Your Guide to Selecting the Right Single Sided PCB Manufacturer
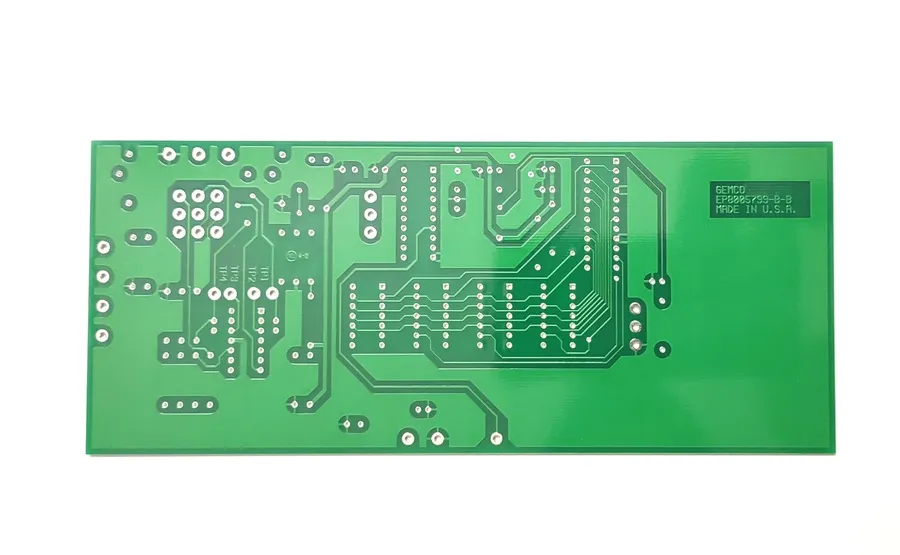
In the world of electronics, single sided PCBs (Printed Circuit Boards) are the workhorses behind countless devices, from simple household appliances to sophisticated industrial equipment. Choosing the right single sided PCB manufacturer is critical to ensure the quality, reliability, and cost-effectiveness of your product. This guide will delve into the intricacies of single sided PCB manufacturing, providing a comprehensive overview to help you make informed decisions, and highlighting the importance of choosing a qualified partner.
Understanding Single Sided PCBs: Basics and Applications
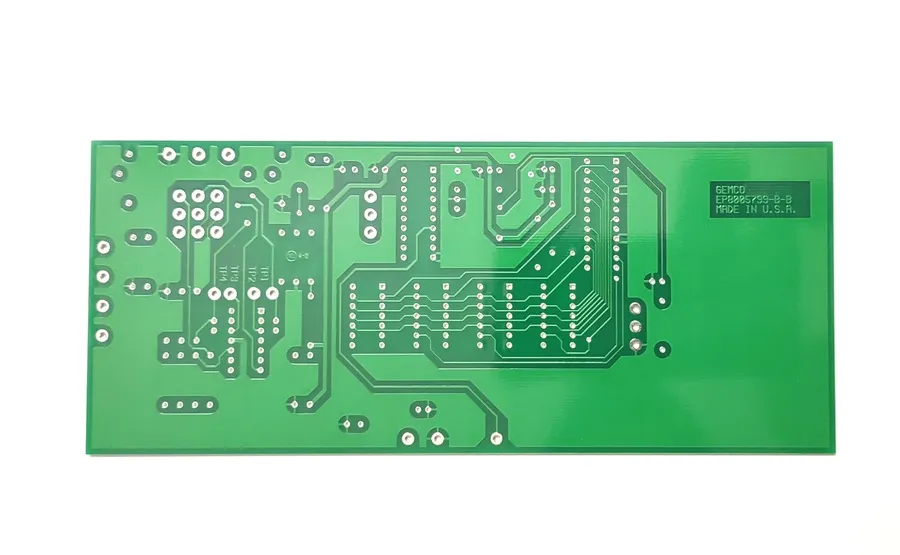
Single-sided PCBs are the foundational building blocks of many electronic devices, characterized by their conductive layer on just one side of the insulating substrate. This design simplicity lends itself to various applications, making them a cost-effective and reliable solution for numerous electronic needs. Their construction typically involves a base material, conductive traces, and a protective solder mask, designed for straightforward component assembly and soldering processes.
These PCBs are widely used in applications where circuit complexity and density are not paramount. Their ease of manufacturing and lower cost make them ideal for consumer electronics, such as simple lighting circuits, basic audio equipment, and control panels. The suitability of single-sided boards often comes down to the complexity of the electronic device's functionality and performance requirements.
Characteristic | Description |
---|---|
Structure | Conductive layer on one side of the substrate |
Materials | Typically FR-4, CEM-1, or similar |
Components | Mounted on one side, soldered to exposed traces |
Common Applications | Lighting, simple control circuits, basic audio equipment |
Single Sided PCB Design Considerations
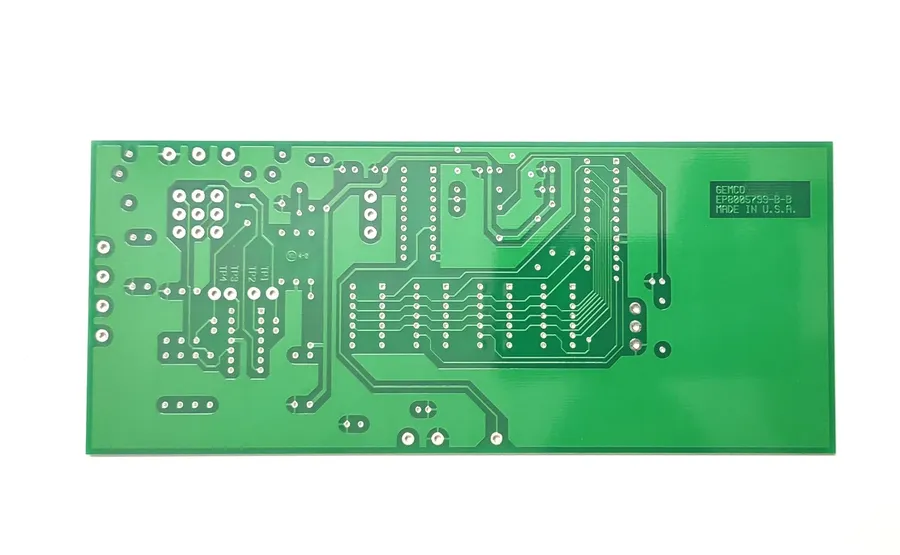
Designing single-sided PCBs requires careful planning to maximize performance within the constraints of a single conductive layer. Key design considerations include trace geometry, component placement, and thermal management, all of which impact the board's functionality and reliability. The limitations of single-sided boards necessitate efficient use of space and strategic design choices.
Achieving optimal performance on a single-sided PCB involves a strategic approach to several key design elements. This includes considerations for trace width and spacing to ensure signal integrity and prevent shorts, optimal component placement for effective routing and minimal interference, and careful thermal management to avoid hotspots and ensure board reliability.
- Trace Width and Spacing
Trace width must be sufficient to handle the required current, while spacing should prevent shorts and signal interference. Adhering to IPC standards for minimum trace width and spacing is crucial. - Component Placement
Carefully consider component placement to minimize trace lengths and avoid signal crossings. Grouping related components can also aid in efficient routing. Consider using a grid layout to improve component density and avoid complex layouts. - Thermal Management
Effective heat dissipation is important. Design for thermal relief, particularly for components that generate significant heat. This can include heat sinks or creating thermal vias. - Signal Integrity
Although generally less critical on single-sided boards than multi-layer designs, signal integrity still needs to be considered. Proper impedance matching and trace routing techniques are important for high speed signals. - Ground Planes
While single-sided PCBs lack a dedicated ground plane, it’s advisable to create a ground net that covers as much of the board as possible to minimize noise and ensure signal return.
Best practices for single-sided PCB design include utilizing design software that supports autorouting (with careful review and adjustment), creating a schematic first, and meticulously checking for errors before fabrication. Furthermore, collaborating with experienced designers or engineers who are familiar with the limitations and nuances of single-sided PCB layouts is highly beneficial.
Aspect | Consideration |
---|---|
Trace Width | Determined by current requirements; wider traces for higher currents |
Trace Spacing | Should meet minimum spacing requirements to avoid shorts and signal interference |
Component Placement | Minimize trace length, group related components, consider thermal effects |
Thermal Relief | Use thermal vias and heat sinks to dissipate heat effectively |
Signal Routing | Avoid signal crossings, maintain proper impedance matching, avoid sharp angles |
Design Tools | Use software with autorouting and error-checking functions |
Materials Used in Single Sided PCB Manufacturing
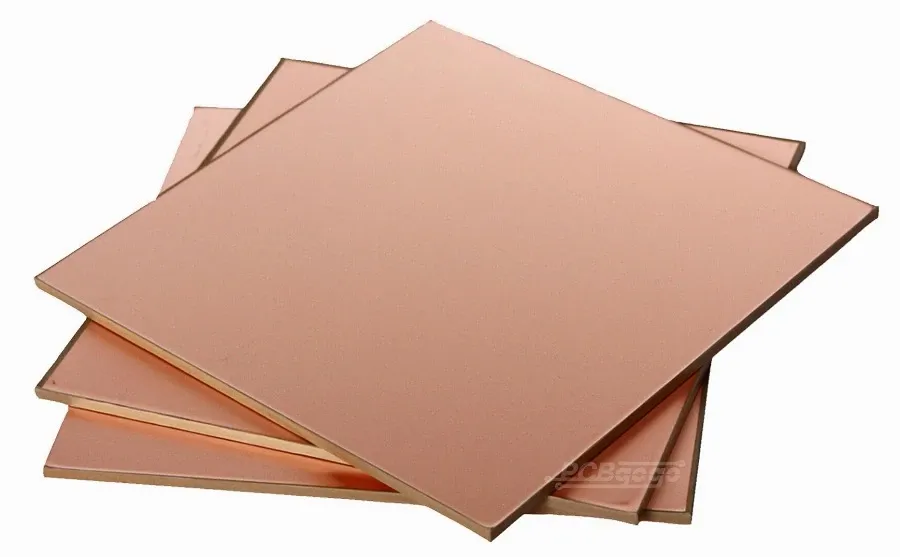
The selection of base materials in single-sided PCB manufacturing is critical, directly influencing performance, durability, and cost. These materials primarily consist of a substrate that provides mechanical support and an insulating layer upon which conductive traces are etched.
Material | Description | Typical Applications | Advantages | Disadvantages |
---|---|---|---|---|
FR-4 | Flame Retardant-4, a glass-reinforced epoxy laminate. | General-purpose electronics, consumer goods, and industrial applications. | Excellent mechanical strength, good electrical properties, cost-effective. | Not suitable for very high frequency applications or high temperature |
CEM-1 | Composite Epoxy Material-1, made from paper and epoxy resin. | Less demanding applications, like lighting and lower frequency electronics. | More cost-effective than FR-4, easy to process. | Lower mechanical strength and less temperature resistance than FR-4. |
Phenolic Paper | Paper-based laminate with a phenolic resin. | Basic, low-cost applications, like toys, or simple household devices. | Very low cost. | Poor moisture resistance, low flexural and mechanical strength. |
Metal Core (Aluminum/Copper) | Metal substrate with a thin insulating layer. | LED lighting, power electronics, and high thermal management applications. | Excellent heat dissipation, robust mechanical structure. | Higher cost and more complex processing. |
The properties of these materials are crucial for the functionality of the PCB. For instance, FR-4 offers a good balance of mechanical strength and electrical insulation, making it a common choice for a wide range of applications. CEM-1, while more cost-effective, may be preferred in simpler applications where high performance is not critical. Metal core PCBs are ideal when thermal dissipation is important, such as in high-power electronic designs.
The Manufacturing Process of Single Sided PCBs
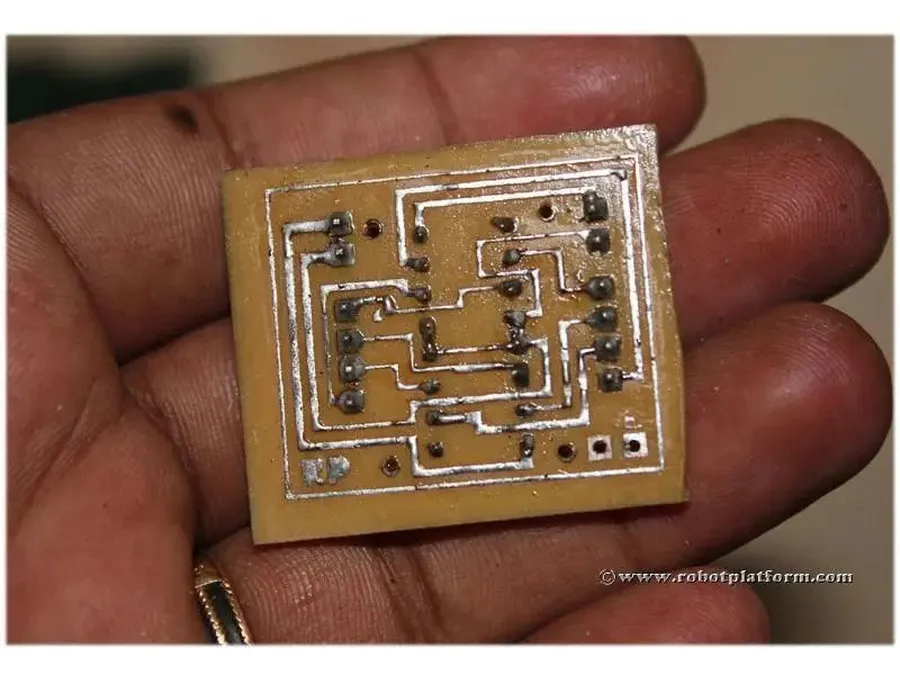
The fabrication of single-sided PCBs involves a series of precise steps to transform a design concept into a functional circuit board. This process, while simpler than that of double-sided or multilayer PCBs, still requires meticulous execution and quality control to ensure reliability.
- Design and Film Preparation
The initial step involves translating the electronic circuit design into a physical layout using specialized PCB design software. This layout is then converted into a film, which serves as a template for the subsequent stages. Accurate film is critical for precision in the final product. - Board Preparation
The base material, typically a rigid substrate like FR-4 or CEM-1, is cut into panels of the required size. The surface of the board is thoroughly cleaned to remove any contaminants and to prepare it for the application of a photosensitive resist. - Photosensitive Resist Application
A thin layer of photosensitive resist is applied evenly across the board using lamination methods, ensuring there are no air pockets or other defects that could affect the final product. - Image Transfer (Exposure)
The film containing the circuit layout is carefully aligned over the coated board, and ultraviolet (UV) light is used to expose the board, causing the resist to harden in areas where it is not covered by the film. This transfer of image from the film to the board will determine the final circuit pattern. - Development
After exposure, the unhardened resist material is dissolved during the development process, leaving behind the hardened resist, which forms a protective layer for the copper traces underneath. The hardened resist shows the circuit pattern that was in the film. - Etching
The board is then immersed in an etching solution, which removes the exposed copper not protected by the hardened resist. This step defines the copper traces of the circuit. Etching speed and uniformity will affect the final result. - Resist Removal
Once the etching is complete, the remaining hardened resist is removed, revealing the final copper traces. - Drilling
Holes for mounting components or through-holes are precision-drilled into the board using specialized drilling machines. The accuracy of drilling operations is important to the later stages of assembly. - Solder Mask Application
A solder mask, which is a protective coating, is applied to the board to prevent solder bridges during component assembly. It also prevents corrosion of the copper traces. The solder mask is applied and cured via a UV curing process. - Surface Finish
A surface finish, such as HASL (Hot Air Solder Leveling), ENIG (Electroless Nickel Immersion Gold) or OSP (Organic Solderability Preservative), is applied to the exposed copper pads to enhance solderability and prevent oxidation. - Silkscreen Printing
A silkscreen printing process is used to add component designators and other important labeling to the board. - Final Inspection and Testing
Finally, each board undergoes visual inspection and electrical testing to ensure its functionality. This phase ensures that no defective board leaves the manufacturing plant.
Quality control is paramount in each of these steps. Manufacturers utilize techniques such as Automated Optical Inspection (AOI), and electrical continuity testing to identify and rectify any potential issues before the product reaches the customer. This ensures that each PCB meets the required specifications and performance standards.
Key Factors to Consider When Choosing a Single Sided PCB Manufacturer
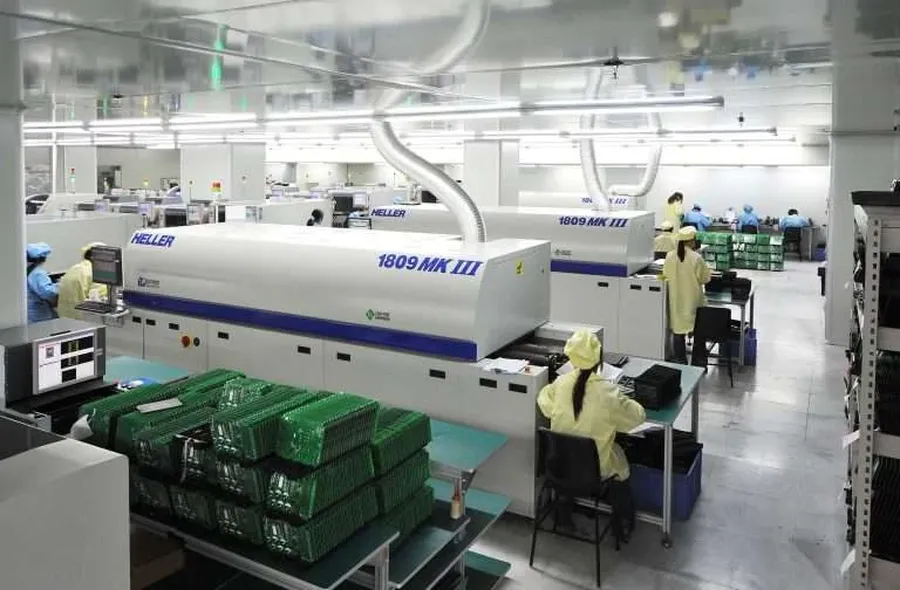
Selecting the right single-sided PCB manufacturer is crucial for ensuring the quality, reliability, and cost-effectiveness of your electronic product. This decision involves a careful evaluation of several key factors, including pricing, lead times, quality certifications, communication effectiveness, and the manufacturer's production capabilities. This section provides guidance on navigating these considerations to make an informed choice that aligns with your specific needs and constraints.
- Price Competitiveness
Evaluate the overall cost, including unit price, tooling charges, and potential shipping fees. Obtain quotes from multiple manufacturers to assess the range of pricing within the market. Be wary of prices that seem unusually low, as they may indicate compromised quality or hidden costs. Consider the long term cost not just the upfront quote. - Lead Time
Assess the manufacturer's stated lead times for production. Verify the ability to meet the requirements of your project schedule. Shorter lead times are preferable, particularly in fast-paced projects, but ensure that shorter times does not sacrifice quality. Ask for a realistic lead time not a best case. - Quality Certifications
Check for relevant certifications, such as ISO 9001, or industry-specific standards. Certifications indicate the manufacturer's adherence to quality management systems and consistent manufacturing practices. These certifications give some reassurance and accountability in the manufacturer process. - Communication Clarity
Evaluate the manufacturer's responsiveness and clarity in communication. Efficient and transparent communication is vital throughout the design, production, and delivery process. Ensure they respond to your queries in a timely and comprehensive manner. Clear communication reduces errors and miscommunications. - Manufacturing Capabilities
Confirm the manufacturer's ability to produce PCBs that meet the required specifications for your design, including size, material, and feature complexity. They need to be able to reliably manufacture the specific requirements of your board. If your design has specific requirements, ensure the manufacturer can accommodate them. - Minimum Order Quantities
Check if the minimum order quantities required by the manufacturer fit with your needs. Some manufacturers might only work with larger volumes while others might have a lower MOQ. Understand the specific minimum order quantities and pricing at various quantities. Some manufacturers may also allow prototype runs and very low volume manufacturing. - Geographic Location
Consider the manufacturer's geographic location. Domestic suppliers may offer advantages in terms of faster shipping and communication, while overseas manufacturers may provide cost benefits. Assess the trade-offs of lead time, shipping costs, and potential communication barriers based on geographical location. Consider the time zone difference, shipping costs, and supply chain reliability of offshore manufacturing.
Single Sided PCB Cost Analysis and Optimization
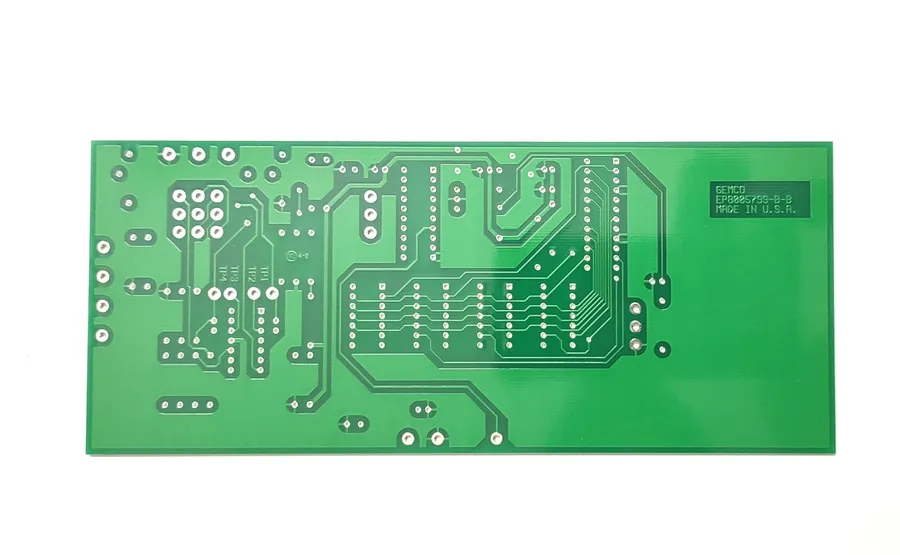
Optimizing the cost of single-sided PCB manufacturing is crucial for many applications. This section explores the primary cost drivers and offers strategies to minimize expenses without compromising board quality. A thorough analysis of these factors can lead to significant savings.
Key cost drivers include material selection, manufacturing volume, design complexity, and the choice of manufacturer. Understanding how these factors affect the final price can help businesses make informed decisions.
Cost Driver | Impact on Cost | Optimization Strategies |
---|---|---|
Base Material | Higher performance materials (e.g., FR-4 with higher Tg) increase cost. CEM-1 is usually less expensive. | Use cost-effective materials (e.g., CEM-1 where applicable) . Evaluate whether high-performance is truly necessary for your application. |
Manufacturing Volume | Larger production runs generally have lower per-unit costs due to economies of scale. | Consolidate orders to increase the total volume, take advantage of bulk pricing. |
Design Complexity | Complex designs with numerous vias, tight spacing, or unusual shapes increase production time and material usage. | Simplify designs where feasible, optimizing for standard shapes and avoiding tight tolerances. Work with a design engineer before fabrication to optimize the design. |
Manufacturer Location | Domestic manufacturers may have higher costs but offer faster turnaround and better communication; overseas manufacturers usually provide lower per-unit costs but may require larger minimum orders, slower lead times, and additional shipping costs. | Evaluate project needs (lead time vs. cost) and choose a manufacturer that best aligns with those needs. Factor in shipping costs and logistics. |
Surface Finish | Different surface finishes such as HASL (Hot Air Solder Leveling), ENIG (Electroless Nickel Immersion Gold), or OSP (Organic Solderability Preservative) have different costs. | Select a surface finish based on application requirements. Use OSP when possible for cost-effectiveness, or HASL if your solderability needs are critical. |
Testing Requirements | Different levels of testing including flying probe, and bed of nail testing have different costs. | Select testing based on requirements, some less complex boards may not need full testing. |
Strategies for cost reduction include optimizing material selection, which can significantly impact cost without compromising functionality. For example, using CEM-1 instead of FR-4 can reduce cost, if application requirements permit. Design for Manufacturability (DFM) is also crucial; simpler designs with standard shapes and component spacing not only reduce costs, but improve yield. Purchasing in larger volumes will also lead to lower per unit costs. Finally, comparing quotes from multiple suppliers helps identify more competitive pricing.
Single Sided PCB vs Double Sided PCB: A Comparative Analysis
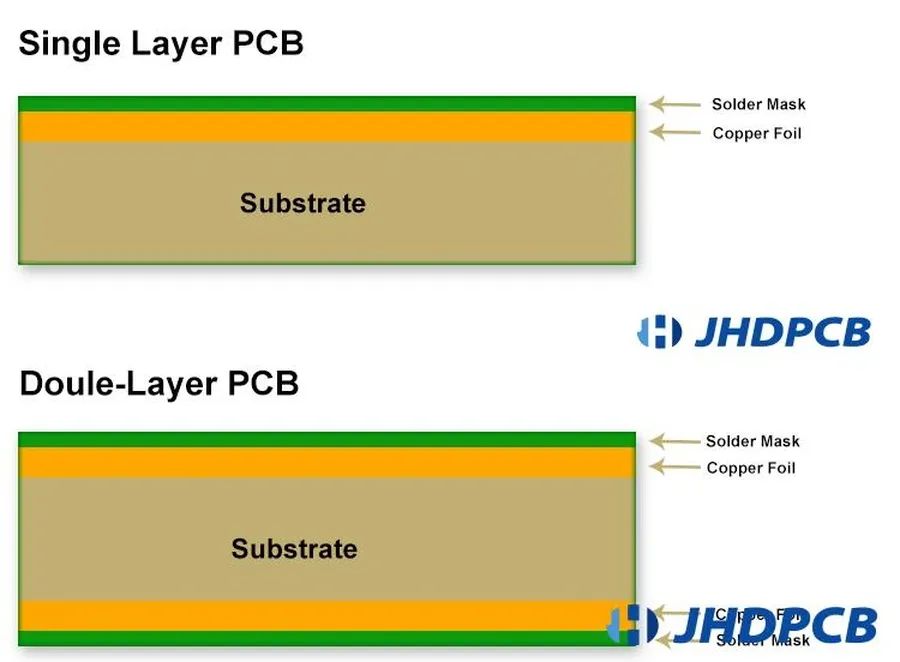
Single-sided PCBs and double-sided PCBs represent fundamental choices in electronic circuit board design, each offering distinct advantages and disadvantages that align with specific application requirements. The selection between these two types hinges on factors such as circuit complexity, component density, cost constraints, and performance needs. Understanding the nuances of each will ensure optimal design choices.
Feature | Single-Sided PCB | Double-Sided PCB |
---|---|---|
Layer Count | One conductive layer | Two conductive layers |
Complexity | Lower complexity, simpler designs | Higher complexity, more intricate designs |
Routing | Limited routing options; all traces on one side | Increased routing options; traces on both sides, vias for layer transitions |
Component Density | Lower component density | Higher component density |
Cost | Generally lower cost | Generally higher cost |
Performance | Suitable for simple, low-density circuits | Suitable for complex, high-density circuits, better signal integrity |
Applications | Basic electronics, simple circuits, cost-sensitive applications | Advanced electronics, complex circuits, where performance matters |
Heat Dissipation | Limited heat dissipation capabilities | Better heat dissipation due to more surface area and vias |
Key differentiators extend beyond the number of conductive layers. Double-sided PCBs, with their ability to route traces on both sides and interconnect layers via vias, allow for more compact designs and greater circuit complexity. Single-sided PCBs, while simpler, present challenges in achieving high-density designs and optimal signal integrity. The cost implications also vary; single-sided boards are generally more cost-effective for simple applications, while double-sided boards, although more expensive, are indispensable for complex, high-performance electronic devices. When choosing, designers need to evaluate the trade-offs, considering not just the immediate cost but also long-term functionality and system demands.
Frequently Asked Questions About Single Sided PCBs
This section addresses common inquiries regarding single-sided PCBs, covering their manufacturing, cost-effectiveness, applications, and comparisons to double-sided PCBs. We'll provide clear, concise answers to help you make informed decisions about using single-sided PCBs.
- How are single-sided PCBs manufactured?
The single-sided PCB manufacturing process involves several key steps: First, a copper clad laminate is cleaned and prepared. A circuit pattern is then transferred onto the copper layer using a photolithographic process or screen printing. Next, the board is chemically etched to remove unwanted copper, leaving the desired traces and pads. Holes are then drilled for component insertion, and finally a solder mask is applied to protect the circuits and facilitate soldering. - Are single-layer PCBs cheaper than double-sided PCBs?
Yes, single-layer PCBs are generally cheaper to manufacture than double-sided PCBs. This is primarily because their production process is simpler, requiring fewer steps and less material. The cost savings are driven by the elimination of through-hole plating and the need for a second copper layer. - Who manufactures PCBs, and how to choose a manufacturer?
PCBs are manufactured by specialized companies that have the necessary equipment and expertise to produce circuit boards to customer specifications. When choosing a manufacturer, consider factors such as manufacturing capabilities, quality certifications (ISO 9001), turnaround time, and cost. It is also crucial to verify their customer reviews and ensure they have strong communication practices. Local and international manufacturers both have advantages so weigh them against your needs. - What are the typical applications for single-sided PCBs?
Single-sided PCBs are commonly used in less complex electronic devices that do not require high density component placement. Typical applications include: LED lighting, consumer electronics (like calculators or remote controls), simple sensors, power supplies, and basic control circuits. They are ideal for cost-sensitive applications where advanced functionality is not a primary requirement. - What is the difference between single-sided and double-sided PCBs?
The key difference between single-sided and double-sided PCBs is the number of copper layers they have. Single-sided PCBs have copper traces on only one side of the board, while double-sided PCBs have copper traces on both sides. Double-sided PCBs allow for higher component density and more complex circuitry due to the increased routing possibilities with vias, but they also cost more. - What materials are commonly used in single sided PCB manufacturing?
Common base materials for single-sided PCBs include FR-4 (a fiberglass-reinforced epoxy laminate), CEM-1 (a composite material that is more cost-effective than FR-4). Other factors include the thickness of the copper layer, the type of solder mask, and the finish used on the copper traces. - What design considerations are important for single sided PCBs?
When designing a single-sided PCB, careful consideration must be given to trace width, spacing, and component placement to avoid electrical interference. Thermal management is also important to minimize heat dissipation issues. Design tools like KiCad, Eagle, or Altium Designer can aid in optimization.
Choosing the right single sided PCB manufacturer is essential for a successful product launch. By understanding the design, manufacturing, and cost considerations, along with the key factors to assess potential partners, you can ensure that your PCBs meet your specifications and budget. Partnering with a reputable single sided PCB manufacturer is crucial for getting quality, low-cost parts for your electronics and hardware needs. A well-chosen single sided PCB manufacturer can help you optimize your designs and product to go to market faster and cheaper.
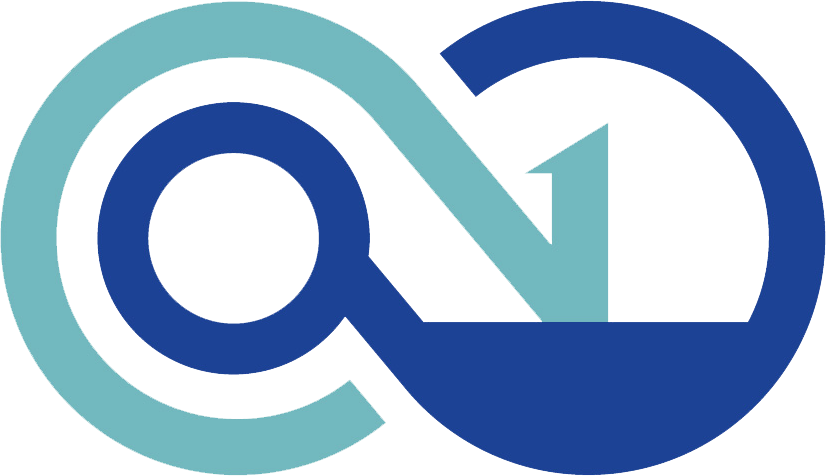