Understanding Thermal Resistors: Types, Uses & How They Work
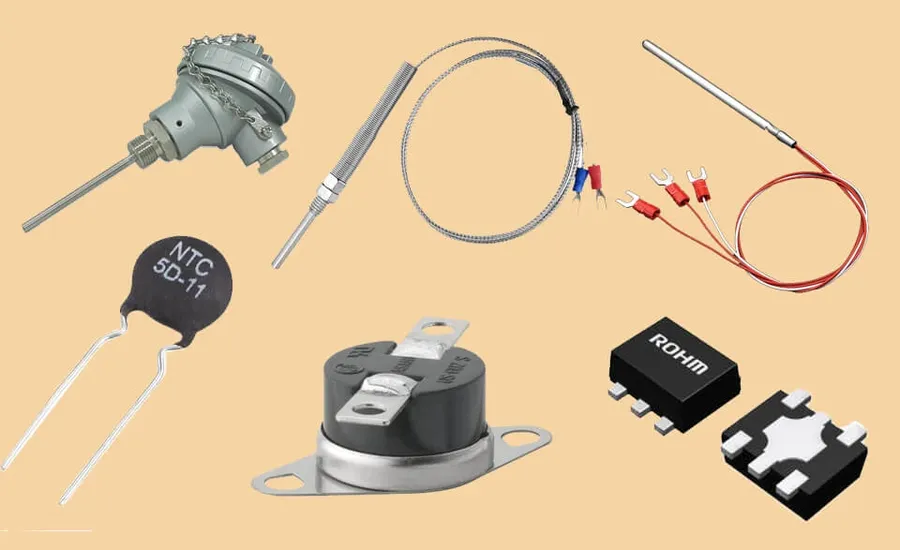
In our technologically advanced world, temperature control and measurement are paramount. Just as a simple fever can signal underlying health issues in humans, variations in temperature can impact the performance and safety of electronics. That's where thermal resistors, also known as thermistors, come into play. These unassuming components change their resistance with temperature, making them invaluable for sensing and controlling thermal conditions in a wide range of applications. From protecting delicate circuits to ensuring the optimal operating temperatures of industrial machinery, understanding thermal resistors is essential in today’s engineering landscape. This article delves deep into the world of thermal resistors, exploring their types, uses, and practical applications.
What is a Thermal Resistor (Thermistor)?
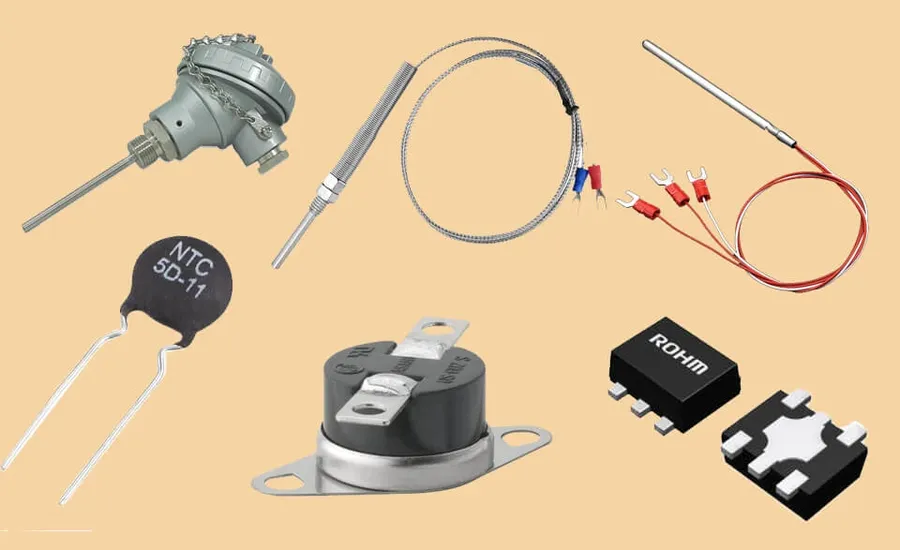
A thermal resistor, commonly known as a thermistor, is a type of resistor whose resistance varies significantly with changes in temperature. This characteristic makes it a vital component in numerous applications requiring precise temperature sensing, control, and circuit protection. Unlike standard resistors which maintain a relatively stable resistance, thermistors are designed to exhibit a predictable and pronounced change in resistance in response to temperature fluctuations.
The core functionality of a thermistor is rooted in the material science and construction of the component. The materials are selected to exhibit either a negative temperature coefficient (NTC), where resistance decreases as temperature increases, or a positive temperature coefficient (PTC), where resistance increases with temperature. This inherent property allows for the utilization of thermistors in diverse roles.
Thermistors, due to their sensitivity to temperature, are indispensable for numerous applications. Their use in temperature sensing leverages their predictable resistance change, while their role in circuit protection depends on their ability to drastically change resistance at specific temperatures. This makes them ideal for preventing damage caused by overcurrent or overheating in electronic devices.
NTC Thermistors: Negative Temperature Coefficient
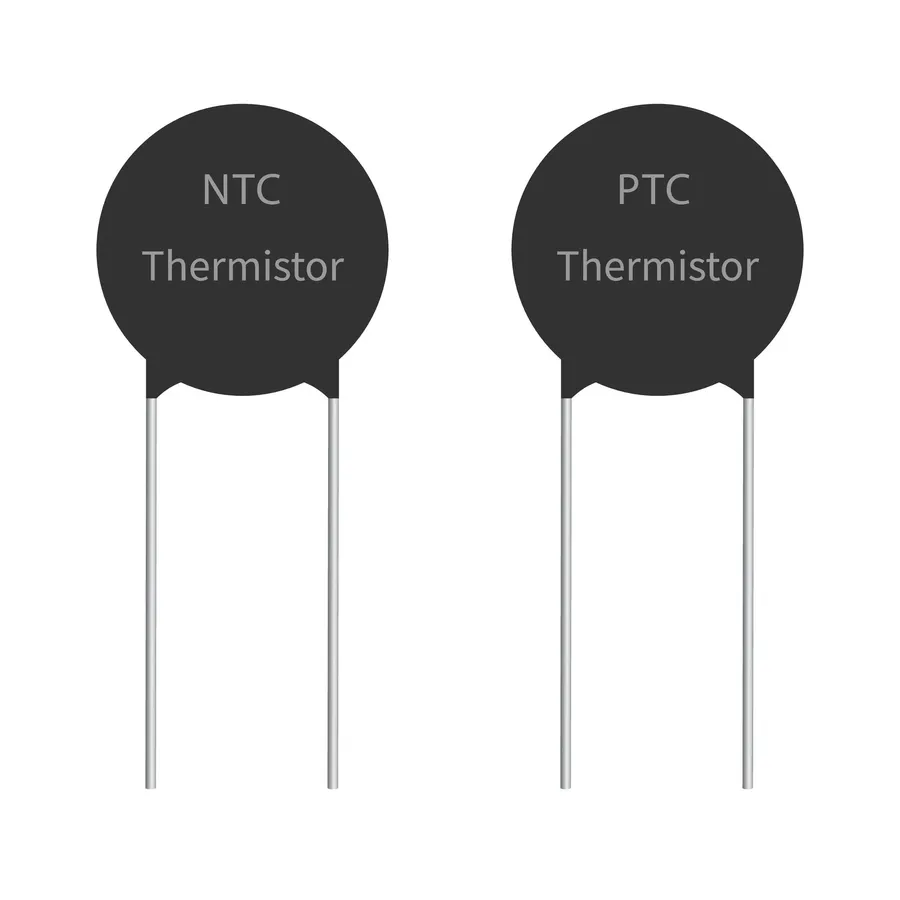
NTC (Negative Temperature Coefficient) thermistors are a class of thermal resistors characterized by a decrease in electrical resistance as their temperature increases. This inverse relationship between resistance and temperature makes NTC thermistors invaluable for a variety of applications, particularly in temperature sensing, inrush current limiting, and temperature compensation circuits.
The relationship between resistance and temperature in NTC thermistors is not linear; instead, it's typically described by a complex exponential equation. The Steinhart-Hart equation is often used to calculate temperature from the measured resistance, offering a higher accuracy than simple approximations. Due to their sensitivity to temperature changes, NTC thermistors are highly effective for precise temperature measurements.
Feature | Description |
---|---|
Temperature Coefficient | Negative: Resistance decreases as temperature increases. |
Typical Applications | Temperature measurement, inrush current limiting, and temperature compensation. |
Resistance-Temperature Relationship | Non-linear, often described by the Steinhart-Hart equation. |
Sensitivity | High sensitivity to temperature changes. |
NTC thermistors are integral to temperature control systems because they can provide real-time temperature feedback by measuring changes in resistance. This feedback is crucial for adjusting heating or cooling mechanisms in various devices and machinery. Additionally, NTC thermistors are used for inrush current limiting by providing high resistance at low temperature to mitigate the initial surge of current when a device is turned on; as the temperature increases due to current flow, their resistance decreases, allowing the circuit to operate normally, preventing component damage and extending the lifecycle of electronic devices. In temperature compensation circuits, NTC thermistors are used to compensate the temperature drift of other components and circuits. They are used to maintain consistent performance of the circuit despite environmental changes.
PTC Thermistors: Positive Temperature Coefficient
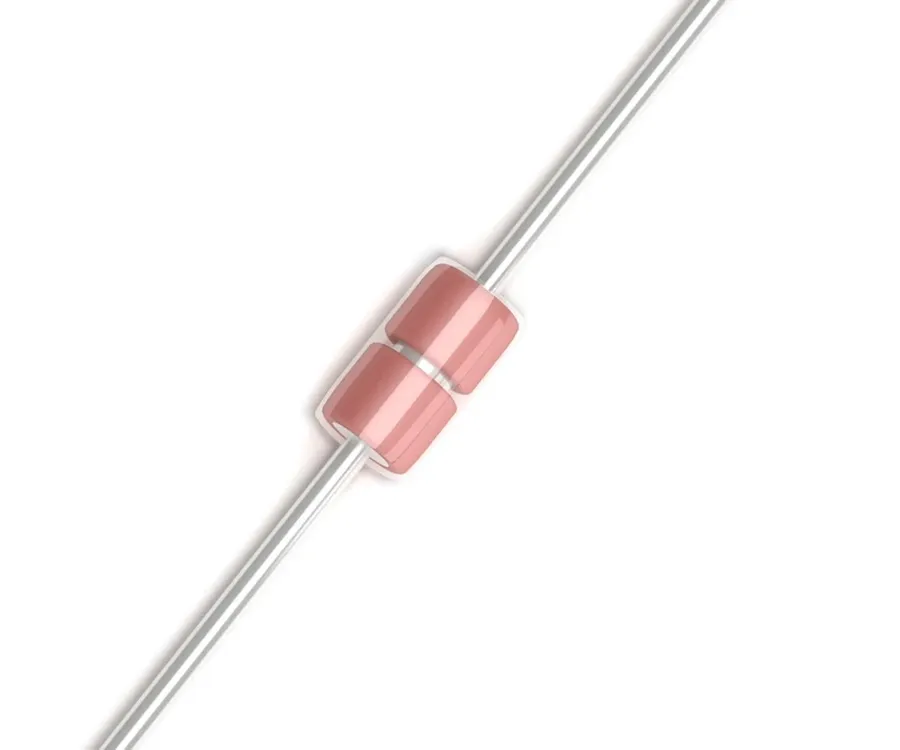
PTC (Positive Temperature Coefficient) thermistors are a class of thermal resistors characterized by a significant increase in electrical resistance as their temperature rises. This behavior makes them invaluable in a range of applications where overcurrent protection, temperature control, or self-resetting capabilities are required. Unlike NTC thermistors, which exhibit a decrease in resistance with increasing temperature, PTC thermistors' unique property is due to the material's crystalline structure undergoing a transition at a certain temperature, known as the Curie temperature or switch temperature.
- Mechanism of Action
The behavior of a PTC thermistor is derived from changes in the material's microstructure, leading to an increase in electrical resistance above a specific temperature. This abrupt increase in resistance helps in controlling current flow as well as temperature, making it a great self-regulating component. - Overcurrent Protection
In the case of an overcurrent event, the temperature of the PTC thermistor increases due to resistive heating. The resulting increase in resistance acts as a limiter, thus protecting the circuit from excessive current. After the cause of the overcurrent is removed, the device cools down and its resistance decreases to its base value. - Self-Resetting Fuses
PTC thermistors are used as self-resetting fuses. When a fault occurs and leads to excessive current flow, the PTC thermistor rapidly heats up, increasing its resistance and effectively stopping the current flow. Once the fault is resolved, the thermistor cools down and returns to its initial low resistance state, allowing the circuit to function again without manual replacement of a fuse. - Temperature Control
Due to their positive temperature coefficient, PTC thermistors are used in temperature control applications, such as heating devices where the temperature is regulated by the current flowing through the thermistor, providing self-limiting temperature control, for instance in small heaters and car seat heaters
Feature | PTC Thermistor |
---|---|
Temperature Coefficient | Positive: Resistance increases with temperature |
Primary Application | Overcurrent protection, Self-resetting fuses, Temperature control |
Temperature Response | Non-linear increase in resistance above a specific (Curie) temperature |
Behavior after Fault | Returns to low resistance state after cooling |
Key Differences: NTC vs PTC Thermistors
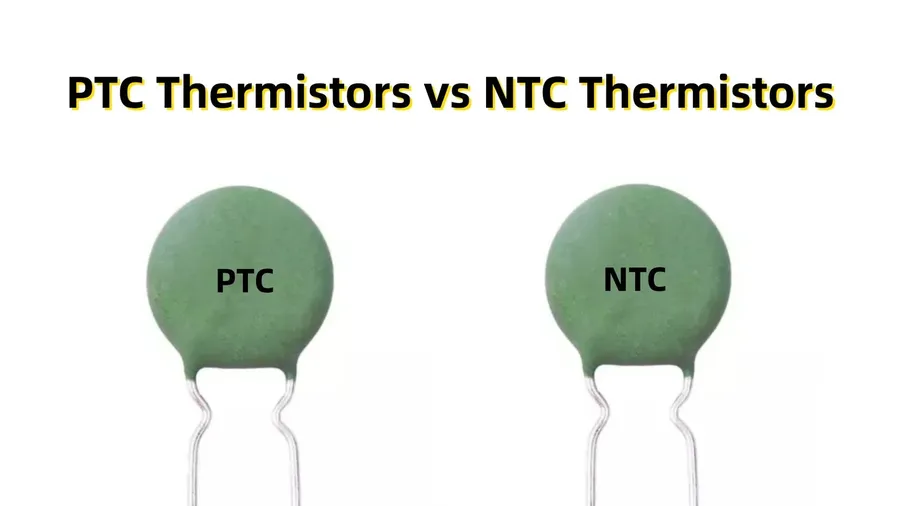
NTC (Negative Temperature Coefficient) and PTC (Positive Temperature Coefficient) thermistors are both temperature-sensitive resistors, but they exhibit opposite behaviors in how their resistance changes with temperature. This fundamental difference dictates their applications and selection criteria. Understanding these distinctions is crucial for choosing the appropriate thermistor for a specific application.
Feature | NTC Thermistor | PTC Thermistor |
---|---|---|
Temperature Coefficient | Negative (Resistance decreases as temperature increases) | Positive (Resistance increases as temperature increases) |
Typical Applications | Temperature measurement, inrush current limiting, temperature compensation | Overcurrent protection, self-resetting fuses, temperature control |
Resistance-Temperature Curve | Decreasing exponential curve | Increasing exponential or 'step' curve, often with a sharp transition temperature |
Response to Overheating | Resistance decreases with increasing temperature, may lead to thermal runaway | Resistance increases drastically with increasing temperature, limiting current flow |
Sensitivity | Highly sensitive to temperature changes, particularly in their operating range | Sensitivity changes greatly at a specific temperature point, and less sensitive beyond that point |
Material Composition | Typically made of metal oxides (e.g., manganese, nickel, cobalt) | Typically made of ceramic materials (e.g., barium titanate) |
Accuracy | Can be very accurate for temperature measurement with appropriate calibration. | Generally less accurate for temperature measurement than NTC thermistors, due to the materials being less precise during manufacturing. |
Thermal Resistor Applications Across Industries
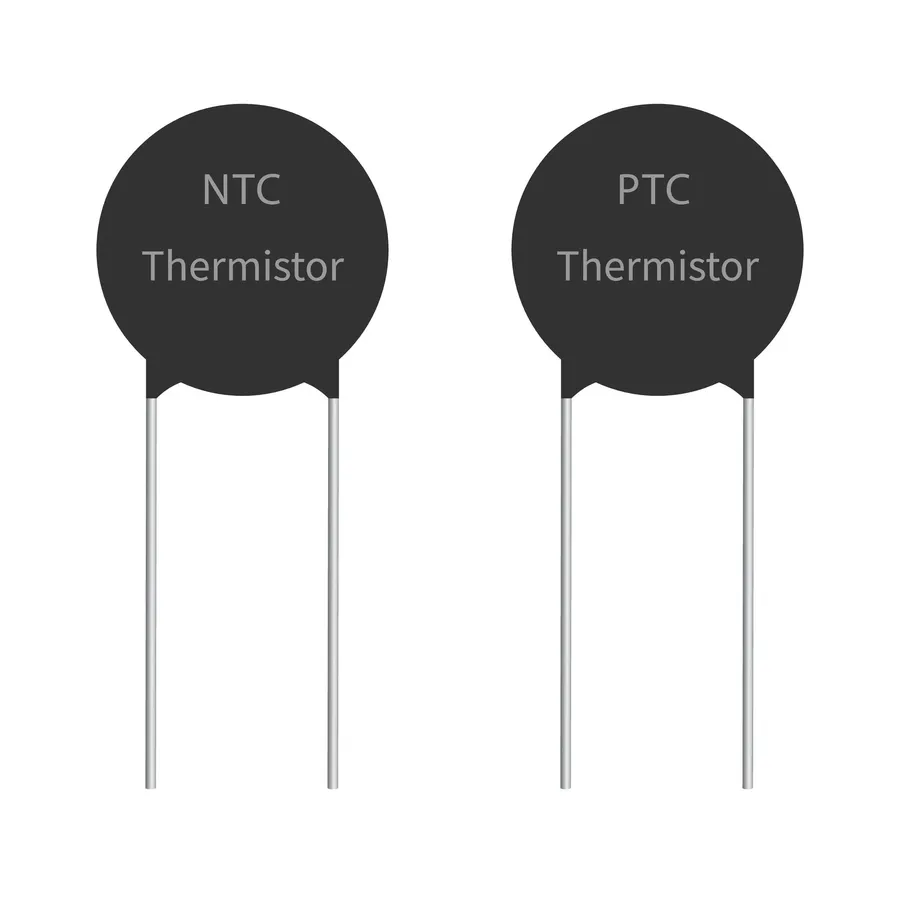
Thermal resistors, commonly known as thermistors, are crucial components across various industries due to their temperature-sensitive resistance. Their ability to accurately measure and respond to temperature changes makes them indispensable in a wide array of applications, from ensuring safety in automotive systems to precise control in medical devices. These applications leverage the unique properties of both Negative Temperature Coefficient (NTC) and Positive Temperature Coefficient (PTC) thermistors.
Industry | Application | Thermistor Type | Specific Use Case |
---|---|---|---|
Automotive | Engine temperature monitoring, cabin climate control | NTC | Monitoring coolant temperature to prevent overheating; adjusting HVAC based on internal cabin temperature. |
Industrial | Process control, temperature regulation in machinery | NTC/PTC | Ensuring precise temperature levels in chemical reactors; preventing overheating in industrial motors. |
Medical | Temperature probes, patient temperature monitoring | NTC | Monitoring body temperature in digital thermometers; precise temperature control in incubators. |
Consumer Electronics | Battery protection, thermal management in devices | PTC/NTC | Preventing battery overcharge and overheating; maintaining safe operating temperatures in smartphones and laptops. |
Aerospace | Avionics temperature monitoring, environmental control systems | NTC | Monitoring critical electronic component temperatures; controlling cabin and cargo temperature. |
Renewable Energy | Solar panel temperature monitoring, wind turbine thermal management | NTC | Optimizing the efficiency of solar panels; preventing overheating in wind turbine generators. |
In summary, the versatility of thermistors allows them to be used for a variety of different applications, each taking advantage of the sensitivity of NTC or PTC thermistors to temperature variation. The choice of which thermistor type to use depends entirely on the application and the need.
How to Choose the Right Thermal Resistor
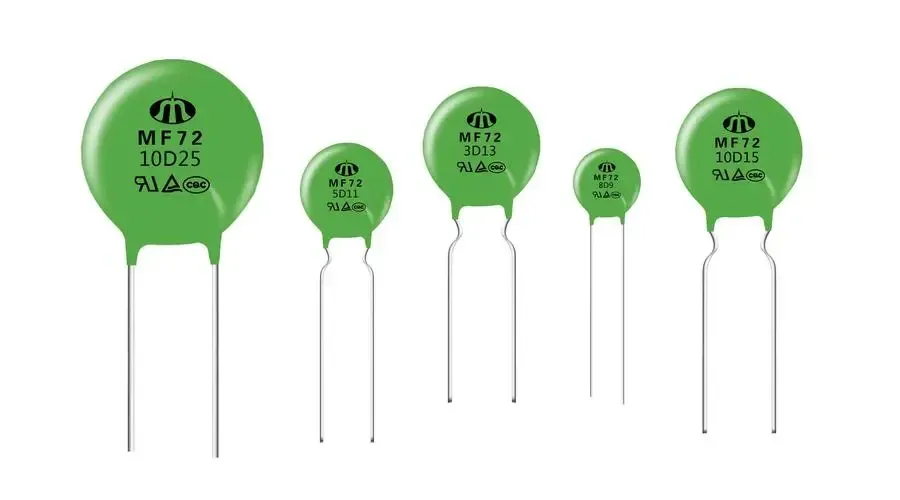
Selecting the appropriate thermal resistor, or thermistor, requires careful consideration of several key factors to ensure accurate temperature sensing, control, or circuit protection. This process involves aligning the thermistor's specifications with the demands of the application environment and performance requirements.
The following table provides a summary of the key parameters to consider when choosing a thermistor:
Parameter | Description | Considerations |
---|---|---|
Temperature Range | The range of temperatures the thermistor is expected to operate within. | Ensure the operating temperature range of the thermistor covers the expected minimum and maximum temperatures of your application. |
Required Accuracy | The precision required for temperature measurement or control. | High-accuracy applications require thermistors with a tight tolerance on their resistance-temperature curve. |
Response Time | How quickly the thermistor reacts to changes in temperature. | Faster response times are needed in applications with rapid temperature fluctuations. |
Resistance Value | The thermistor's resistance at a specified temperature (typically 25°C). | Select a resistance value appropriate for your circuit design to ensure proper signal conditioning and avoid loading issues. |
Physical Size | The physical dimensions of the thermistor. | Consider the available space and mounting requirements of your application. |
Environmental Conditions | Factors such as humidity, corrosion, and mechanical stress. | Select a thermistor packaged to withstand the operating environment. Coating with epoxy may also be needed. |
B Value (for NTC thermistors) | A parameter representing the rate of change in resistance with temperature. | This is important for calculating resistance at different temperatures and ensuring thermal resistor performance. |
Material and Type | Choice between NTC, PTC, and other material-specific thermal resistors | NTC for temperature sensing, PTC for overcurrent protection. Selection impacts the change in resistance according to change in temperature. |
Frequently Asked Questions About Thermal Resistors (Thermistors)
This section addresses common questions about thermal resistors, also known as thermistors, providing clear and concise answers to enhance understanding of their functionality and applications. We delve into the nuances of both PTC and NTC thermistors, offering practical insights into their use.
- What are the primary applications of PTC thermistors?
PTC (Positive Temperature Coefficient) thermistors are primarily used for overcurrent protection, acting as self-resetting fuses. When a current surge occurs, their resistance rapidly increases, limiting the current and protecting the circuit. They also find application in temperature control and heaters, where their characteristic resistance change with temperature can be utilized. - How do thermistors compare to RTDs for temperature measurement?
Thermistors and RTDs (Resistance Temperature Detectors) are both used for temperature sensing, but they differ in characteristics. Thermistors offer higher sensitivity and faster response times within a narrower temperature range, while RTDs are more linear and stable over a wider temperature range but may have lower sensitivity. The choice between them depends on the specific application's accuracy, temperature range, and response time requirements. - What parameters of the environment can a thermistor detect?
Thermistors are primarily designed to detect changes in temperature. However, since their resistance varies with temperature, they can indirectly sense other environmental parameters that influence temperature, such as changes in air flow, liquid levels, or the presence of heat-generating components. It is important to note that the temperature itself is the direct measurement. - What is the thermal resistance of a typical resistor, and how does it relate to a thermistor?
The term "thermal resistance of a resistor" refers to how much the temperature of a standard resistor increases with power dissipation. Unlike thermistors, standard resistors have minimal changes in resistance with temperature, making them unsuitable for temperature sensing. However, both will generate heat when current flows. Thermistors, on the other hand, are specifically designed with a high temperature coefficient, causing significant resistance changes with temperature, making them ideal for temperature-related applications. - How are NTC thermistors used for temperature measurement?
NTC (Negative Temperature Coefficient) thermistors are highly effective in temperature measurement due to their characteristic of decreasing resistance as temperature increases. They are often used in a voltage divider circuit with a known reference resistor. The voltage change across the thermistor, due to its changing resistance, can be converted into an accurate temperature measurement. This makes them suitable for applications requiring sensitive temperature detection such as medical probes and battery protection systems. - How do you calculate resistance based on temperature for a thermistor?
The resistance-temperature relationship for a thermistor is non-linear, typically described by the Steinhart-Hart equation or simplified versions like the beta parameter model. Manufacturers provide specific parameters for each thermistor. In practical use, the basic relationship is an exponential curve. While these equations help calculate the resistance at different temperatures, calibration with known temperatures is generally recommended for high accuracy, using reference tables. - What are the advantages and disadvantages of using a thermistor?
Thermistors offer advantages such as high sensitivity to temperature changes, fast response time, small size, and relatively low cost. However, they exhibit non-linear resistance-temperature characteristics, which may require complex signal processing or look-up tables. They also have a limited temperature range, especially compared to RTDs, and can be susceptible to self-heating if not used carefully.
Testing and Troubleshooting Thermal Resistors
Effective testing and troubleshooting of thermal resistors, or thermistors, are crucial for ensuring the reliability and accuracy of temperature-sensitive circuits. This involves understanding how to measure resistance variations with temperature changes and diagnosing common issues.
The primary method for testing a thermistor involves using a multimeter to measure its resistance at different temperatures. Here's how to do it:
- Initial Resistance Measurement
Begin by using a digital multimeter set to measure ohms, measure the resistance of the thermistor at room temperature. Record this value as your baseline resistance. - Controlled Temperature Changes
Apply controlled temperature variations using a heat source, such as a heat gun (at a safe distance) or a refrigerator. Measure and record the resistance at each temperature point. Ensure the temperature range covers the operating range of your specific thermistor. - Data Analysis
Compare the measured resistance values against the manufacturer's specifications. The resistance should change in the expected manner (decreasing for NTC thermistors, increasing for PTC) and within the expected range.
Common problems with thermistors include:
- Open circuit
An open circuit is indicated by an infinite resistance reading. This usually means the thermistor is damaged. - Short circuit
A short circuit will read a resistance close to zero ohms. This is indicative of internal damage to the thermistor. - Incorrect resistance value
If the resistance values deviate substantially from the manufacturer's datasheet, the thermistor may be damaged or degraded over time. - Non-linear behaviour
Thermistors have a non-linear resistance-temperature relationship. However, if the resistance change at a given temperature is dramatically different from the expected behaviour, the thermistor might be malfunctioning.
Troubleshooting techniques for thermal resistors involve:
- Visual Inspection
Examine the thermistor for any physical damage, such as cracks, burns or broken leads. - Resistance verification
Ensure that the resistance readings are consistent with the thermal resistor’s specifications by using an accurate multimeter. - Datasheet comparison
Refer to the thermal resistor’s datasheet and compare the resistance vs. temperature readings to the specified characteristics. Discrepancies can point towards a faulty device. - Circuit Analysis
Inspect the connection points of the thermistor to ensure no breaks or shorts in the circuit.
By following these testing and troubleshooting methods, engineers can accurately evaluate thermal resistor performance, identify any potential issues, and ensure that these components operate within the expected parameters.
Thermal Resistor Symbol and Measurement
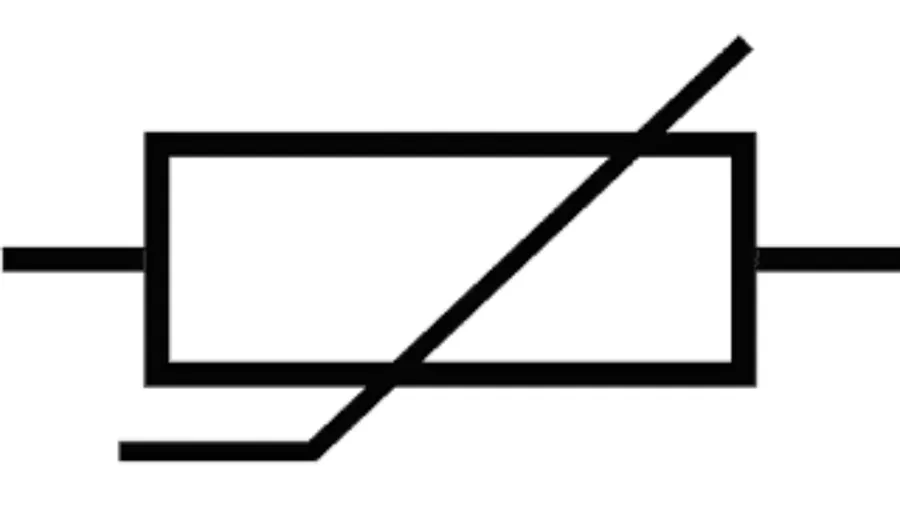
Understanding the symbolic representation and measurement techniques for thermal resistors, commonly known as thermistors, is crucial for effective circuit design and troubleshooting. This section details the standard schematic symbol used in electronic diagrams, clarifies the units of thermal resistance, and outlines the process for performing practical tests using a multimeter.
The schematic symbol for a thermistor typically resembles a standard resistor, but with an added curve or a ‘T’ to denote its temperature sensitivity. While there isn't a single, universally standardized symbol, two common symbols are frequently used: one resembling a standard resistor with a diagonal line crossing it, often used for NTC thermistors, and another with the addition of a T-shape, generally used for PTC thermistors.
Thermal resistance, in contrast, is a measure of a material's ability to impede the flow of heat and is expressed in units of degrees Celsius per Watt (°C/W) or Kelvin per Watt (K/W). It’s important to note that while the term 'thermal resistance' is used in the context of both a resistor's resistance to heat and a thermistor's change in electrical resistance with temperature, they are distinct concepts. A thermistor's temperature sensitivity is generally characterized by its temperature coefficient (NTC or PTC) and a nominal resistance at a specific temperature.
Practical testing of thermistors usually involves measuring their resistance at various temperatures using a digital multimeter. The procedure is as follows:
- Gather your Equipment
You will need a digital multimeter, the thermistor to be tested, and a method for controlling or measuring temperature (e.g., a calibrated heat source or thermometer). - Set the Multimeter
Configure the multimeter to measure resistance (Ohms, Ω). Select an appropriate range setting; often a 20kΩ range is suitable for starting. - Measure at Room Temperature
Measure the resistance of the thermistor at a known ambient temperature. Record both the resistance reading and the ambient temperature. This will serve as your initial data point for further comparisons. - Apply a Controlled Temperature
Using your heat source (like a hot plate), carefully expose the thermistor to an altered, measured temperature. This could be achieved via a controlled hot air gun or immersion in a heated liquid. Avoid overheating and ensure the thermistor is heated uniformly. Record both the resistance and the temperature. - Repeat for Multiple Points
Measure at several different temperatures, allowing the thermistor to stabilize before each reading. For accurate readings, wait for the resistance reading to stabilize. Plot these values on a graph to see the characteristic resistance-to-temperature curve. - Analyze the Data
Compare the measured resistances at different temperatures to the thermistor's datasheet specifications. This will verify its operation and also be helpful in calibration.
This process helps establish the thermistor’s behaviour and is crucial for ensuring its suitability for temperature sensing, compensation or control applications.
Future Trends in Thermal Resistors
The field of thermal resistors, or thermistors, is continuously evolving, driven by the demands for greater precision, miniaturization, and adaptability in diverse applications. Future trends point towards significant advancements in material science, fabrication techniques, and application-specific designs, promising enhanced performance and wider adoption of thermistor technology.
- Miniaturization
Ongoing research focuses on developing smaller and thinner thermistors. This miniaturization is crucial for applications in portable devices, wearable technology, and integrated circuits where space is limited. Advances in thin-film deposition and microfabrication are key drivers. - Improved Sensitivity and Accuracy
Future thermistors will likely feature improved sensitivity, allowing for the detection of minute temperature variations. Enhanced accuracy will be achieved through new materials with more stable temperature coefficients and precise manufacturing processes. This is critical for applications like medical temperature monitoring and precise industrial process control. - Higher Operating Temperatures
Research is being conducted to develop thermistors that can function reliably in high-temperature environments, which is essential for automotive, aerospace, and industrial applications. New ceramic and composite materials are being explored to meet these challenging conditions. - Smart Thermistors and Integration
The integration of thermistors with microcontrollers and wireless communication modules is a growing trend, leading to "smart" thermistors that can provide real-time temperature data and facilitate remote monitoring and control. These smart sensors will be increasingly vital for IoT and smart home applications. - Self-Healing and Adaptive Thermistors
The development of thermistors with self-healing capabilities or adaptive response to environmental changes is an area of active research. These advanced functionalities could extend the operational life and reliability of thermistors in harsh conditions, and reduce maintenance. - New Materials and Fabrication Techniques
Novel materials and fabrication methods are constantly explored to enhance performance and lower production costs. Nanomaterials, 3D printing, and advanced ceramic techniques are being investigated to create thermistors with tailored properties. These advances will unlock capabilities not seen before. - Emerging Applications
Beyond existing applications, future thermistors are poised to play significant roles in new technologies such as renewable energy systems, electric vehicles, advanced medical diagnostics, and environmental monitoring. Their versatility will drive adoption into more fields.
In conclusion, thermal resistors, or thermistors, are indispensable components in modern electronics and thermal management systems. Their unique ability to change resistance with temperature makes them ideal for a vast array of applications, from simple temperature sensing to complex thermal control. Understanding the difference between NTC and PTC thermistors, their specific properties and uses, is crucial to ensuring the efficient and safe operation of countless devices and systems we rely on daily. As technology advances, so too will the capabilities and applications of thermal resistors, making them a vital area of ongoing study and development for future innovations.
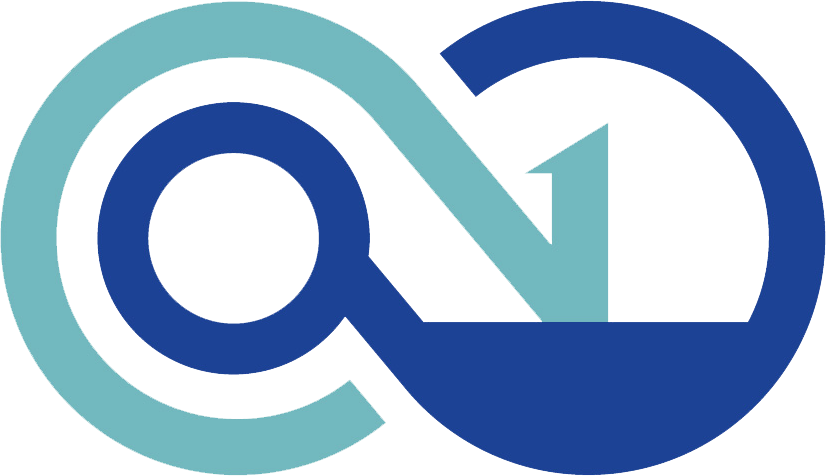