Your Guide to Mastering Flexible PCB Quotes: Cost, Design, and More
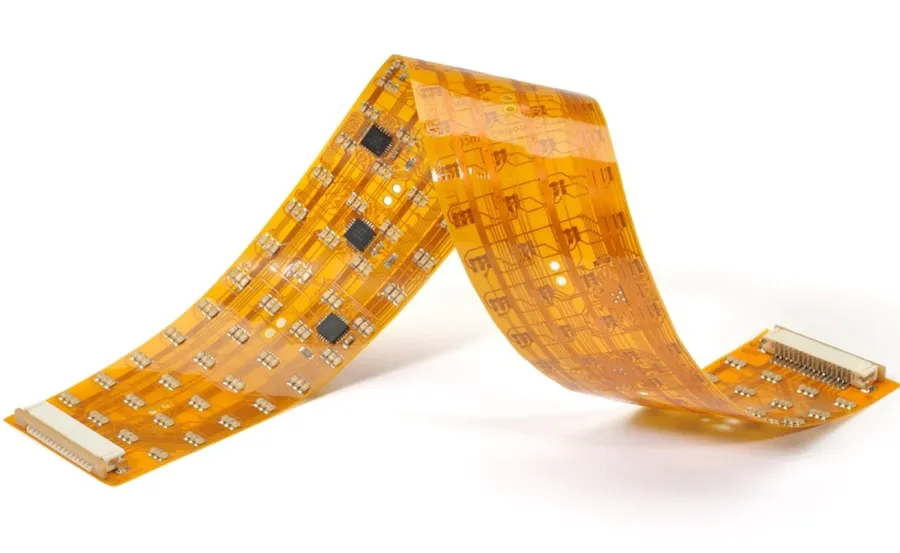
In today's fast-paced tech world, flexible PCBs are revolutionizing everything from wearable tech to aerospace, offering unique design possibilities compared to rigid circuit boards. Just like how a tailor needs precise measurements for a custom suit, getting an accurate flexible PCB quote is crucial. This article will guide you through the process, helping you understand the factors influencing cost and how to secure the best quote for your project. We'll unpack the complexities, demystify the jargon, and equip you with the knowledge to navigate the quoting process like a pro, ensuring you get the perfect 'flexible fit' for your electronic needs.
Understanding Flexible PCB Basics
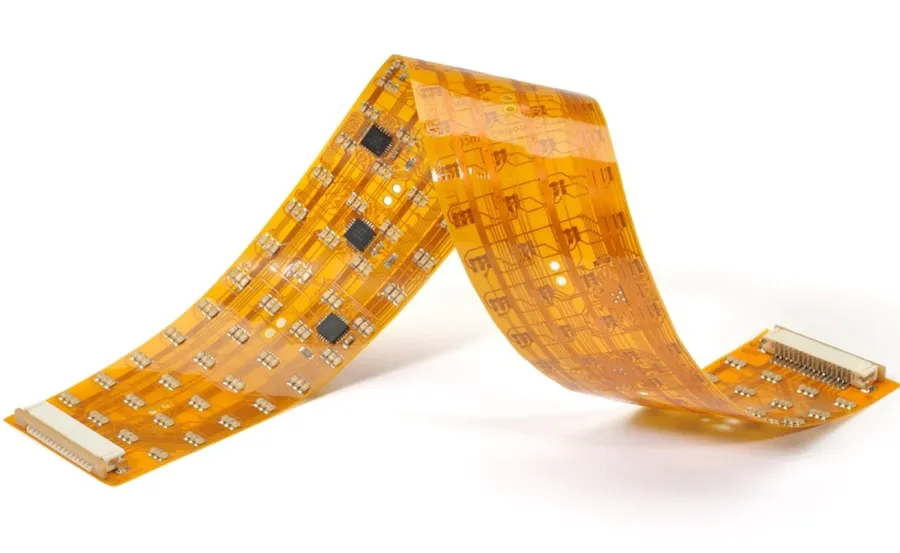
Flexible PCBs, or flex PCBs, are circuit boards constructed on a flexible substrate, allowing them to bend and conform to various shapes, a significant advantage over traditional rigid PCBs. This inherent flexibility, coupled with their space-saving potential, makes them indispensable in applications where form factor and movement are critical. Flex PCBs are essential components in modern electronics, ranging from handheld devices to aerospace technology.
The core construction of a flexible PCB comprises several key elements:
- Base Material:
Typically a thin, flexible polymer film such as polyimide (PI) or polyester (PET), which provides the structural foundation and flexibility to the PCB. - Conductive Layers:
Thin layers of copper are laminated onto the base material, forming the circuit traces and pads. These conductive pathways facilitate the flow of electrical signals within the device. These copper layers can be single-sided, double-sided, or multi-layered depending on the complexity of the circuit. - Adhesive Layer:
An adhesive layer is used to bond the copper and other functional layers to the base material, ensuring a robust and reliable assembly. - Coverlay:
A protective layer, such as polyimide, applied over the conductive traces to provide insulation and protect the circuit from environmental factors.
Common applications include:
- Consumer Electronics:
Smartphones, laptops, wearables, and cameras, where flexibility and small form factors are crucial. - Automotive:
Dashboard electronics, sensors, and lighting systems, enabling compact and reliable integration within vehicles. - Medical Devices:
Implantable devices, diagnostic tools, and patient monitoring equipment, where biocompatibility and flexibility are paramount. - Aerospace:
Avionics, satellite systems, and aerospace instrumentation, where space and weight savings are critical.
Key Factors Influencing Flexible PCB Quotes
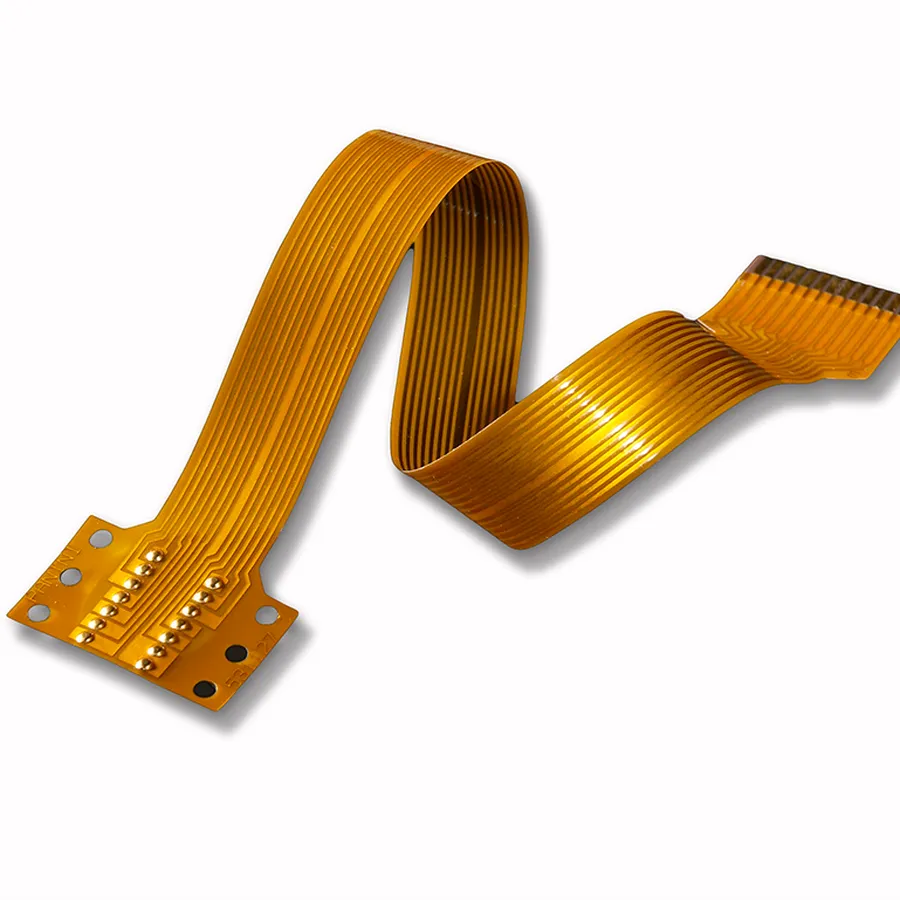
The cost of flexible PCBs is determined by a multitude of interconnected factors, each contributing to the final quote. Understanding these key drivers is crucial for both designers and purchasers aiming for cost-effective solutions. These factors encompass design complexities, material choices, and manufacturing requirements.
Factor | Description | Impact on Cost |
---|---|---|
PCB Size and Complexity | The overall area and intricacy of the PCB design. | Larger and more complex designs generally lead to higher costs due to increased material usage and manufacturing time. |
Layer Count | Number of conductive layers in the PCB (single-sided, double-sided, multilayer). | More layers increase complexity, material costs, and manufacturing steps, directly raising the price. |
Material Selection | Type of base material (e.g., polyimide, PET). | Polyimide, known for its excellent thermal and chemical resistance, is generally more expensive than PET. |
Copper Thickness | Thickness of the copper conductive layers. | Thicker copper layers require more material and specialized processing, increasing costs. |
Surface Finish | Type of coating applied to exposed copper (e.g., ENIG, HASL). | Surface finishes like ENIG, providing better solderability, tend to be more expensive than HASL. |
Special Features | Specific design requirements such as impedance control and via types. | Features like controlled impedance require tighter tolerances and specialized manufacturing processes, raising costs. |
Production Volume | Number of PCBs to be manufactured. | Higher production volumes can lead to lower per-unit costs due to economies of scale. |
Types of Flexible PCBs: Single-Sided, Double-Sided, and Multilayer
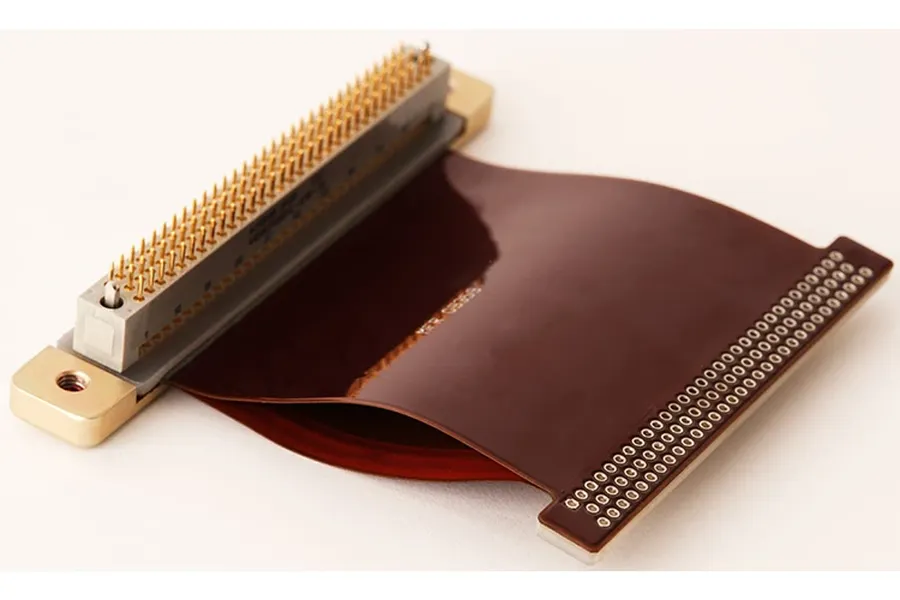
Flexible PCBs are categorized into single-sided, double-sided, and multilayer designs, each offering different levels of complexity, performance, and cost. Understanding these distinctions is crucial for selecting the right type for your specific application. The cost implications, design considerations and manufacturing processes are affected significantly by the number of layers and complexity. Furthermore, rigid-flex PCBs which combine the properties of both rigid and flexible circuits add to the available options.
Feature | Single-Sided Flex PCB | Double-Sided Flex PCB | Multilayer Flex PCB | Rigid-Flex PCB |
---|---|---|---|---|
Layer Count | One conductive layer | Two conductive layers | Three or more conductive layers | Combines rigid and flexible layers |
Complexity | Least complex | Moderate complexity | Most complex | Complex |
Cost | Lowest cost | Medium cost | Highest cost | High cost |
Flexibility | High flexibility | Good flexibility | Reduced flexibility with increased layer count | Flexibility only in designated flex areas |
Applications | Simple circuits, static applications | More complex circuits, dynamic applications | High-density, high-performance applications | Applications needing both rigid and flex |
Via Types | Limited to surface mounted components | Through hole or surface mounted | Through-hole, blind, and buried vias | Mix of via types |
How to Prepare for a Flexible PCB Quote Request
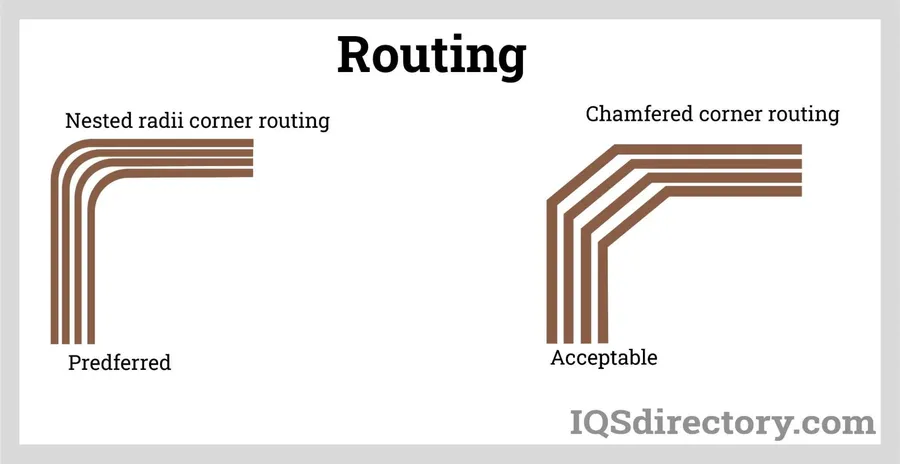
Preparing a comprehensive quote request for flexible PCBs is crucial for obtaining accurate pricing and avoiding production delays. This involves providing detailed specifications and design data that allow manufacturers to precisely understand your project requirements. Clear and complete documentation will streamline the quoting process, minimize errors, and ultimately save both time and money.
- Gerber Files
Provide complete and accurate Gerber files, which are standard CAD files used for PCB manufacturing. These files should include all necessary layers (copper, solder mask, silkscreen, drill), and the file naming convention should be clear and consistent. - Layer Stack-up
Specify the layer stack-up, including the type and thickness of each layer (base material, copper, adhesive), including the type and thickness of each layer (base material, copper, adhesive). This ensures the manufacturer understands the structure of the board. - Material Requirements
Clearly state the specific materials needed for your flex PCB. This includes the base material (e.g., polyimide, PET), copper type and thickness, and adhesive type. Indicate any specific material properties or certifications needed. - Finished PCB Thickness
Specify the desired finished thickness of the flexible PCB. This dimension is important for fit and assembly purposes, especially in constrained spaces. - Surface Finish
Detail your requirements for the surface finish, for example, ENIG, HASL, or other options. The choice of finish impacts solderability and long-term reliability. - Via Specifications
Outline the types and sizes of vias needed, including plated through-hole (PTH) vias, blind vias, and buried vias. Indicate any specific fill requirements and aspect ratios for the vias. - Special Features
Identify any special features required, such as impedance control, controlled impedance traces, or specific routing requirements. Clearly communicate any unique manufacturing requirements or considerations. - Tolerances
Specify the required tolerances for critical dimensions, trace widths, spacing, and layer alignment. This information is essential to maintain the design integrity and performance of the PCB. - Quantities
State the required number of boards for prototype and production runs. The quantity is a key factor for determining the manufacturing cost per unit. Indicate if you require a small quantity for prototyping followed by a larger production run. - Delivery Requirements
Specify your delivery timeframe or lead time requirements. Indicate any special packaging needs or shipping considerations to meet your timelines.
Comparing Flexible PCB Quotes: What to Look For
Evaluating flexible PCB quotes requires a comprehensive approach that extends beyond just the bottom line price. A thorough comparison should consider several crucial factors that impact the quality, reliability, and overall value of the final product.
A well-structured comparison ensures that you partner with a manufacturer who can deliver high-quality PCBs that meet your specific requirements, on time and within budget. Focusing on the right criteria can save time, money, and mitigate potential risks in the long run.
Factor | Description | Importance |
---|---|---|
Price | The total cost for the PCBs, including tooling and other charges. | Important, but should not be the sole deciding factor. Low prices may indicate lower quality. |
Lead Time | The time it takes from order placement to delivery of finished PCBs. | Crucial for project timelines; delays can lead to significant setbacks. |
Manufacturer's Reputation | The manufacturer's history, customer reviews, and industry standing. | Indicates reliability and commitment to quality. Research their past performance. |
Material Quality | The type and quality of base materials and conductive layers used. | Directly affects the performance, durability, and reliability of the PCB. |
Certifications | ISO certifications and other industry-specific certifications. | Ensures that the manufacturer follows standardized processes and quality controls. |
Production Capabilities | The manufacturer’s ability to produce PCBs with the required specifications. | Confirms they have the equipment and expertise for your complex requirements. |
Tooling Charges | Costs associated with preparing for production, including tooling and setup. | Can add significant costs; confirm charges before committing. |
Quality Control | The quality control and testing processes employed by the manufacturer. | Ensures the PCBs meet all required standards and performance criteria. |
Flexible PCB Cost Estimation: A Practical Approach
Estimating the cost of flexible PCBs requires a multifaceted approach, considering both fixed and variable factors. A rudimentary starting point often involves a per-square-inch average, with figures around $100 per square inch frequently cited. However, this figure serves only as a preliminary guideline. The actual cost is significantly affected by design complexity, material choices, tooling requirements, and production volume. A crucial step in this process is to obtain quotations for prototypes, which will serve to validate cost estimates and provide vital insights for scaling up to mass production.
Cost Factor | Description | Impact on Cost |
---|---|---|
Base Material Cost | Polyimide, PET, etc. | Varies based on material type and thickness |
Copper Layer Count | Single, double or multi-layer | Higher layer count significantly increases cost |
PCB Size | Length and width | Larger PCBs consume more materials and time |
Design Complexity | Intricate shapes, small traces/spaces | Higher complexity means longer production and potentially lower yield |
Surface Finish | ENIG, HASL, etc. | Premium surface finishes increase cost |
Special Features | Impedance control, blind vias, etc. | Special features require more processes and can increase costs |
Tooling Costs | Setup for manufacturing | Can be a significant upfront cost, especially for complex designs |
Production Volume | Number of boards | Higher volumes typically have lower per-unit costs due to economies of scale |
Frequently Asked Questions About Flexible PCBs
This section addresses common questions regarding flexible PCBs, offering concise answers to help you navigate the complexities of flex circuit technology, design, and cost.
- How much does a flexible PCB cost?
The cost of a flexible PCB varies significantly based on factors such as size, layer count, material selection, design complexity, and production volume. A basic estimate can start around $100 per square inch, but this figure can fluctuate significantly. Prototypes will generally cost more per unit than high volume orders due to tooling and set up cost. For a precise quote it’s best to provide your design specifications to a manufacturer. - What are the primary disadvantages of flexible PCBs?
While flexible PCBs offer numerous advantages, some drawbacks include higher initial manufacturing costs compared to rigid PCBs, the potential for increased fragility if not designed correctly, and more complex assembly processes which may require specialized equipment and expertise. Material limitations may also be a factor for certain applications involving high temperatures or other extremes. - Are all PCBs flexible?
No, the majority of PCBs are rigid, and made from materials like FR-4. Flexible PCBs, on the other hand, are made from flexible substrates like polyimide or polyester, enabling them to bend and conform to various shapes. The choice between rigid and flexible depends on the application requirements for mechanical flexibility, size and assembly. - How should I determine my charges for flexible PCB design?
Pricing for flexible PCB design should account for the complexity of the layout, the required design hours, and the designer's expertise. Market rates for PCB design vary widely, but project based pricing is advisable where the risk and responsibility is clearly defined. Consider project size, the number of layers, component density, and any special design rules and constraints. A detailed project scope is critical for proper cost estimation. - Can Flexible PCBs be used in high temperature applications?
Flexible PCBs using polyimide substrates can operate in high temperature environments, typically up to around 200°C, depending on the material grade and specific design. However, other flexible materials like PET are generally unsuitable for high temperature applications. It’s critical to choose the correct material based on the operating environment to ensure the performance and reliability of the board. - What are the key factors to consider for a reliable flex PCB design?
Key factors for reliable flex PCB design include material selection appropriate for the intended application, proper mechanical design to avoid stress concentrations and reduce the likelihood of tearing during flexing, appropriate layer stack up to enable reliable connection, and via type selection which must accommodate flexing. Also considering tooling and assembly processes that will ensure reliable manufacturability and assembly are critical.
Design Considerations for Cost-Effective Flexible PCBs
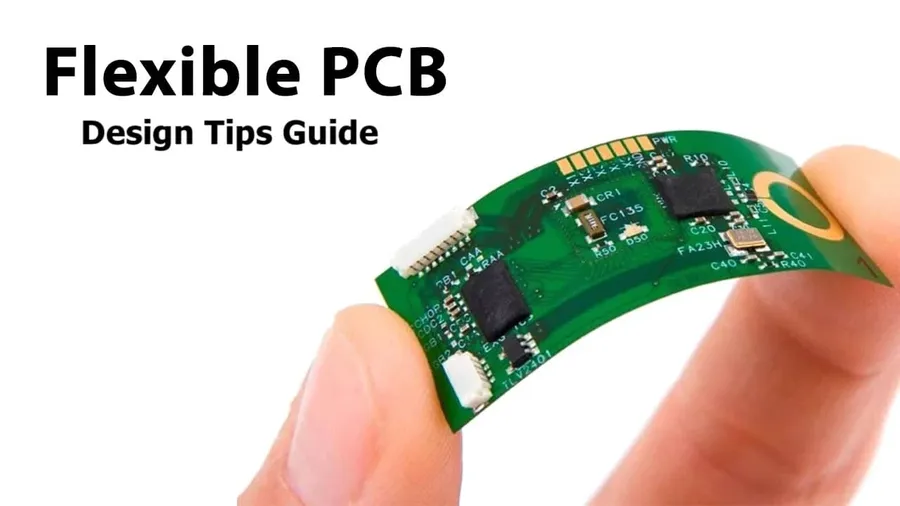
Optimizing flexible PCB design is crucial for controlling manufacturing costs. By making strategic decisions during the design phase, engineers can significantly reduce expenses without compromising functionality. This involves standardizing design elements, choosing cost-effective materials, and minimizing manufacturing complexities.
- Standardize Layer Count and Material Choices
Using standard layer counts (e.g., single or double-sided) and commonly available materials (like standard polyimide) reduces material waste and lowers manufacturing costs. Standard materials benefit from economies of scale and typically have shorter lead times. - Avoid Complex Shapes and Features
Intricate shapes, sharp corners, and non-standard cutouts require more precise machining, leading to increased manufacturing time and costs. Opting for simpler shapes and rounded corners can significantly reduce expenses. - Maximize Panel Utilization
Efficiently arranging multiple PCBs on a single manufacturing panel maximizes material usage and reduces waste. Careful panelization minimizes raw material consumption and overall costs. Consider arraying designs or placing multiple designs on one panel to maximize material usage. - Minimize the Number of Vias
Vias, especially microvias, add complexity to the manufacturing process. Reducing the number of vias, and using through-hole vias instead of blind or buried vias, simplifies fabrication and reduces costs. Strategically plan trace routing to minimize via usage. - Use Standard Trace Widths and Spacing
Adhering to standard trace widths and spacing simplifies the fabrication process and reduces the risk of manufacturing defects. Using standard design rules for trace and space results in higher yields and lower costs. - Design for Manufacturability (DFM)
Early engagement with the manufacturer during the design phase helps to identify and resolve potential manufacturing challenges proactively. Designing with the manufacturer's capabilities in mind, and following their design rules, reduces the risk of errors, rework, and delays.
Advanced Techniques in Flexible PCB Manufacturing
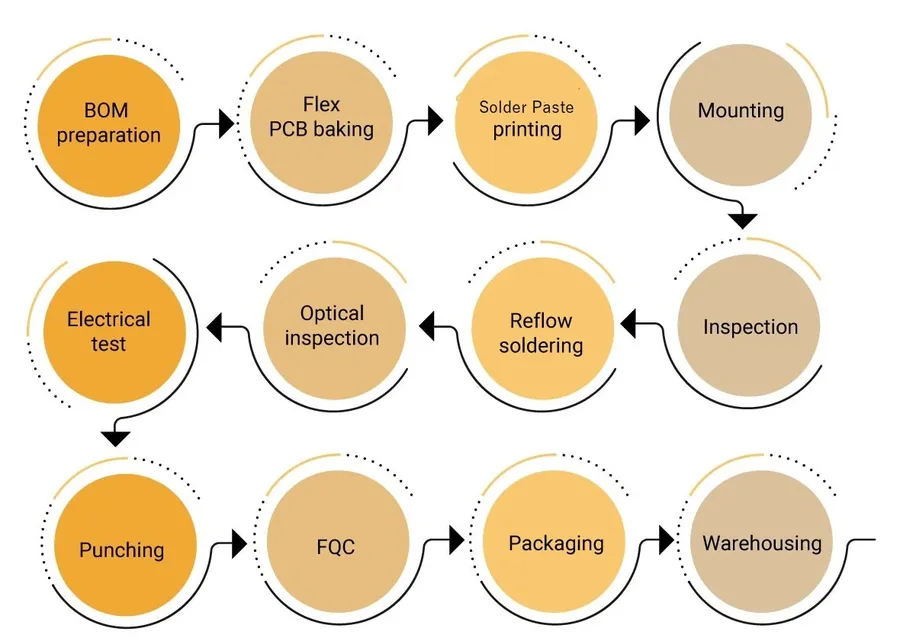
Advanced flexible PCB manufacturing techniques are driving innovation, enabling more complex designs and improved performance. These techniques, while potentially increasing initial costs, can lead to more robust, efficient, and application-specific solutions, expanding the possibilities for flexible electronics.
These methods offer design freedoms and performance enhancements that are often unattainable with conventional processes. Exploring and understanding these techniques enables designers and engineers to create cutting-edge products with superior functionality and adaptability.
- Laser Ablation
Laser ablation uses focused laser beams to selectively remove material, offering high precision for creating fine features, intricate patterns, and microvias. It is especially useful for drilling small holes and patterning complex shapes in flexible substrates, and for creating very small vias. The precision afforded by laser ablation enables higher component densities and more compact designs. - Additive Manufacturing
Also known as 3D printing, additive manufacturing builds PCBs layer by layer using conductive inks and other materials. This method is especially useful for rapid prototyping and low-volume production of customized flexible PCBs. It minimizes material waste and enables the creation of highly complex and non-planar circuit geometries. Additive manufacturing can also integrate electronic components directly during the fabrication process. - Advanced Via Structures
Advanced via technologies, such as blind and buried vias, are critical for multilayer flex PCBs as they create interconnections between layers, providing greater design flexibility and improved signal integrity. These methods create shorter signal paths, which reduces parasitic effects and improves the overall performance of high-speed electronic circuits.
Technique | Description | Impact on Cost | Design Opportunities |
---|---|---|---|
Laser Ablation | Material removal using laser | Increased tooling costs, high precision | Fine features, intricate patterns, microvias |
Additive Manufacturing | Layer-by-layer PCB construction | Potentially lower prototyping costs, higher material costs | Rapid prototyping, complex geometries, embedded components |
Advanced Via Structures | Blind and buried vias | Higher fabrication costs, improves signal integrity | Layer-to-layer interconnections, compact designs |
Getting a precise flexible PCB quote involves more than just requesting a price; it requires a solid understanding of your design needs, material options, and manufacturing capabilities. Like a well-engineered bridge, every aspect of a flexible PCB is interconnected. By understanding these nuances and being meticulous in your request, you can ensure a cost-effective and successful production run. Remember, the cheapest quote isn't always the best; it's about finding the right balance between price, quality, and reliability to ensure that your final product has a truly 'flexible' performance advantage.
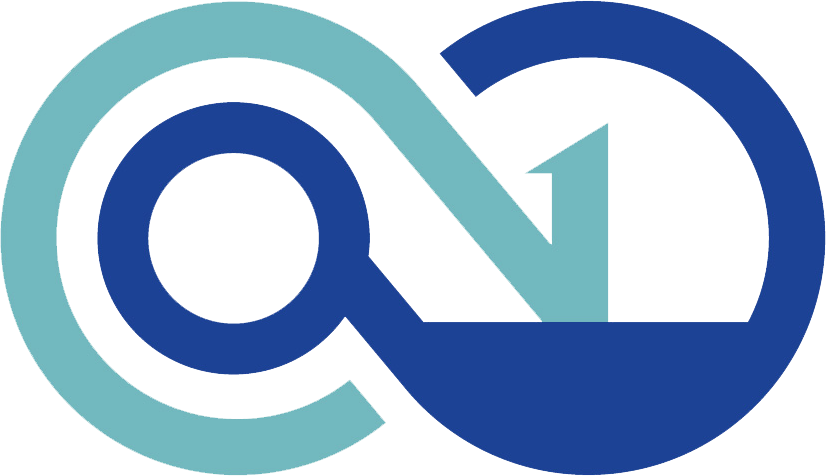