Unlocking the Power of TRIACs: A Comprehensive Guide
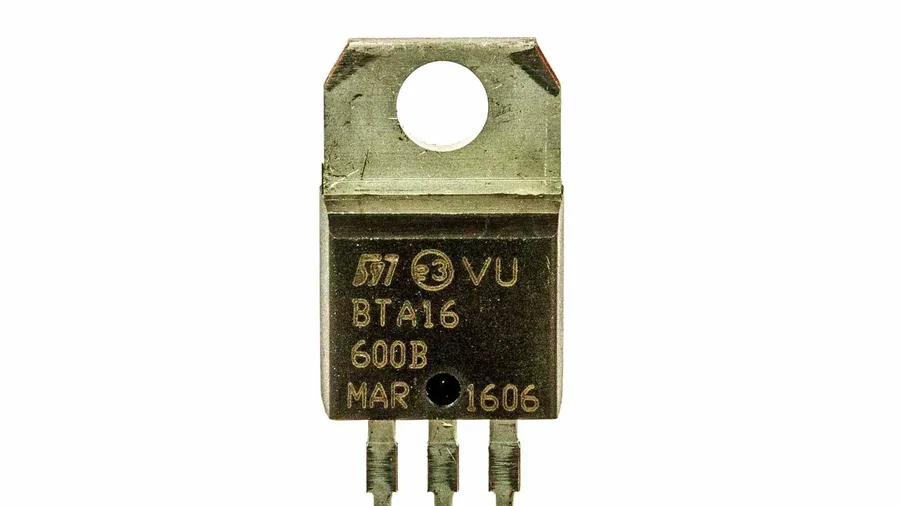
Imagine a light switch that can control the brightness of your lamp smoothly, or a motor that changes speed without sudden jumps. This precise control over alternating current (AC) is often achieved using a fascinating semiconductor device called a TRIAC. Similar to how a transistor acts as a digital switch, a TRIAC manages AC power flow. This article delves deep into the workings, applications, and advantages of TRIACs, providing you with the knowledge to harness their potential.
What is a TRIAC?
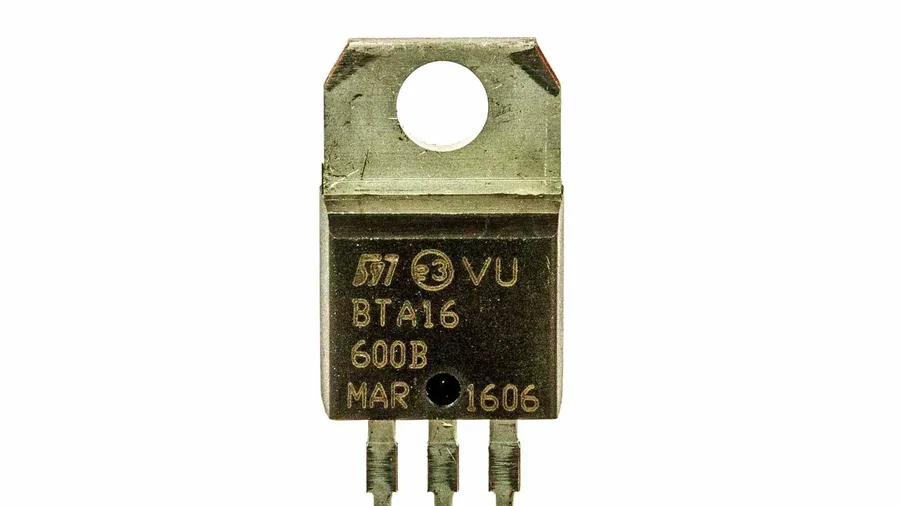
A TRIAC, or Triode for Alternating Current, is a three-terminal semiconductor device engineered to function as a bidirectional switch for AC power control. Its core functionality lies in its ability to conduct current in either direction upon activation, distinguishing it from diodes which only allow unidirectional current flow. This bidirectional conductivity makes TRIACs particularly suitable for AC circuit applications where controlled switching is required.
How TRIACs Work: The Underlying Mechanism
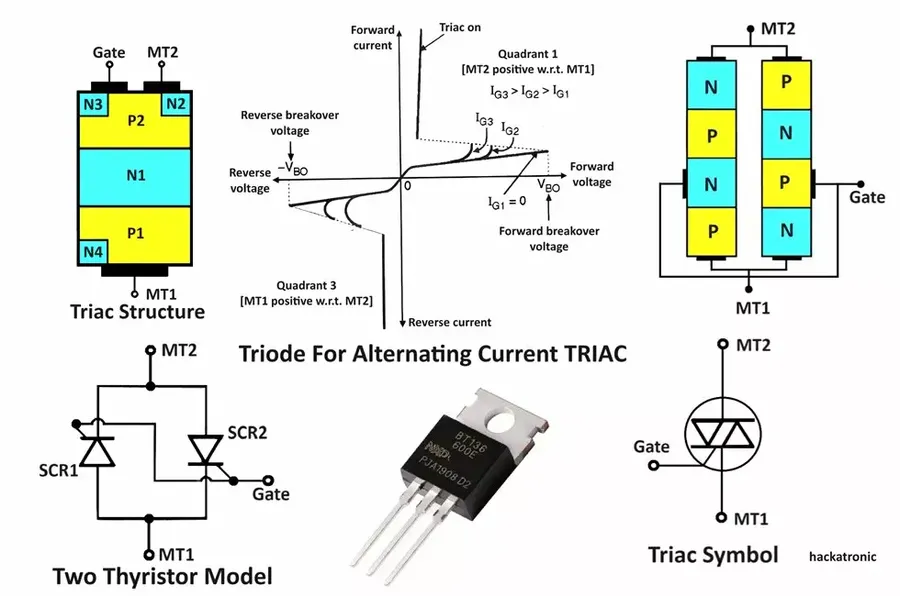
TRIACs, or Triode for Alternating Current, function as bidirectional switches, enabling current flow in either direction within an AC circuit. This behavior is achieved through a sophisticated four-layer semiconductor structure, analogous to two thyristors connected in inverse parallel within the same device, facilitating conduction during both positive and negative alternations of the AC waveform.
Central to the operation of a TRIAC is the gate terminal. Applying a small current to this terminal triggers the TRIAC into a conductive state, allowing current to flow between Main Terminal 1 (MT1) and Main Terminal 2 (MT2), regardless of polarity. Once triggered, the TRIAC remains conductive until the current flowing through the device falls below a certain threshold known as the holding current. This is different from SCR's which once triggered require the current to drop to zero to turn off. The triggering and holding mechanisms are fundamental to a TRIAC's function as an AC switch.
The internal structure of a TRIAC can be visualized as a combination of two SCRs (Silicon Controlled Rectifiers) integrated together. This integration allows the TRIAC to switch current in both directions unlike an SCR which can only switch in one direction. When a positive voltage is applied to the gate with respect to MT1 or a negative voltage with respect to MT2, the device will switch on. Likewise, when a negative voltage is applied to the gate with respect to MT1 or a positive voltage with respect to MT2, the device will also switch on. The minimum gate current to switch the device varies with the voltage difference between MT1 and MT2 and the temperature of the device.
TRIAC vs. SCR: Key Differences
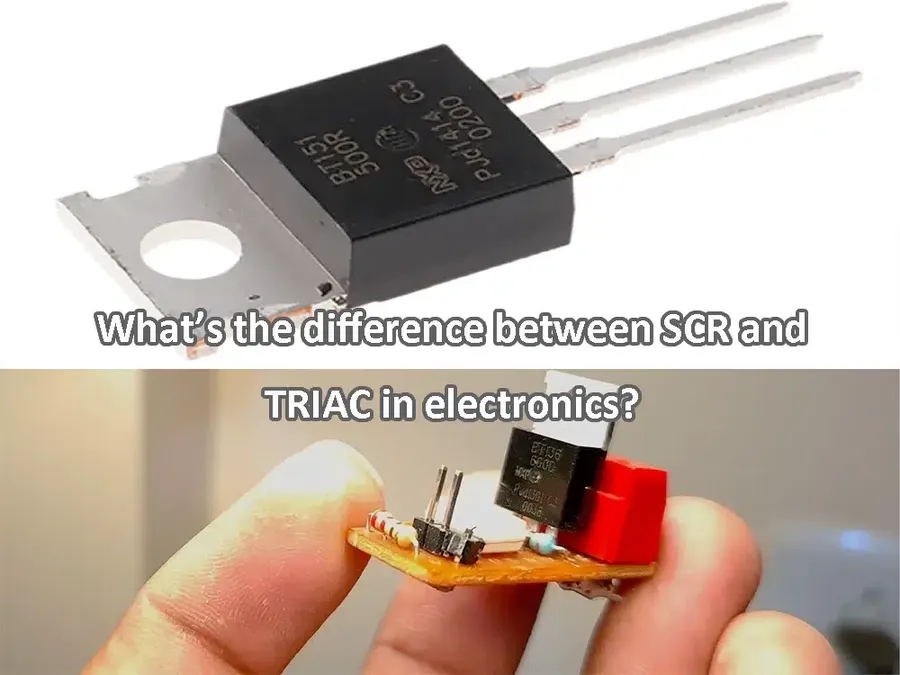
TRIACs and Silicon Controlled Rectifiers (SCRs) are both semiconductor devices used for switching applications, but they exhibit fundamental differences in their conduction behavior. TRIACs are specifically designed for bidirectional AC current control, while SCRs are unidirectional devices typically used in DC circuits or controlled rectification of AC.
Feature | TRIAC | SCR |
---|---|---|
Conduction Direction | Bidirectional (AC) | Unidirectional (DC) |
Number of Terminals | 3 (MT1, MT2, Gate) | 3 (Anode, Cathode, Gate) |
Primary Application | AC power control, phase control | Controlled rectification, DC power control |
Gate Triggering | Can be triggered with either positive or negative gate current | Triggered with positive gate current |
Holding Current | Maintains conduction until current falls below a minimum level in either direction | Maintains conduction until current falls below a minimum level in forward direction |
Typical Circuit | AC circuits, light dimmers, motor speed controls | DC circuits, rectifiers, inverters |
The fundamental difference lies in their structure and capability to handle current flow. TRIACs are effectively two SCRs connected in inverse parallel, which allows them to conduct in both directions. This makes them well suited for AC applications. SCRs, on the other hand, have a single p-n junction structure, allowing current to flow only from anode to cathode, making them suitable for unidirectional DC applications or situations where only half the AC cycle needs to be controlled.
TRIAC Symbol and Terminal Identification
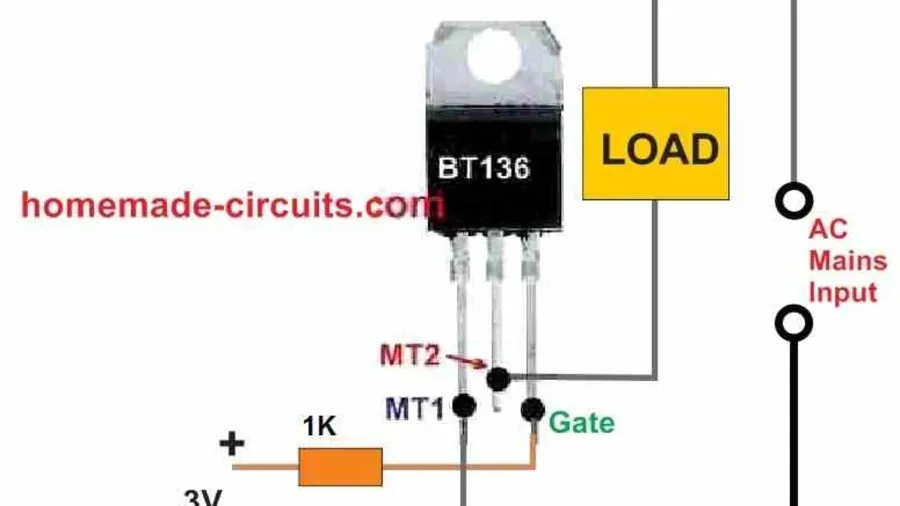
TRIACs, essential components in AC power control, are represented by a specific symbol in circuit diagrams, which facilitates clear communication in technical designs. Identifying the terminals correctly is crucial for proper circuit implementation and functionality. The TRIAC's three terminals—Main Terminal 1 (MT1), Main Terminal 2 (MT2), and Gate (G)—each play a distinct role in its operation.
The schematic symbol for a TRIAC visually conveys its bidirectional capability, and understanding its representation is fundamental to circuit analysis and design involving AC power control.
- Main Terminal 1 (MT1)
This terminal serves as one of the two main current conduction points in the TRIAC. Its role is analogous to the cathode in a diode, but with bidirectional functionality. - Main Terminal 2 (MT2)
This terminal acts as the second main current conduction point, comparable to the anode in a diode but, again, with the ability to conduct current in either direction. - Gate (G)
The gate terminal is the control input that triggers the TRIAC into its conductive state. Applying a small current pulse to the gate, either positive or negative relative to MT1, enables current flow between MT1 and MT2.
TRIAC Switching Characteristics and Parameters
Understanding the switching characteristics and parameters of TRIACs is crucial for effective circuit design and application. These parameters define the TRIAC's operational limits and influence its behavior in AC power control. Key parameters include gate trigger voltage, holding current, maximum current handling capacity, and the nuances of symmetrical and asymmetrical firing.
Parameter | Description | Typical Values | Significance |
---|---|---|---|
Gate Trigger Voltage (VGT) | The minimum voltage required at the gate terminal to initiate conduction. This voltage is applied between the gate and MT1. | 0.5V to 2V (DC) | Ensures the TRIAC turns ON reliably. It must be considered in gate driver design. |
Gate Trigger Current (IGT) | The minimum current required at the gate terminal to initiate conduction. | 1mA to 50mA | Along with VGT, this defines the power requirement of gate triggering circuit. |
Holding Current (IH) | The minimum current required to maintain the TRIAC in the ON state. If the current drops below this, the TRIAC turns OFF. | 5mA to 100mA | Determines the minimum load current required to keep the TRIAC conducting after triggering. |
Maximum On-State Current (IT(RMS)) | The maximum root mean square (RMS) current that the TRIAC can safely handle in the conducting state. | 1A to 100A+ | Specifies the TRIAC's load-handling capacity; exceeding this can cause damage. |
Maximum Repetitive Peak Off-State Voltage (VDRM) | The maximum peak voltage that the TRIAC can block in the non-conducting state | 200V to 1200V+ | Defines the maximum reverse voltage the TRIAC can handle. This is critical for selecting a TRIAC for the application. |
Surge Current (ITSM) | The non-repetitive peak current that the TRIAC can handle for a short duration. | 10A to 1000A+ | Defines the TRIAC capability to handle short duration current surges, which are common in inductive loads. |
Symmetrical Firing | The TRIAC can be triggered by a positive or negative gate voltage with respect to MT1. | N/A | TRIACs inherently exhibit symmetrical firing, allowing for bidirectional control in AC circuits. |
Asymmetrical Firing | Some specialized TRIACs are designed with slightly different trigger sensitivities for positive and negative gate voltages | N/A | Used in specialized applications that require precise phase control. |
Common Applications of TRIACs
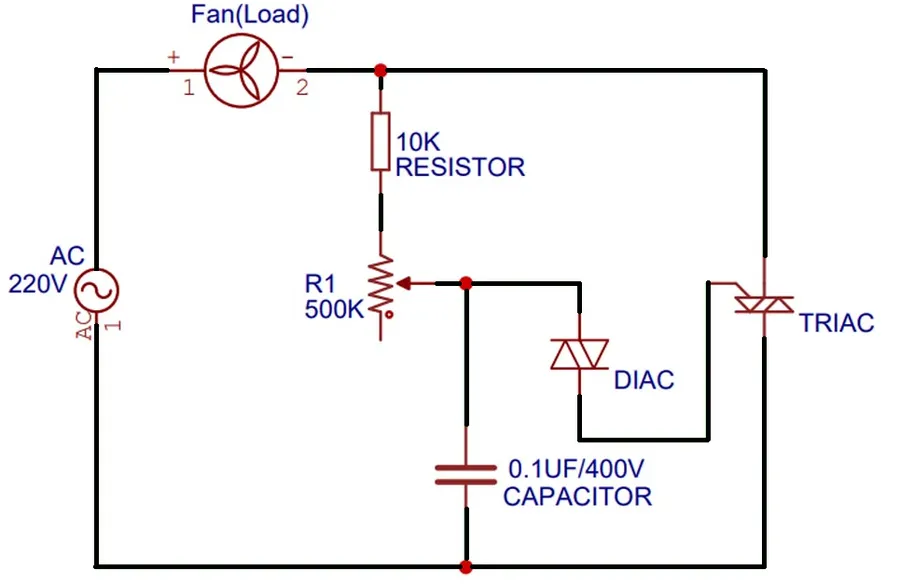
TRIACs, due to their ability to control AC power bidirectionally, are integral components in a multitude of applications across various sectors. These applications range from simple household devices to complex industrial control systems, showcasing the versatility of TRIACs in managing electrical loads.
- Light Dimmers
TRIACs are frequently used in light dimmers, enabling smooth and efficient control of light intensity. By varying the conduction angle of the AC waveform, the power delivered to the light bulb can be accurately adjusted, providing a range of lighting levels. This feature is highly valued for energy saving and creating ambience. - Motor Speed Control
TRIACs play a key role in controlling the speed of AC motors. In applications such as fans, pumps, and small appliances, TRIAC-based circuits modulate the power to the motor, allowing for precise speed adjustments. This control is crucial for optimizing performance and reducing energy consumption. - Temperature Controllers
In heating and cooling systems, TRIACs are instrumental in temperature control. By switching the power to resistive heating elements or cooling devices, TRIACs facilitate precise thermal regulation. This is used in applications from household heaters to industrial ovens and process control systems, where temperature stability is paramount. - Solid State Relays (SSRs)
TRIACs are core elements in solid-state relays, offering a reliable and fast switching alternative to mechanical relays. SSRs based on TRIACs can switch AC loads without the mechanical wear and tear associated with traditional relays, leading to improved reliability and lifespan. This is used across many industrial and commercial settings for switching high power loads.
Application | Control Method | Benefit | Typical Settings |
---|---|---|---|
Light Dimmer | Phase Angle Control | Adjustable Lighting, Energy saving | Residential and commercial lighting. |
Motor Speed Control | Phase Angle Control, Voltage Adjustment | Precise speed regulation, Energy saving | Fans, pumps, power tools |
Temperature Control | On/Off Switching, Phase Angle control | Accurate temperature regulation | Heaters, ovens, HVAC |
Solid State Relays | Switching | Reliable AC switching, long lifetime | Industrial automation, Power control systems |
TRIAC Circuit Design: Practical Tips
Designing reliable TRIAC circuits requires careful consideration of several key factors. Proper gate driving, the implementation of snubber circuits, and effective heat dissipation are paramount to prevent device failure and ensure optimal performance in AC power control applications. This section outlines practical tips for robust TRIAC circuit design.
- Gate Driving Considerations
Adequate gate current is crucial for reliably triggering the TRIAC. The gate drive circuit must supply sufficient current, typically specified in the TRIAC's datasheet, to turn the device 'ON' consistently and promptly. Conversely, when the device is expected to be 'OFF', it is essential that the gate current is insufficient to trigger conduction. Proper design should account for variations in supply voltage, component tolerance, and temperature changes to ensure reliable firing. A resistor between the gate and MT1 is commonly used to limit the current into the gate. - Snubber Circuits
Rapid changes in voltage (dv/dt) across a TRIAC can lead to unwanted triggering, especially in inductive loads. A snubber circuit, typically consisting of a resistor and capacitor in series, is placed in parallel with the TRIAC to suppress these voltage transients and prevent spurious triggering, thus improving the overall circuit reliability. The proper selection of component values is essential for achieving optimum performance from the snubber. - Heat Dissipation
TRIACs generate heat as they conduct current, particularly at higher power levels. Proper heat dissipation is essential to prevent overheating, which can lead to device failure or decreased lifespan. This can be achieved through the use of heatsinks, careful thermal management considerations in circuit layout, and ensuring the TRIAC is adequately rated for the intended load currents. The datasheet will provide the maximum operating junction temperature for the device which should not be exceeded. - Load Compatibility
The characteristics of the load being controlled significantly influence the selection of the TRIAC and its associated circuit components. Inductive loads, like motors, require snubber circuits and robust gate drive. Capacitive loads can cause high inrush currents at turn-on and require circuit designs to limit that current. It's necessary to consider the type of load and its impact on the TRIAC. - Component Selection
Component tolerances, such as resistor and capacitor variation, should also be accounted for. The use of robust components, meeting or exceeding required specifications, increases reliability and longevity. Select components whose specifications meet the design requirements of the application, and consider derating for increased operating life. - Layout and Noise Immunity
Careful attention to PCB layout minimizes noise and interference that could cause false triggering of the device. Keep gate and main circuit traces separate, and use appropriate shielding to minimize electromagnetic interference (EMI) that could affect circuit function. The gate circuit should be routed away from any sources of noise on the PCB.
Frequently Asked Questions About TRIACs
This section addresses common queries regarding TRIACs, clarifying their functionalities and applications in AC power control. Understanding these frequently asked questions will solidify your grasp of TRIAC operation and their suitability for diverse electrical engineering tasks.
- What are TRIACs primarily used for?
TRIACs are primarily used for controlling AC power in various applications. They act as electronic switches that can regulate the amount of power delivered to a load by controlling the phase angle of the AC waveform. This makes them ideal for applications such as light dimmers, motor speed controllers, and heating element regulators. Their bidirectional conduction capability is crucial for AC circuits. - Are TRIACs designed for AC or DC circuits?
TRIACs are specifically designed for AC circuits. Unlike devices like diodes or thyristors (SCRs) that have unidirectional current flow, TRIACs can conduct current in both directions. This bidirectional capability is essential for controlling alternating current, which periodically reverses direction. TRIACs cannot effectively control DC current since the gate trigger is only effective to start conduction, once the DC is flowing, the TRIAC can't be shut off. - What distinguishes a TRIAC from a thyristor (SCR)?
The primary difference lies in their conduction capabilities. A thyristor (SCR) is a unidirectional device, meaning it only conducts current in one direction. Once triggered, an SCR will continue conducting as long as the current does not fall below a certain threshold (holding current), but it will never conduct in reverse. A TRIAC, however, is bidirectional and can conduct current in both directions. This difference makes TRIACs suitable for AC circuits, while SCRs are primarily used in DC or rectified AC applications. - What are common applications of TRIAC outputs?
TRIAC outputs are commonly used to control various AC loads. These include, but are not limited to, resistive loads such as incandescent light bulbs and heating elements, as well as inductive loads such as AC motors and transformers. The control provided by TRIACs can vary from simple on/off switching to more complex phase angle control, offering a wide range of AC load management capabilities. - How does the gate signal control a TRIAC?
A TRIAC is triggered into conduction by applying a current pulse to its gate terminal. The gate signal only initiates the conduction; once triggered, the TRIAC continues to conduct until the current through the device drops below its holding current. The TRIAC will then block in either direction until another gate pulse is applied. The polarity of the gate signal can be positive or negative relative to MT1; in either case, it turns the TRIAC on. - What is 'phase control' and how does it relate to TRIACs?
Phase control is a technique used to regulate the average power delivered to an AC load by controlling the portion of the AC waveform during which the TRIAC conducts. By adjusting the point in the AC cycle where the TRIAC is triggered, the power delivered to the load is precisely controlled. This technique is common in light dimmers and motor speed controllers. - What are some important design considerations when using TRIACs?
Key design considerations when using TRIACs include proper gate driving to ensure reliable triggering, employing snubber circuits to prevent false triggering due to transient voltage spikes or rapid voltage changes (dv/dt), and adequate heat sinking to manage thermal buildup during operation. Correct component selection and circuit design are critical for reliable and safe operation.
TRIAC Selection Guide: Choosing the Right Device
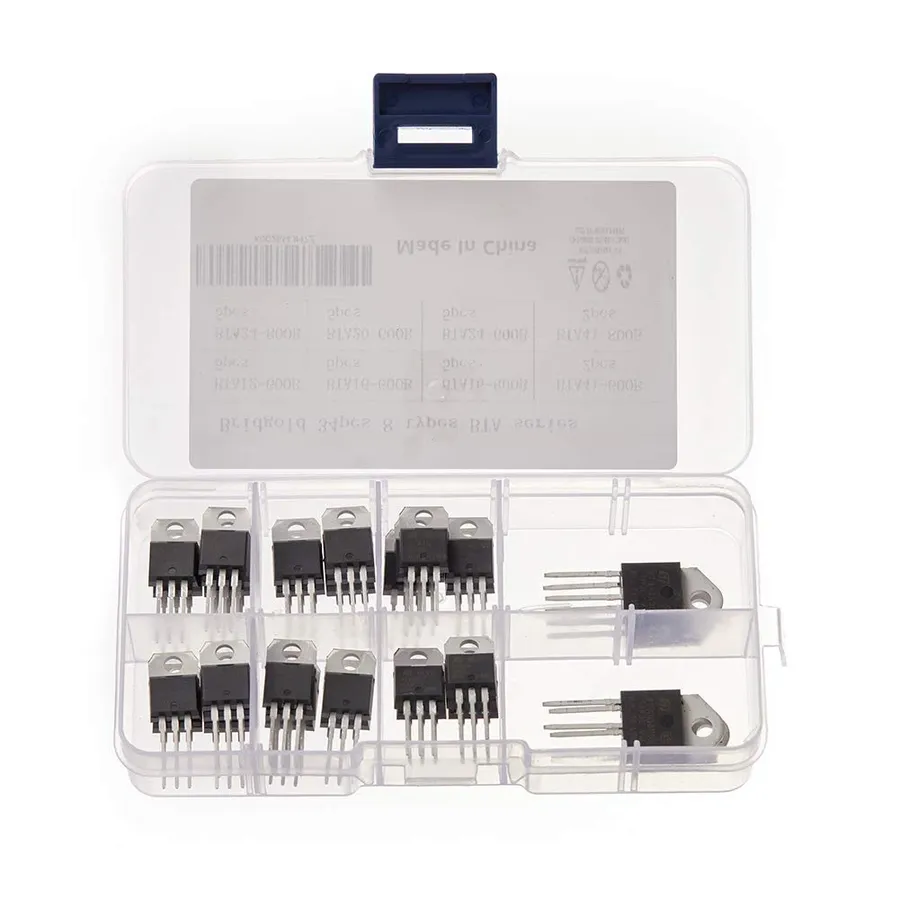
Selecting the appropriate TRIAC for a given application is crucial for ensuring both reliable circuit operation and longevity. This process involves carefully evaluating the circuit requirements and matching them with the TRIAC’s operational specifications. A mismatch can result in device failure, erratic performance, or insufficient control over the load. The key factors to consider when selecting a TRIAC include voltage and current handling capabilities, load characteristics, package type, and specific triggering requirements.
Parameter | Description | Importance |
---|---|---|
Voltage Rating (VDRM, VRRM) | The maximum allowable voltage the TRIAC can withstand in both forward and reverse directions without conducting. It’s specified as repetitive peak off-state voltage. | Must exceed the peak voltage of the AC supply to prevent damage. |
Current Rating (IT(RMS)) | The maximum RMS current the TRIAC can continuously handle. It's crucial for managing the current requirements of the load. | Must be greater than or equal to the load’s expected current draw to avoid thermal overload and failure. |
Gate Trigger Current (IGT) | The minimum gate current required to switch the TRIAC into conduction. | Affects the design of the gate drive circuit and the sensitivity of the device. |
Holding Current (IH) | The minimum current required to maintain the TRIAC in a conducting state. Once the current drops below this value, the device will turn off. | Important to avoid unwanted turn-off of TRIAC, especially with inductive loads |
Surge Current Rating (ITSM) | The maximum non-repetitive surge current the TRIAC can tolerate. | Must exceed the inrush current associated with the connected load to prevent device degradation. |
Operating Temperature Range | The range of ambient temperatures within which the TRIAC is designed to operate reliably. | Proper thermal design and heatsinking are required to prevent thermal overload. |
Package Type | The physical casing of the TRIAC (e.g., TO-220, TO-252, SMD). | Determines the mounting method and thermal characteristics, influencing the overall design and heatsinking needs. |
When choosing a TRIAC, it's essential to consider the load type. Resistive loads, like heaters or incandescent lights, have relatively stable current demands. However, inductive loads, such as motors or transformers, can cause significant inrush currents during turn-on or turn-off events, requiring TRIACs with higher surge current ratings and snubber circuits for proper operation. Additionally, the control circuit must be carefully designed to provide the required gate trigger current (IGT) and to prevent false triggering. Furthermore, ensure that the selected TRIAC matches the specific requirements of the circuit’s application, whether it be phase control, full-wave control, or zero-crossing switching.
- Step 1: Identify Application Requirements
Determine the voltage and current requirements of your load. What is the mains voltage? What is the peak and RMS current draw? - Step 2: Calculate Peak Voltage
For AC applications, calculate the peak voltage, as this value exceeds the RMS voltage. A TRIAC must handle this peak voltage without breakdown. - Step 3: Calculate RMS Current
Determine the required RMS current handling capability for the TRIAC based on the continuous current demand of your load. - Step 4: Consider Surge Currents
Assess the inrush current of your load, especially for inductive loads like motors. The TRIAC's surge current rating must exceed this to prevent device failure. - Step 5: Select the Right Package
Select a package that suits your mounting and thermal dissipation needs. Larger packages will be more suitable for larger currents. - Step 6: Triggering Requirements
Consider the required gate trigger current and design a gate drive circuit that meets these demands to ensure the TRIAC turns on reliably. - Step 7: Temperature Considerations
Consider the operating ambient temperature and how temperature rise will affect your component’s operation. Heatsinking may be required.
Advanced TRIAC Control Techniques
Advanced TRIAC control transcends basic on/off switching, delving into sophisticated methods that allow for precise modulation of AC power. These techniques, including phase angle control, zero-crossing detection, and microcontroller-based implementations, enable applications requiring finer control of electrical loads.
The following section will discuss three advanced techniques: phase angle control, zero-crossing detection, and microcontroller-based control.
**Phase Angle Control:** This technique involves triggering the TRIAC at a specific point within the AC waveform, rather than at the zero-crossing point. By delaying the firing angle, the average power delivered to the load can be adjusted. This is crucial for applications like light dimmers and motor speed controls, where a gradual increase or decrease in power is required. The firing angle is typically controlled using a control circuit that is synchronized with the AC line frequency.
**Zero-Crossing Detection:** Zero-crossing detection is a method used to trigger the TRIAC at or near the point where the AC waveform crosses zero volts. This technique minimizes electrical noise and electromagnetic interference (EMI) that can occur when switching at higher voltage points. By switching at zero crossing, the current waveform is more sinusoidal, which can increase component life and reduce stress on both the device and the load. Zero-crossing detection is often used in combination with other control techniques.
**Microcontroller-Based Control:** Microcontrollers allow for sophisticated, adaptive control of TRIACs. Using a microcontroller enables implementation of closed-loop control systems, where the actual output (e.g. temperature or light intensity) is measured and fed back into the control loop to adjust the firing angle. Microcontrollers also facilitate complex control algorithms that can respond to various inputs to achieve desired system operation. This is particularly beneficial for applications requiring precise and dynamic control of AC power.
TRIACs are truly the unsung heroes of AC power control, enabling seamless operation of countless devices around us. From dimming the lights to powering large motors, these versatile semiconductors are fundamental in electronics. Understanding how TRIACs function, their advantages, and proper application methods unlocks the potential for more sophisticated and efficient control over electrical systems. As technology continues to evolve, TRIACs will surely remain a key component in many areas of electrical engineering, particularly where precise AC control is required, thus underscoring the importance of understanding the power of TRIACs.
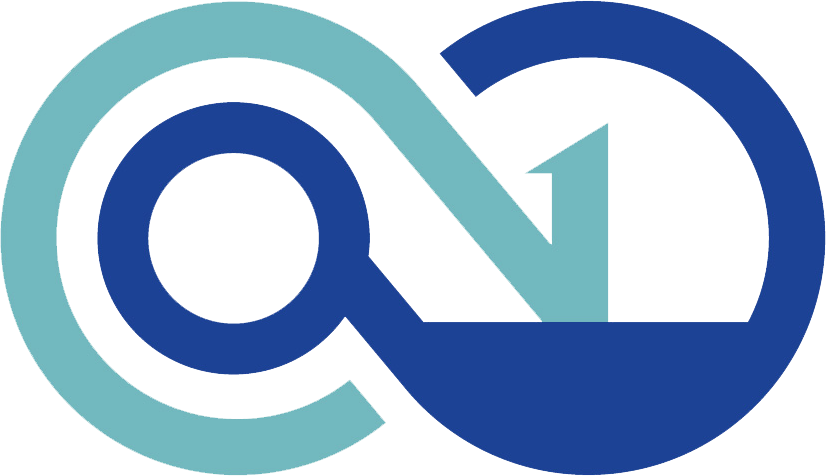