Capacitor Compressor: The Unsung Hero of Your Cooling System
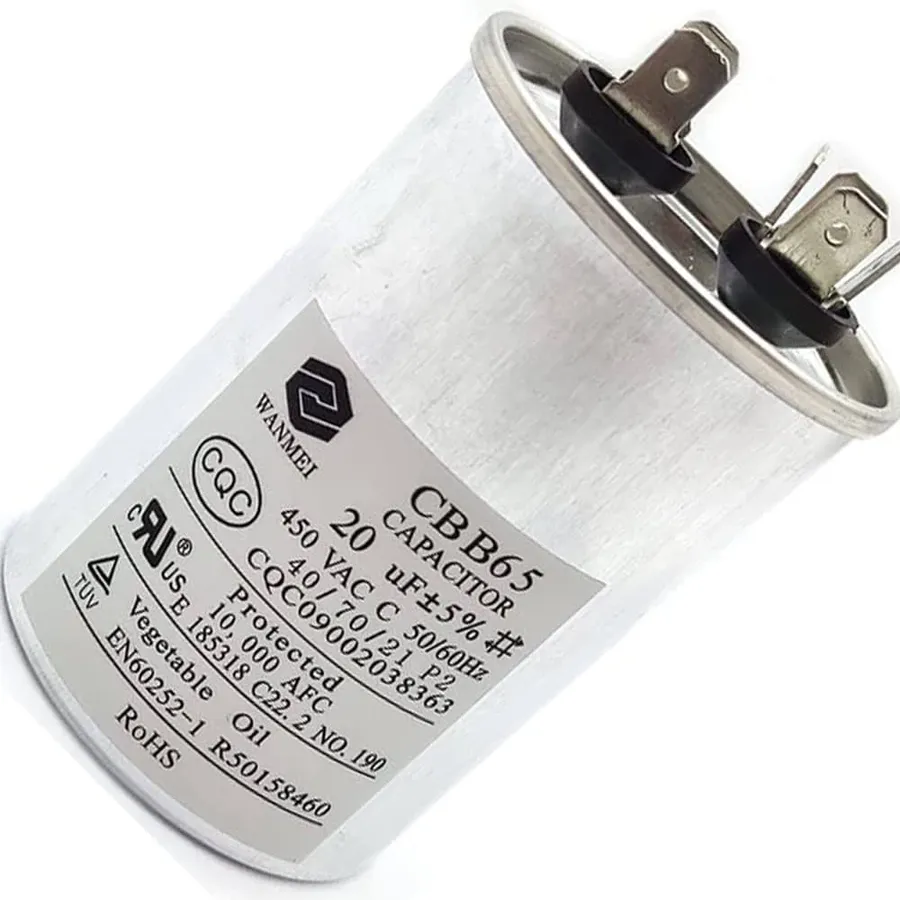
In our daily lives, the hum of air conditioners or the reliable chill of a refrigerator is often taken for granted. These crucial appliances, powered by motors, rely on a seemingly small component: the capacitor compressor. Much like a sprinter needing an initial burst of energy, the capacitor provides the necessary jolt to start the compressor, ensuring smooth and efficient operation. This article will delve into the world of capacitor compressors, exploring their function, troubleshooting, and essential maintenance to keep your cooling systems running optimally.
Understanding the Role of a Capacitor in a Compressor
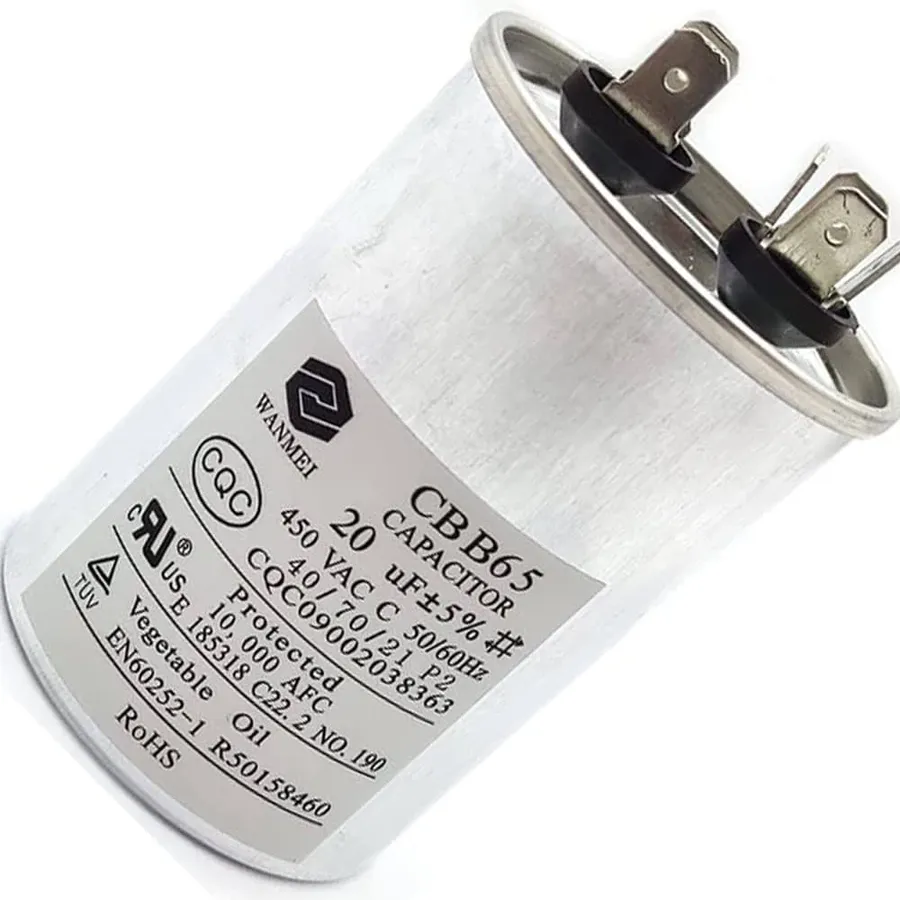
A capacitor in a compressor acts as a crucial energy storage device, providing the necessary surge of electrical power to initiate the compressor motor's rotation. This initial boost is particularly critical because electric motors require significantly more torque to start than to continue running. Capacitors are thus fundamental to the reliable operation of compressors, ensuring they can consistently overcome static inertia and begin their cycle.
There are two primary types of capacitors used in compressor systems: start capacitors and run capacitors. Start capacitors provide a high-energy, short-duration burst of power to get the motor spinning, after which they typically disengage from the circuit. Run capacitors, on the other hand, provide a lower but continuous boost to the motor while it operates, which improves energy efficiency and reduces motor wear. Understanding the distinction is essential for effective maintenance and troubleshooting.
Types of Capacitors Used in Compressor Systems
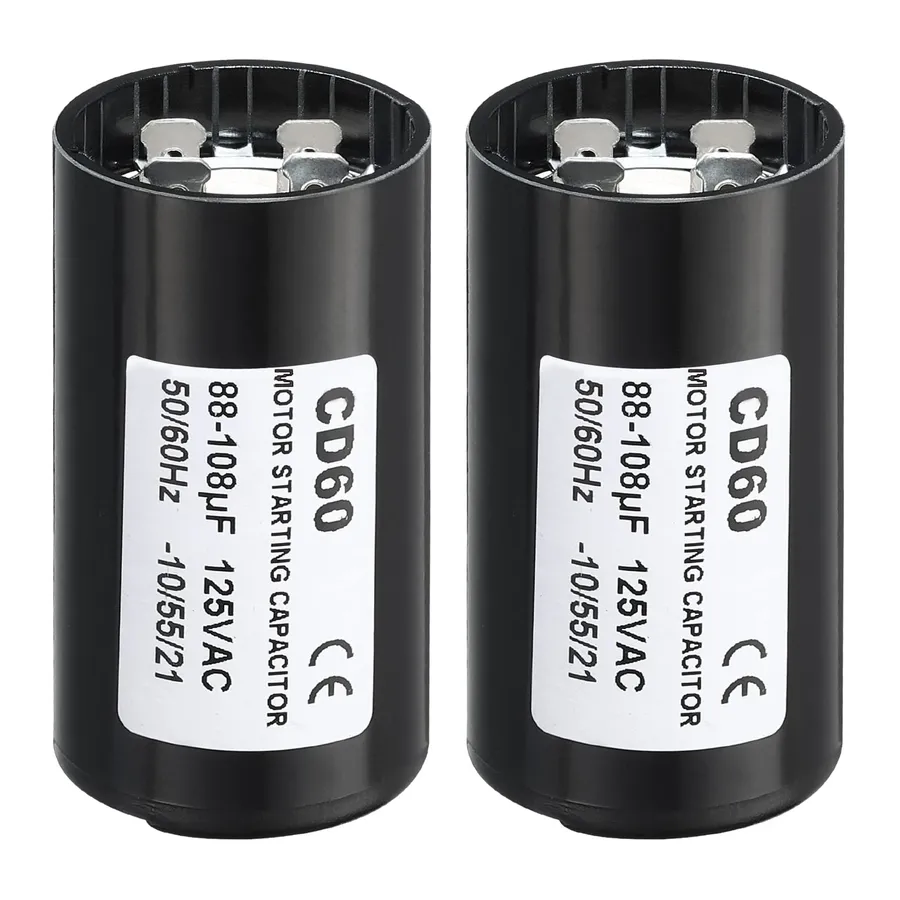
Compressor systems utilize different types of capacitors, each designed for specific functions. These capacitors are crucial for the efficient and reliable operation of the compressor motor. The primary types include start capacitors, run capacitors, and dual run capacitors, each serving a distinct purpose within the system.
Capacitor Type | Function | Application | Characteristics |
---|---|---|---|
Start Capacitor | Provides a high-energy surge for initial motor start-up. | Used during the initial starting phase of the compressor motor. | Typically a higher capacitance rating than run capacitors. Designed for short-term use and is not continuously in the circuit. |
Run Capacitor | Maintains the motor's electrical phase during continuous operation. | Used to keep the motor running smoothly once started. | Lower capacitance than start capacitors, designed for continuous use during motor operation. |
Dual Run Capacitor | Combines the functions of a start and run capacitor. | Used in systems requiring both starting and running capacitance, such as some HVAC systems. | Contains three terminals: one common, one for the compressor fan, and one for the compressor motor. |
Recognizing the Symptoms of a Failing Capacitor Compressor
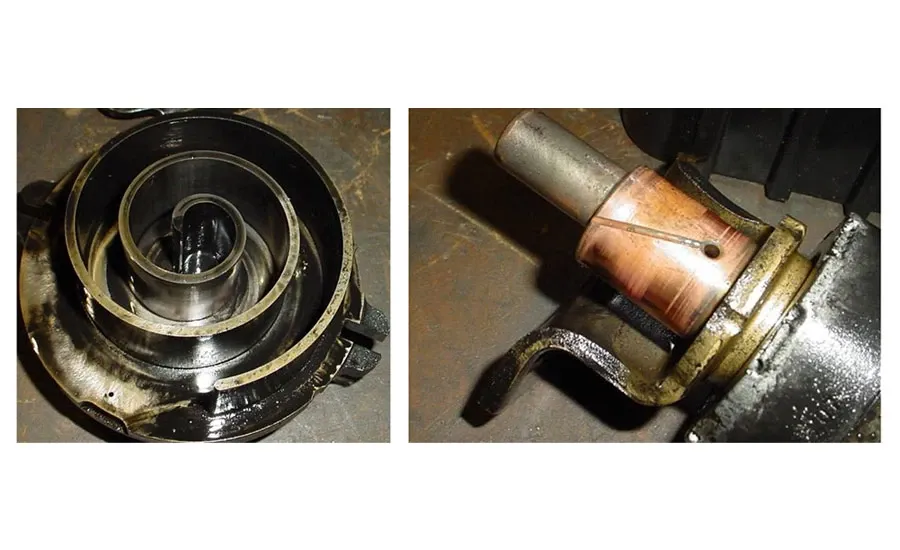
A failing compressor capacitor can manifest in several ways, often mimicking other compressor issues, making accurate diagnosis crucial. These symptoms typically indicate the capacitor is no longer efficiently storing and releasing the electrical charge necessary to start and run the compressor motor. Identifying these signs early can prevent further damage and more costly repairs.
- Slow or Delayed Start-up
The compressor struggles to initiate, taking longer than usual to start. This delay is due to the capacitor's reduced capacity to provide the necessary power surge. The motor might try to start repeatedly with a struggling or groaning sound. - Humming Sounds
A persistent humming noise from the compressor unit, especially upon start-up, often indicates the capacitor is not providing sufficient initial torque to get the motor running. This humming often occurs as the motor repeatedly attempts to engage, drawing increased current without starting properly. - Reduced Cooling Efficiency
The overall cooling capacity of the system decreases, even if the compressor is running. This is because a weakened capacitor can cause the motor to run inefficiently, reducing its performance and the amount of refrigerant that is cycled, leading to insufficient cooling. - Compressor Overheating
A failing capacitor can cause the compressor motor to overheat due to inefficient start up and run conditions and could lead to premature failure. This overheating could be detected by excessive warmth coming from the compressor unit. - Visible Physical Damage to the Capacitor
Bulging or leaking capacitors can indicate a failure and are usually the result of extreme heat and pressure within the component. In some cases the capacitor may have a cracked or distorted casing.
The primary cause of capacitor failure is the degradation of the dielectric material, the insulating material, within the capacitor, which can happen through heat, age, and the passage of high voltage. Voltage surges, incorrect capacitor ratings, and exposure to extreme temperatures can expedite the degradation.
DIY or Professional Help: When to Replace a Capacitor Compressor
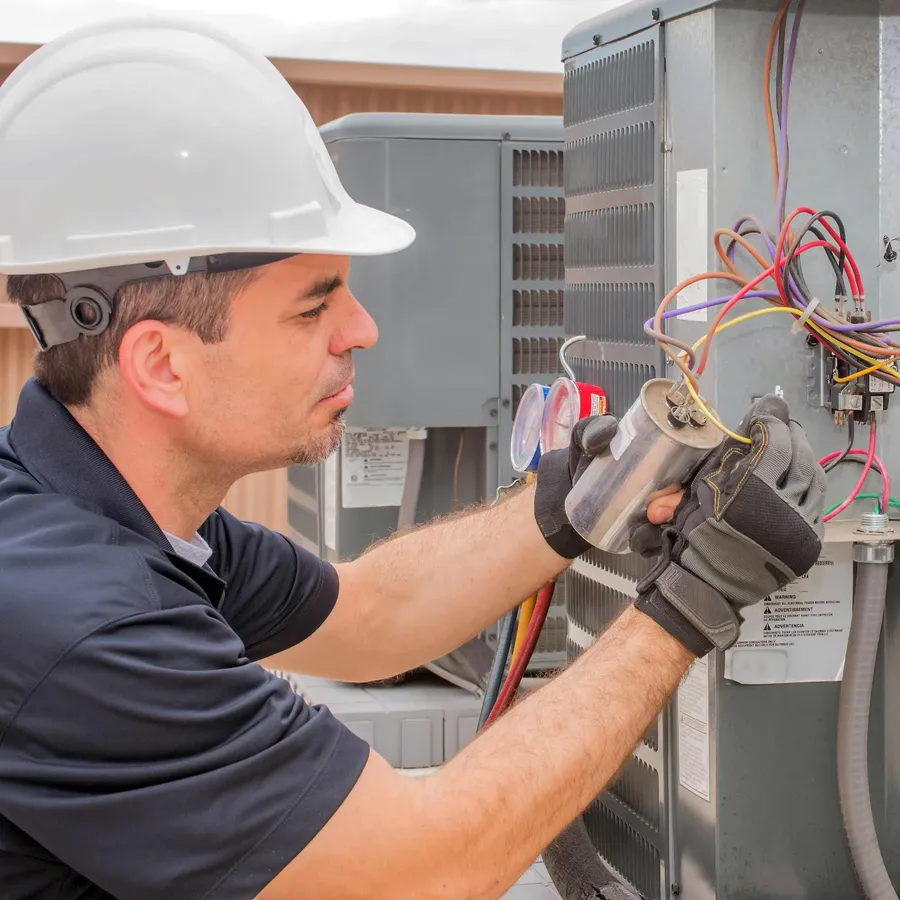
Deciding whether to replace a compressor capacitor yourself or call a professional depends largely on your comfort level with electrical work and the complexity of your system. While a capacitor replacement can be a straightforward task for some, it involves working with potentially dangerous electrical components and high-voltage systems. Proper precautions must be taken. If improperly handled, capacitor replacements can lead to severe electrical shock or damage to the equipment. Understanding when a DIY approach is appropriate and when to call an expert is critical for safety and success.
- When DIY is a Viable Option
If you have prior experience working with electrical components, a strong understanding of electrical safety, possess the right tools like a multimeter, and are confident in following detailed instructions, a DIY replacement might be suitable. This typically involves disconnecting power, identifying the correct replacement capacitor, discharging the old capacitor, and installing the new one. The compressor system is relatively simple with easy access to the capacitor. - When to Seek Professional Assistance
If you are unfamiliar with electrical work, unsure about the diagnosis, dealing with complex wiring or hard-to-access components, or if the compressor system is under warranty, it's always best to call a qualified HVAC technician. Technicians have specialized knowledge, training, tools, and safety equipment that are required for a safe and effective repair. Additionally, they can diagnose other potential issues in the system that might not be obvious to a novice. - Key Safety Considerations
Regardless of whether you choose DIY or professional help, ALWAYS de-energize the system by turning off the breaker and checking the power is off with a multimeter. Be sure to discharge the old capacitor before handling, and verify proper wiring connections to avoid damage to the compressor or risk of electrical shock. Using insulated tools and proper PPE should be a priority for personal safety.
Step-by-Step Guide to Safely Testing a Compressor Capacitor
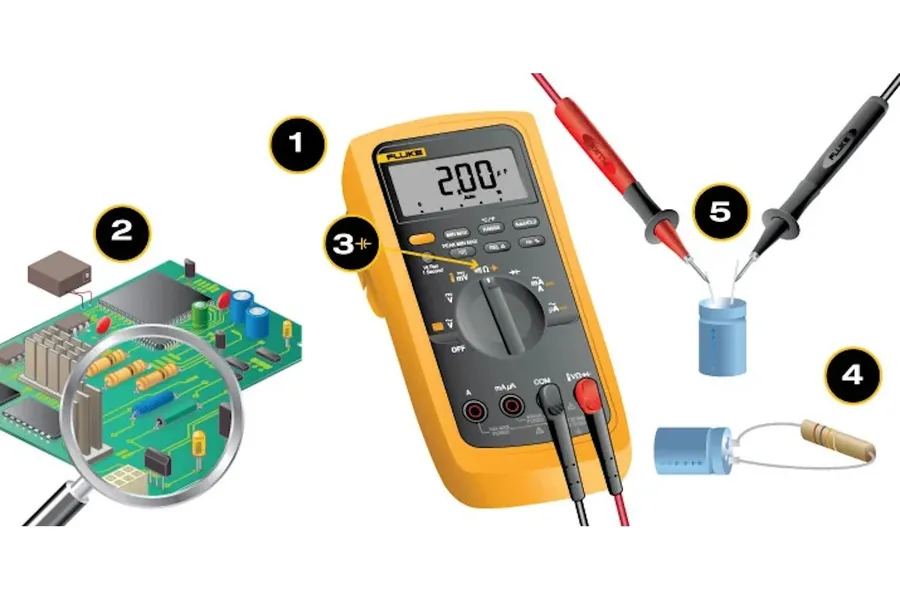
Testing a compressor capacitor is crucial for diagnosing issues in your cooling or refrigeration systems. A multimeter can accurately assess the capacitor's functionality. This process requires careful execution to avoid electrical hazards, focusing on safety, precision, and proper understanding of the testing procedure.
- Safety First: Disconnect Power
Before commencing any testing, completely disconnect the power supply to the compressor unit. This step is paramount to prevent electrical shock. Verify the power is off using a non-contact voltage tester. - Discharge the Capacitor
Capacitors store electrical charge, even when disconnected. Use a screwdriver with an insulated handle to carefully short the capacitor terminals. This will safely discharge any residual power. Confirm discharge with the non-contact voltage tester after shorting. - Access the Capacitor
Locate the capacitor within the compressor unit. This typically involves removing an access panel. Note the wiring connections before disconnecting any wires. Taking photos can help with correct reconnection later. - Disconnect the Capacitor
Carefully disconnect the wires connected to the capacitor terminals. Use insulated pliers and take note of each wire’s position for correct reassembly. Ensure wires are kept from touching each other or the metal case during testing. - Prepare Your Multimeter
Set your multimeter to measure capacitance, usually denoted by 'µF' or 'nF'. Ensure it is set to an appropriate range, usually starting at the highest setting. Many digital multimeters automatically adjust, but manual range selection may be necessary for older models. - Test the Capacitor
Connect the multimeter probes to the capacitor terminals. The meter will display the capacitor's capacitance value. Compare this value to the capacitor's rated capacitance (typically printed on the capacitor casing). A reading significantly lower than the rated value indicates a failing capacitor. - Assess the Reading
A healthy capacitor should read within approximately +/- 5-10% of its rated microfarad (µF) value. If the multimeter reads zero or vastly different from its rated capacity, it requires replacement. Look for any obvious signs of damage like bulging or leaks on the capacitor before concluding.
Choosing the Correct Replacement Capacitor for Your Compressor
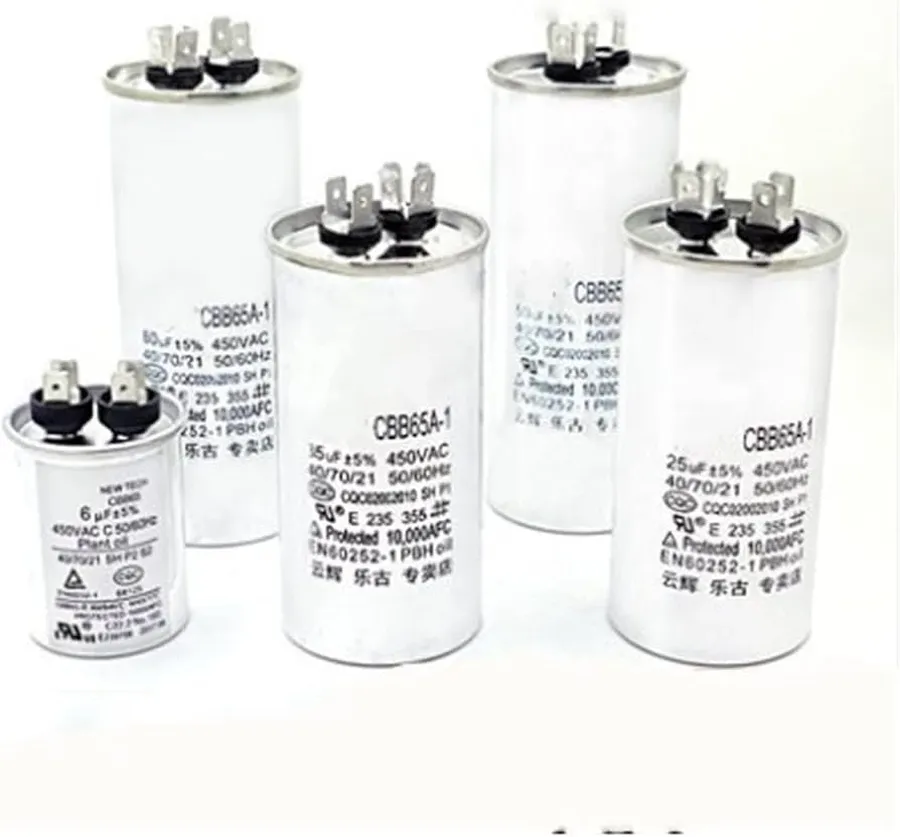
Selecting the correct replacement capacitor for your compressor is crucial for ensuring proper operation and longevity. A mismatch in specifications can lead to compressor damage or failure. The primary factors to consider are the capacitance, measured in microfarads (µF), and the voltage rating. Always prioritize matching or exceeding the original capacitor's specifications to guarantee compatibility and safety.
Parameter | Description | Importance |
---|---|---|
Capacitance (µF) | The capacity of the capacitor to store electrical charge. | Must match the original capacitor's rating. A difference can prevent the compressor from starting. |
Voltage Rating (VAC) | The maximum voltage the capacitor can safely withstand. | Replacement capacitor's voltage rating must be equal to or higher than original. Underrated capacitors can fail catastrophically. |
Physical Size | The dimensions of the capacitor. | Should be comparable to ensure a proper fit in the compressor unit. Mismatches could cause mounting issues. |
Terminal Type | The style of the electrical connection terminals | Should match to facilitate easy installation. A different terminal type would require modification |
Type (Start, Run, Dual) | Type of capacitor which depends on its function | Match the type to ensure it serves the right purpose |
When selecting a replacement capacitor, take these critical steps. First, carefully note the original capacitor's microfarad (µF) rating and voltage. This is usually printed directly on the capacitor's casing. Second, consider if the capacitor is a start, run, or dual-run capacitor, which can be determined based on the application. Third, the physical dimensions should be considered to ensure proper fit and installation. Finally, make sure that the terminals match. You can purchase replacement capacitors at local hardware stores or online retailers.
Frequently Asked Questions About Capacitor Compressors
This section addresses common queries regarding capacitor compressors, offering concise, authoritative answers to assist in understanding their function, troubleshooting, and replacement. The aim is to clarify key aspects related to these crucial components within compressor systems.
- What is the primary function of a capacitor in a compressor?
A capacitor's primary role in a compressor system is to provide a high-energy electrical surge to initiate the compressor motor's rotation. It acts as a temporary energy storage device, delivering the initial torque required to overcome inertia and start the motor. The capacitor ensures the motor starts smoothly and reliably. - How can I differentiate between a faulty capacitor and a faulty compressor?
A failing capacitor typically exhibits symptoms such as slow or delayed start-up, a humming sound from the compressor, or complete failure to start. A faulty compressor, on the other hand, might show symptoms like excessive noise, overheating, or a burnt smell. Accurate diagnosis requires testing both components with a multimeter to measure capacitance (for the capacitor) and resistance (for the compressor). - Is it possible to operate an AC compressor without a capacitor?
No, it is generally not advisable, and often impossible, to run an AC compressor without a functioning capacitor. The capacitor provides the necessary electrical boost to start the motor. Without it, the motor will likely fail to start, or at the very least experience a greatly reduced lifespan due to starting stress. - What is the typical cost to replace a compressor capacitor?
The cost to replace a compressor capacitor can vary greatly depending on the capacitor type, labor costs, and location. For DIY replacement, the capacitor itself might cost between $10 to $50. Professional replacement, including labor, can range from $100 to $300 or higher. It’s best to get a quote from a qualified professional before engaging in repair. - Are there any inherent safety risks associated with replacing a compressor capacitor?
Yes, replacing a capacitor poses electrical shock hazards. Capacitors can store a high electrical charge even after the power has been disconnected. It's crucial to discharge the capacitor using a properly rated resistor before handling it. Additionally, correct wiring and capacitor sizing are critical to safe and effective replacement; therefore, if you are uncomfortable with electrical work, it's best to seek professional assistance. - What is the lifespan of a typical compressor capacitor?
A typical compressor capacitor's lifespan varies depending on several factors, including operating temperature, electrical load, and ambient conditions. Generally, it can range from 3 to 10 years. Regular maintenance, like inspecting and ensuring good ventilation, can help prolong its life. However, the capacitor should be seen as a consumable component that needs periodic replacement. - How do I select the right capacitor for my compressor?
Selecting the correct replacement capacitor requires matching the microfarad (μF) rating and voltage specified on the existing capacitor. Using a capacitor with a mismatched rating can cause compressor malfunction and damage. It’s essential to use a compatible capacitor to ensure safe and efficient operation. Always confirm the specifications of your compressor and select the correct capacitor by consulting the product manual or the manufacturer's website.
Extending the Life of Your Compressor Capacitor
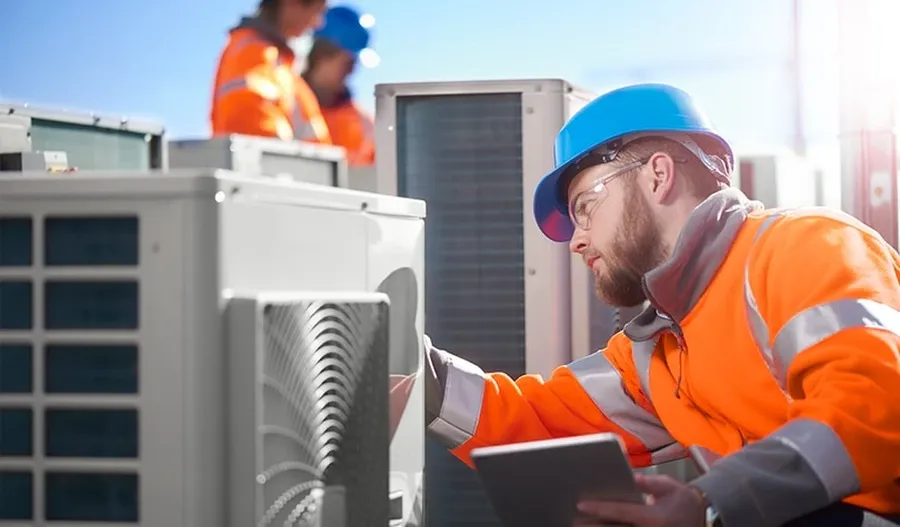
Extending the lifespan of your compressor capacitor is crucial for maintaining the efficiency and reliability of your cooling system. Implementing preventative maintenance measures can significantly reduce the likelihood of premature failure, saving you time and money on repairs or replacements.
- Regular Inspections
Perform routine visual inspections of the capacitor. Look for signs of physical damage such as bulging, cracking, leaking, or corrosion. These indicators often signal that the capacitor is nearing the end of its operational life or has already failed. - Ensure Proper Ventilation
Capacitors, like other electrical components, generate heat during operation. Adequate airflow around the compressor unit is vital to prevent overheating. Make sure that the compressor's ventilation openings are not blocked by debris or vegetation. Restricted airflow can cause the capacitor to overheat, reducing its performance and lifespan. - Stabilize Voltage Fluctuations
Voltage fluctuations and spikes are detrimental to capacitor health. Install surge protectors or voltage stabilizers to protect the compressor and its capacitor from power surges. A stable power supply will ensure the capacitor operates within its design parameters and reduce the risk of damage. - Avoid Overloading the System
Operating the compressor beyond its rated capacity puts extra stress on the capacitor and the motor. Use the compressor within the manufacturer's specifications to prevent component wear and premature failure. Check the compressor unit specifications and avoid exceeding them. - Professional Servicing
Schedule regular professional servicing. A qualified technician can conduct thorough inspections, clean internal components, and measure the capacitance value of the capacitor to assess its health. Professional maintenance allows for early detection of potential issues and can prevent costly breakdowns.
Capacitor Compressor: Comparative Analysis Table
Understanding the nuances between different capacitor types used in compressor systems is crucial for selecting the right component for optimal performance and longevity. This comparative analysis table highlights the key differences in their applications, costs, lifespan and features.
Feature | Start Capacitor | Run Capacitor | Dual Run Capacitor |
---|---|---|---|
Primary Function | Provides high starting torque to motor, only used briefly during start-up | Provides continuous current for efficient motor operation during run-time | Provides continuous current to two motor components such as a compressor motor and fan motor, while also using a common capacitor |
Typical Applications | Air conditioners, refrigerators, and some larger compressors where high torque is needed for initial motor rotation. | HVAC systems, refrigerators and freezers, pumps and other appliances where sustained power is needed to maintain motor rotation. | Typically used in HVAC systems where both the compressor and fan motors need capacitor assistance. |
Capacitance (µF) | High (e.g. 50-300 µF), value can vary greatly depending on the compressor. | Lower (e.g., 5-60 µF) compared to start capacitors, often precisely matched to the motor requirements. | Varies, often two or more ratings are printed on a single capacitor such as 30+5 µF. |
Voltage Rating | Typically rated for higher AC voltage, usually 125V or higher but only under short use | Typically rated for continuous duty AC voltage, generally around 370 or 440 VAC. | Typically rated for continuous duty AC voltage, generally around 370 or 440 VAC, same as a run capacitor. |
Lifespan | Shorter life as they operate briefly. Expected to last several years under normal use. Frequent starts can shorten the lifespan. | Longer lifespan than start capacitors. Generally rated for several years to 10 years, depending on operating conditions and quality. | Similar lifespan as a run capacitor when properly used and sized. |
Cost | Relatively inexpensive due to simple design and short use. | More expensive than start capacitors due to continuous duty design and quality requirements. | More expensive than start capacitors, with similar price points to run capacitors. Generally is more cost-effective than using two separate capacitors. |
Key Features | Designed for high starting torque and brief operation. | Designed for continuous operation, better internal components and higher thermal resistance | One unit saves space while providing power to multiple motor components. Reduces the number of components needed in the system. |
The capacitor compressor, though small, is a pivotal component in the functionality of your cooling systems. Understanding its role, recognizing the signs of failure, and knowing how to properly maintain it can save you from costly repairs and ensure your comfort. By taking proactive measures and implementing simple maintenance routines, you can keep your air conditioners and refrigerators humming reliably for years to come. Whether you're a seasoned DIY enthusiast or prefer to call a professional, a little knowledge about the capacitor compressor goes a long way in preserving the lifespan and efficiency of your appliances.
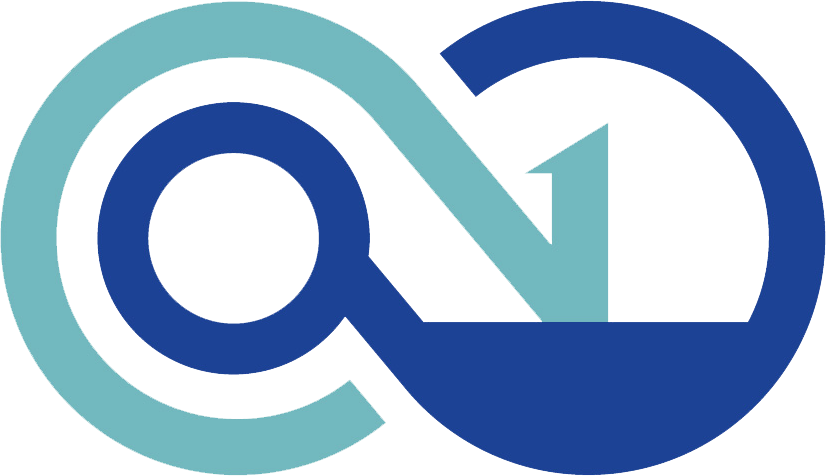