Understanding Ceramic Resonators: Applications, Principles, and Comparisons
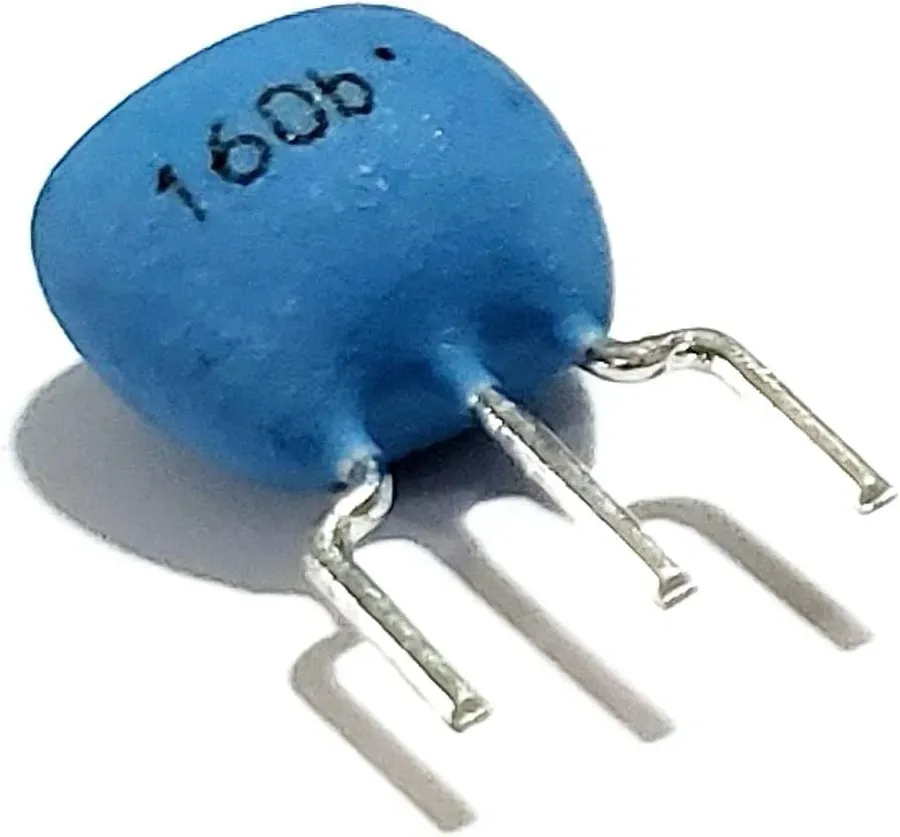
Just as the rhythmic beat of a drum guides a musical performance, electronic devices require precise timing signals to function. The ceramic resonator, a seemingly simple component crafted from piezoelectric ceramics, plays a vital role in generating these signals. Like a microscopic metronome, the ceramic resonator sets the pace for countless electronic systems, from the humble microcontroller to sophisticated communication circuits. This article demystifies the workings of ceramic resonators, explores their diverse applications, and compares them to other timing devices, unlocking their potential for a world increasingly reliant on precise timing.
What is a Ceramic Resonator?
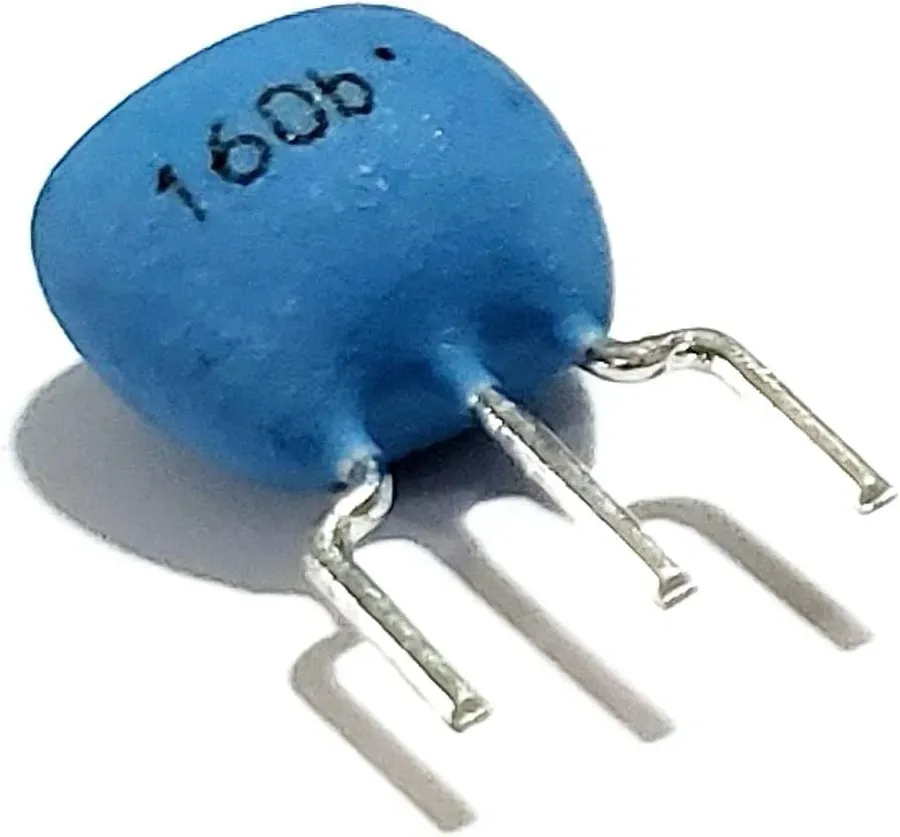
A ceramic resonator is a compact, passive electronic component crafted from piezoelectric ceramic material, engineered to oscillate at a specific frequency when subjected to an electrical signal. This precisely controlled vibration serves as a stable timing reference for a variety of electronic circuits, particularly in applications requiring a reliable clock signal but where the extreme accuracy of a crystal oscillator is not essential.
- Key Characteristics
Ceramic resonators are known for their cost-effectiveness, relatively small size, and ease of use in circuit design. They are a reliable alternative to quartz crystals when less stringent timing accuracy is sufficient. - Piezoelectric Principle
Their operation is based on the piezoelectric effect, wherein the ceramic material vibrates mechanically when an electric field is applied. This mechanical oscillation, at the component’s resonant frequency, generates a stable electrical signal. - Typical Applications
These components are frequently utilized in microcontroller circuits, remote controls, and other devices where precise timing is necessary for functional operation, but high precision is not critical.
How Ceramic Resonators Work: The Piezoelectric Effect
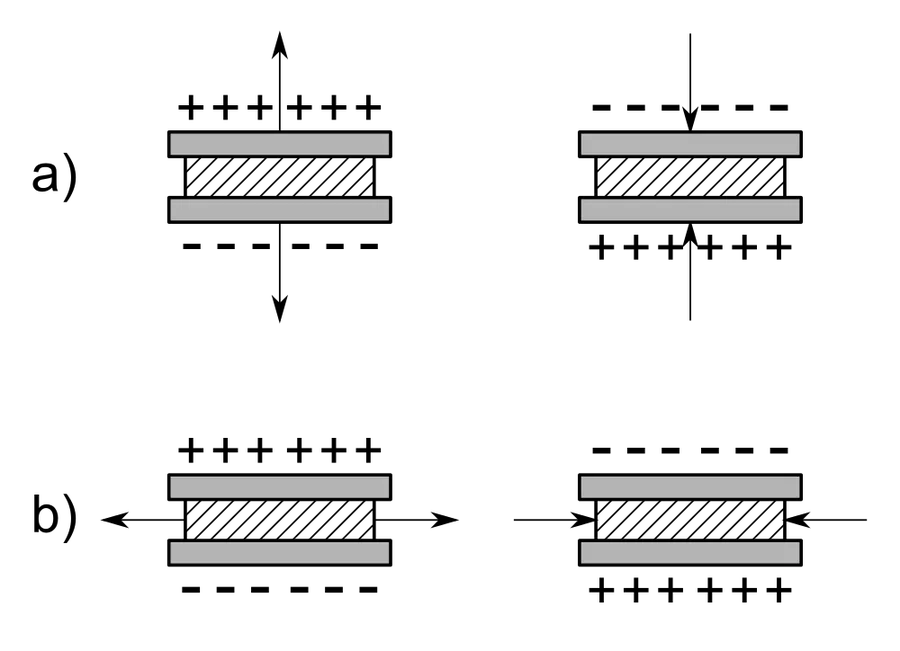
Ceramic resonators operate based on the piezoelectric effect, a phenomenon where mechanical stress applied to certain materials generates an electrical charge, and conversely, applying an electrical field induces mechanical deformation. In a ceramic resonator, this effect is harnessed using a specifically formulated piezoelectric ceramic material, typically a lead zirconate titanate (PZT) ceramic or similar compound.
When an alternating electrical signal is applied to the ceramic element, the material undergoes rapid, minute deformations corresponding to the frequency of the electrical signal. Conversely, when the ceramic is subjected to mechanical stress, such as through the vibrations, it will produce an electrical charge. The ceramic resonator will resonate most strongly at its specific resonant frequency, acting similarly to a tuned circuit.
The resonant frequency is primarily determined by the physical dimensions, material composition, and geometry of the resonator. This mechanical vibration is transformed into a stable electrical oscillation when properly integrated within a circuit, serving as a timing reference. The interlinked nature of mechanical stress and electrical charge within the piezoelectric material is the fundamental operating principle of a ceramic resonator, allowing it to convert electrical energy into mechanical energy, and back again, with a high degree of precision at its resonant frequency.
Ceramic Resonator Types: 2-Pin vs 3-Pin
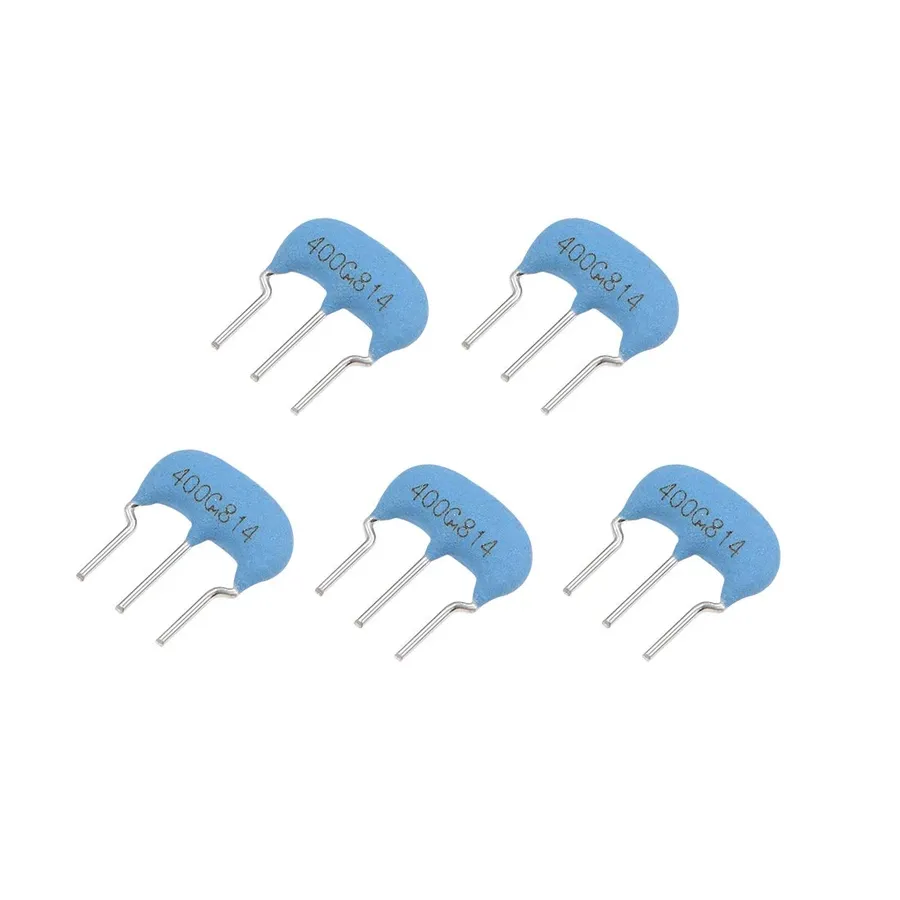
Ceramic resonators are available in two primary configurations: 2-pin and 3-pin. These configurations differ in their internal structure and external connection points, directly impacting their application and required circuit design. The key distinction lies in the presence of integrated capacitors in the 3-pin variant, which are absent in the 2-pin version. Understanding these differences is crucial for selecting the appropriate resonator for a given application.
Feature | 2-Pin Ceramic Resonator | 3-Pin Ceramic Resonator |
---|---|---|
Number of Pins | 2 | 3 |
Integrated Capacitors | No | Yes (typically two, connected between each pin and the central ground pin) |
Circuit Design | Requires external load capacitors | Load capacitors are integrated, simplifying circuit design |
Application | Suitable for designs where external tuning and load capacitors are necessary | Ideal for applications needing a simple oscillator circuit with a low component count |
Stability | Slightly more susceptible to noise due to the lack of integrated capacitors | More stable in certain circuit configurations due to the presence of integrated capacitors |
In essence, the 2-pin configuration functions as a simple piezoelectric element, requiring external capacitors to establish the correct resonant frequency and ensure stable oscillation. Conversely, the 3-pin variant, with its integrated capacitors, streamlines the circuit design process, enabling easier integration into systems where space and component count are critical. The integrated capacitors in 3-pin resonators simplify the oscillator circuit, often allowing a direct connection to a microcontroller or microprocessor clock input. It's important to remember that these internal capacitors are designed to operate within a certain range, and may be suitable for some applications but not others, when selecting ceramic resonators.
Key Applications of Ceramic Resonators
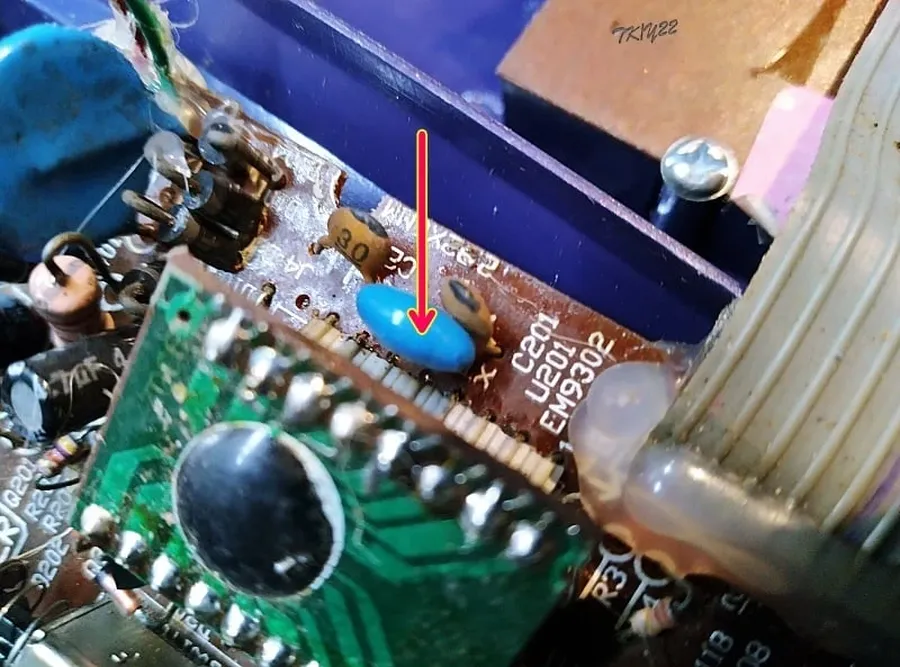
Ceramic resonators are indispensable components in a wide array of electronic devices, providing a stable frequency reference essential for timing and synchronization. Their compact size, cost-effectiveness, and relatively stable performance make them suitable for diverse applications, especially where high precision quartz crystals may be overkill or cost-prohibitive.
- Microcontrollers and Microprocessors
Ceramic resonators are frequently employed in microcontroller and microprocessor circuits for generating clock signals. These devices utilize the resonator's precise oscillations to regulate the timing of internal operations, including instruction execution and data processing. For example, 4-bit, 8-bit, and 16-bit processors commonly employ ceramic resonators as their timing base due to their balance between size, cost, and adequate stability. The resonant frequency determines the processor's operational speed. - Consumer Electronics
Many everyday consumer electronics devices use ceramic resonators. Examples include remote controls, toys, and various low-power devices, where the critical need for cost-effectiveness and compact size outweighs the requirement for extremely high accuracy and stability. - Automotive Electronics
Within automotive applications, ceramic resonators are found in various control systems, such as engine control units (ECUs), and anti-lock braking systems (ABS). These applications benefit from the resonator's ability to provide reliable timing in a variety of operating temperatures, though some more demanding automotive applications may opt for the higher stability of crystal oscillators. - Communication Devices
Ceramic resonators find use in some communication systems such as radio frequency (RF) modules, where they help generate clock signals for various communication protocols. While they are not always the preferred choice for very high-frequency or high-precision applications, they offer a practical solution for lower-frequency communications where cost and size are critical. - Industrial Control Systems
In industrial environments, ceramic resonators are utilized in control systems and embedded devices. Their cost-effectiveness makes them attractive for large-scale deployments, providing a reliable timing base for various processes.
Ceramic Resonators vs. Quartz Crystals: A Detailed Comparison
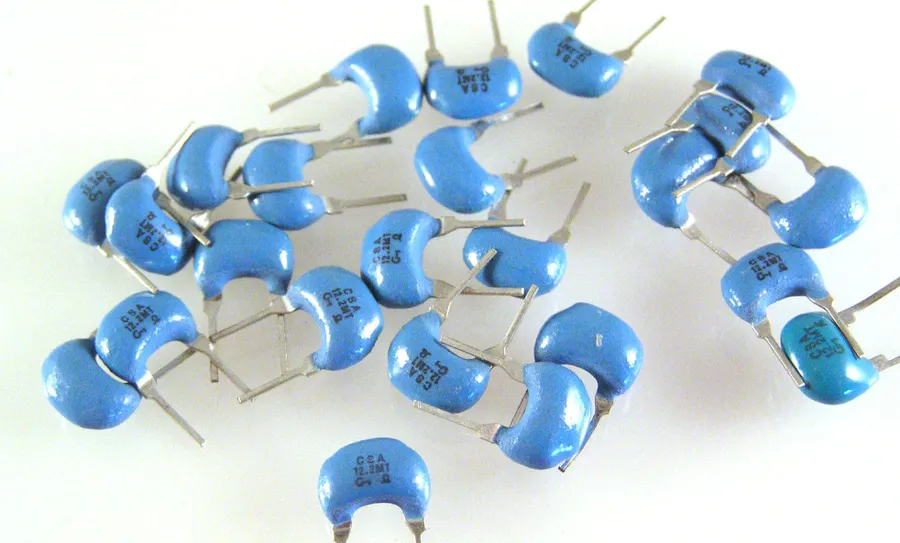
Ceramic resonators and quartz crystals are both piezoelectric devices used for generating stable frequencies in electronic circuits, but they differ significantly in their performance characteristics and applications. Understanding these differences is crucial for selecting the appropriate component for a given design. Quartz crystals, known for their high precision and stability, are often the choice for applications demanding accurate timing. Conversely, ceramic resonators, while less precise, offer a more cost-effective and compact solution for less stringent applications.
Feature | Ceramic Resonator | Quartz Crystal |
---|---|---|
Accuracy | Moderate (0.1% to 0.5% typical) | High (0.001% to 0.01% typical) |
Stability | Moderate, sensitive to temperature and aging | Very high, less sensitive to temperature and aging |
Cost | Lower | Higher |
Size | Compact | Larger, can be miniaturized with more cost |
Frequency Range | Typically up to 20 MHz | Wide range, from kHz to hundreds of MHz |
Startup Time | Generally faster | Can be slower, depending on crystal and circuit design |
Load Capacitance | Typically higher | Typically lower |
Applications | Microcontrollers, consumer electronics, low precision timing circuits | High-precision timers, communication systems, high-accuracy microprocessors |
Accuracy and Stability of Ceramic Resonators
The accuracy and stability of ceramic resonators are critical for their reliable performance in electronic circuits. These characteristics define how closely a resonator's oscillation frequency matches its specified value and how consistently it maintains this frequency over time and under varying conditions. Several factors can influence these parameters, necessitating careful consideration in design and application.
- Temperature Variation
Temperature fluctuations significantly impact the resonant frequency of ceramic resonators. Typically, as temperature increases, the resonant frequency decreases. This effect, known as the temperature coefficient, is inherent to the piezoelectric material used. Manufacturers specify this coefficient, often in parts per million per degree Celsius (ppm/°C), allowing designers to predict and compensate for temperature-induced frequency shifts. For applications requiring high precision, temperature-compensated resonators or careful thermal management are essential. - Aging
Over time, the resonant frequency of a ceramic resonator can drift. This phenomenon, known as aging, is attributed to gradual changes within the piezoelectric material’s structure. The rate of aging is typically highest during the initial operational period, gradually slowing down as the resonator stabilizes. Aging is usually specified by manufacturers in terms of frequency shift over a certain time period. For critical applications, aging effects may require periodic recalibration or the use of resonators specifically rated for long-term stability. - Manufacturing Tolerances
Variations in the manufacturing process result in slight differences in the physical dimensions and material properties of individual resonators. These inconsistencies lead to variations in the initial resonant frequency across a batch of resonators, impacting accuracy. Designers often consider this inherent tolerance when selecting a resonator for a specific application, ensuring that the device operates within acceptable frequency limits. Furthermore, for more precise requirements, using matched or precision-trimmed resonators may be considered. - Load Capacitance
The external circuitry connected to a ceramic resonator affects its operating frequency. The load capacitance, including the capacitance of the circuit traces, load capacitors, and input capacitance of the microcontroller, forms part of the resonant circuit and directly influences the oscillation frequency. The datasheet specifies the optimal load capacitance for a given resonator, and designers must ensure that the actual load capacitance in their circuit matches this to achieve the desired frequency. Any mismatch can result in frequency deviations and instability. - Mechanical Stress
External mechanical stresses applied to the ceramic resonator can also alter its resonant frequency. Physical vibrations or pressure on the device may induce changes in its crystal structure or material properties, causing slight but noticeable frequency shifts. This is especially relevant in applications that involve shock or vibration, for which it is important to minimize such stresses.
To mitigate the adverse effects of these factors, several methods are employed. Temperature compensation circuits can counteract temperature variations, while high-stability resonators with lower aging rates are available for long-term applications. Careful circuit design and component selection are crucial in reducing the effects of load capacitance, and protective packaging minimizes the impact of mechanical stress. Understanding and addressing these factors is paramount for achieving reliable and accurate performance from ceramic resonators in diverse electronic applications.
Selecting the Right Ceramic Resonator: Key Considerations
Selecting the appropriate ceramic resonator for a specific application requires careful consideration of several key specifications. These parameters directly influence the performance and stability of the oscillator circuit. Key considerations include frequency tolerance, operating temperature range, load capacitance, and aging effects. Ignoring these specifications can lead to unpredictable circuit behavior, reduced performance or even malfunction.
Parameter | Description | Importance |
---|---|---|
Frequency Tolerance | The allowable deviation of the actual resonant frequency from the specified nominal frequency, usually expressed in percentage or ppm. | Critical for accurate timing and frequency generation. Directly impacts the stability of the oscillator and the precision of the timing reference. |
Operating Temperature Range | The range of temperatures over which the resonator will operate within its specified performance limits. | Essential for reliable operation across different environmental conditions. Performance characteristics such as resonant frequency and stability may vary with temperature. |
Load Capacitance | The external capacitance required for the resonator to operate at its specified resonant frequency. | Determines the frequency of oscillation. Matching the load capacitance to the datasheet specification is critical for achieving desired performance. |
Aging | The gradual change in the resonant frequency of the ceramic resonator over time. | Affects long-term stability. Needs to be factored in for applications where long-term accuracy is required |
Resonance Mode | Ceramic resonators can operate in series or parallel resonant modes. Choosing the appropriate mode based on the circuit requirements is crucial. | Incorrect mode selection can lead to unstable operation or failure to oscillate. |
Package Type and Size | Physical dimensions and form factor of the resonator for compatibility with PCB layout. | Must align with physical board space and mounting methods. A compact package helps to reduce the overall size of the device |
Practical Tips for Using Ceramic Resonators in Circuits
Effectively integrating ceramic resonators into electronic circuits requires careful attention to design and layout to ensure stable and reliable oscillation. This section provides practical guidance on proper trace routing, component placement, and noise mitigation strategies.
- Minimize Trace Lengths
Keep the PCB traces connecting the resonator to the microcontroller or oscillator circuit as short as possible. Shorter traces reduce parasitic inductance and capacitance, minimizing signal degradation and ensuring better frequency stability. - Strategic Component Placement
Place the ceramic resonator close to the microcontroller or oscillator circuit pins to further reduce trace lengths. Position related components (e.g., load capacitors) close to the resonator, to prevent introducing additional parasitic effects. - Dedicated Ground Plane
Implement a continuous ground plane beneath the resonator and its associated circuitry. A solid ground plane provides a low-impedance path for return currents, which can reduce noise and improve signal integrity. - Use Appropriate Load Capacitors
Ceramic resonators require appropriate load capacitors, often specified by the resonator manufacturer, to achieve the stated frequency. Deviations in capacitor values can shift the oscillation frequency and cause operational issues. Always use capacitors with low temperature coefficient to ensure frequency stability across operating temperatures. - Shielding Sensitive Components
If the circuit operates in a noisy environment, consider shielding the resonator and its supporting components with a metallic shield. Ground the shielding layer to the ground plane which will reduce electromagnetic interference (EMI). - Avoid Sharp Bends in Traces
Use smooth and wide traces for the resonator connections. Avoid sharp 90-degree bends in the traces as these create impedance discontinuities that can cause signal reflections. Use 45-degree or rounded bends instead. - Isolate Resonator from Noise
Keep the resonator circuit isolated from high-speed switching circuits, high current paths, and other potential sources of noise. Avoid routing other traces above the ceramic resonator to minimize cross talk.
Ceramic Resonators and Their Role in Filter Design
Ceramic resonators, leveraging their resonant frequency characteristics, are integral components in filter design, particularly in applications requiring band-pass filtering. Their ability to selectively pass or reject specific frequency ranges makes them suitable for signal processing and conditioning tasks. By carefully selecting resonators with the appropriate resonant frequency and impedance, engineers can create effective filters for various electronic systems.
- How Ceramic Resonators Function in Filters?
Ceramic resonators, when incorporated into a filter circuit, act as a selective frequency gate. At their resonant frequency, they exhibit a low impedance, allowing signals at that frequency to pass through. Frequencies away from the resonant point experience high impedance, and are thus attenuated. This property is fundamental to the construction of band-pass filters. - Why are ceramic resonators often used in band-pass filters?
Their ability to resonate at a specific frequency, coupled with their compact size and cost-effectiveness, make ceramic resonators ideal for creating band-pass filters. These filters are designed to allow a specific range of frequencies to pass while attenuating frequencies outside of that range. This is crucial in signal processing where selective frequency passing is necessary. - What is the main principle behind utilizing a ceramic resonator in filters?
The core concept is to capitalize on the resonance. At their resonant frequency, ceramic resonators exhibit low impedance, facilitating signal passage, and high impedance otherwise, leading to signal attenuation. This selective behavior is what allows a signal to pass through or be rejected. - In what specific filter applications are ceramic resonators used?
Ceramic resonators are primarily employed in band-pass filters, where they selectively permit a defined band of frequencies. These types of filters are common in applications such as radio frequency (RF) circuits, intermediate frequency (IF) stages, and clock recovery circuits. - How are ceramic resonators different from other components used in filters?
Unlike inductors or capacitors, ceramic resonators act as a resonant component, combining inductive and capacitive properties at their resonant frequency. This allows for sharper frequency responses in filter designs compared to simple LC circuits. Ceramic resonators are also smaller and have more cost advantages.
The ceramic resonator, a fundamental component in modern electronics, provides a cost-effective and reliable means of generating precise timing signals. From powering the clocks in our microcontrollers to serving as the heart of complex communication systems, ceramic resonators are indispensable. Although not as accurate as quartz crystals, their ease of use, affordability, and stability make them an ideal choice for a vast range of applications. Understanding their principles, advantages, and limitations allows engineers to harness their potential for innovative and reliable electronic designs. As technology advances, ceramic resonators will continue to play a vital role, resonating at the core of our increasingly connected world, demonstrating the crucial role of ceramic technology in shaping our daily lives.
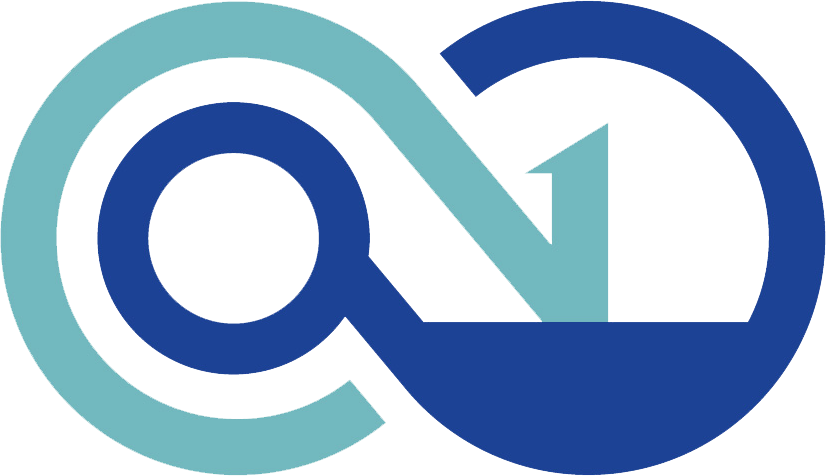