Unlocking the Secrets of Carbon Composite Resistors: A Comprehensive Guide
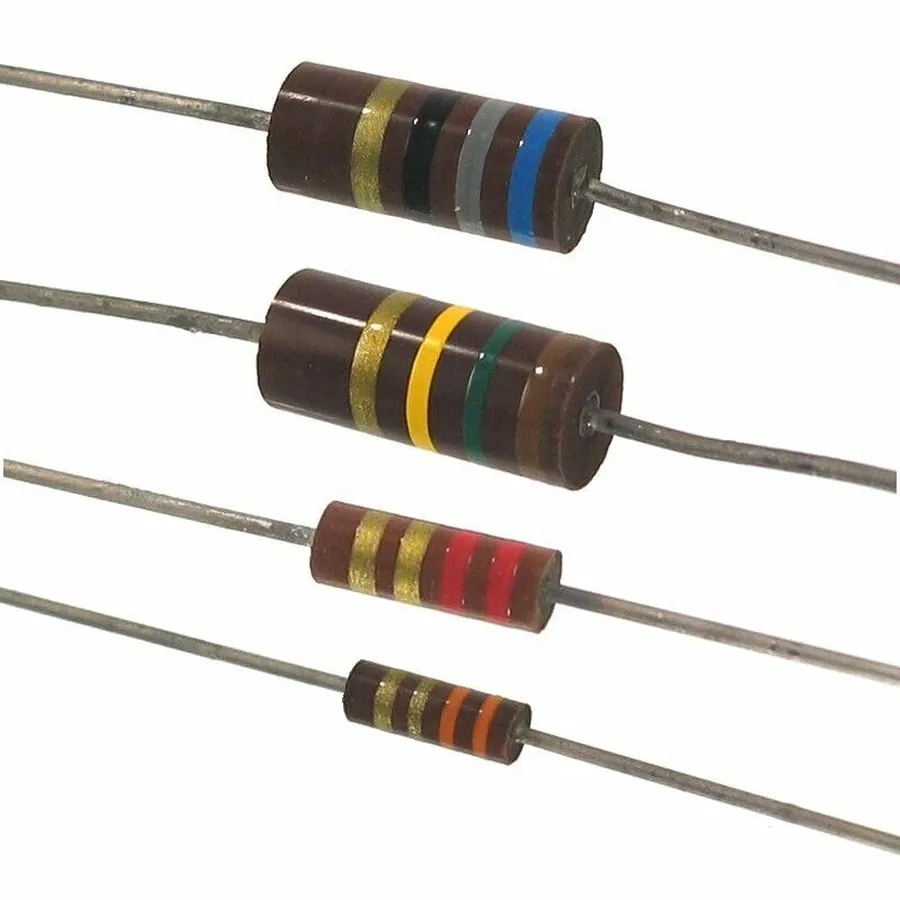
In our increasingly digitized world, electronic components like resistors are the unsung heroes behind countless devices. Among them, the carbon composite resistor stands out for its unique characteristics. This article delves into the composition, function, and practical applications of carbon composite resistors, bridging the gap between technical jargon and everyday understanding. We will explore its construction, advantages, limitations, and how it compares to other resistor types, offering insights beneficial for enthusiasts and seasoned professionals alike.
What is a Carbon Composite Resistor?
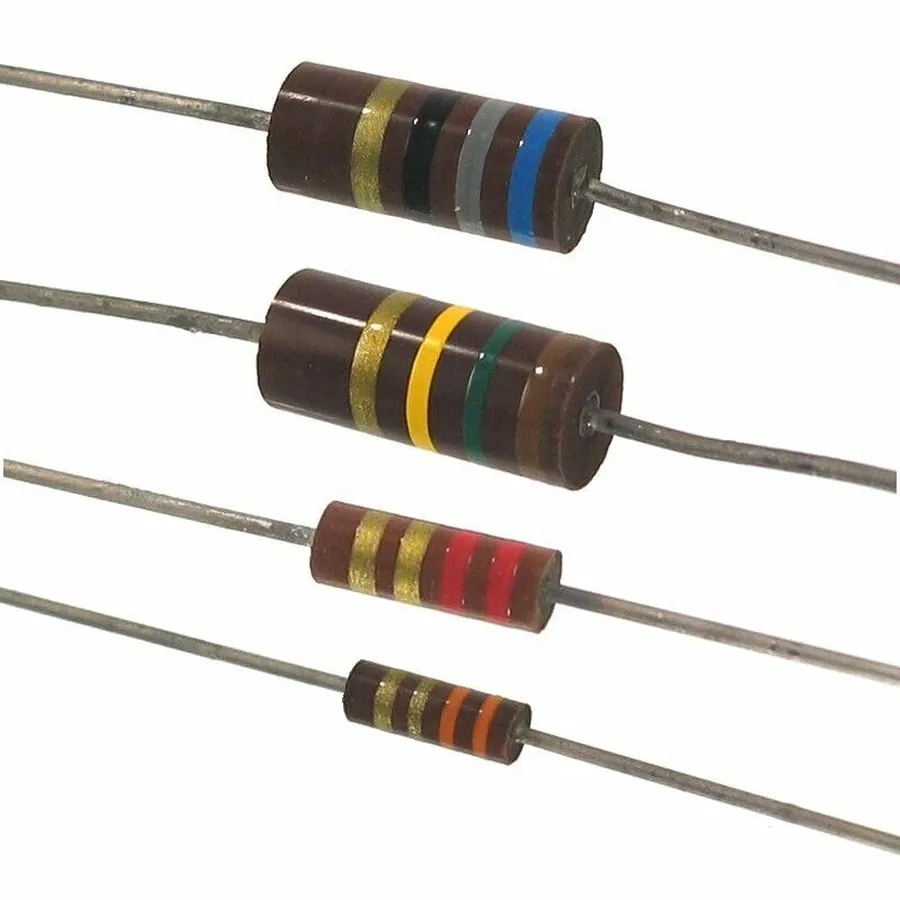
A carbon composite resistor, also known as a carbon composition resistor, is a type of fixed resistor characterized by its resistive element, which is made from a mixture of finely ground carbon particles and a non-conductive binder, typically a ceramic material. This mixture is molded into a cylindrical shape with embedded leads and then baked to create a solid, robust component. These resistors are fundamental in electronics, providing a defined resistance to electrical current, and stand out for their unique blend of performance characteristics.
The primary function of a carbon composite resistor, like all resistors, is to impede the flow of electrical current in a circuit. They achieve this by converting electrical energy into heat as electrons move through the carbon-binder composite. The resistance value is determined by the ratio of carbon to binder, with a higher carbon content leading to a lower resistance. Unlike film resistors that are constructed with a thin layer of resistive material, carbon composite resistors utilize a bulky solid core which grants it specific advantages and disadvantages.
Construction and Materials of Carbon Composite Resistors
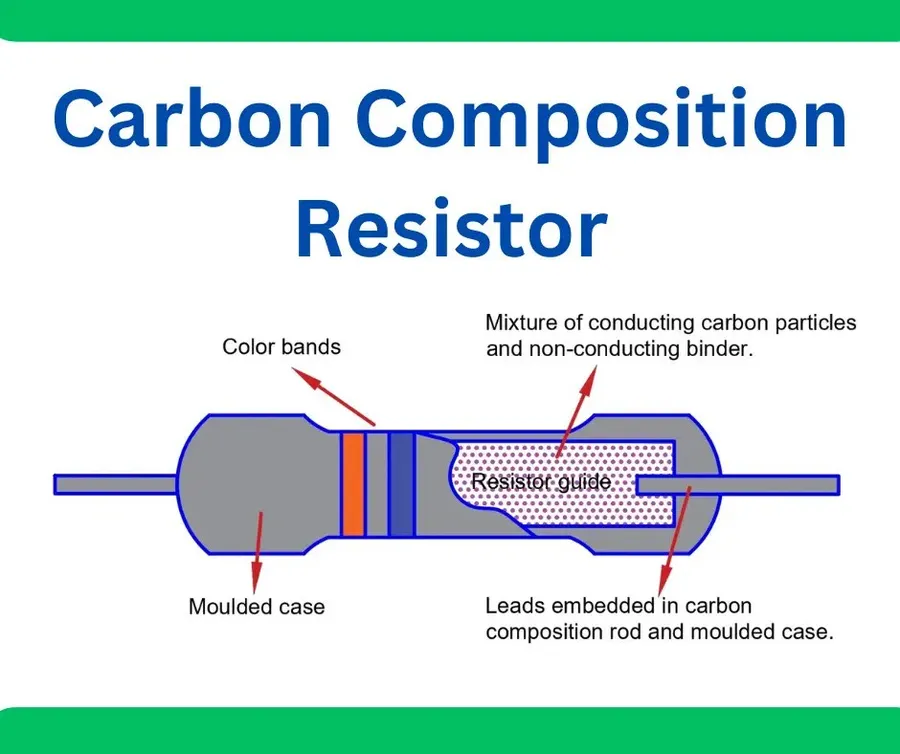
Carbon composite resistors are fabricated from a mixture of finely ground carbon particles and a non-conductive binder material, which are combined and molded to achieve a specific resistance value. The construction and composition of these resistors directly influence their electrical characteristics and performance.
The primary materials involved in the construction of carbon composite resistors are:
- Carbon Particles
Typically, carbon black or graphite is used. The concentration, particle size, and distribution of the carbon particles are critical in determining the overall resistance of the component. Higher concentrations of carbon lead to lower resistance values. - Binder Material
The binder acts as an insulator, holding the carbon particles together. Materials used include phenolic resins or ceramic materials. The choice of binder influences the resistor's mechanical strength, thermal stability, and moisture resistance. - Leads and Encapsulation
Metal leads are connected to the resistor body for circuit integration. The entire assembly is usually encapsulated in a protective coating (typically an insulating epoxy or similar compound) to shield it from environmental factors, further enhancing durability and stability.
The manufacturing process significantly influences the properties of carbon composite resistors. During production, the mixture of carbon and binder is compressed and molded into cylindrical or rod-like shapes, with metal leads attached to each end. The molding process ensures a solid, consistent structure. The resistor then undergoes curing, which hardens the binder, followed by precise trimming to achieve the desired resistance. The external coating provides environmental protection and insulation.
Variations in the carbon-to-binder ratio and the precise manufacturing process lead to slight differences in resistance values across production batches. Thus, the tolerance of carbon composite resistors is typically higher compared to other resistor types. The overall structure and material properties contribute to the characteristic performance of carbon composite resistors, including their high pulse energy handling capacity and relatively high temperature tolerance, making them well-suited for specific types of applications.
Key Advantages of Carbon Composite Resistors
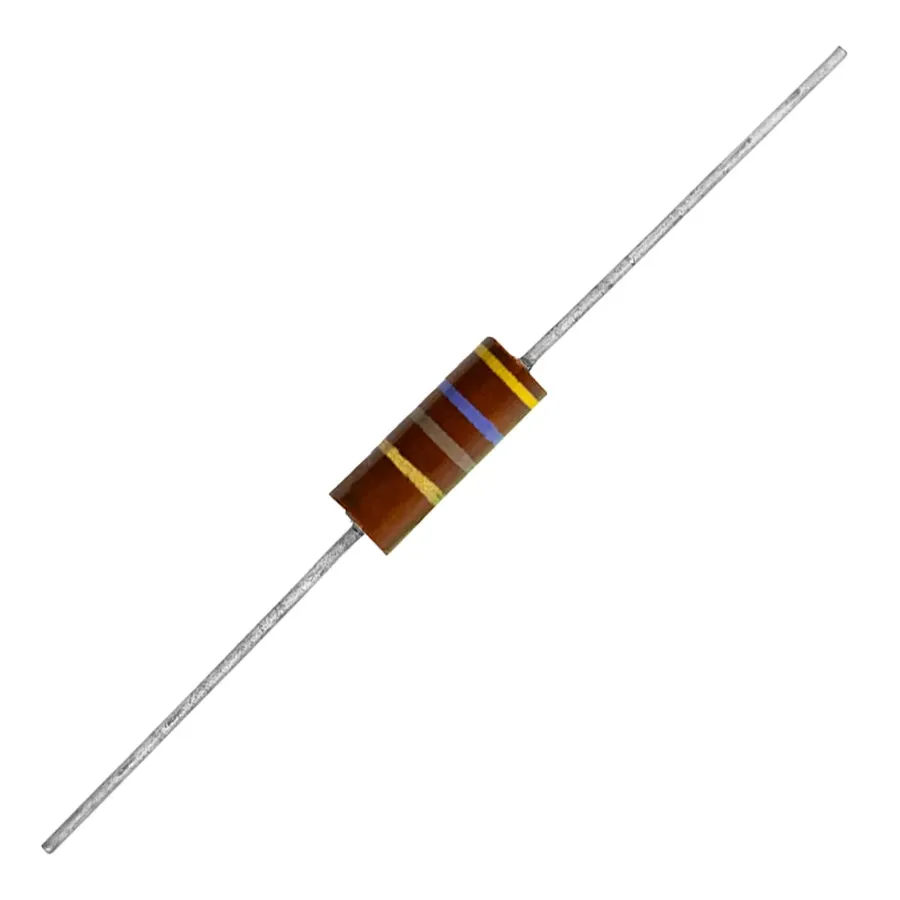
Carbon composite resistors are valued for their unique set of advantages that make them suitable for specific applications. These strengths primarily stem from their construction and material composition, allowing them to perform well under conditions where other resistor types might falter.
- High Pulse Energy Handling:
Carbon composite resistors can withstand very high surge currents and pulse loads without significant damage or change in resistance, a crucial attribute in applications with transient power spikes. - Low Inductance:
The non-spiral construction of carbon composite resistors results in very low inductance, making them ideal for high-frequency circuits where inductive reactance can be a major issue. - High Temperature Stability:
These resistors can operate reliably at elevated temperatures, making them suitable for applications with significant heat generation, although their temperature coefficient is not negligible. - Robustness
Due to their relatively simple construction, these resistors tend to be physically robust and less susceptible to damage from mechanical stress compared to thin-film counterparts.
Limitations and Disadvantages of Carbon Composite Resistors
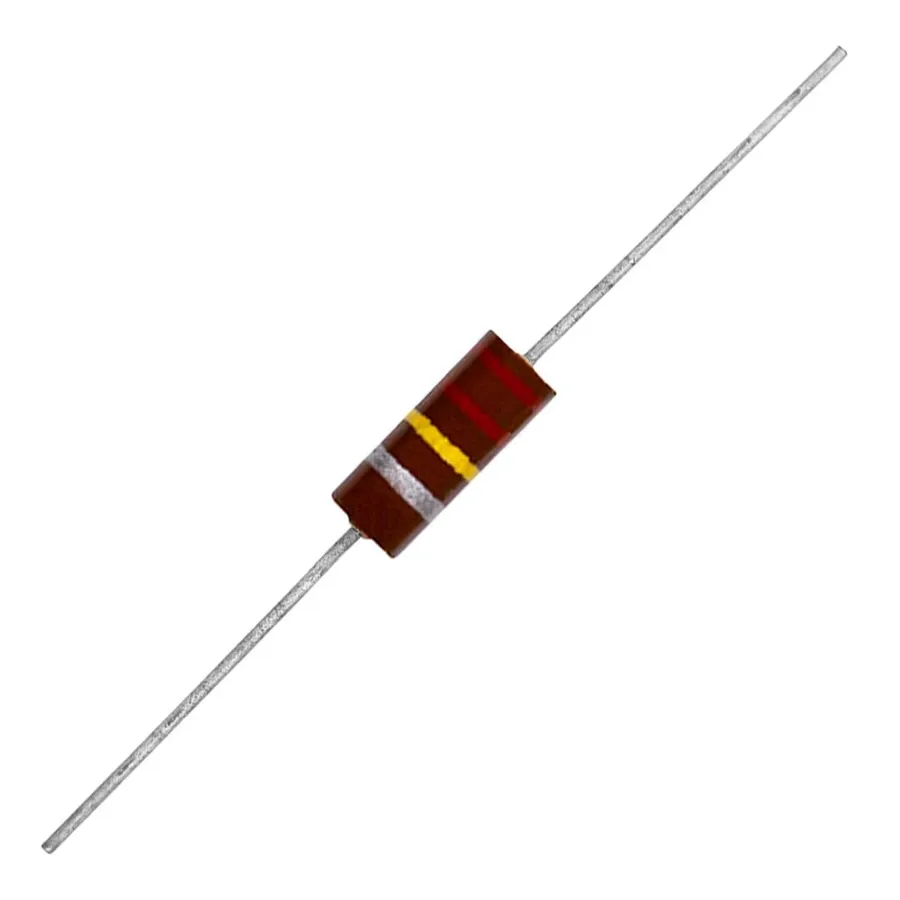
While carbon composite resistors offer distinct advantages, they also present certain limitations that must be considered in circuit design. These drawbacks primarily stem from their inherent material properties and manufacturing process, making them unsuitable for certain applications requiring high precision and stability.
- Higher Noise Levels
Carbon composite resistors generate more electrical noise compared to other resistor types like metal film resistors. This noise, a result of the random movement of charge carriers within the carbon matrix, can be problematic in sensitive analog circuits or high-gain applications. This is a key disadvantage that limits its use in certain high-fidelity audio circuits or instrumentation where minimal noise is crucial. - Lower Precision and Tolerance
The manufacturing process of carbon composite resistors results in a wider tolerance range, meaning their actual resistance can vary significantly from the stated value. Typically, they have a tolerance of ±5% to ±20%, while other types can achieve ±0.1%. This lack of precision can cause circuit performance variations and make them unsuitable for applications needing accurate resistance values. For precision applications, metal film or wire-wound resistors are often preferred due to their tighter tolerances. - Temperature Coefficient of Resistance (TCR)
Carbon composite resistors exhibit a higher temperature coefficient, which means their resistance changes noticeably with temperature fluctuations. This characteristic can lead to unreliable circuit performance in environments with varying temperatures. The TCR for carbon composite resistors is generally negative, decreasing resistance as temperature increases. It is important to account for this behavior in circuit design by using resistors with lower temperature coefficients or incorporating compensation methods. This factor must be carefully considered, especially when carbon composite resistors operate in a fluctuating thermal environment. - Resistance Drift Over Time
Over time, carbon composite resistors can experience resistance drift, meaning their resistance value changes with age, usage and/or environmental conditions. This long-term instability can lead to unpredictable circuit behavior and require periodic recalibration in critical applications. The change is usually caused by moisture absorption, thermal stress, and the gradual degradation of the carbon and binder materials. This potential drift is a critical concern when long-term stability is vital. - Larger Size for Given Power Rating
Compared to other resistor types, carbon composite resistors tend to be physically larger for a similar power rating. This can be a disadvantage in compact electronic designs, where space is often a constraint. Due to their construction and heat dissipation characteristics, they often require a bulkier form factor compared to film type resistors or surface mount options which can be a limiting factor in small form-factor design. - Higher Inductance at High Frequencies
While carbon composite resistors are generally considered to have lower inductance than wire wound resistors, they do exhibit a higher inductance compared to film-type resistors, especially at higher frequencies. This can cause impedance issues in high-frequency circuits and applications, where the parasitic inductance can alter the performance. Therefore, at higher frequencies, the inherent inductance of these components may have to be mitigated with other components.
Applications of Carbon Composite Resistors
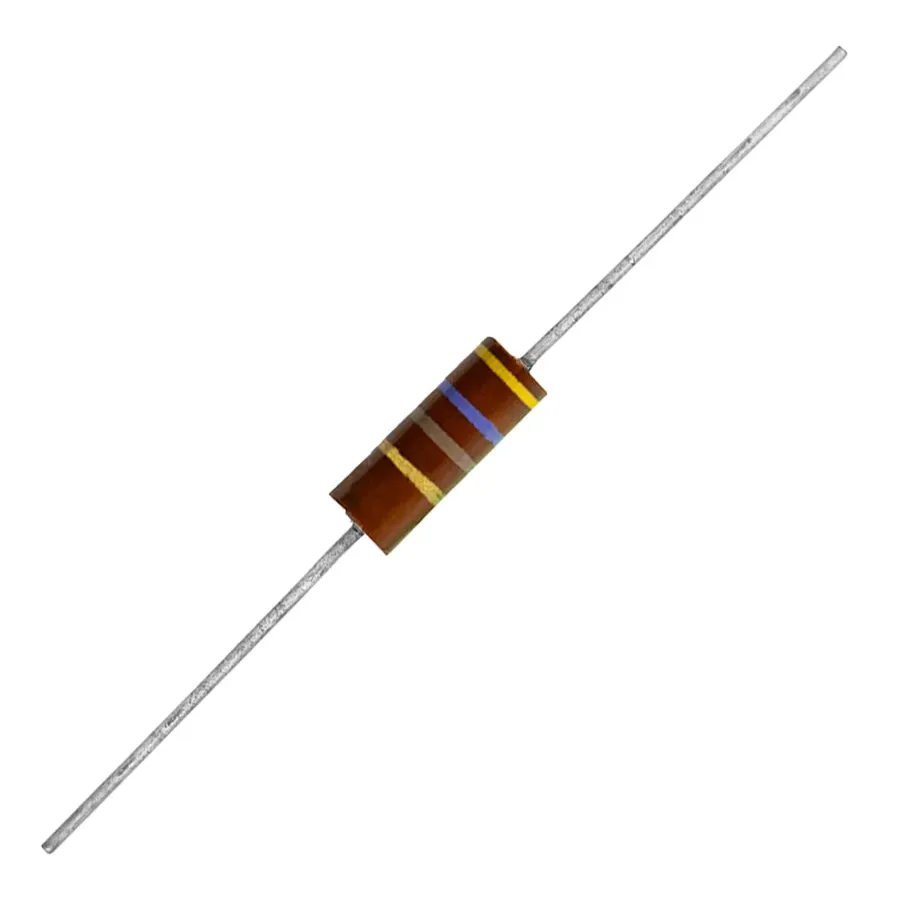
Carbon composite resistors, owing to their unique characteristics such as high pulse energy handling and low inductance, find applications in various specialized areas. Their robust nature and ability to withstand high temperatures make them particularly suitable for environments where precision and low noise are not paramount, but ruggedness and reliability are essential.
- Audio Equipment
In audio circuits, particularly within tube amplifiers, carbon composite resistors are favored for their ability to handle high voltages and their subtle contribution to the 'warm' tonal characteristics sought by some audiophiles. This is often attributed to the resistor's non-linear behavior under high signal levels. - Power Supplies
Due to their high surge current capability, carbon composite resistors are useful in power supply circuits for handling inrush currents during startup. They can absorb transient surges without failing catastrophically, contributing to the overall reliability of the power supply. They are less precise than other resistor types, which is acceptable in most general power supply circuits. - Vintage Electronics Restoration
Carbon composite resistors are indispensable for restoring older electronic equipment, including radios and vintage test equipment. Using the same type of resistor maintains the original circuit characteristics and aesthetic of the equipment, which is especially important in the restoration of valuable, historically significant devices. - High-Voltage Circuits
Their ability to withstand high temperatures and voltages makes them suitable for applications in high-voltage circuits, including certain types of test equipment, as well as various power transmission and distribution systems. - Welding Equipment
In high-current welding applications, carbon composite resistors can act as current limiting devices to provide controlled power in circuits with high voltages, because of their ruggedness. - Military and Aerospace Applications
Carbon composite resistors are used in some military and aerospace applications where resilience and high temperature tolerances are needed, even if precision is not always critical. This may include control systems or certain types of power management circuits.
Carbon Composite Resistors vs. Other Resistor Types
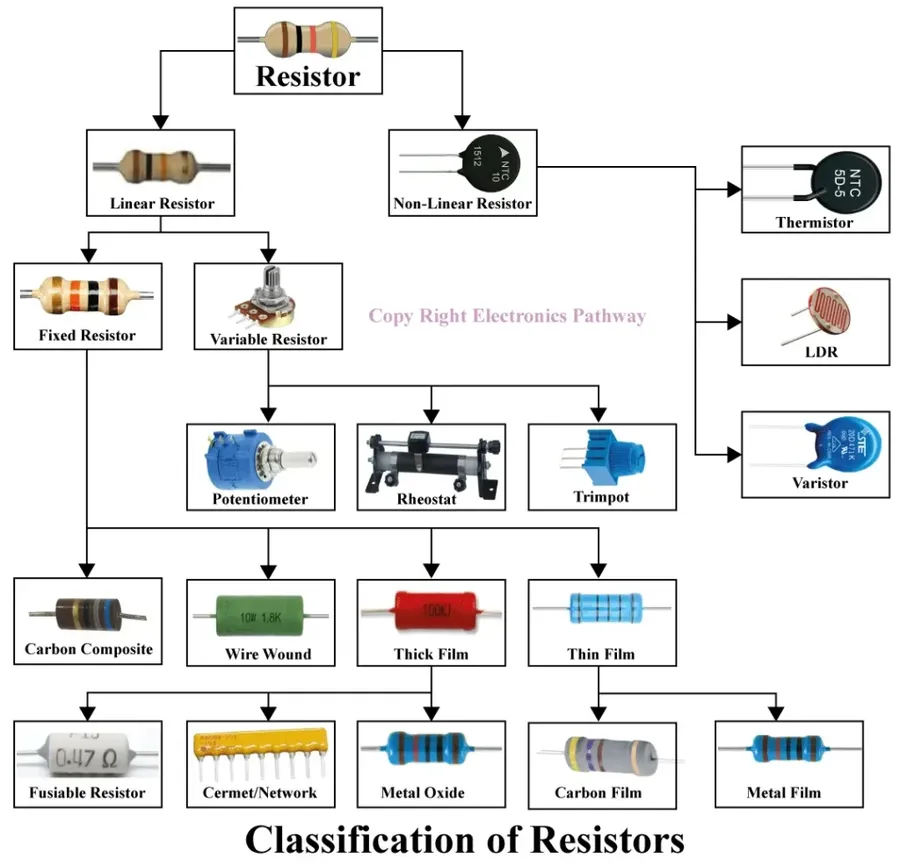
Carbon composite resistors, while possessing unique advantages, are not universally optimal. A comparative analysis with carbon film and wire-wound resistors reveals distinct differences in performance, cost, and appropriate applications. Understanding these distinctions is critical for informed component selection in electronic circuit design.
Characteristic | Carbon Composite Resistors | Carbon Film Resistors | Wire-Wound Resistors |
---|---|---|---|
Resistance Range | Moderate (1 Ohm to 10 Megaohms) | Wide (1 Ohm to 100 Megaohms) | Low (sub-Ohm to kOhms) |
Tolerance | High (±5% to ±20%) | Moderate (±1% to ±5%) | Low (±0.1% to ±5%) |
Temperature Coefficient | High | Moderate | Very Low |
Power Rating | Moderate (1/8W to 2W, higher wattage available) | Low to Moderate (1/8W to 1W, SMD is lower) | High (1W to hundreds of Watts) |
Noise | High | Low | Very Low |
Inductance | Low | Low | High |
Pulse Handling | High | Moderate | Low |
Cost | Moderate | Low | High |
Typical Applications | Audio Equipment, High Power Circuits, Vintage Equipment | General Purpose, Precision Circuits | Power Electronics, Current Sensing |
Frequently Asked Questions about Carbon Composite Resistors
This section addresses common inquiries about carbon composite resistors, providing concise and informative answers to help users understand their characteristics and applications. These FAQs are designed to address key aspects of carbon composite resistor functionality and performance.
- Are carbon composition resistors a good choice for modern electronics?
While not as prevalent in modern high-precision applications, carbon composition resistors possess characteristics that make them valuable in specific scenarios. Their ability to handle high pulse energy and high temperature make them suitable for certain power-related and legacy applications, however, they are not ideal for applications requiring low noise, high precision, and long-term stability. - Why are carbon composite resistors still used in some applications?
Carbon composition resistors are still favored for their high pulse energy handling capability and relatively low inductance. These qualities are beneficial in high-voltage and high-current circuits, such as in power supplies, surge protection, and vintage audio equipment. - Do carbon composite resistors exhibit unique audio characteristics?
Some audiophiles believe that carbon composite resistors introduce a warmer or more 'vintage' tone compared to modern film resistors. This is often attributed to their higher noise floor and non-linear behavior under high signal conditions, which can cause subtle harmonic distortions that can be perceived as favorable by some. However, these are subjective experiences and should not be confused with accuracy or precision. - What is the primary difference between carbon composite and wire-wound resistors?
Carbon composite resistors are made from a mixture of carbon particles and a binder, while wire-wound resistors use a metal wire wound around a core. Carbon composite resistors are known for their pulse handling and low inductance but have poorer precision and stability compared to wire-wound resistors. Wire-wound resistors offer high accuracy and low temperature coefficients, but are inductive and typically have lower pulse energy capabilities. The choice between the two depends on specific application requirements. - Are carbon composite resistors prone to resistance drift over time?
Yes, carbon composite resistors are susceptible to resistance drift, particularly under conditions of high temperature and humidity. This drift can affect the accuracy of the circuit over time and should be considered when designing long-term applications, especially where precise resistance is required. - What are the typical tolerance and temperature coefficient characteristics of carbon composite resistors?
Carbon composite resistors usually have a higher tolerance, typically ranging from 5% to 20%, making them unsuitable for high-precision applications. They also have a relatively high temperature coefficient, meaning that their resistance changes significantly with temperature variation, affecting their accuracy and reliability in variable environments. - How does the construction of carbon composite resistors affect their performance?
The construction of carbon composite resistors, with carbon particles embedded in a binder, inherently contributes to their unique characteristics. This material composition gives them high pulse energy capacity, but it also causes higher noise and temperature instability than other resistor types. The mixture and manufacturing process largely determine the final resistance and performance characteristics.
Selecting the Right Carbon Composite Resistor
Selecting the appropriate carbon composite resistor requires careful consideration of several key parameters to ensure optimal performance within a given circuit. These parameters primarily include resistance value, power rating, tolerance, and application-specific requirements. Understanding these factors is critical for effective circuit design and preventing component failure.
- Resistance Value
The resistance value, measured in ohms (Ω), dictates the resistor's opposition to current flow. Choose a value that meets the circuit's design requirements. Standard values are available, but precise requirements may necessitate series or parallel combinations to achieve the target resistance. Pay attention to the color code, or printed value on the resistor body when selecting. This value directly affects the current and voltage in your circuit. - Power Rating
The power rating, measured in watts (W), specifies the maximum power the resistor can dissipate as heat without damage. Always choose a resistor with a power rating higher than the maximum power the resistor will be expected to dissipate to prevent premature failure. A generally accepted rule is to select a power rating that's at least twice the expected power dissipation to ensure a safety margin. If a resistor is not properly rated, it could lead to overheating, premature failure, or even a fire. - Tolerance
Tolerance indicates the maximum allowable deviation from the specified resistance value, usually expressed as a percentage (e.g., ±5%). Lower tolerance values mean higher precision, resulting in more consistent performance within the specified range. Select tolerance based on the precision requirements of your application. Precision applications require tighter tolerances. For example, a 100-ohm resistor with a 5% tolerance can have an actual resistance between 95 and 105 ohms. Less critical applications may use a 10% or even 20% tolerance. - Application Requirements
Consider the specific application needs. For high-temperature environments, ensure the resistor's operating temperature range is sufficient. Pulse energy handling capability of carbon composite resistors also needs consideration if they are used in pulsed applications. In high-frequency applications, ensure that the resistor's inherent inductance is acceptable. A lower inductance is ideal for high-frequency applications. For high current applications, choose a resistor with a higher power rating and pay attention to the physical size of the resistor as well. Size determines heat dissipation capabilities.
In summary, the selection of carbon composite resistors involves a balanced evaluation of resistance, power, precision and application-specific characteristics. By taking these factors into account, engineers can ensure that circuits operate reliably and as intended. Always consult datasheets to get the precise specifications before selecting a resistor.
Practical Tips for Using Carbon Composite Resistors
Proper handling, storage, and soldering techniques are crucial for maximizing the lifespan and performance of carbon composite resistors in electronic circuits. These guidelines are essential to prevent degradation and ensure the reliability of your circuits.
- Handling Precautions
Avoid excessive mechanical stress, such as bending or twisting the resistor leads, as this can damage the internal structure of the resistor and alter its resistance value or cause it to fail prematurely. Handle resistors by their leads or the body to avoid contamination from skin oils, which can accelerate corrosion or affect performance. - Storage Recommendations
Store carbon composite resistors in a cool, dry place away from direct sunlight and excessive humidity. High humidity can lead to moisture absorption, which can cause resistance changes and premature degradation. Storing resistors in anti-static bags is recommended, especially when handling in areas with potential static discharge. - Soldering Guidelines
Use proper soldering techniques, limiting heat exposure to avoid thermal stress. Excessive heat can alter the resistance or damage the resistor. Use a temperature-controlled soldering iron, set to a temperature recommended for the specific type of solder you are using. Apply solder quickly and allow the resistor to cool naturally after soldering to avoid internal stress. Ensure that the solder joints are clean and without oxidation or excess solder. - Lead Preparation
Before soldering, ensure that the leads are clean and free of any oxidation or corrosion. If leads are corroded, lightly clean them with a fine abrasive pad or specialized chemical cleaners. Leads that are not cleaned can result in poor solder joints and erratic performance. - Component Placement
When mounting resistors on a circuit board, ensure sufficient spacing to allow for proper heat dissipation. Carbon composite resistors can generate heat under load, and sufficient space will prevent overheating. Consider adding thermal vias to your PCB layout to aid heat dissipation. - Environmental Considerations
Avoid using these resistors in highly corrosive environments. Chemical vapors can affect the resistor's properties and lead to premature failure.
Carbon composite resistors, with their unique blend of strengths and limitations, continue to be an essential component in specific electronic applications. They excel in situations requiring high pulse energy handling and low inductance but are less suitable where precision and low noise are paramount. Understanding these nuances allows designers and enthusiasts to select and utilize carbon composite resistors effectively, ensuring optimal performance in their projects. By choosing the right resistor, like the carbon composite resistor, users can continue to build and innovate in electronics.
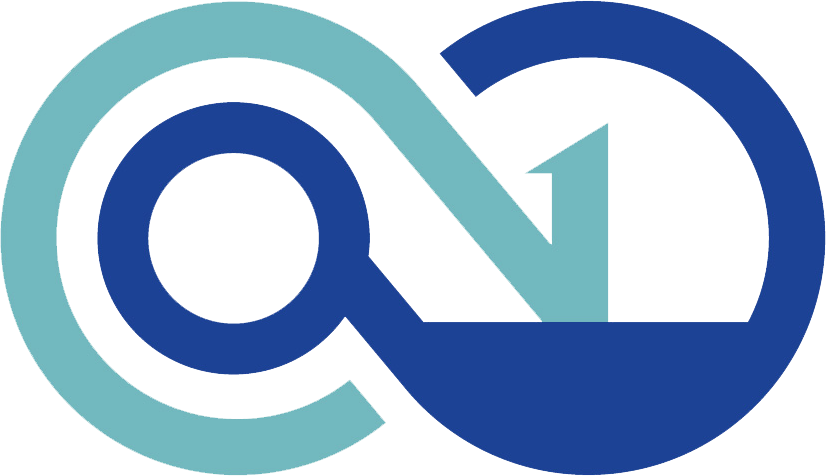