MELF Resistors: The Ultimate Guide to Cylindrical Precision
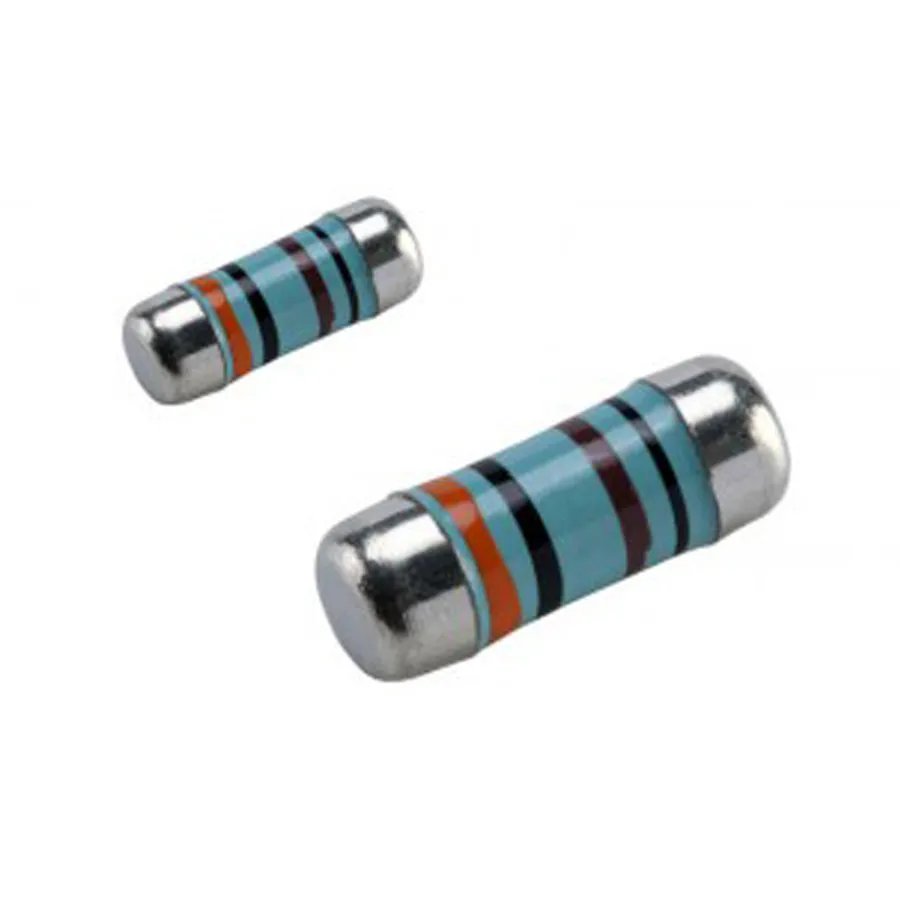
In our increasingly technology-dependent world, electronic components like the unassuming MELF resistor play a pivotal role in ensuring the reliability and performance of countless devices. From the smartphone in your hand to the complex circuitry of industrial machinery, MELF resistors are the unsung heroes, offering precision and stability that many standard components can’t match. In this article, we'll delve into the world of MELF resistors, exploring what they are, their unique advantages, and why they might just be the ideal solution for your next electronic project.
What Exactly is a MELF Resistor?
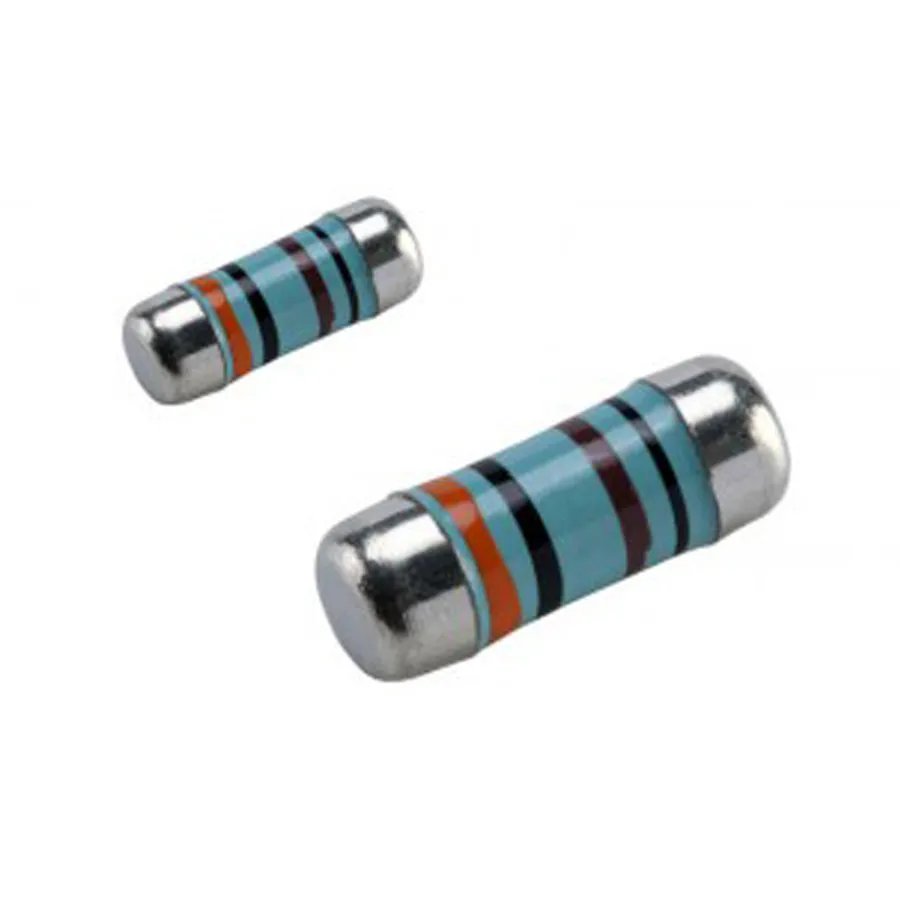
Metal Electrode Leadless Face (MELF) resistors are a distinct type of surface mount resistor characterized by their cylindrical shape, differing significantly from the more common rectangular surface mount technology (SMT) chip resistors. This unique design is not merely aesthetic; it dictates performance characteristics and suitability for specific applications. MELF resistors employ a metal electrode construction, which is a key factor in their robust performance and reliability. The 'leadless face' design indicates that the electrical connection is made via the end caps of the cylinder, rather than side contacts as in standard chip resistors.
The construction involves a ceramic core on which a resistive film is deposited, often metal film, which is then laser trimmed to achieve the precise resistance value. Metal end caps are attached, providing the conductive surface for soldering to a circuit board. This construction method leads to several benefits over chip resistors, including improved power handling, stability, and heat dissipation. The cylindrical form factor also reduces stress concentrations during thermal cycling, improving reliability under harsh operating conditions. Understanding the fundamental construction and principles of MELF resistors provides insight into why they are the preferred component in demanding applications requiring high precision and long-term stability.
Key Advantages of MELF Resistors
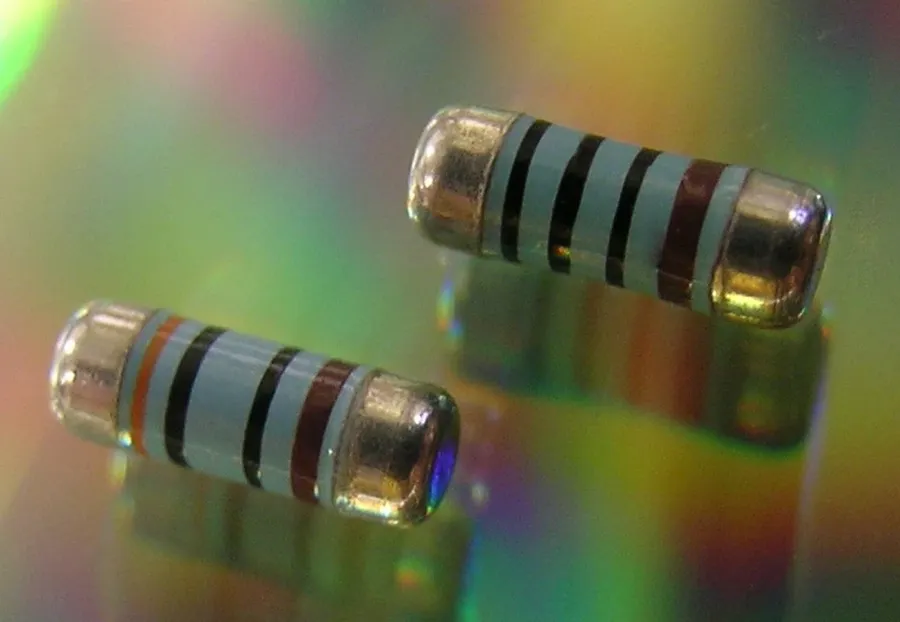
MELF (Metal Electrode Leadless Face) resistors distinguish themselves through a suite of performance advantages compared to standard chip resistors, primarily stemming from their cylindrical construction. These benefits include superior accuracy, long-term stability, high reliability, pulse load capability, thermal shock resistance, and enhanced heat dissipation.
Advantage | Description | Benefit |
---|---|---|
Superior Accuracy | Tighter manufacturing tolerances and more uniform resistive film deposition. | More precise circuit performance and reduced calibration needs. |
Long-Term Stability | Less drift in resistance value over time and under various operating conditions. | Maintains circuit performance consistency, ensuring reliability over the lifespan of the application. |
High Reliability | Robust construction reduces susceptibility to mechanical stress and environmental factors. | Lower failure rates in harsh environments, critical for long-term operation. |
Pulse Load Capability | Ability to withstand higher energy pulses without significant degradation. | Enhanced resilience in applications with transient power spikes. |
Thermal Shock Resistance | Can endure rapid temperature fluctuations without fracturing or performance changes. | Ensures stable operation across varying thermal conditions, improving durability. |
Enhanced Heat Dissipation | Cylindrical shape allows for better heat transfer and lower operating temperatures. | Reduces thermal stress on the component, increasing its operational life and performance. |
MELF Resistor vs. Standard Chip Resistors: A Detailed Comparison
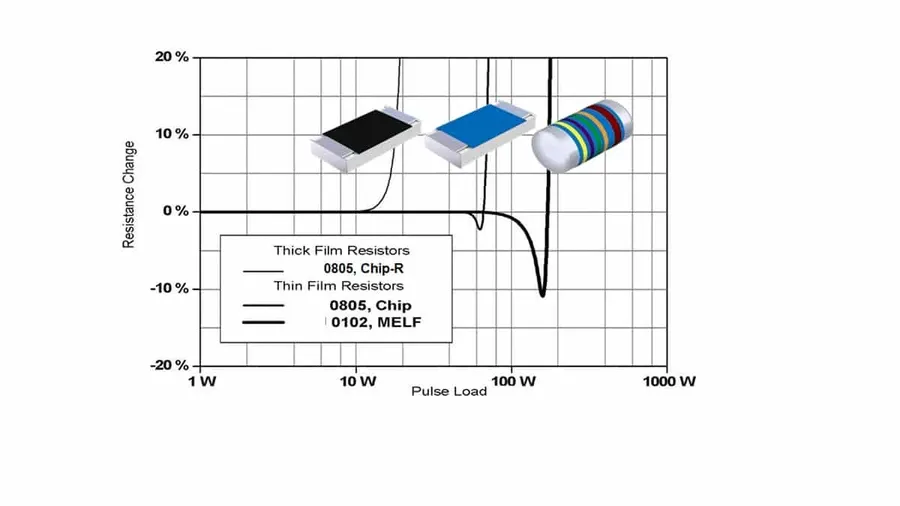
MELF (Metal Electrode Leadless Face) resistors and standard SMD (Surface Mount Device) chip resistors represent two common approaches to resistor design, each possessing distinct characteristics that make them suitable for different applications. While both serve the fundamental purpose of providing electrical resistance, their construction, performance, and optimal use-cases differ significantly.
Feature | MELF Resistors | Standard Chip Resistors (SMD) |
---|---|---|
Shape | Cylindrical | Rectangular |
Electrode Design | Metalized caps on the ends | Metalized terminals on the bottom face |
Solder Joint | Wrap-around contact | Flat contact |
Mechanical Strength | Higher, better for vibration and shock | Lower, more sensitive to stress |
Power Handling | Typically higher for similar size | Typically lower for similar size |
Pulse Load Capability | Excellent | Good |
Thermal Shock Resistance | Superior | Moderate |
Accuracy and Stability | Generally better, especially in high-precision applications | Sufficient for most general applications |
Heat Dissipation | More efficient due to cylindrical shape and metal end caps | Less efficient |
Cost | Generally higher | Generally lower |
Assembly | Requires special pick and place nozzles | Standard SMT assembly process |
Typical Application | High-reliability, high-precision, high-power applications | General-purpose applications, cost-sensitive projects |
In summary, MELF resistors offer superior performance in demanding environments where reliability, precision, and power handling are critical. Standard chip resistors, with their simpler construction and lower cost, are generally better suited for general-purpose applications.
MELF Resistor Sizes and Specifications
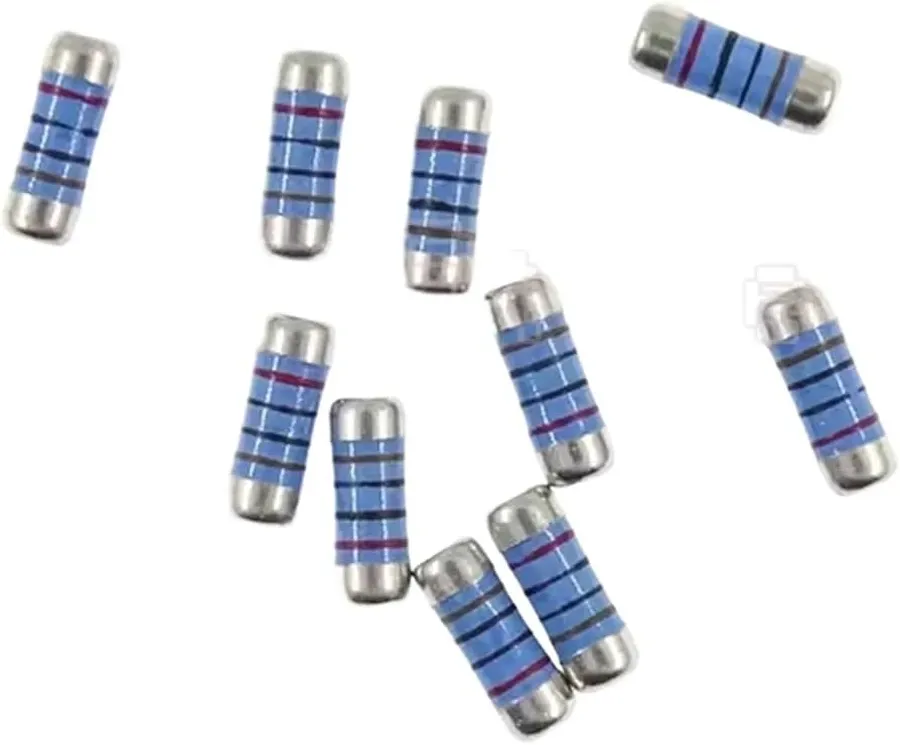
MELF (Metal Electrode Leadless Face) resistors are characterized not only by their cylindrical shape but also by their standardized sizes, each corresponding to specific dimensions, power ratings, and resistance ranges. These specifications are crucial for selecting the correct component for various applications. The most common sizes are designated using a four-digit code that relates to their physical dimensions.
Size Code | Length (mm) | Diameter (mm) | Typical Power Rating (W) | Typical Resistance Range |
---|---|---|---|---|
0102 | 3.6 | 1.5 | 0.25 | 1Ω - 1MΩ |
0204 | 4.0 | 2.2 | 0.4 | 1Ω - 10MΩ |
0207 | 6.1 | 2.2 | 0.6 | 1Ω - 20MΩ |
0309 | 8.6 | 2.5 | 1.0 | 1Ω - 22MΩ |
0411 | 11.0 | 3.5 | 1.25 | 1Ω - 30MΩ |
MELF resistors also utilize a color-coding system, similar to that of leaded resistors, to indicate their resistance value and tolerance. This system uses a series of colored bands around the resistor body. Typically, MELF resistors use a 4 or 5 band color coding system; however, a 6 band system is also found.
- 4-Band System
The first two bands represent the significant digits of the resistance value, the third band acts as a multiplier, and the fourth band specifies the tolerance. - 5-Band System
The first three bands represent the significant digits of the resistance value, the fourth band acts as a multiplier, and the fifth band specifies the tolerance. - 6-Band System
The first three bands represent the significant digits of the resistance value, the fourth band acts as a multiplier, the fifth band specifies the tolerance and the sixth band specifies the temperature coefficient.
MELF Resistor Applications
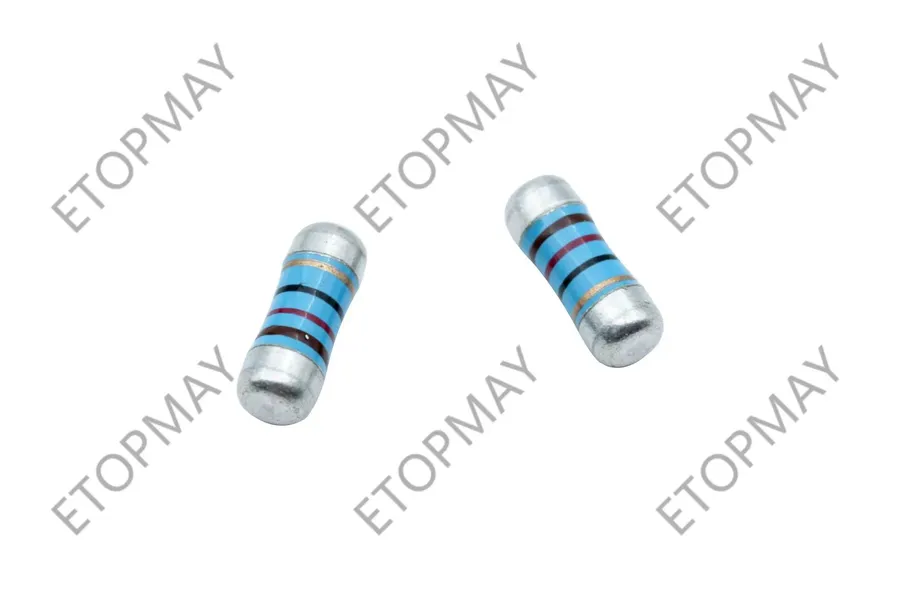
MELF resistors, with their superior performance characteristics, find widespread use across various demanding industries. Their high reliability, stability, and precision make them ideal for applications requiring robust and consistent performance in harsh conditions. This section details specific use-cases across several key sectors.
- Automotive Electronics
MELF resistors are crucial in automotive control systems, engine management, and safety features like airbags due to their resistance to thermal shock and vibration. Their ability to withstand harsh operating environments and temperature fluctuations makes them a reliable choice for automotive applications. Examples include use in Electronic Control Units (ECUs), power steering systems, and anti-lock braking systems. - Medical Equipment
The high reliability and stability of MELF resistors make them essential in medical devices, including patient monitoring equipment, diagnostic tools, and implantable devices. Precision is paramount in medical applications to ensure accurate measurements and safe operation; the low tolerance and long-term stability of MELF resistors address these requirements, for example in pacemakers, blood pressure monitors, and diagnostic imaging equipment. - Aerospace
In aerospace, MELF resistors are used in navigation systems, communication equipment, and flight control systems where reliability and performance are critical. Their robust construction and resistance to extreme temperatures and vibration make them ideal for the harsh conditions of aerospace, contributing to the dependability of navigation equipment, communication arrays, and flight control mechanisms. - Industrial Control Systems
MELF resistors are widely employed in industrial control systems and automation equipment, such as Programmable Logic Controllers (PLCs), motor drives, and sensors, where they provide reliable operation in demanding environments. Their capacity to handle pulse loads and thermal stress makes them suitable for industrial applications that undergo heavy usage, for example industrial robotics, machinery control systems and process automation equipment. - High-Precision Measuring Instruments
Due to their high accuracy and stability, MELF resistors are essential in precision measuring devices, such as laboratory instruments, multimeters, and calibrators. In applications where accuracy is the priority, the tight tolerances and high temperature stability of MELF resistors enable accurate and consistent measurements. This includes high precision voltmeters, oscilloscopes and calibration equipment.
MELF Resistor Manufacturing and Materials
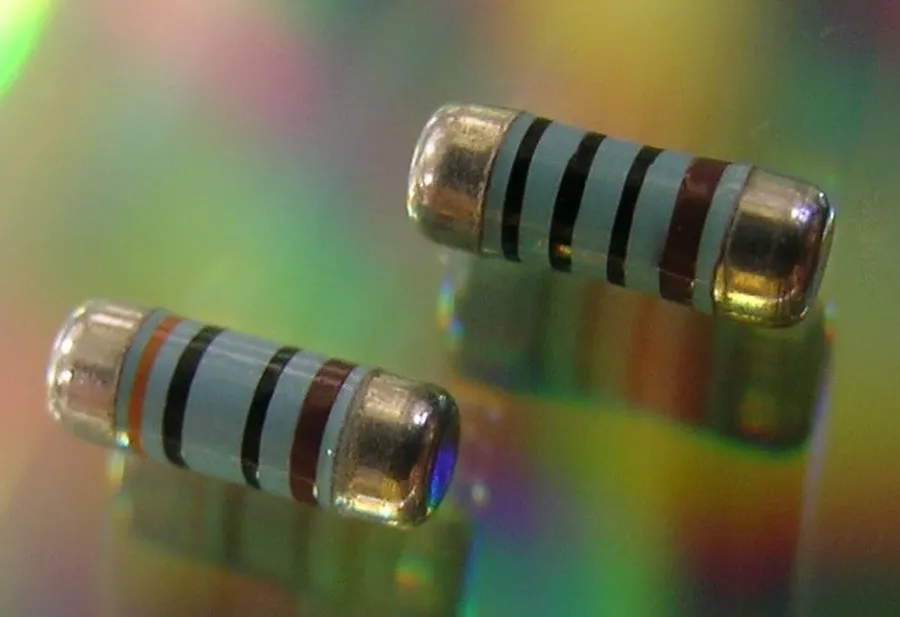
The manufacturing of MELF (Metal Electrode Leadless Face) resistors involves a precise process that integrates advanced material science and engineering techniques to achieve high performance and reliability. This process directly influences their electrical properties and durability. The key to MELF resistor excellence lies in the careful selection and processing of materials, coupled with stringent manufacturing control.
- Core Material
The core of a MELF resistor is typically a high-purity ceramic substrate, often alumina (Al₂O₃), known for its excellent electrical insulation, thermal conductivity, and mechanical strength. This material provides a stable platform for the resistive element and ensures the resistor can withstand varying thermal conditions. - Resistive Film Deposition
A thin film of resistive material is meticulously deposited onto the ceramic substrate. This film is typically composed of metal alloys such as nickel-chromium (NiCr) or tantalum nitride (Ta₂N). The exact composition and thickness of this film determine the final resistance value of the resistor, and are precisely controlled during manufacturing using techniques like sputtering or chemical vapor deposition. - Electrode Formation
Metal electrodes are formed on each end of the resistor body, using processes like thick-film printing and plating with highly conductive materials like silver or gold. These electrodes provide low-resistance contact points for circuit integration. The quality and adhesion of these electrodes are crucial for ensuring low contact resistance and excellent long term reliability. - Protective Coating
A protective coating, usually an epoxy or glass layer, is applied over the resistive film and electrodes. This coating safeguards the resistor from physical damage, moisture, and corrosive environments. The coating is also important for electrical insulation and for enhancing the long term environmental stability of the resistor. - Trimming and Testing
The final step involves trimming the resistive film to precisely adjust the resistance value to the required specification, typically with a laser trimming process. Each resistor undergoes rigorous electrical testing to confirm that it meets specified parameters, before being packaged for shipment. This ensures the resistor performs within its designed tolerances.
The selection of these materials, coupled with the precise manufacturing techniques, directly contributes to MELF resistors' key advantages, including superior long-term stability, high reliability, and excellent pulse load capability. The quality of these materials and the controlled manufacturing environment directly reduce the variability of the electrical parameters, enhancing the performance and reliability of electronic circuits. This detailed manufacturing approach highlights why MELF resistors are often preferred in high-reliability applications.
Frequently Asked Questions about MELF Resistors
This section addresses common inquiries regarding Metal Electrode Leadless Face (MELF) resistors, clarifying their distinctions, reliability, advantages, and selection criteria to ensure comprehensive understanding.
- What is a MELF resistor and how does it differ from a standard chip resistor?
MELF resistors are cylindrical surface-mount devices, unlike the rectangular shape of standard chip resistors. This cylindrical design provides enhanced mechanical strength, improved power handling capabilities and a more uniform distribution of heat, leading to superior performance in certain applications compared to chip resistors. - Are MELF resistors more reliable than standard chip resistors?
Generally, MELF resistors exhibit higher reliability than standard chip resistors, especially in harsh environments. Their robust construction, particularly the cylindrical shape and electrode design, makes them more resistant to mechanical stress, thermal shock, and vibration. This enhanced reliability is crucial in applications where failure can have serious consequences. - What are the main advantages of using MELF resistors over other resistor types?
MELF resistors boast several advantages, including superior power handling capabilities for their size, enhanced long-term stability, improved pulse load capability, and better heat dissipation due to their cylindrical design. Their robustness also ensures that they perform reliably in high-stress and harsh environments, making them ideal for demanding applications. - How do I choose the correct MELF resistor for a specific application?
Selecting the right MELF resistor involves considering several key parameters. First, you must determine the required resistance value and tolerance based on the circuit's design needs. Secondly, the power rating of the resistor should be adequate to prevent overheating. Finally, environmental factors such as operating temperature and expected mechanical stresses should be carefully considered to ensure that the chosen resistor has the correct specification and is suitable for the particular application. Consideration should also be given to the temperature coefficient of resistance and, where necessary, pulse load capability. - What power ratings are typical for MELF resistors?
MELF resistors are available in various power ratings, generally ranging from 0.25W to 2W, with specific values dependent on the physical size of the component. Common sizes include 0204, 0207, and 0102, each with different maximum power ratings. Refer to manufacturer datasheets for precise values, and always select a resistor with a power rating significantly above the circuit requirements. - What are the typical applications for MELF resistors?
MELF resistors find use in applications demanding high reliability and stability. This includes automotive electronics, industrial control systems, medical devices, aerospace, and high-precision measuring equipment. They are also preferred in circuits subjected to high mechanical stress or significant temperature fluctuations, where standard chip resistors may not be suitable. - How do MELF resistor color codes compare to standard resistor color codes?
MELF resistors use a similar color-coding system to standard axial resistors, but the color bands are printed around the cylindrical body. The color code is still based on the same standard, with each color representing a numeric value and multiplier. A calculator or datasheet is needed to accurately decode the value and tolerance of a specific MELF resistor.
Selecting the Right MELF Resistor: Key Considerations
Selecting the appropriate MELF resistor for a given application requires careful consideration of several key parameters. These parameters directly impact the performance and reliability of the circuit, and choosing incorrectly can lead to issues with accuracy, stability, and longevity. This section will outline the critical factors to consider when choosing a MELF resistor.
- Resistance Value
The nominal resistance value is the first and foremost parameter. Select a resistance value that accurately fulfills the circuit design requirements. Precise resistance values ensure that the circuit functions as designed. - Tolerance
Tolerance specifies the maximum allowed deviation from the nominal resistance value. Common tolerances are ±1%, ±0.5%, and ±0.1%. Higher precision applications require tighter tolerance resistors to ensure accurate and stable operation. - Power Rating
Power rating indicates the maximum power that the MELF resistor can safely dissipate as heat. Operation above this rating can lead to resistor damage. Calculate the expected power dissipation within your circuit and select a MELF resistor that provides adequate margin for safe operation. - Temperature Coefficient of Resistance (TCR)
TCR describes how much the resistance changes with temperature. Low TCR values indicate that the resistor’s resistance will remain stable over a range of temperatures. High precision applications usually necessitate low TCR resistors to minimise thermal induced error. - Size and Dimensions
MELF resistors come in various standardized sizes, such as 0204, 0207, and 0102. The physical dimensions of the component may be critical to compatibility with the chosen PCB footprint, and should be selected to accommodate design constraints. - Environmental Conditions
Consider operating temperature, humidity, and any other harsh environmental factors. High-stress environments require robust components with appropriate temperature and moisture ratings.
Future Trends in MELF Resistor Technology
The field of MELF resistor technology is continuously evolving, driven by the increasing demands for higher performance, smaller size, and greater environmental resilience in electronic devices. Future trends point towards significant advancements in precision, miniaturization, and the overall sustainability of these critical components.
Ongoing research and development efforts are focused on several key areas:
- Enhanced Precision
Manufacturers are striving to produce MELF resistors with tighter tolerances and lower temperature coefficients. This is crucial for applications where accuracy and stability are paramount, such as precision measuring instruments and high-frequency circuits. The move towards thinner film deposition techniques and advanced laser trimming processes allows for greater control over resistance values. - Miniaturization
As electronic devices become smaller and more densely packed, there is a pressing need to reduce the size of passive components. New designs and materials are being explored to achieve smaller MELF resistors while maintaining their electrical and thermal performance. This includes advancements in material deposition techniques, allowing for thinner conductive films and more compact designs. - Improved Environmental Performance
The electronics industry is increasingly focused on sustainability. Future MELF resistors will be engineered with environmentally friendly materials and manufacturing processes. This includes reducing hazardous substances, improving recyclability, and increasing durability to extend the lifespan of devices. There's a growing focus on materials that can withstand extreme temperatures and harsh conditions. - Advanced Materials
The use of new materials with superior electrical and thermal properties is expected to play a significant role in the future of MELF resistors. Research is being conducted on novel alloys, ceramics, and polymers that can enable improved performance, reliability, and environmental resistance. These materials will contribute to higher precision and greater stability. - Integration with Advanced Manufacturing Techniques
Integration with advanced manufacturing techniques such as 3D printing and additive manufacturing will enable customized MELF resistors that meet specific design requirements. This will provide greater flexibility in the production of devices, optimize space, and ensure maximum component performance.
MELF resistors, though sometimes overlooked, are crucial for advanced electronics. Their unique cylindrical structure and metal electrode design make them superior to standard SMT resistors in high-stress, high-reliability applications. From automotive to medical technology, MELF resistors ensure performance and stability. As technology advances, the need for such precise components will only increase, highlighting the essential role of the MELF resistor in shaping the future of electronics.
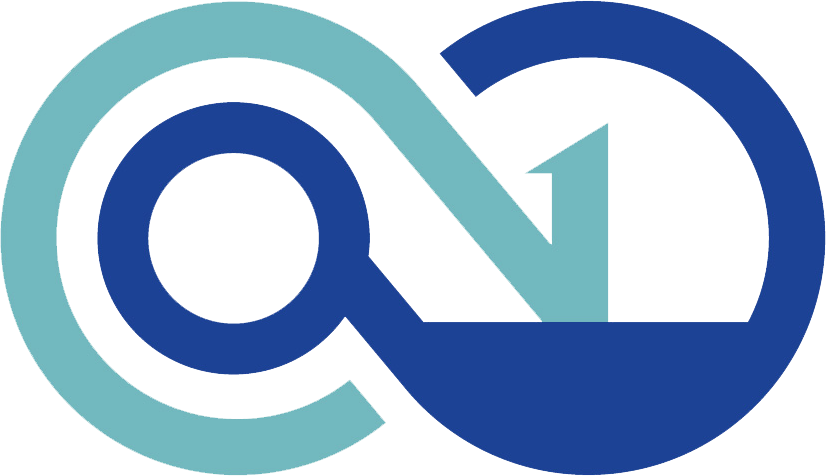