The Smart Distribution Box PCB Solution
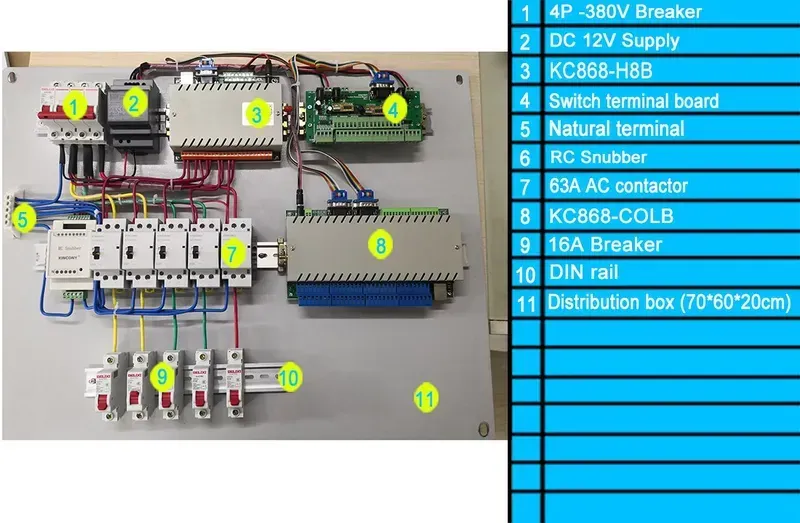
In today's rapidly evolving technological landscape, smart distribution boxes are becoming increasingly crucial for efficient power management and distribution. These intelligent systems require sophisticated printed circuit boards (PCBs) to function effectively. At Zero One Solution Limited, we specialize in providing comprehensive PCB solutions for smart distribution boxes, ensuring optimal performance, reliability, and scalability. As a leading PCB solution provider with extensive experience in rapid prototyping and a commitment to innovation, we empower our clients to accelerate product development and bring cutting-edge solutions to market with exceptional efficiency. This article delves into the intricacies of smart distribution box PCB solutions, exploring their design, manufacturing, and assembly, and highlighting how Zero One Solution Limited can help you achieve your goals.
Understanding Smart Distribution Boxes
A smart distribution box is a sophisticated evolution of the traditional electrical panel, integrating advanced digital technology to provide real-time monitoring, intelligent control, and enhanced safety features for electrical circuits. Unlike conventional distribution boxes that merely distribute power, smart versions act as central nervous systems for modern power systems, optimizing energy usage, detecting faults proactively, and enabling remote management. This transformation is pivotal in today's increasingly interconnected and energy-conscious world, forming a critical component of smart grids, smart homes, and industrial automation.
- Real-time Monitoring
Smart distribution boxes continuously monitor electrical parameters such as voltage, current, power consumption, and temperature, providing immediate insights into grid health and anomalies. This capability helps in identifying potential issues before they escalate, preventing downtime and ensuring operational stability. - Intelligent Control
Equipped with microcontrollers and communication modules, these boxes allow for automated or remote control over individual circuits. This includes features like load shedding, circuit breaker tripping for overload protection, and scheduled power adjustments, leading to significant energy savings and improved safety. - Enhanced Safety Features
Beyond basic overload protection, smart distribution boxes incorporate advanced safety mechanisms such as arc fault circuit interrupters (AFCI) and ground fault circuit interrupters (GFCI), as well as real-time fault detection and reporting. This significantly reduces the risk of electrical fires and shocks. - Data Logging and Analytics
By collecting historical data on energy consumption and system performance, smart distribution boxes enable comprehensive analytics. This data is invaluable for optimizing energy strategies, predictive maintenance, and identifying inefficiencies in power distribution networks. - Integration with Smart Grids and IoT
Designed to be interoperable, smart distribution boxes seamlessly integrate with broader smart grid infrastructures and Internet of Things (IoT) ecosystems. This connectivity facilitates centralized management, demand-response programs, and the integration of renewable energy sources, contributing to a more resilient and sustainable energy future.
The Critical Role of PCBs in Smart Distribution
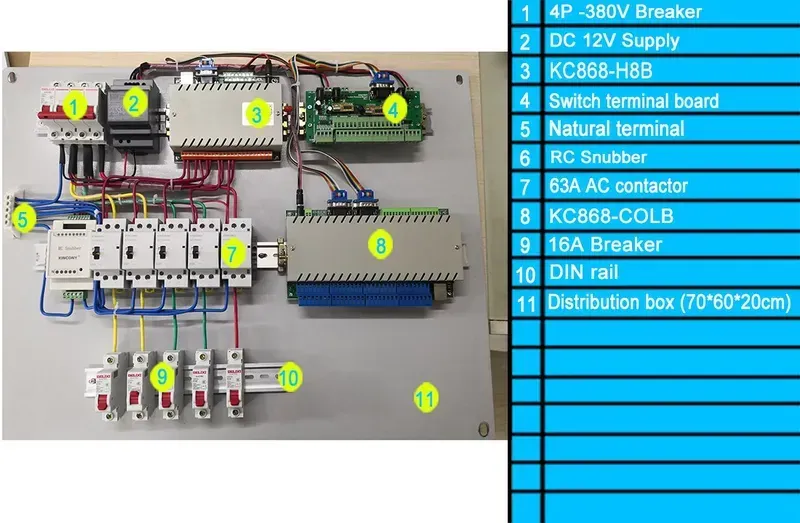
Printed Circuit Boards (PCBs) are the indispensable backbone of smart distribution boxes, enabling their advanced functionality, intelligence, and reliable operation. Far beyond simple wiring, PCBs provide the intricate pathways for electrical signals and power, facilitating the sophisticated communication, control, and data processing capabilities that define a "smart" system. Without robust and precisely engineered PCBs, smart distribution boxes would merely be static power distribution units, incapable of real-time monitoring, remote management, and proactive fault detection essential for modern grid resilience and efficiency. Their role is central to transforming traditional power infrastructure into intelligent, responsive, and adaptive networks.
- Centralized Control and Automation
PCBs integrate microcontrollers, sensors, and communication modules, enabling the central processing unit of a smart distribution box to monitor parameters, analyze data, and execute automated actions like circuit switching and load balancing without human intervention. - Data Acquisition and Monitoring
Embedded sensors on PCBs collect critical data points such as voltage, current, temperature, and power consumption. The PCB routes this data to the processing unit for real-time analysis, allowing for precise monitoring of electrical parameters and early detection of anomalies. - Communication Capabilities
PCBs host the necessary interfaces and components for various communication protocols (e.g., Modbus, Ethernet, Wi-Fi, LoRaWAN). This connectivity allows smart distribution boxes to transmit data to central control systems, SCADA platforms, or cloud-based analytics, enabling remote monitoring and management. - Protection and Safety Mechanisms
Sophisticated PCBs incorporate components for overcurrent protection, surge suppression, and ground fault detection. They are designed to rapidly detect and isolate faults, minimizing damage to equipment and ensuring the safety of personnel and the electrical system. - Enhanced Reliability and Durability
Designed for demanding environments, PCBs in smart distribution boxes are often engineered to withstand temperature fluctuations, humidity, and electromagnetic interference. The compact and robust nature of PCB assemblies contributes significantly to the overall reliability and longevity of the distribution box.
Aspect | Traditional Distribution Box | Smart Distribution Box (PCB-Enabled) |
---|---|---|
Core Functionality | Passive power distribution and basic protection | Active monitoring, control, and data analytics |
Intelligence | None | High (due to integrated PCBs) |
Fault Detection | Manual/Delayed | Automated/Real-time |
Remote Management | Not possible | Enabled by PCB communication modules |
Efficiency | Basic | Optimized through data-driven decisions |
Integration | Limited | High (with IoT and smart grid systems) |
Key Considerations for Smart Distribution Box PCB Design
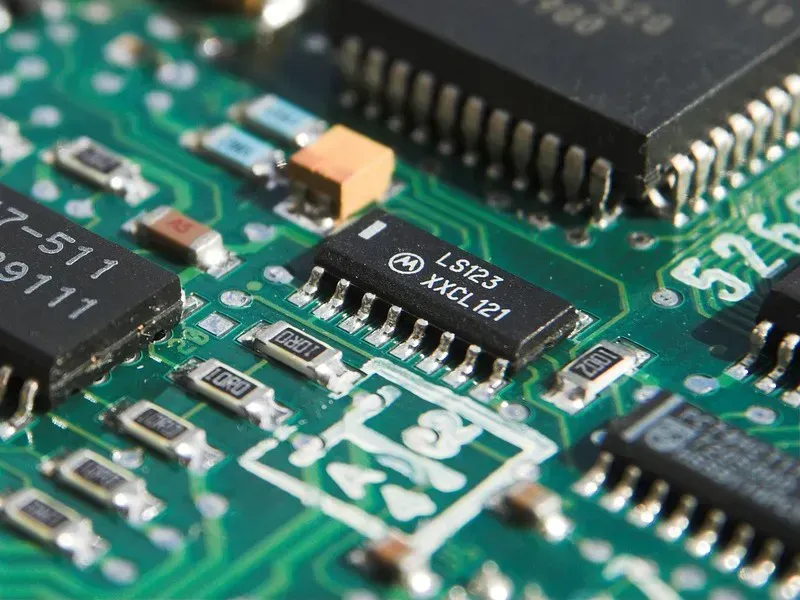
Designing Printed Circuit Boards (PCBs) for smart distribution boxes demands a meticulous approach, as these systems operate in environments where reliability, safety, and performance are paramount. The design process must integrate advanced engineering principles to ensure the PCB can withstand operational stresses, manage complex data flows, and facilitate precise power control. This includes careful attention to thermal dynamics to prevent overheating, maintaining signal integrity for accurate data transmission, optimizing component placement for efficiency and compactness, and leveraging High-Density Interconnect (HDI) technologies for enhanced functionality within limited space. Each consideration directly impacts the longevity and effectiveness of the smart distribution box, making robust PCB design the bedrock of a successful system.
Design Consideration | Description | Impact on Smart Distribution Box Performance |
---|---|---|
Thermal Management | Implementing heatsinks, thermal vias, and proper copper pours to dissipate heat generated by power components and microcontrollers. | Prevents overheating, extends component lifespan, and maintains stable system operation. |
Signal Integrity | Controlling impedance, reducing crosstalk, and ensuring clean power delivery to prevent signal degradation and data errors. | Ensures accurate data acquisition, reliable communication, and precise control of electrical parameters. |
Component Placement | Strategic positioning of components to minimize trace lengths, reduce electromagnetic interference (EMI), and optimize thermal pathways. | Enhances electrical performance, simplifies assembly, and improves overall system reliability and compactness. |
High-Density Interconnect (HDI) | Utilizing microvias, buried vias, and fine lines to increase wiring density and reduce board size. | Enables complex circuitry in compact form factors, supports advanced features, and reduces manufacturing costs through miniaturization. |
- Compliance with Industry Standards
Adherence to international standards like IPC (Association Connecting Electronics Industries) is crucial. IPC-2221 provides generic design standards, while IPC-6012 outlines qualification and performance specifications for rigid PCBs. These standards ensure the PCB's reliability, manufacturability, and safety, especially important for power distribution applications where failure can have significant consequences.
Material Selection for Enhanced Performance and Reliability
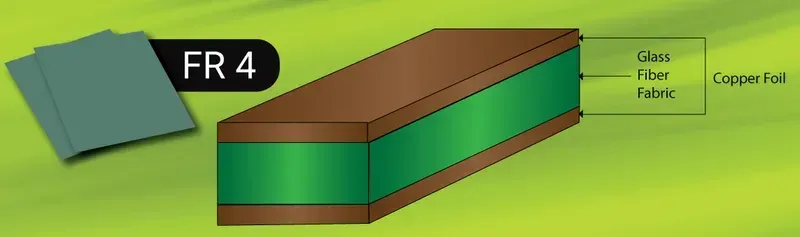
The backbone of any robust Smart Distribution Box PCB solution lies in the meticulous selection of materials. The chosen substrate must withstand demanding operational environments, including fluctuations in temperature, humidity, and electrical stress, while ensuring optimal signal integrity and long-term reliability. Prioritizing the right materials is paramount to achieving superior performance and extending the lifespan of smart distribution systems, directly impacting their efficiency and safety.
Material Type | Key Characteristics | Typical Application in Smart Distribution Box PCBs |
---|---|---|
FR-4 (Flame Retardant 4) | Widely used, cost-effective, good electrical properties, and mechanical strength. | General-purpose control boards, less demanding signal paths, power routing. |
High-Tg Epoxy Laminates | Elevated glass transition temperature (Tg), enhanced thermal stability, improved resistance to delamination under high heat. | Power management units, high-current sections, areas with significant heat generation, ensuring reliability in hot environments. |
Metal Core PCBs (MCPCB) | Excellent thermal conductivity due to a metal base (e.g., aluminum, copper), superior heat dissipation. | LED driver boards, power converter modules, high-power switching circuits where efficient heat removal is critical. |
Polyimide | High-temperature resistance, excellent flexibility (for flexible PCBs), good chemical resistance. | Flexible interconnects within complex enclosures, sensor integration, and compact module designs requiring dynamic movement. |
High-Frequency Laminates (e.g., PTFE, Hydrocarbon Ceramic) | Low dielectric loss, stable dielectric constant over frequency, ideal for high-speed signal transmission. | Communication modules (e.g., Wi-Fi, LoRa, 5G), data acquisition circuits requiring precise signal integrity. |
Manufacturing Processes: Ensuring Quality and Precision
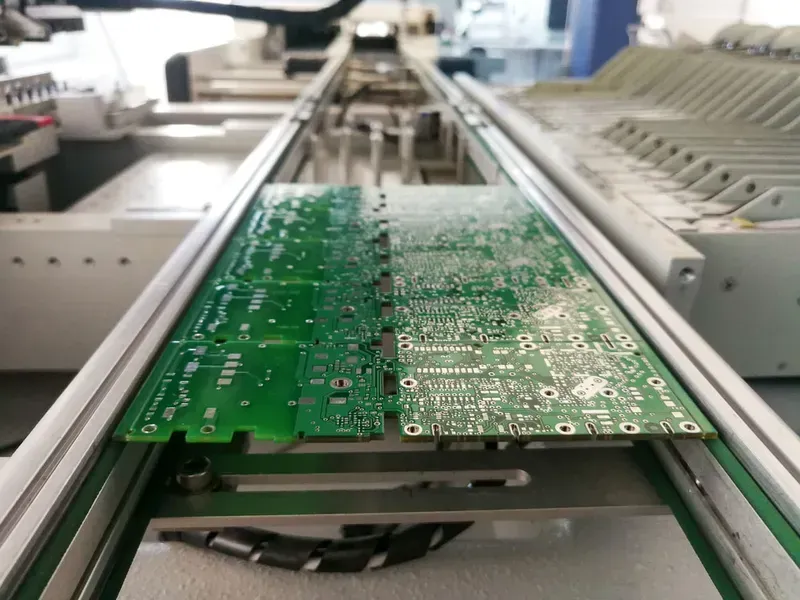
The robust functionality and long-term reliability of a Smart Distribution Box PCB are fundamentally reliant on stringent manufacturing processes. From raw material to final assembly, each stage must adhere to exacting standards to ensure the PCB can withstand demanding electrical environments, perform complex control functions, and guarantee the safety inherent in power distribution systems. This precision is paramount, as any defect can lead to critical system failures, emphasizing the need for advanced manufacturing techniques and rigorous quality control.
- PCB Fabrication: The Foundation
This initial phase involves creating the bare PCB board. It encompasses steps like circuit layout imaging, etching to remove unwanted copper, multi-layer lamination under high pressure and temperature, and drilling of vias (through-holes, blind, and buried). Material selection (e.g., FR-4 for standard applications, high-Tg materials for thermal stability) and precise layer alignment are critical for electrical performance and structural integrity. Adherence to IPC-2221 (Generic Standard on Printed Board Design) and IPC-6012 (Qualification and Performance Specification for Rigid Printed Boards) is essential for foundational quality. - Component Sourcing and Management
Beyond the bare board, the quality of components is crucial. This involves meticulous sourcing from reputable suppliers to ensure authenticity and performance, as well as efficient inventory management. Counterfeit components pose significant risks to smart distribution box reliability and safety. Verification processes, often including visual inspection, X-ray, and functional testing, are employed to mitigate these risks, ensuring every component meets the specified electrical and environmental parameters.
Process Stage | Key Activities | Critical Quality Check Points | Relevant IPC Standard |
---|---|---|---|
Fabrication | Imaging, Etching, Drilling, Lamination, Plating | Trace integrity, Via quality, Layer registration, Material properties | IPC-6012 (Rigid PCB Performance) |
Assembly (SMT & THT) | Solder Paste Printing, Component Placement, Reflow Soldering, Wave Soldering | Solder joint quality (voids, bridges), Component alignment, Polarity | IPC-A-610 (Acceptability of Electronic Assemblies) |
Testing | AOI, X-ray, ICT, Functional Testing, Environmental Testing | Shorts/Opens, Component presence/value, Electrical performance, Reliability under stress | IPC-9252 (Electrical Test Guidelines) |
- Automated Optical Inspection (AOI)
Utilizes cameras to scan the PCB for various defects such as missing components, incorrect polarity, solder bridges, and open circuits after component placement and soldering. AOI provides rapid and consistent inspection, significantly reducing human error and enhancing overall quality early in the assembly process, crucial for the high-density nature of smart distribution box PCBs.
Advanced PCB Technologies for Smart Distribution
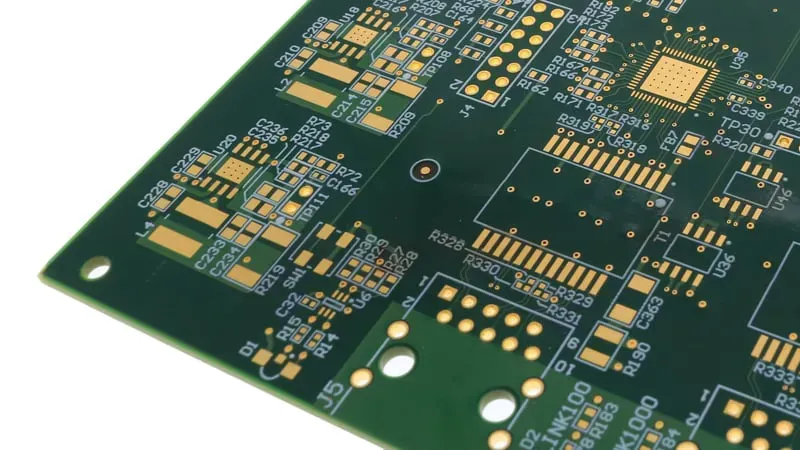
The evolution of smart distribution boxes demands not just reliable but also increasingly sophisticated PCB solutions. Advanced PCB technologies are pivotal in enabling the high-density integration, enhanced signal integrity, and superior thermal management required for these intelligent systems. These innovations allow for compact designs with greater functionality, directly contributing to the efficiency, safety, and data processing capabilities of modern power distribution networks.
- Multi-Layer PCBs for Enhanced Functionality
Multi-layer PCBs, featuring more than two layers of conductive material, are fundamental for smart distribution boxes. They provide significantly increased routing density, allowing for complex circuit designs within a smaller footprint. This is crucial for integrating microcontrollers, communication modules, and sensing elements while maintaining signal integrity and reducing electromagnetic interference (EMI). - Blind and Buried Vias for Compactness
Blind vias connect an outer layer to one or more inner layers, while buried vias connect only inner layers. These advanced drilling techniques minimize the space required for interconnections, enabling higher component density and more compact board designs. For smart distribution boxes where space is often at a premium, blind and buried vias facilitate complex routing and better thermal dissipation by freeing up surface area. - Embedded Components for Miniaturization and Performance
Embedding components, such as resistors, capacitors, and even active devices, directly into the PCB substrate is a cutting-edge technology. This approach significantly reduces board size, improves electrical performance by shortening trace lengths, and enhances reliability by protecting sensitive components from environmental factors. For smart distribution, embedded components lead to more robust, smaller, and higher-performing control units. - High-Frequency Laminates for Data Communication
With smart distribution boxes increasingly relying on robust data communication (e.g., Wi-Fi, LoRa, 5G), the use of high-frequency laminates becomes essential. Materials like PTFE or specialized ceramic-filled hydrocarbons offer stable dielectric constants and low dissipation factors, ensuring minimal signal loss and distortion at higher frequencies, critical for reliable data transmission. - Integrated Sensor Technologies for Predictive Maintenance
Advanced PCBs can integrate a multitude of sensors directly onto the board, including temperature, humidity, vibration, and current sensors. This integration allows smart distribution boxes to perform real-time monitoring of their operational environment and internal conditions, enabling predictive maintenance, fault detection, and optimized energy management.
Zero One Solution Limited: Your Partner for Smart Distribution Box PCB Solutions
Zero One Solution Limited stands at the forefront of providing comprehensive, high-quality PCB solutions specifically tailored for smart distribution boxes. Our extensive experience, rapid prototyping capabilities, and end-to-end service model ensure that your innovative smart energy projects are supported by the most reliable and efficient PCB technology from concept to production. We are committed to accelerating your product development cycle and bringing cutting-edge solutions to market with unparalleled precision and speed.
- Integrated PCB Design & Engineering
Leveraging decades of expertise, our design team specializes in creating robust and intelligent PCB layouts optimized for the demanding environment of smart distribution boxes. We focus on critical aspects like thermal management, EMI shielding, high-current path design, and signal integrity to ensure peak performance and reliability. Our collaborative approach integrates seamlessly with your R&D efforts, transforming complex requirements into highly functional PCB designs that meet stringent industry standards (e.g., IEC, UL). - Rapid Prototyping & Iteration
As a leader in rapid-response R&D prototype manufacturing, Zero One Solution Limited significantly reduces your time-to-market. Our agile prototyping process allows for quick iterations and rigorous testing, enabling efficient validation of your smart distribution box designs. This rapid turnaround capability is crucial for identifying and addressing potential issues early, saving valuable time and resources in the development phase. We empower you to accelerate innovation by providing functional prototypes within days, not weeks or months. - Advanced Manufacturing & Assembly
Our state-of-the-art manufacturing facilities in Shenzhen, coupled with a robust global supply chain network, ensure the highest quality production of smart distribution box PCBs. We employ advanced manufacturing techniques, including multi-layer PCB fabrication, blind/buried via technology, and precise surface-mount technology (SMT) assembly. Every board undergoes rigorous quality control, including Automated Optical Inspection (AOI), X-ray inspection, and in-circuit testing (ICT), to guarantee flawless performance and adherence to IPC Class 2/3 standards, essential for critical power infrastructure applications.
Case Studies: Successful Smart Distribution Box PCB Projects
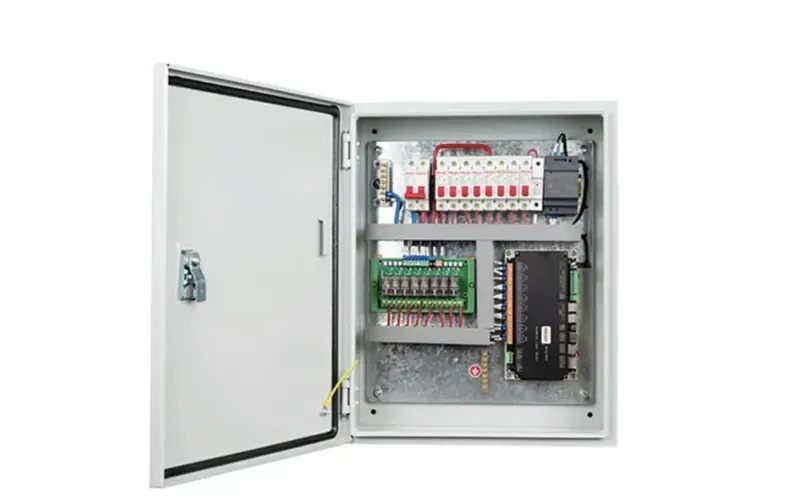
Zero One Solution Limited's commitment to innovation and engineering excellence is best demonstrated through our successful collaborations on advanced Smart Distribution Box PCB projects. These case studies highlight our capability to transform complex requirements into robust, high-performance PCB solutions that drive efficiency and reliability in modern power distribution systems.
Project Title | Challenge | Zero One Solution | Impact |
---|---|---|---|
Advanced Grid Monitoring Unit | Integration of diverse sensor data with real-time processing and communication on a compact board. | Designed a 12-layer HDI PCB with impedance-controlled lines, enabling high-speed data acquisition and integrated wireless modules (LoRa, NB-IoT). | Achieved 30% reduction in board size and 25% improvement in data processing speed, leading to enhanced grid stability and fault detection. |
Project Title | Challenge | Zero One Solution | Impact |
---|---|---|---|
Residential Smart Metering Hub | Development of a cost-effective, high-reliability PCB for harsh residential environments, requiring precise power measurement and secure data transmission. | Utilized a robust FR-4 material with enhanced thermal properties and implemented precise analog and digital ground plane isolation techniques. Provided full DFM/DFA analysis. | Reduced manufacturing costs by 15% and increased product lifespan by 20%, resulting in higher consumer satisfaction and lower maintenance. |
Project Title | Challenge | Zero One Solution | Impact |
---|---|---|---|
Industrial Power Management System | Creation of a high-power density PCB capable of handling significant current loads while maintaining thermal integrity and supporting modular expansion. | Developed a metal core PCB (MCPCB) solution for superior thermal dissipation, combined with a modular connector design to facilitate future upgrades and scalability. | Improved thermal efficiency by 40%, preventing overheating and extending component life, critical for continuous industrial operation. |
FAQs About Smart Distribution Box PCBs
Navigating the complexities of Smart Distribution Box PCB solutions can raise numerous questions regarding design, manufacturing, and assembly. This section addresses the most frequently asked questions, providing clear and authoritative answers to help you understand the critical aspects of these specialized PCBs and the value they bring to modern power management systems.
- What specific challenges do Smart Distribution Box PCBs present in terms of environmental factors?
Smart distribution boxes operate in diverse and often harsh environments, necessitating PCBs that can withstand significant temperature fluctuations, humidity, dust, and potential electromagnetic interference (EMI). Key challenges include ensuring reliable operation in extreme temperatures, preventing corrosion due to moisture, and mitigating signal degradation from EMI, all of which require robust material selection and meticulous design practices for resilience and longevity. Zero One Solution Limited addresses these through high-Tg laminates, conformal coatings, and optimized grounding planes to ensure robust performance in demanding conditions. - How do multi-layer PCBs benefit Smart Distribution Box applications?
Multi-layer PCBs are crucial for Smart Distribution Box applications because they enable higher component density and shorter signal paths. This translates to reduced EMI, improved signal integrity, and the ability to integrate complex functionalities within a compact footprint. For smart distribution, this means more precise control, advanced data processing, and greater reliability in managing electrical loads and communications, directly supporting the integration of smart grid technologies and IoT capabilities. - What role does thermal management play in the reliability of Smart Distribution Box PCBs?
Thermal management is paramount for Smart Distribution Box PCB reliability due to the high currents and power dissipation involved. Inadequate thermal design can lead to component overheating, accelerated degradation, and ultimately system failure. Effective thermal management, including optimized copper pours, thermal vias, and the use of metal core PCBs or specialized substrates, ensures components operate within their safe temperature limits, extending the lifespan and ensuring the consistent performance of the smart distribution system. - Why is high-density interconnect (HDI) technology important for Smart Distribution Box PCBs?
HDI technology is vital for Smart Distribution Box PCBs as it allows for increased routing density and miniaturization, enabling the integration of more sophisticated features and higher processing power within limited space. This is critical for smart distribution systems that require extensive sensor integration, communication modules, and advanced control circuitry. HDI facilitates the compact packaging of complex digital and analog circuits, leading to more efficient, intelligent, and space-saving distribution box designs.
- What industry standards are crucial for Smart Distribution Box PCB manufacturing and assembly?
Adherence to industry standards like IPC-A-610 (Acceptability of Electronic Assemblies), IPC-6012 (Qualification and Performance Specification for Rigid Printed Boards), and IPC-J-STD-001 (Requirements for Soldered Electrical and Electronic Assemblies) is crucial for Smart Distribution Box PCB manufacturing and assembly. These standards ensure high-quality production, reliability, and interoperability of the PCBs, which are vital for safety and performance in critical power infrastructure. Compliance guarantees that the PCBs meet rigorous performance and environmental criteria.
In conclusion, the PCB is the nerve center of any smart distribution box, and choosing the right PCB solution provider is critical for ensuring optimal performance, reliability, and longevity. Zero One Solution Limited offers comprehensive PCB solutions tailored to the specific needs of smart distribution box manufacturers, from design and prototyping to manufacturing and assembly. With our expertise, advanced technology, and commitment to quality, we empower our clients to develop innovative and efficient smart distribution systems that meet the demands of today's dynamic energy landscape. Contact Zero One Solution Limited today to discuss your smart distribution box PCB needs and discover how we can help you achieve your goals.
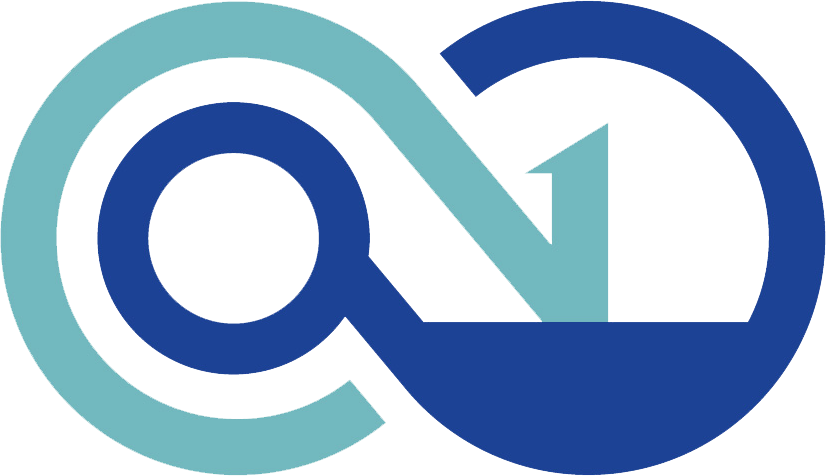