Motor Start Capacitors: Powering Up Your Motors Efficiently
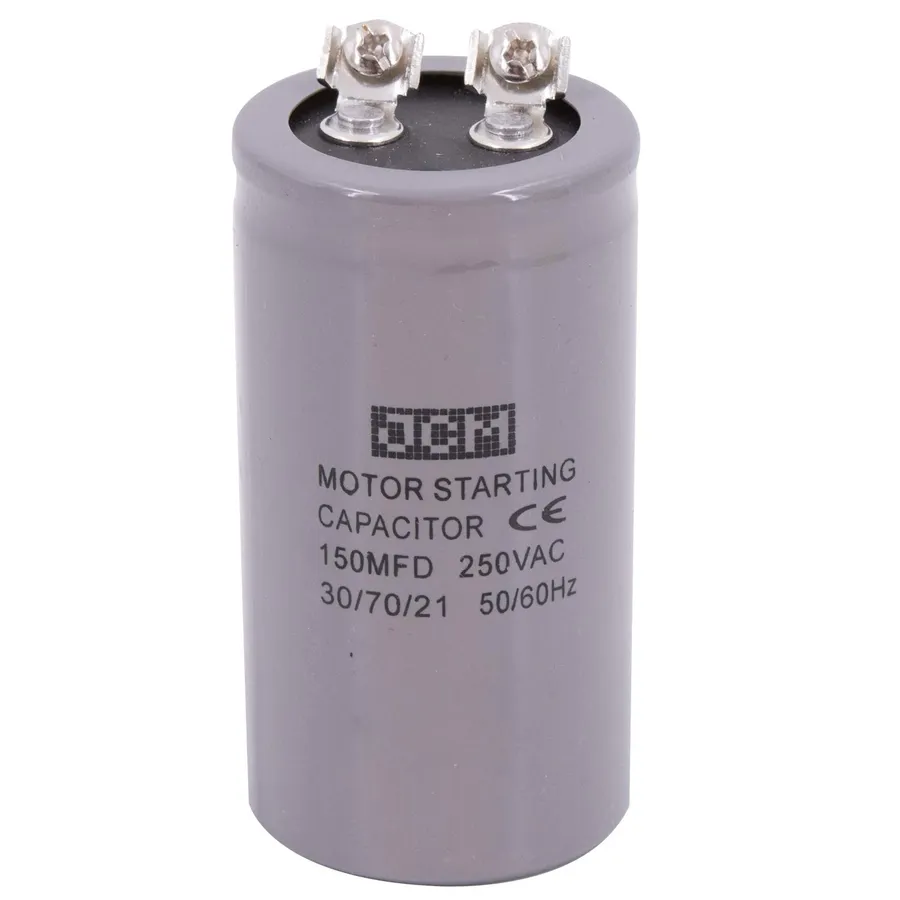
In the world of electric motors, a humble component plays a vital role in ensuring a smooth and powerful start—the motor start capacitor. Like a tiny power booster, this device provides that extra push needed to overcome inertia and get motors spinning. This article delves into the functions, selection, and troubleshooting of motor start capacitors, bridging the gap between technical understanding and practical application for anyone working with motors.
Understanding the Function of a Motor Start Capacitor
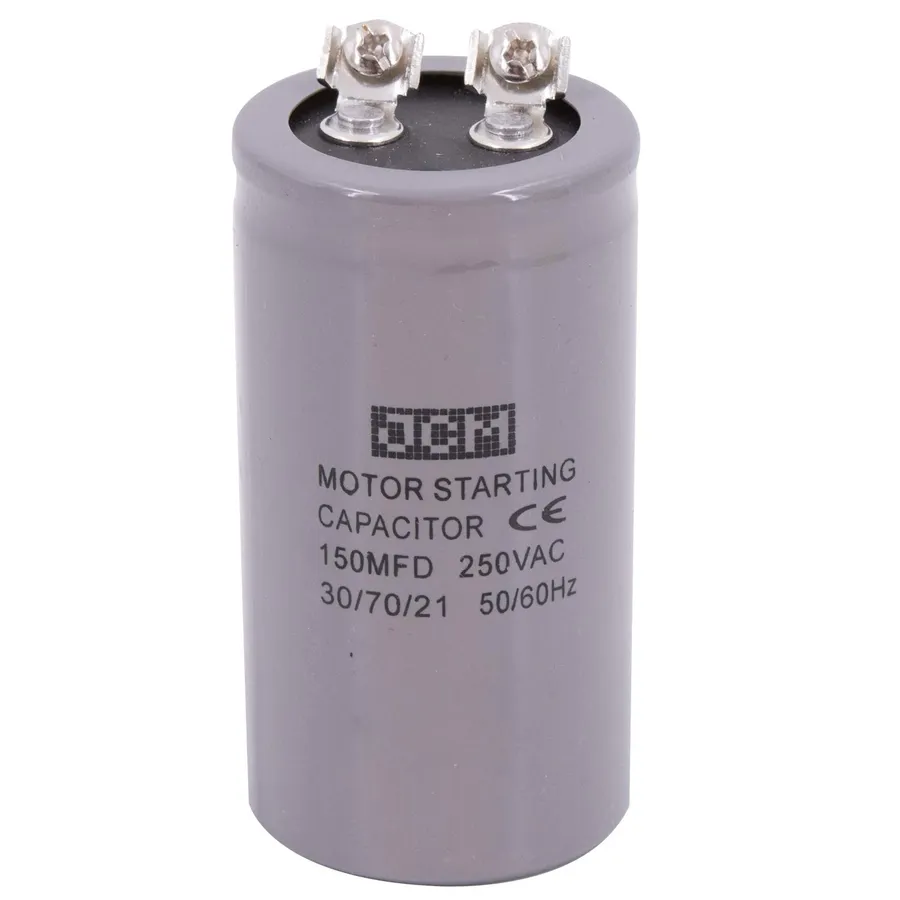
A motor start capacitor's primary function is to provide the necessary surge of electrical energy to initiate the rotation of a single-phase AC motor. This is achieved by briefly shifting the phase of the current in the motor's start winding, creating a rotating magnetic field that gives the rotor the initial 'push' needed to overcome inertia and begin turning. Without this additional torque, many single-phase motors, especially those under load, would be unable to start.
How Motor Start Capacitors Work: A Detailed Explanation
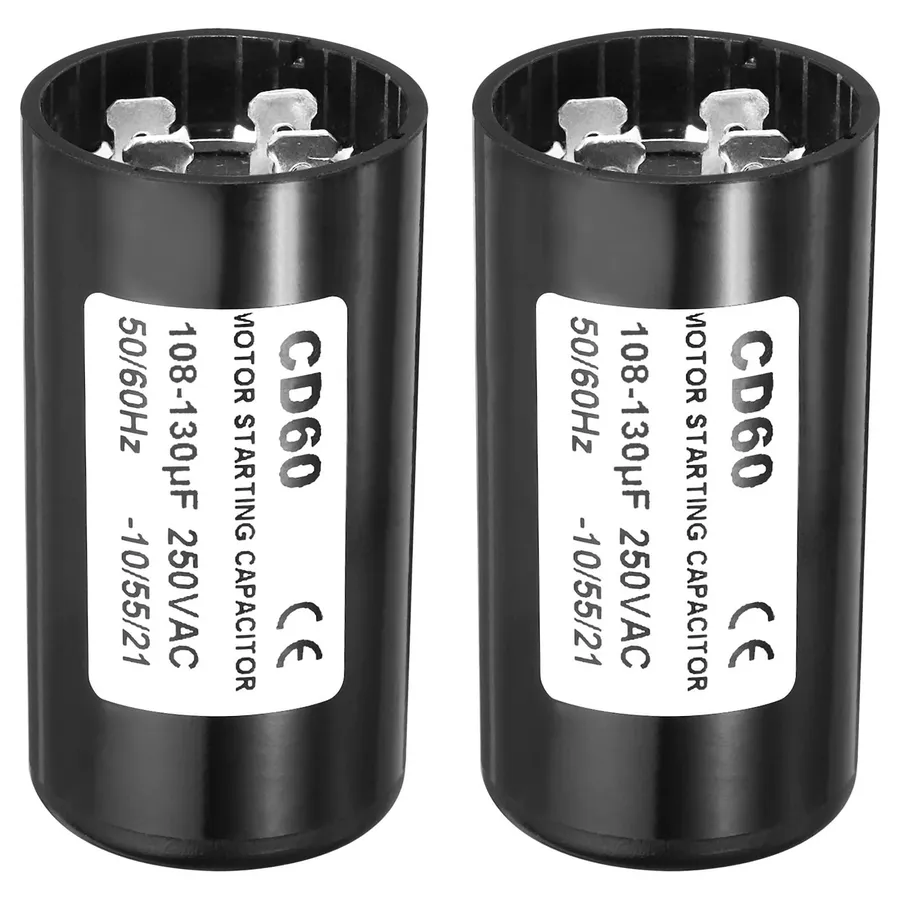
Motor start capacitors are crucial for initiating the rotation of single-phase AC induction motors. Their primary function is to provide a temporary boost of torque during the startup phase, enabling the motor to overcome inertia and begin rotating. This is achieved through the strategic manipulation of electrical phases within the motor's windings.
At the heart of its operation lies the principle of phase shifting. Single-phase AC power, by its nature, does not produce a rotating magnetic field necessary for self-starting motor operation. A start capacitor introduces a phase difference in the current flowing through the start winding relative to the current in the main winding. This is achieved by storing and releasing electrical energy, altering the current's phase by approximately 90 degrees. The result is the creation of a rotating magnetic field that initiates the motor's rotation.
Specifically, the start capacitor is connected in series with the auxiliary or start winding of the motor. When power is applied, the capacitor allows the current in the start winding to lead the current in the main winding by the phase angle difference. This is due to the capacitor's impedance, which creates a phase shift of approximately 90 degrees. The capacitor's ability to store charge and discharge alters the timing of the current. This temporary phase shift creates a rotating magnetic field that produces the necessary starting torque. Once the motor reaches a certain speed, a centrifugal switch or similar mechanism disconnects the start winding and capacitor from the circuit, leaving the motor to run using only the main winding. This entire process occurs quickly, typically within seconds.
Identifying a Failing Motor Start Capacitor: Key Symptoms
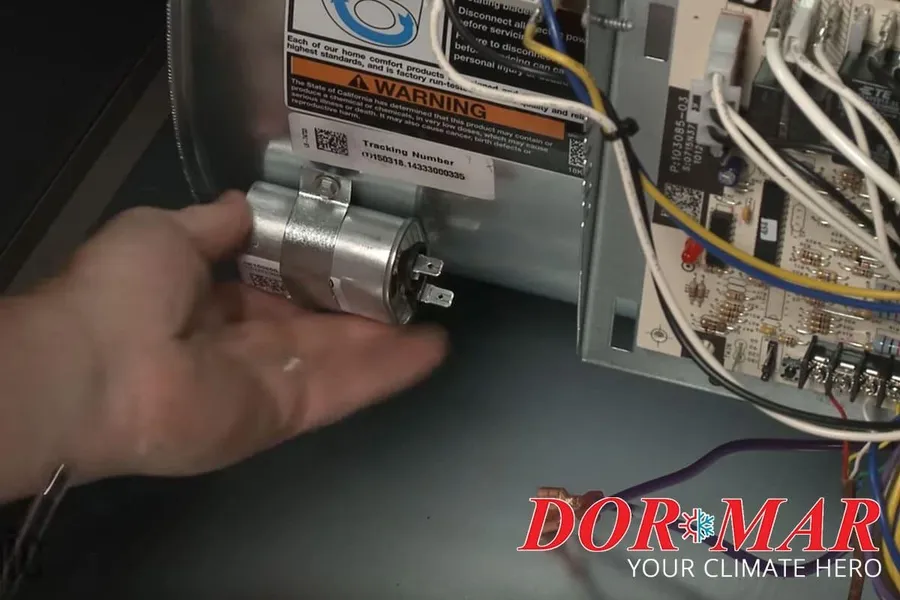
A failing motor start capacitor manifests through several distinct symptoms, primarily stemming from its inability to adequately provide the necessary torque for motor startup. These signs are critical to recognize promptly to prevent further motor damage and ensure efficient operation. Early detection allows for timely replacement of the capacitor, avoiding more costly repairs or complete motor failure.
- Slow Motor Starts
A key indicator of a failing start capacitor is a noticeable delay or sluggishness in the motor’s startup. The motor may take longer than usual to reach its operational speed, signaling that the capacitor is not delivering the required electrical boost. - Humming Noises
A persistent humming sound emanating from the motor, particularly during startup, often points to a capacitor that's struggling or unable to facilitate the necessary phase shift. This humming occurs as the motor attempts to start without sufficient torque. - Motor Fails to Start
In severe cases, a completely non-functional start capacitor will prevent the motor from starting at all. The motor might only hum or produce a clicking sound but will fail to rotate, indicating that the startup torque is absent. - Overheating of Motor
A failing start capacitor can cause the motor to overheat due to prolonged attempts to start. This excessive heat can lead to further damage to the motor’s components and potentially cause safety hazards. - Intermittent Operation
The motor may start and run sporadically or inconsistently, failing to start reliably each time it's turned on. This intermittent behavior is often a sign that the capacitor is failing, though it can still temporarily provide some function. - Visible Capacitor Damage
Physical damage to the capacitor, such as bulging, leaking, or cracking can indicate that it is no longer functioning correctly and is a reliable sign of component failure, signaling immediate replacement is needed.
Choosing the Correct Motor Start Capacitor: Specifications and Compatibility
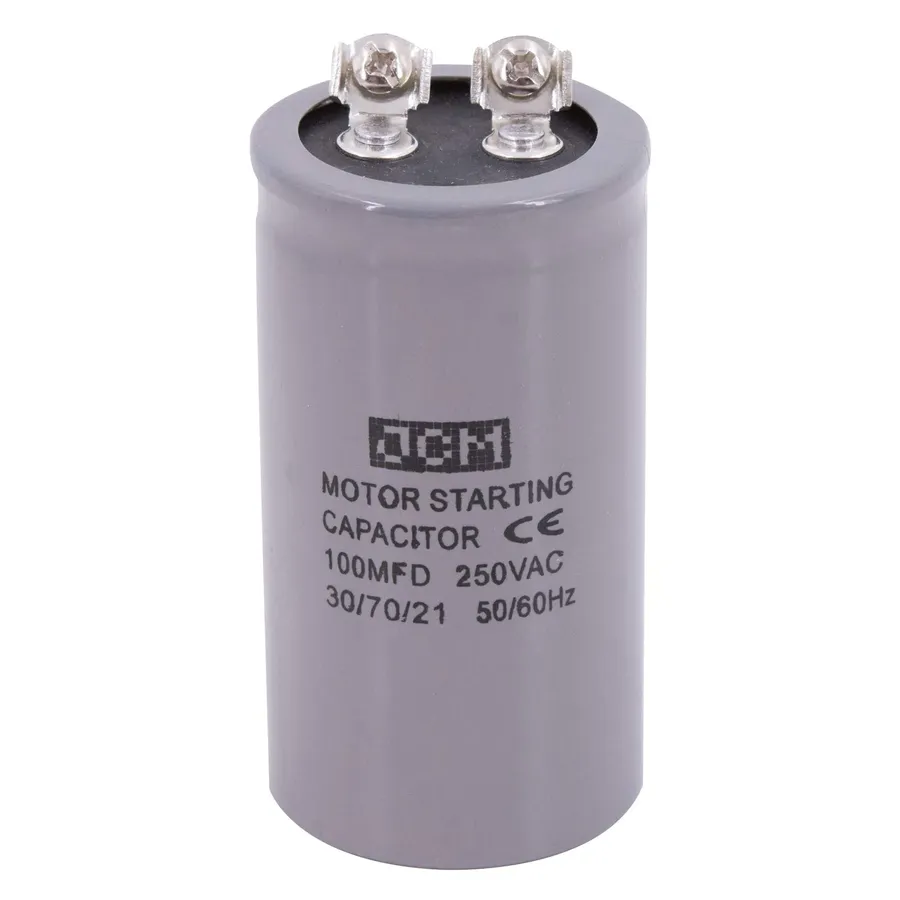
Selecting the correct motor start capacitor is crucial for ensuring proper motor function and longevity. The two primary specifications to consider are capacitance, measured in microfarads (µF), and voltage rating. These parameters must match or exceed those of the original capacitor to avoid damage and ensure reliable starting torque.
Parameter | Description | Importance |
---|---|---|
Capacitance (µF) | The amount of electrical charge the capacitor can store, measured in microfarads. | Directly affects the motor's starting torque. An incorrect value may cause the motor to fail to start, hum loudly, or overheat. |
Voltage Rating (V) | The maximum voltage the capacitor can withstand without damage. | The capacitor's voltage rating must match or exceed the motor's operating voltage. Using a lower-rated capacitor can cause failure, potentially leading to short circuits. |
Physical Size | The physical dimensions of the capacitor. | The replacement capacitor should physically fit within the designated mounting area of the motor. |
Operating Temperature | The safe operating temperature range of the capacitor. | Operating the capacitor above the rated operating temperature can shorten its life and potentially lead to failure. |
When replacing a start capacitor, always prioritize matching the original capacitor's specifications. In cases where an exact match is unavailable, choosing a replacement capacitor with a capacitance value within 10% of the original and an equal or higher voltage rating is generally acceptable. It is also crucial to verify the physical dimensions of the replacement capacitor to ensure it fits properly in the motor's housing.
Step-by-Step Guide to Motor Start Capacitor Replacement
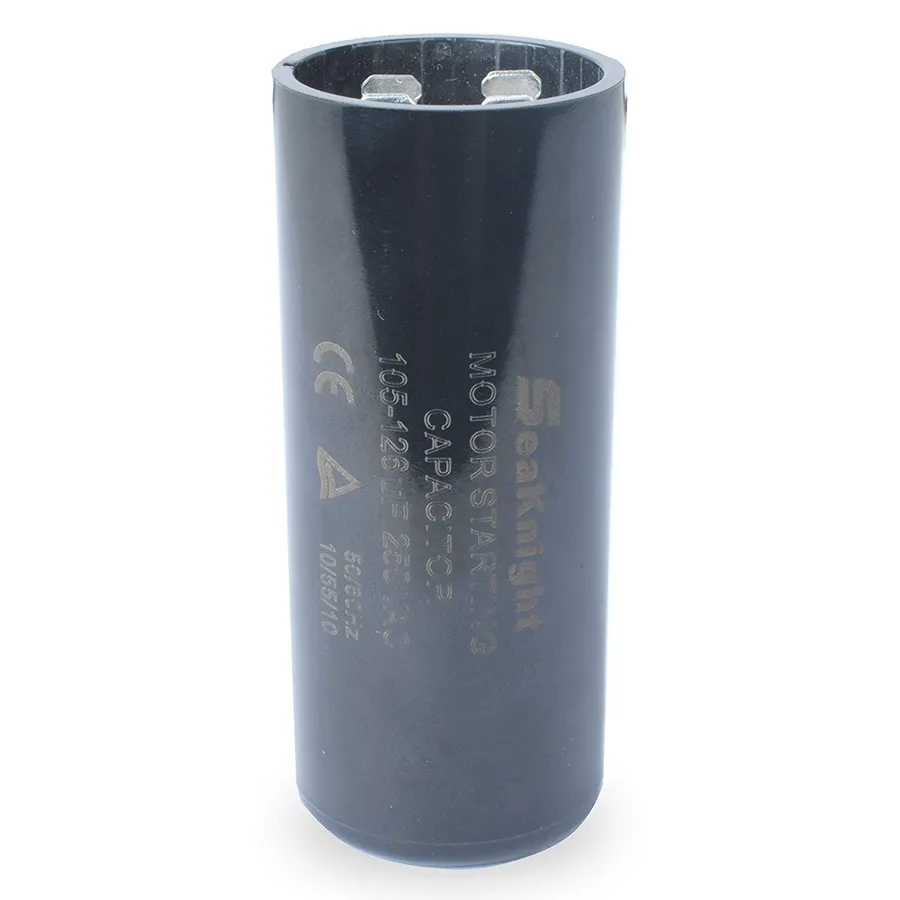
Replacing a motor start capacitor is a straightforward process that can often be completed at home with the right tools and safety precautions. This guide provides a detailed, step-by-step approach to ensure a safe and successful replacement.
Before starting, it is imperative to understand the role of the capacitor within the motor circuit. A start capacitor briefly boosts the motor's starting torque by creating a phase shift in the starting winding. Improper handling or incorrect installation could lead to motor damage or electrical shock.
- Safety First: Disconnect Power
Ensure the power supply to the motor is completely disconnected. This involves switching off the circuit breaker or unplugging the equipment from the mains. Verify that no power is flowing using a non-contact voltage tester or multimeter. - Discharge the Capacitor
Capacitors store electrical energy, even after the power is off. To safely discharge the capacitor, use a screwdriver with an insulated handle to carefully short the terminals. This process will dissipate any residual charge, reducing the risk of electric shock. It is recommended to use a discharge tool, which is specially made for the task, and to verify that the voltage across the capacitor terminals is 0V with a multimeter. - Locate the Capacitor
The start capacitor is usually housed in a plastic or metal casing near the motor. Identify the capacitor and note its location and the wiring connections to it. Take a photograph of the wiring if necessary to aid correct reassembly. - Remove the Old Capacitor
Carefully detach the wiring from the old capacitor terminals. Note the orientation and position of the wires. If they're labeled, record the labels for reference. If they are not, a photograph will be useful. Loosen any securing brackets, clips or screws holding the capacitor in place. Remove the old capacitor and note any mounting orientation. - Inspect the New Capacitor
Compare the new capacitor with the old one, ensuring that the ratings (capacitance in μF, and voltage rating in V) match. Check that the capacitor is not damaged and is safe for installation. - Install the New Capacitor
Place the new capacitor into the mounting location, following any orientation from the old capacitor. Connect the wires to the capacitor terminals according to your notes or photos, ensuring the connections are firm and secure. Double check the wiring to be sure it is as it was on the old capacitor. - Secure and Test
Secure the capacitor in place with any brackets or screws. Double-check all connections and wiring, ensuring everything is correctly installed. Reconnect the power supply to the motor and test the motor. The motor should now start smoothly, without any hesitation or humming noises.
If the motor still has issues starting or operating after the capacitor replacement, additional troubleshooting may be required. Verify the motor windings and other components for potential faults.
Motor Start Capacitor vs. Run Capacitor: Key Differences
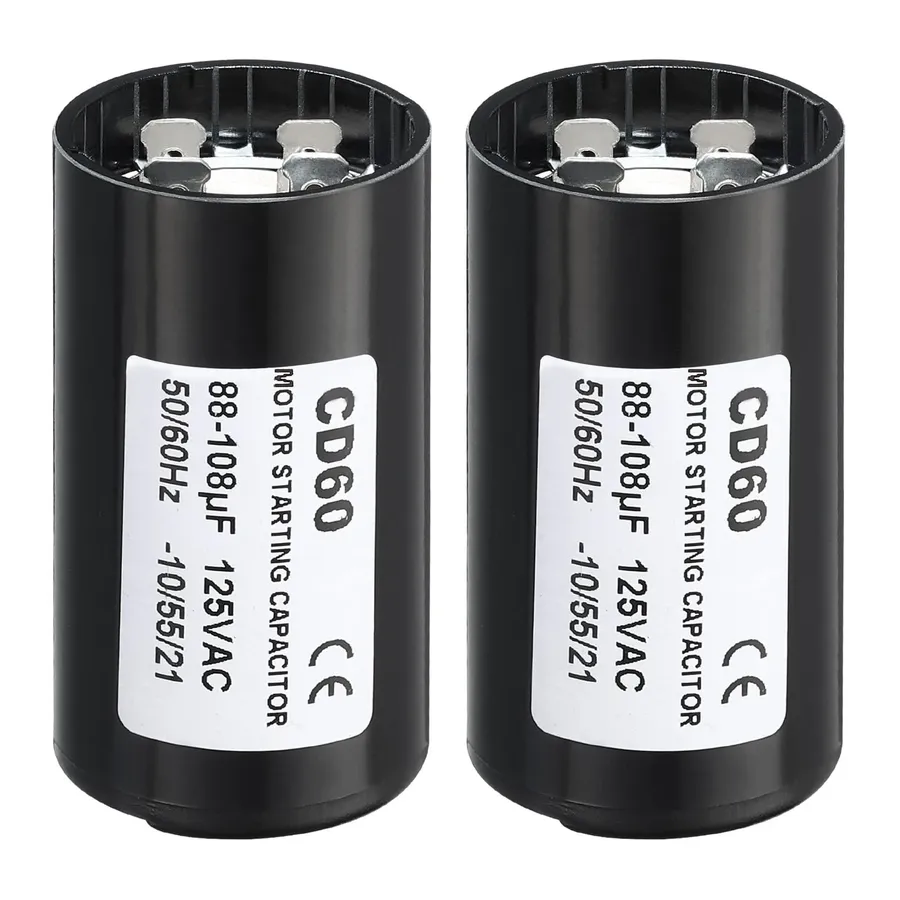
Motor start capacitors and run capacitors are both crucial components in single-phase AC motors, but they serve distinctly different purposes and operate under different conditions. The key difference lies in their function, duty cycle, and how they impact motor performance. Start capacitors provide a high burst of torque for starting, while run capacitors continuously aid in efficient motor operation.
Feature | Start Capacitor | Run Capacitor |
---|---|---|
Primary Function | Provides a high torque boost during motor startup. | Maintains motor torque and power factor during continuous operation. |
Duty Cycle | Active only during the initial start-up phase for a short duration. | Operates continuously while the motor is running. |
Construction | Typically made with non-polarized electrolytic capacitors designed for intermittent use. | Usually made with film capacitors, designed for continuous operation. |
Capacitance Value | Generally higher capacitance values (measured in microfarads, uF). | Typically lower capacitance values compared to start capacitors. |
Connection | Connected in series with the start winding and disconnected by a centrifugal switch once the motor reaches speed. | Permanently connected in series with the motor's auxiliary winding. |
Impact on Motor Performance | Provides the necessary starting torque to overcome inertia and start the motor quickly. | Optimizes motor efficiency, running torque, and power factor, reducing energy consumption and heat. |
Physical Size | Often larger in size for the same voltage rating due to higher capacitance. | Smaller in physical size compared to a start capacitor with the same voltage. |
Frequently Asked Questions About Motor Start Capacitors
This section addresses common queries regarding motor start capacitors, providing essential insights into their operation, maintenance, and potential issues. Understanding these aspects is crucial for ensuring the reliable performance of single-phase motors.
- What is the primary function of a motor start capacitor?
A motor start capacitor's primary function is to provide a temporary boost of electrical energy during the motor's startup phase. It introduces a phase shift in the current flowing through the start winding, generating the high starting torque needed to overcome initial inertia and load, facilitating rotation. This phase shift is essential only during startup, after which the capacitor is typically disconnected from the circuit. - What are the key indicators of a failing motor start capacitor?
Key symptoms of a failing start capacitor include the motor failing to start, slow or labored starts, a humming or buzzing sound during startup, or the motor only starting after multiple attempts. A visible bulge or leaking fluid from the capacitor also indicates a fault, indicating internal damage or component failure. - Can a motor operate without a start capacitor?
Typically, a single-phase motor that relies on a start capacitor will not start without it, or will struggle to start. The start capacitor is crucial to generate the necessary torque to begin rotation. If the start capacitor fails, the motor may not have sufficient initial turning force and might stall, or it will attempt to draw high amounts of current to get going. However, once started, some motors might continue running, albeit inefficiently, if the capacitor is not required for continuous operation. - Is it possible for a motor to start with a bad start capacitor?
While it's highly unlikely, a motor might briefly start with a failing start capacitor if the capacitor still retains some limited functionality, however it will exhibit the previously stated symptoms. This is extremely uncommon and not something to rely on, prolonged attempts to start the motor with a bad capacitor can cause damage to both the motor's windings and other components due to the high current draw involved. The motor will eventually not start at all. - What are the risks of using an incorrect size of motor start capacitor?
Using a start capacitor with an incorrect capacitance (measured in microfarads, µF) can cause several problems. An undersized capacitor may not provide enough starting torque, leading to the motor failing to start or stalling during operation. An oversized capacitor can cause excessive starting current, leading to overheating, winding damage, and premature failure of the motor. It can also reduce the life of the capacitor itself. Additionally, mismatched voltage ratings can result in capacitor failure due to overvoltage. - How long should a motor start capacitor typically last?
The lifespan of a motor start capacitor can vary widely based on factors like operating temperature, usage frequency, and the quality of the capacitor itself. A well-matched capacitor, operated under normal conditions, may last for several years. However, it's essential to periodically inspect capacitors for physical damage and symptoms of failure to preempt potential problems. In particularly demanding or high heat applications, the lifespan may be shorter, requiring more frequent replacements. - Can a start capacitor pose a fire risk?
Yes, a faulty or incorrectly rated start capacitor can pose a fire risk. Overheating, internal shorts, and ruptures can occur, potentially igniting surrounding materials and creating fire hazard. This is most likely to happen if the capacitor voltage rating is insufficient for the motor it’s used with, leading to a catastrophic failure. Regular checks and adherence to appropriate installation and specification guidelines are critical to mitigating this danger. Always ensure the replacement capacitor meets or exceeds the manufacturer's specifications.
Troubleshooting Common Issues with Motor Start Capacitors
Diagnosing problems with motor start capacitors typically involves recognizing specific symptoms that indicate a capacitor is failing or has failed. These issues can range from visible damage to subtle performance degradations, and it’s crucial to identify them correctly to ensure efficient motor operation and avoid further complications.
- Capacitor Bulging or Swelling
A physically deformed capacitor, often with a bulging or swollen case, indicates internal damage due to overpressure or overheating. This is a clear sign that the capacitor is no longer functioning correctly and should be replaced immediately. The bulging is caused by the breakdown of the dielectric material inside the capacitor, which produces gases. These gases increase the internal pressure, leading to the swelling. This condition often results from excessive current or prolonged use under elevated temperatures. - Electrical Shorts
An electrical short within a start capacitor can result in the motor failing to start, or tripping circuit breakers. This short often happens when the capacitor's internal insulation breaks down. It may also manifest as visible arcing or burn marks around the capacitor's terminals or casing. If a short occurs, the electrical pathway through the capacitor is compromised, impeding its ability to store and release charge effectively. It often results in overheating and potentially further damages the motor and connected electrical systems. - Motor Humming or Slow Starts
When the motor struggles to reach its operating speed and produces a humming sound, it often points to a failing start capacitor. The capacitor's inability to provide the needed torque during startup is the reason for these symptoms. The humming indicates that the motor is getting power, but cannot overcome the load and startup friction. When the capacitor degrades, its capacitance decreases, diminishing its ability to provide the necessary starting boost. The symptoms can also be a result of a wrong size capacitor being used. It is essential to match the motor start capacitor's capacitance, specified in microfarads (µF) and voltage ratings to that of the motor. - Motor Fails to Start
A completely failed capacitor will often prevent the motor from starting at all. This is a straightforward indication of a severely damaged capacitor or a related issue in the start circuit. The absence of the needed phase shift and current boost prevents the motor from initiating the rotation. It is a clear indicator of a failed or very weak capacitor and warrants immediate investigation and potential replacement. - Capacitor Leaking
The leakage of dielectric fluid from a capacitor is a sign of severe internal damage or a breach in its casing. It's imperative to handle leaky capacitors with caution, as the fluids might be hazardous. This can arise from material degradation of the internal components, external mechanical damages or other environmental factors. A leaking capacitor is always defective and should be replaced. - When to Consider a Full Motor Inspection
When a capacitor failure is persistent or accompanied by other motor performance problems, it may be essential to conduct a full motor inspection. This is to ensure that the underlying issues are identified and are not being caused by other motor components. A comprehensive motor inspection is beneficial to evaluate the overall condition of the motor and may prevent future malfunctions. Often an early full motor inspection can identify multiple issues and prevent much larger and more expensive repairs later on.
Extending the Lifespan of Your Motor Start Capacitor
The longevity of a motor start capacitor is influenced by several factors, primarily heat, electrical stress, and component quality. Implementing preventative measures can significantly prolong its service life and prevent premature failure, thus ensuring efficient motor operation and reducing maintenance costs. By addressing these key factors, one can reduce the risk of failure and maintain system performance.
- Temperature Management
Excessive heat is a primary cause of capacitor degradation. Ensure adequate ventilation around the motor to prevent overheating. Consider using heat shields in particularly hot environments, and always verify that the capacitor's operating temperature is within its specified range. - Proper Electrical Connections
Loose or improperly made connections lead to electrical arcing and heat generation, causing premature capacitor failure. Inspect wiring regularly for signs of damage and ensure all connections are secure. Use appropriate torque settings for terminal screws, as specified by the manufacturer. - Quality Components
When replacing capacitors, opt for reputable brands that adhere to industry standards. These typically have tighter tolerances and better build quality. A higher quality component will generally be more robust and reliable, providing a longer operational lifespan. Avoid purchasing capacitors from unknown or unverified sources which might not meet necessary performance and safety standards. - Avoid Overvoltage
Ensure that the power supply to the motor adheres to the specifications of the capacitor. Overvoltage can cause dielectric breakdown and lead to premature failure. Use surge protectors where necessary, particularly in areas prone to voltage spikes. Regularly check voltage levels at the motor to ensure they are within recommended parameters. - Regular Inspection
Conduct periodic visual inspections of the start capacitor. Look for signs of bulging, cracking, or leaks, which may indicate imminent failure. It's also essential to observe the motor's behavior and address issues such as abnormal noise or slow starting, which could be early signs of capacitor wear.
The motor start capacitor is a small but mighty component that plays an indispensable role in the smooth operation of many electric motors. Understanding its function, knowing how to diagnose issues, and making informed replacement choices are essential to maintaining efficient motor performance. By following the guidelines provided, you're equipped to ensure your motors start reliably, keeping your world spinning efficiently. Always prioritize safety and proper technical handling of electrical components for optimal results.
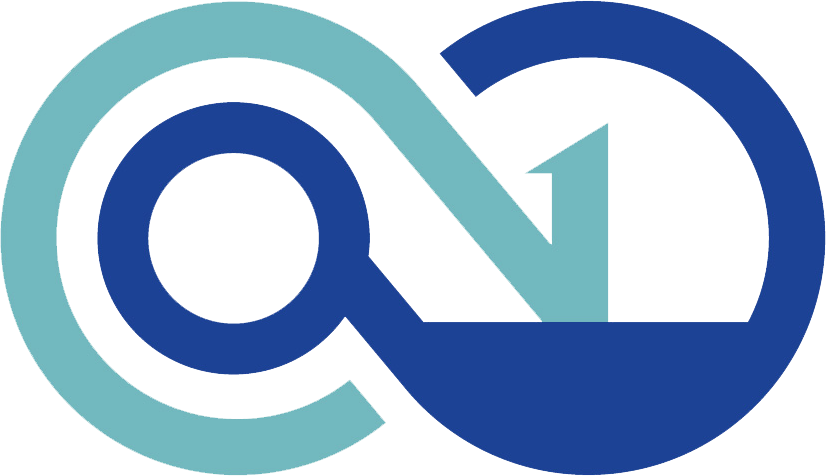