is to provide a comprehensive understanding of IMS technology for users, guiding them through design, application, and manufacturing aspects.
- What exactly is a PCB in the context of IMS?
In IMS, the term PCB refers to the copper circuitry layer that is etched onto the dielectric layer. This patterned copper acts as the conductive path for electrical signals, similar to the function of a copper layer in a conventional PCB but with the added benefit of direct thermal dissipation via the metallic substrate. - What differentiates an IMS PCB from a standard FR4 PCB?
The fundamental difference lies in their base material: FR4 PCBs use a fiberglass-reinforced epoxy resin, while IMS PCBs utilize a metal base, typically aluminum or copper. This metallic substrate in IMS PCBs enables superior heat dissipation, making them ideal for high-power applications. FR4 PCBs, however, offer a lower cost for less demanding thermal applications. - What are the common applications for IMS PCBs?
IMS PCBs are essential in applications requiring efficient thermal management, such as LED lighting, power converters, automotive electronics (especially in LED headlights and power modules), industrial control systems, and renewable energy technologies (like solar panel inverters). Their ability to effectively dissipate heat is crucial in these sectors to ensure long-term operational reliability and performance. - Are there any design constraints unique to IMS PCBs?
Yes, designing with IMS PCBs requires attention to trace widths for adequate current handling, proper thermal via placement to maximize heat transfer to the metal base, and careful consideration of the dielectric material and its properties for optimal performance and reliability. The coefficient of thermal expansion differences between the metal base and other materials must also be factored in for dimensional stability. - What materials are typically used in the construction of an IMS PCB?
Typical materials include aluminum or copper for the metal base, a thermally conductive dielectric layer (often a ceramic-filled polymer) for electrical insulation and thermal transfer, and copper for the circuitry layer. The selection of materials is tailored based on the specific thermal requirements of the application and cost considerations. Aluminum is commonly used for its lightweight and cost effectiveness, while copper is preferred for highest thermal performance. - Can an IMS PCB be used for high-frequency applications?
While IMS PCBs are mainly used for thermal management, they can be designed for high-frequency applications by carefully selecting the dielectric material and optimizing the layer stack-up to control impedance and minimize signal loss. However, their primary advantage remains in thermal performance, which may make them less optimal for purely high-frequency applications when compared to specifically designed RF boards. - How does the choice of IMS PCB material affect cost?
The cost of an IMS PCB is significantly influenced by the materials used. Copper substrates generally command higher prices than aluminum due to higher material cost and enhanced thermal conductivity. Similarly, the type and thermal performance of the dielectric material impacts the overall cost, with high thermal conductivity materials generally having a higher cost. Material choice should align with both technical requirements and budget constraints.
The Future of IMS PCB Technology
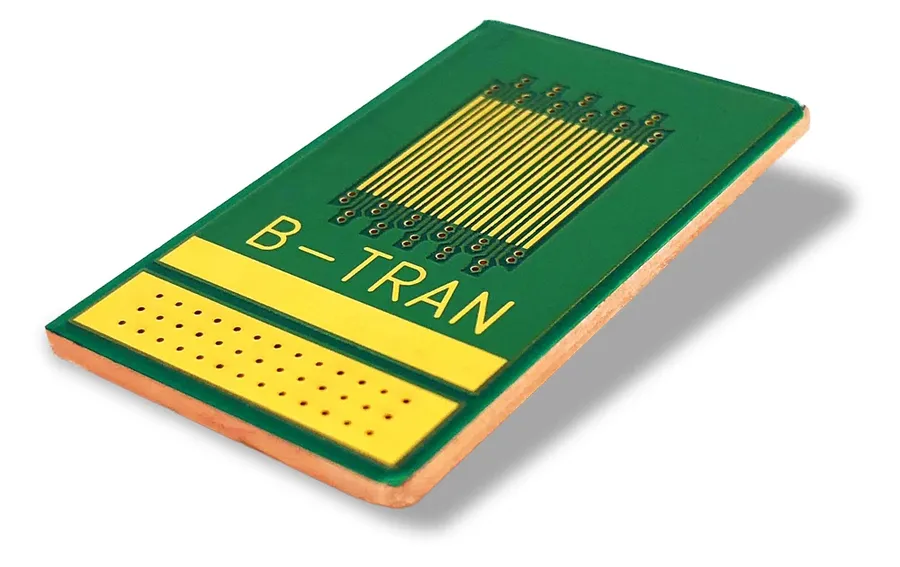
The trajectory of Insulated Metal Substrate (IMS) PCB technology is marked by continuous innovation, driven by the ever-increasing demands for enhanced thermal management, higher power densities, and greater reliability in electronic devices. The future of IMS PCBs will likely involve the introduction of novel materials, more sophisticated manufacturing processes, and the adoption of new design methodologies.
- Emerging Materials
Research and development efforts are focused on exploring materials with superior thermal conductivity and dielectric properties. This includes advancements in ceramic-filled polymers, metal matrix composites, and nano-materials. These materials aim to further enhance heat dissipation while maintaining electrical insulation and mechanical integrity. The aim is to reduce reliance on traditional materials like aluminum and copper to achieve greater performance. - Advanced Fabrication Techniques
Manufacturers are adopting more precise and efficient manufacturing processes, such as additive manufacturing (3D printing) and laser ablation. These techniques enable the creation of more complex and customized PCB designs with greater accuracy, reduced waste, and faster production times. Such innovation allows for higher design flexibility and reduced cost for complex IMS PCB layouts. - Integration and Miniaturization
The trend toward miniaturization in electronic devices requires IMS PCBs with higher component densities and finer features. Future IMS PCBs will likely incorporate integrated components and advanced packaging techniques to reduce overall size and improve functionality. This is particularly important for applications in portable electronics and high-density power modules. - Intelligent Thermal Management
Future IMS PCBs are expected to incorporate smart thermal management systems, such as integrated thermal sensors and adaptive cooling technologies. These systems will enable real-time monitoring and adjustment of heat dissipation, ensuring optimal performance and reliability under varying operating conditions, and also help prevent device failures and extend their lifespan. - Sustainable Manufacturing Practices
With increasing environmental concerns, sustainable manufacturing practices are becoming a major focus. Future IMS PCB manufacturing will prioritize the use of eco-friendly materials and processes, such as recycling and waste reduction, contributing to lower environmental impact and improved regulatory compliance. The focus will be on creating greener alternatives to conventional PCB production. - Role of Leading IMS PCB Manufacturers
Leading IMS PCB manufacturers are at the forefront of this innovation, heavily investing in R&D to pioneer new materials and manufacturing techniques. They are working to push the limits of IMS PCB performance, offering customized solutions for the most demanding applications and actively engaging with researchers and designers to refine their offerings.
Choosing the right IMS PCB manufacturer is crucial for the success of your thermally demanding projects. By understanding the benefits of IMS PCBs and carefully evaluating potential manufacturers, you can ensure your product's reliability and performance. Remember, a trusted IMS PCB manufacturer can provide not only high-quality boards, but also valuable insights and support throughout your product development journey. The future of high-performance electronics depends on continual advancements in thermal management, making IMS PCB manufacturers like us, essential partners in technological innovation.
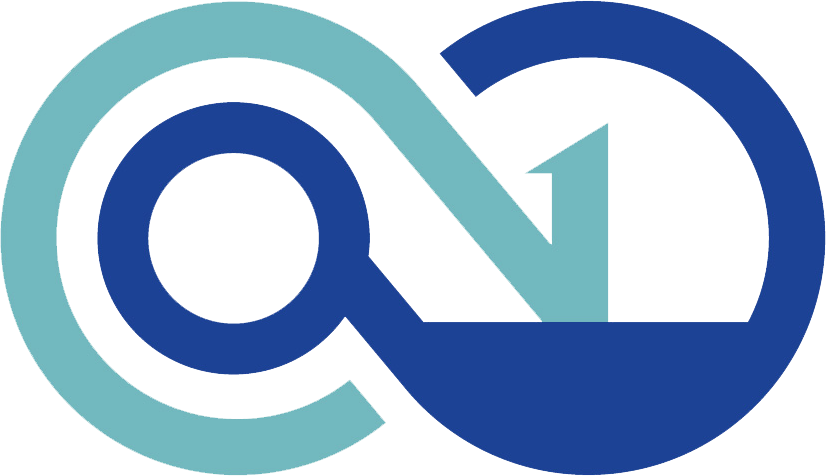